I've been wanting to build a furnace for years now and the combination of wanting to finish my Dad's engine this is it so far: hey I've been buying tools
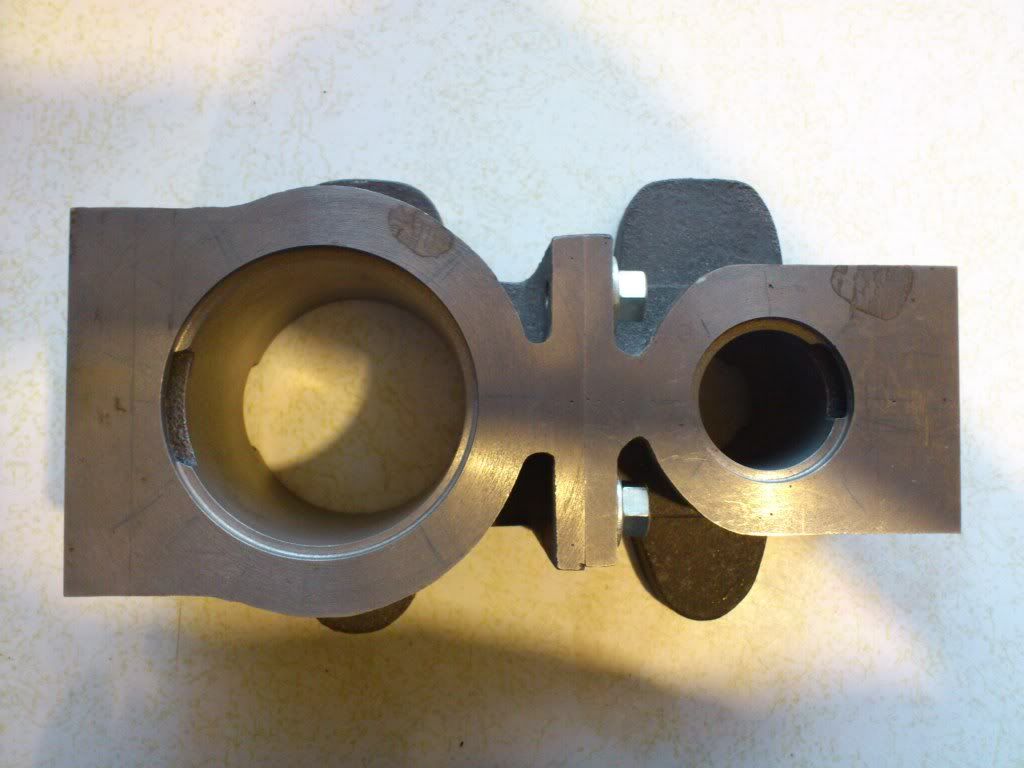
and seeing what all you guy's are doing I've made the plunge. I did a bit of casting back in school, grade 8 metal class (of 68) and am just getting to it now ..... better late than never. I can't take credit for the design I followed Ironman's design It is a beer keg with 2 inch thick fiber insulation type using a blower..
http://madmodder.net/index.php/topic,7802.0.html I mixed up some fireclay which cracked as it dried out so I leveled it off with sand and put a single layer of fiber down for the base I figured with the fireclay one layer will be fine and in the pic you can see a shelf for a kiln I am using this because I don't have a crucible yet so I don't know how big to make the recess, if needed I can put another doughnut layer of fiber. The sides are coated with sodium silicate to glue the 1" fibrefax as it's called here and a second layer goes on top of that staggering the joints.
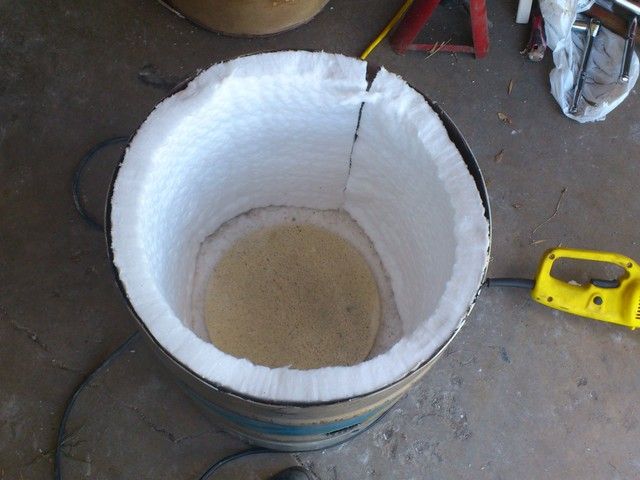
The lid was a bit of a disappointment I had two lines marked out, one where the top meets the side and the to cut line 2 " lower my son wanted to cut it and by the time I looked the top line was cut, plasma cuts quick! not his fault though.

