Hi,
I realise from the number of photos that I just uploaded to Botophucket (dyslexia rules!) that I haven't updated in a while. In addition, I've decided to make it so that I can use three different sets of gears. Two disadvantages,:-
I. I can't drill for a draw bar to enable me to use a Morse taper which could have been useful.
II. I have a lot more little parts to make!
So here it is, starting with the gear carriers.

The top slide on the lathe still being set up with the taper (about 20°) it's a good place to start.

By turning the end of the 17mmØ down to 14mm and flipping it round, I could then cut the taper in the same direction as it was cut on the inside of the spindle.
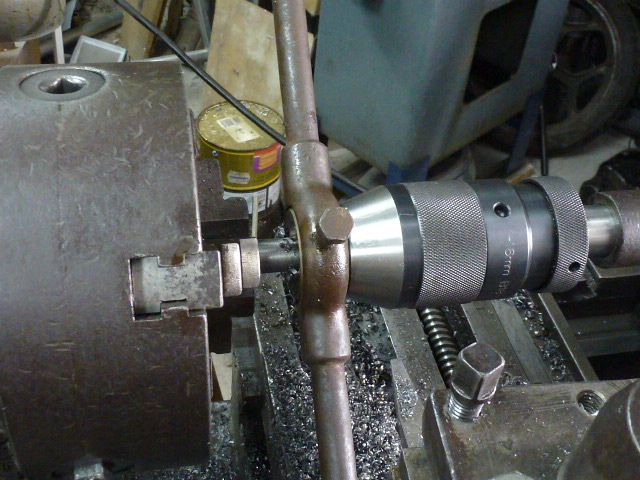
Cutting the M14 thread. I made four as who knows what gears might turn up in the future!
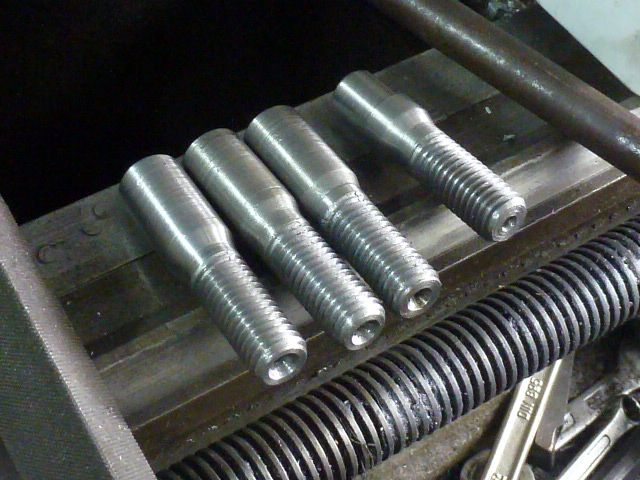
Three blanks plus the one that I already reduced to 14mm.

I set the spindle up in the fixed steady to use it as a mandrel to reduce the ends of the carriers and to drill and tap to M8 for the gear retaining bolt.
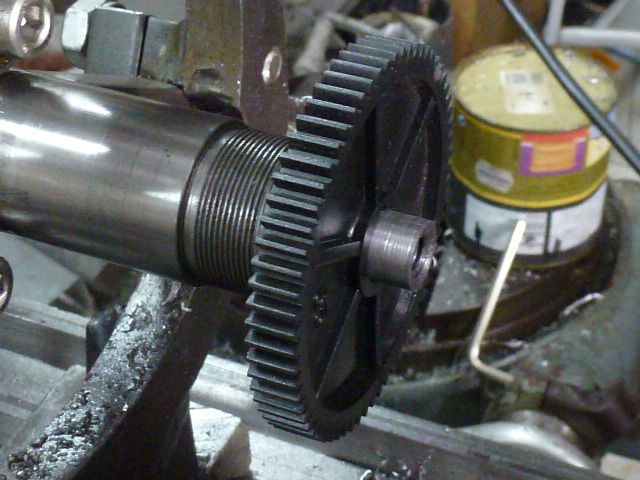
The 12mm carrier test with a plastic gear!

