Hi lads, thanks much for the complements, and comments, I'm enjoying this build ever more, as I see the many other projects going together at the same time. I reckon I'll have to live another hundred years to finish all my projects on my list

I've got a bit more done, having roughed out the outside of the hot cap, I cut it off, surprizingly easily, with a cutoff tool, glad the cut was right at the chuck jaws, and put the chuck on my dividing head, the hot cap in the chuck, to mill the "fins" to collect the heat.
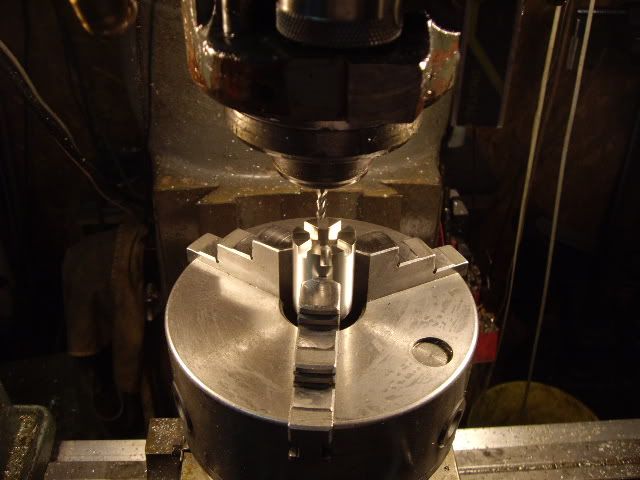
This is after several cuts, taking care with a sharp 3/16ths mill as the carbide end mill I was using snapped off as it broke out of the first cut, it being a long cutter, and catching the brand new edge on the edge of the end of the cut, hate stainless.
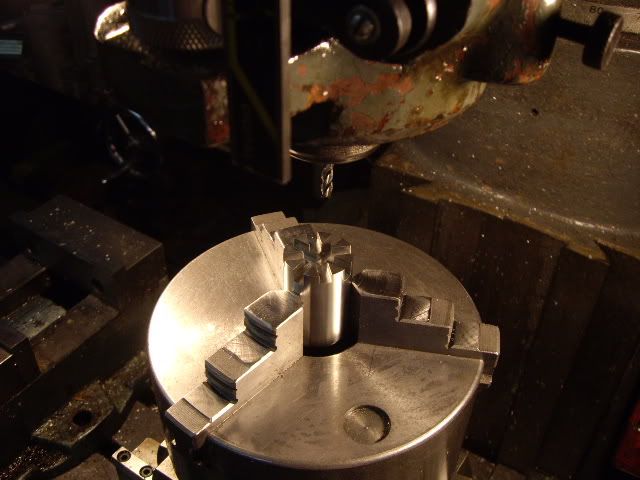
This is among the last cuts, I went .250 deep twice at 90 degrees, and .125 in deep at 90 degrees, offset by forty five, making lots of little points to absorb heat from the flame, and retain a thick cap end.
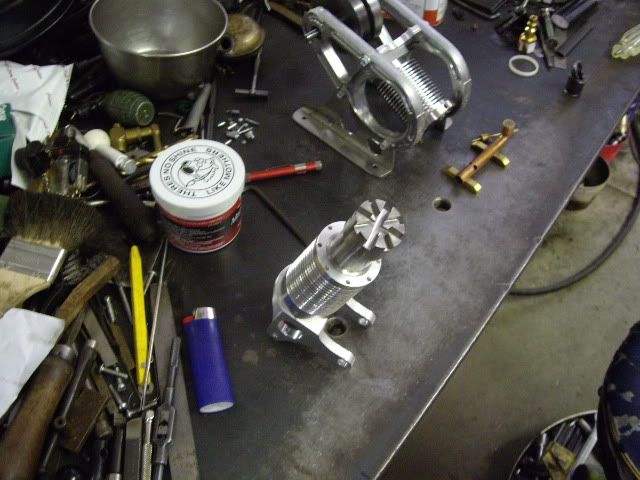
of course after milling the slots, I put it back in the lathe and turned the part right behind the recess for the seal, down to about fifteen thousandths thickness to minimize heat conduction directly.