there is also a 4" vent hole in the top. I decided to just lay the fiber flat, it is a rounded surface so I could still get 2 layers in the center area so it was silicone'd and I drilled a few small holes to tie it off with some high heat wire for a kiln from the ceramic store. Worse case scenario I can weld a band to extend it back to the desired dimensions.
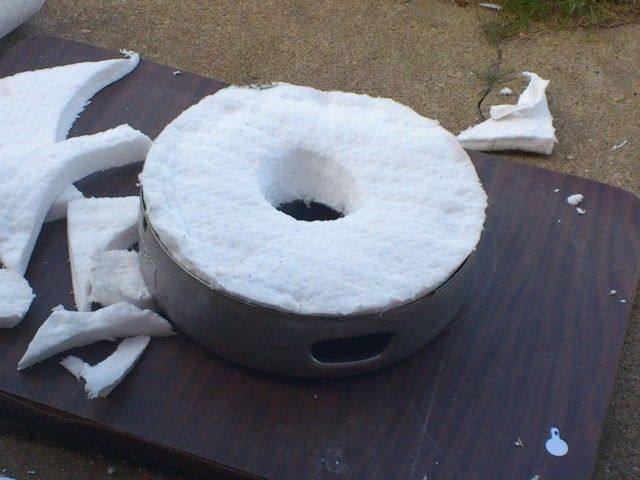
The next thing to do is apply a zircon refractory coating I used itc 100, I mixed it 2 parts water to 1 part itc strange stuff leaves some grit like sand at the bottom of the cup seems to have mixed ok though so i brushed it into the bottom joint.
The blower I had for a long time, actually I don't remember where I got it so there ya go, anyways I found a motor and made a adapter plate for it and it seems to push enough air. I could only find some pipe with a 1" inside dia so that means the flow is being reduced from the get go the blower opening is 2 3/8" it should take the next size pipe so for the time being I reversed the flange turning it down in the lathe to fit the blower the threads still catch for a couple of turns. My thinking is I could unscrew one pipe and screw in the other although the larger probably will not need the reducer. For the fuel line I milled a slot and bent the tubing so it will spray down the center, I also because of the reduced pipe size made a brass jet with a 19 drill hole I figured without using a regulator it would slow the gas down a bit maybe making it last a bit longer it looks ok on the chart and I can run it flat out so maybe a bit bigger I'll see how it melts metal!

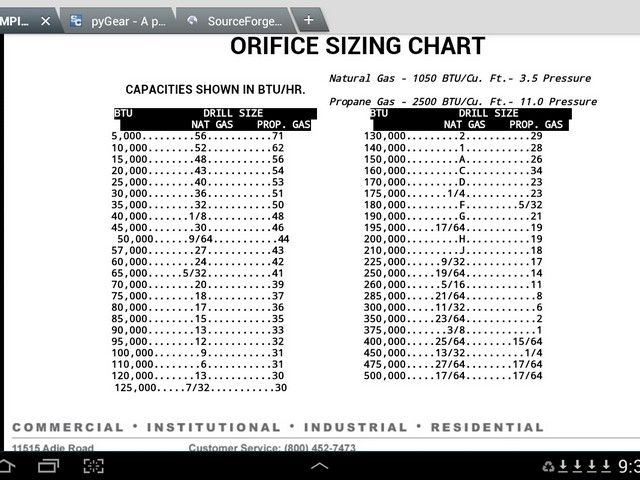
I didn't know if I would keep the two separate or put on one base so a temporary stand was screwed together out of wood.
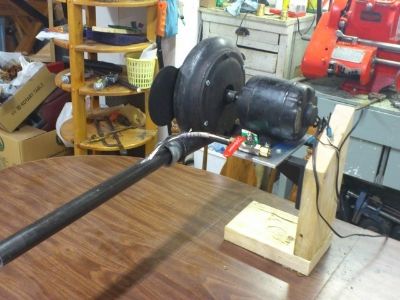
This was all purcased at the local ceramic supply store
cost: fiberfax 1" $12.60 per foot
sodium silicate $8.95 per liter
itc 100 $100.00 per pint
fireclay $7.00 2.5 kg
bentonite vollclay iron free $32.00 50 lbs
I figure it probably cost me about $250.00 the end result is a inside measurement of 13.5" high by 11 " wide, so that's it thanks for looking and here are some pics of it running!
