Hi all, there was some interest in the die filer I showed in use, and so I took some pictures to display it better. The die filer is a kit build from Metal Lathe Accessories, which is still listed on the internet with a good many quality bits of tooling. I bought a cross slide casting so I could mill on my lathe, before I got a mill, then a dial indicator holder, a quick retract threading tool post, and about a half a dozen other bits and pieces, all of which are top quality iron castings, among the best I've ever machined, no blow holes or pockets, and very fine grain structure, and very well designed, written up instructions for what ever level of machining you've reached, and useful, with easy access to help if needed.
The die filer was a present to myself, and it does a great job of profiling parts putting angles on edges evenly, and since it cuts rather fast, with very little pressure, files last a long time. It takes files designed to cut on the pull stroke, however if such are difficult to find, one can easily grind a regular file down to fit in the spindle end, and they work fine too.
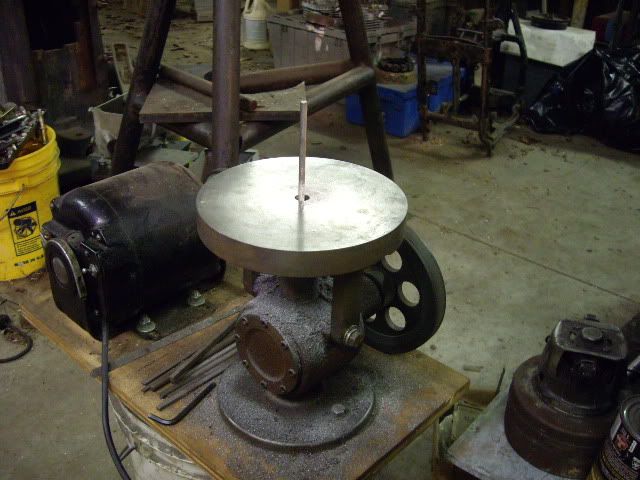