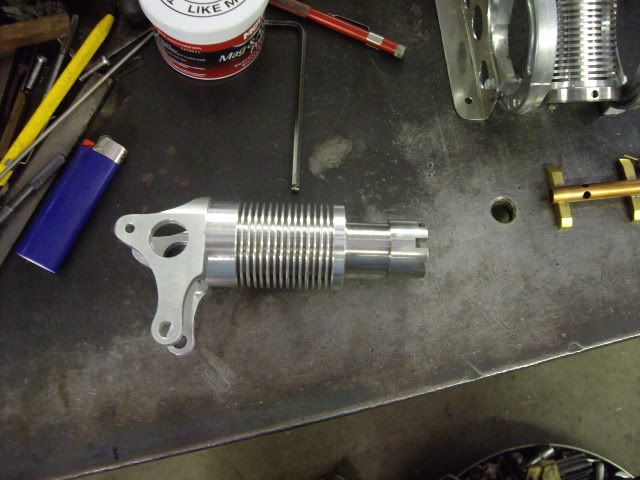
here's a shot of the whole mess lying on its side
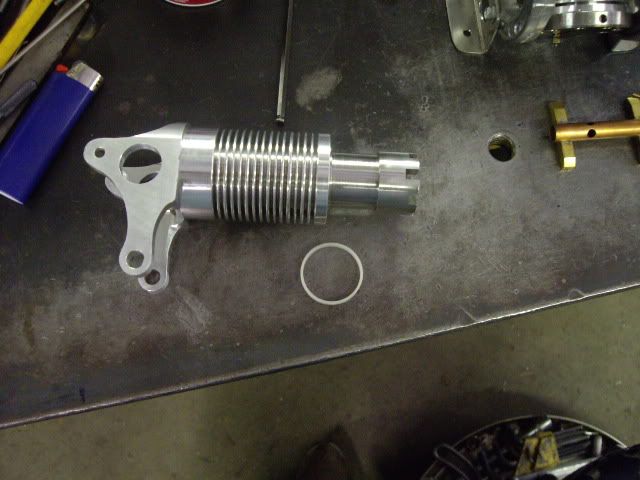
lying on its side with a spare seal, turned out of a scrap of delrin I think, picked up off the floor waiting to be thrown away and ecstatic at being put to use again.
Of course, having lapped the cylinder, made the hot cap and seal, and fitted everything, I had to turn a piston, so a 1 in bar of graphite was centered in a four jaw, about five minutes taken to produce a teaspoon of black dust, and a perfect on size piston turned, with a touch of the finest file I have, just to take a quarter of a thousandth off, using a real micrometer instead of the all important calipers.
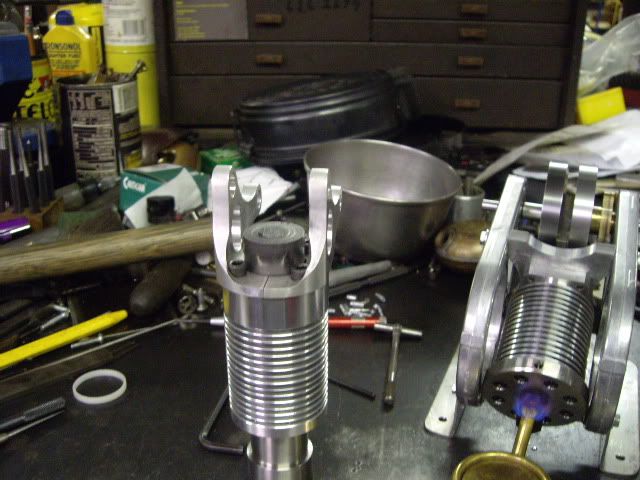
Here is the assembly, standing on the hot cap, with the piston floating on air in the very top of the cylinder. Of course there was another hour of lapping, as measuring for a fit is a different story from fitting a plug into the actual hole. Next, I will be machining the rough piston to take the aluminum piece which will hold the gudeon pins, and the bronze guide for the displacer rod, which runs vertically through the power piston. With a bit of luck, I can get a crankshaft assembled as well, it's hard to have all these pieces and not have a shaft to turn with the fingers and watch things move as they should. I am seriously challenged by that video of the Gold Blend engine running so sweetly with such a small flame. Ta ta for now,

Cheers, mad jack