With the spindle once again set up in the dividing head, I centred with a centre finder and centre drilled for an M6 thread.
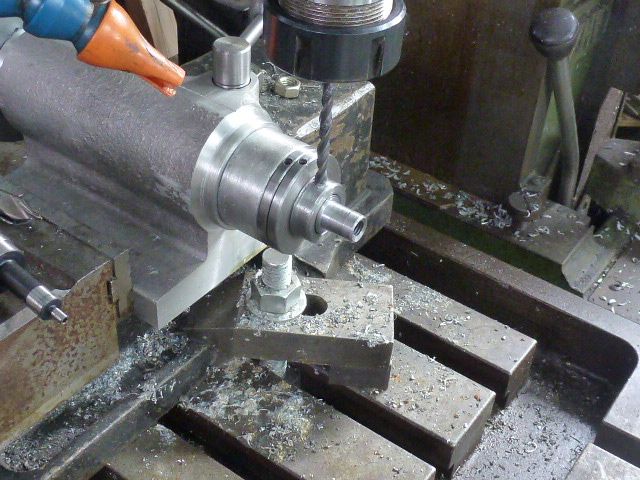
Without moving the setup, I drilled all of the carriers 5mm .

Tapping the spindle M6.

The drive belts arrived today, now I can use that nice precise little three jaw and the power feed again!
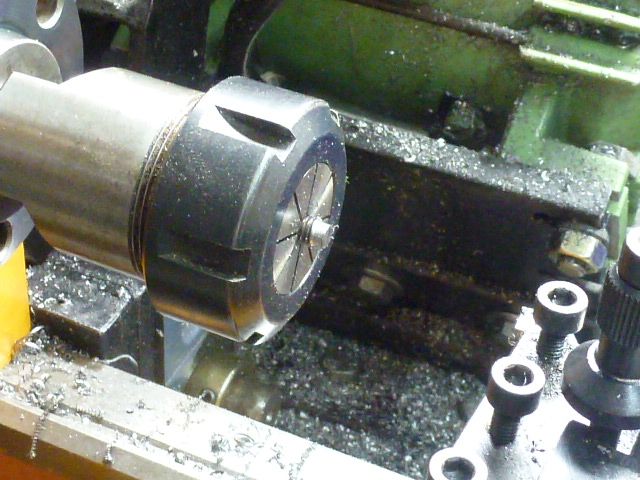
In addition, I can use my ER32 collets, handy when shortening and reducing grub screws.
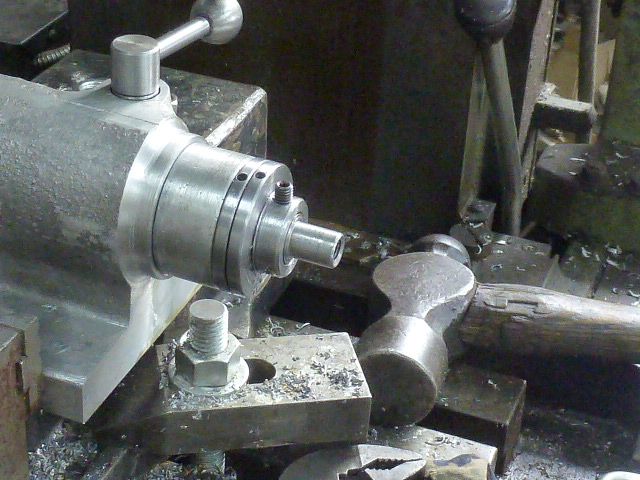
Grubscrew, now there will be two Allen key sizes on the dividing head.
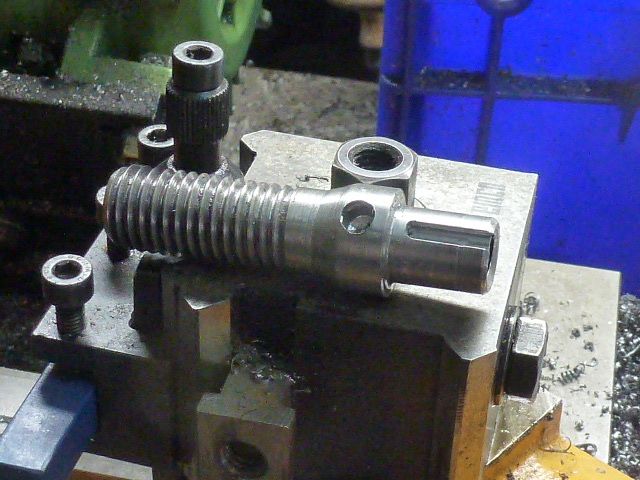
The finished product, just needs deburring. I forgot to take pictures of cutting the keyways. I was nervous, having never cut 3 and 4mm keyways with a 2mm slot drill before, my mill seems enormous with that tiny little end mill in it! No problems encountered!