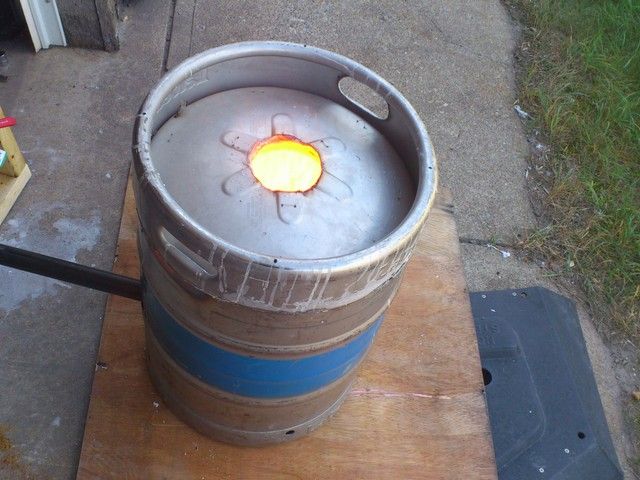
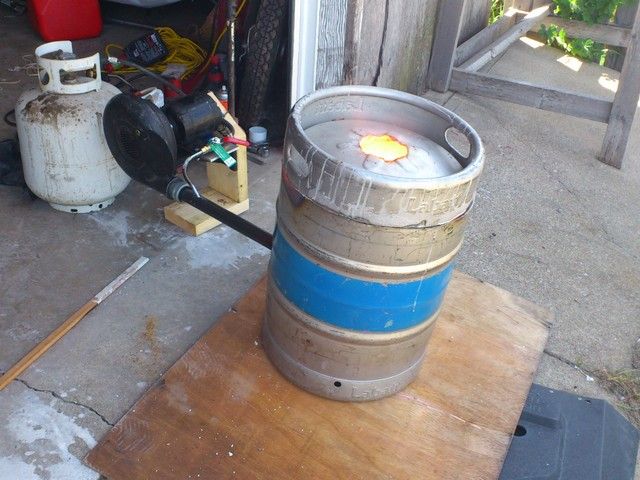
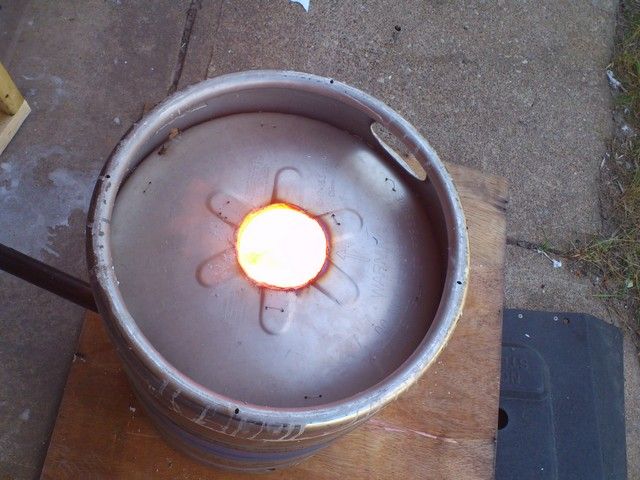
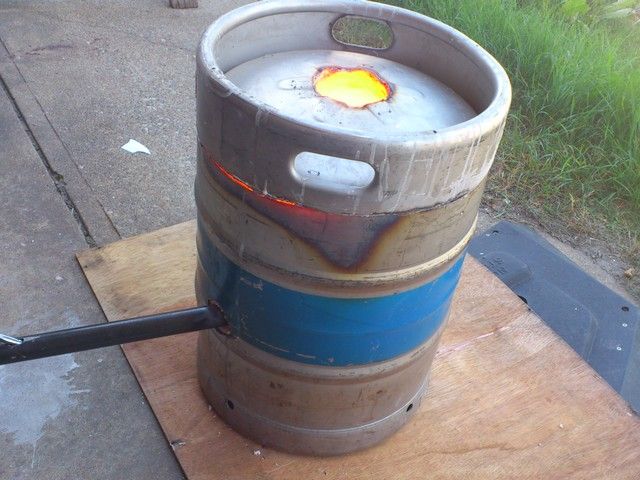
thanks for looking!
