I made several changes and cast iron today.
First change was the enlarged exhaust hole in the furnace lid.
Second change was reducing the size of the sprue from 1.25" to 1" in order to keep it choked with metal.
Third change was to add some of my 140 mesh sand to the 60 mesh greensand I have used recently. About 15% was added.
Fourth change was to ram somewhat lighter
Fifth change was to use no sodium carbonate as flux
Sixth change was to preheat the new crucible to red heat at moderate burner throttle before adding metal.
Seventh change was to alter the pattern to include a semicircular groove to form a greensand core. This piece willl later be bored out, and the cored channel will make this easier. It also reduces the the mass of metal poured..
First Try:
I'd like to say everything worked out, but unfortunately I poured short. The much larger amount of slag of a very pasty consistency fooled me into thinking there was more metal in the crucible than there was -- and that it was hotter than it was when i dipped in a poker and it came out clean. Also the gates were a little shallow, so basically I ended up with a nice bar ingot of about 3/4" thick, but not a part.
Second Try:I could tell the pour was short, so I didn't wait very long to unmold. I decided to use the residual heat in the furnace to attempt another melt. So I quickly broke up more scrap, and fired up the furnace. While it was heating I rammed up a new mold. I decided that I'd try a riser in this one as an additional change, but make sure the crucible was full of metal, not just 1/3 slag. I figured my smaller sprue, and the new core groove would give me enough additional metal in a full crucible to afford an 1.25" riser. Also I'd put in slightly deeper gates, and be absolutely sure the metal under the slag was fluid.
I pulled the crucible out when I thought it was ready, and scraped the very thick sluggish slag out of the way where I would pour -- I couldn't scoop it all off easily, as I had when I used Sodium Carbonate -- that stuff really liquifies the slag.
I poured and watched the riser fill to the brim, and had enough metal left over to pour an ingot as well. Good!
In a couple minutes the riser started to shrink down -- which I took as a good sign! Both the sprue and riser dropped quite a bit. Here's a pic:
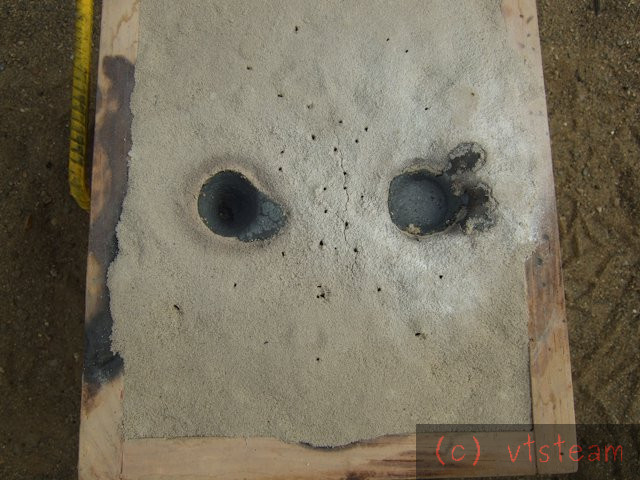