All three of the key-ways are different! This is the Emco one which is four mm wide.
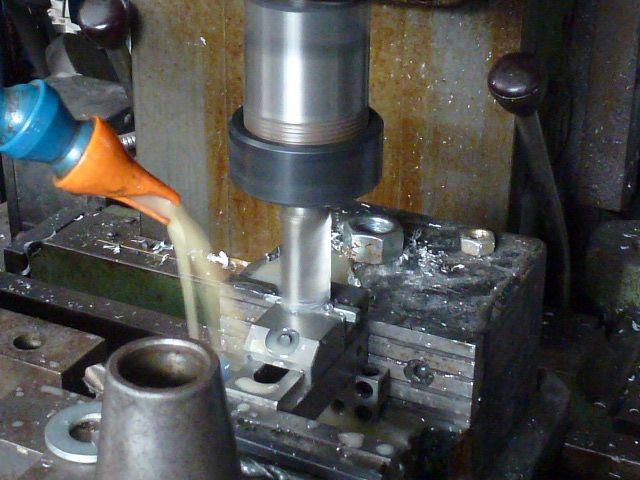
Milling the keys to size.
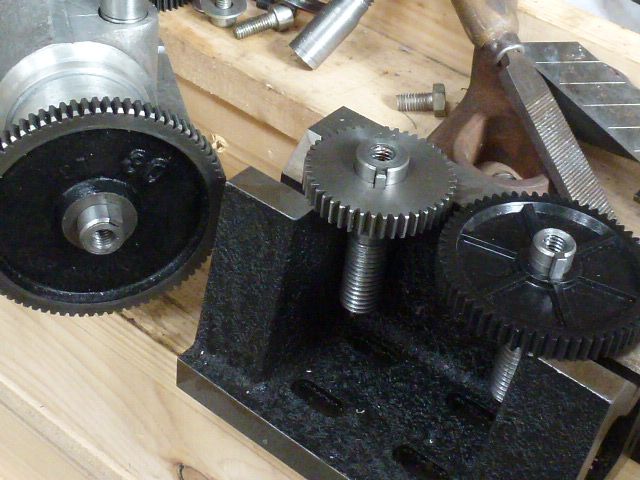
The three carriers finished with their respective gears and keys.
I may soft solder the keys in place so that they don't get lost.

With the gear carriers done, I can get on with the Banjo. Spot the mistake!
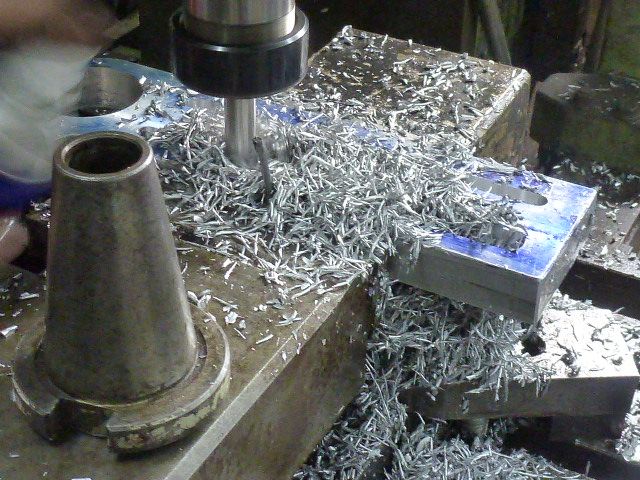
Carving out the slots.
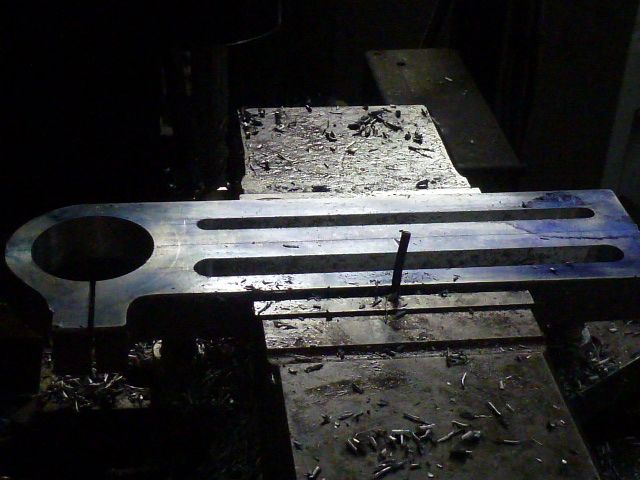
The set up is flawed, having not tried to cut slots this way before, I hadn't thought about the fact that I was squeezing up on an area that I was removing metal from!
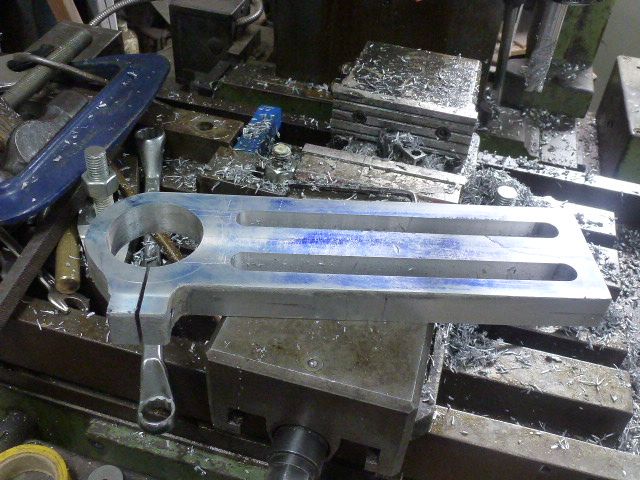
The Banjo gently started to rise in the vice, no damage, but another reminder about how to set up!
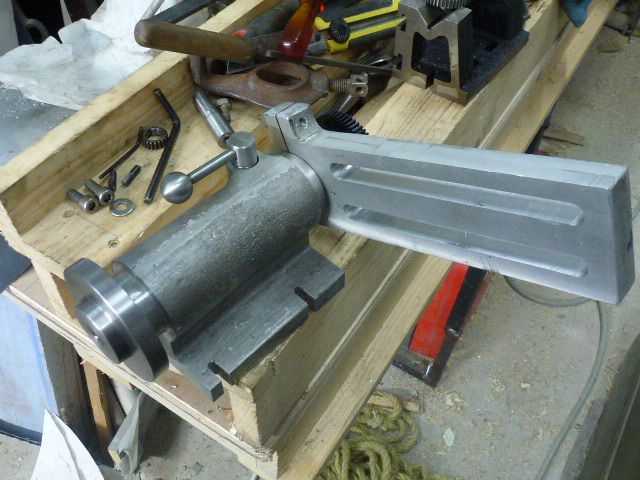
The slots are finished, Al that the Banjo needs is a clean up and chamfer.
I'll be back later, I'm not even half way through the photos that I've taken!
Regards, Matthew