The basic machine, about thirty pounds, mostly cast iron with the main casting well made with plenty of room inside for the operating parts
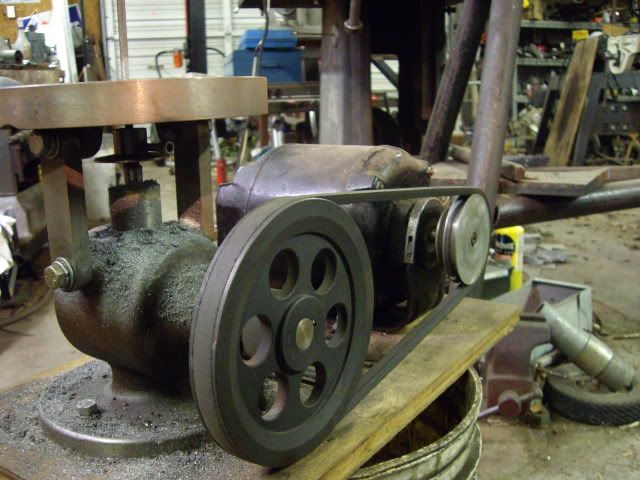
The pulley side, a nice heavy cast iron pulley does a good job as a flywheel 1/4 hp motor is more than enough
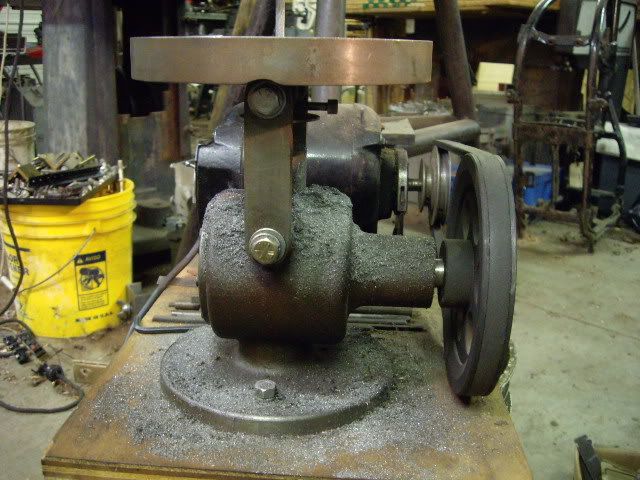
side view of the machine, showing relative locations of the main shaft, pulley and main housing
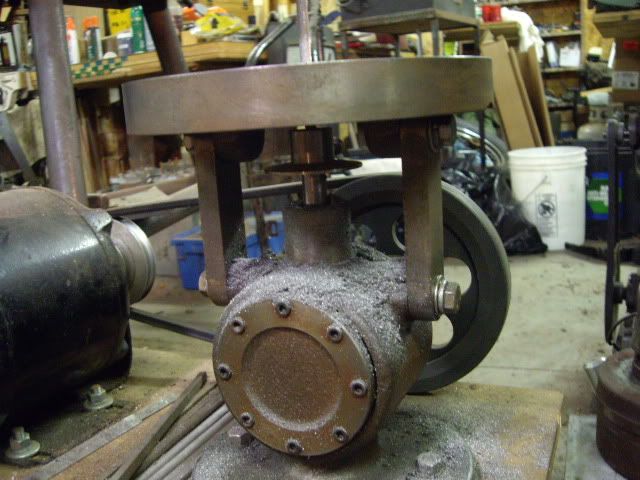
a look under the table, never been cleaned off since it first filed, no scoring on the file shaft
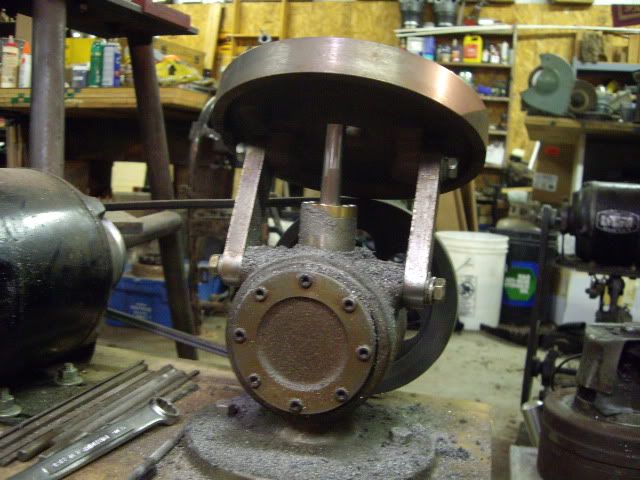
another view of the machine
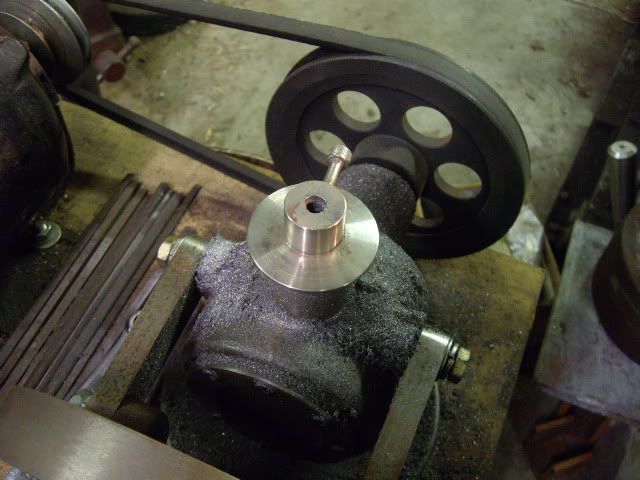
with the table off, you can see the "top hat" which sheds most of the filings away from the shaft, turned out of stainless scrap it holds the allen screw which holds the files in place
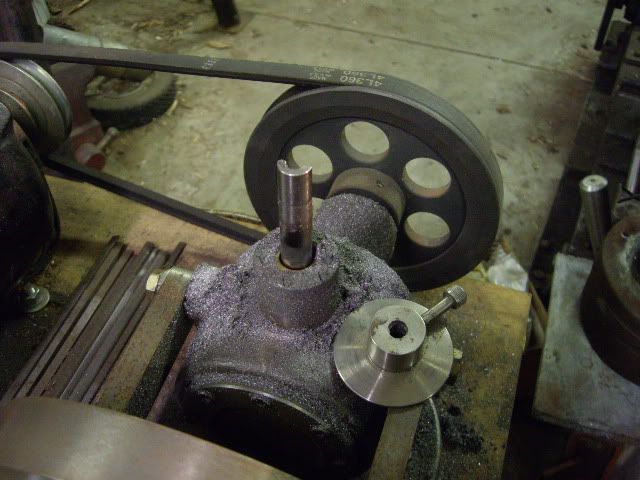
under the top hat, lots of filings built up, no problems
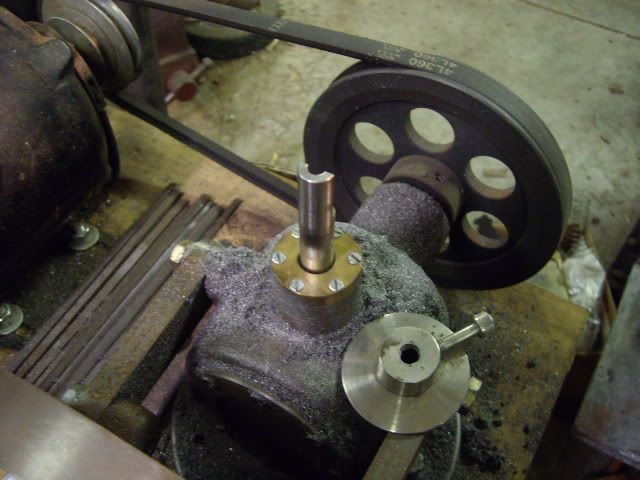
filings brushed away showing the bronze cap with a felt washer underneath, keeping out stray filings, works very well at keeping the shaft clean
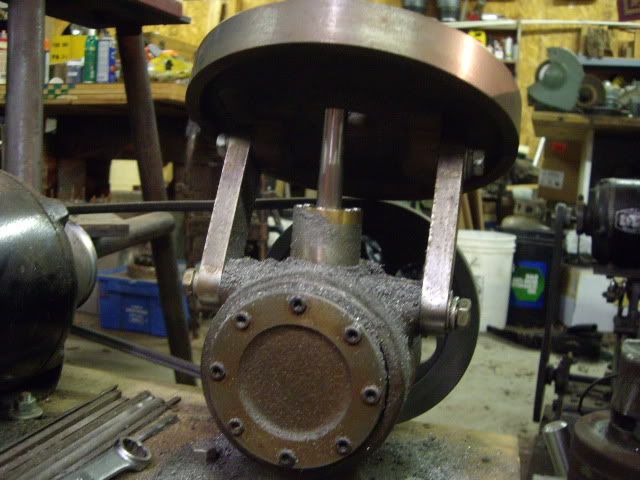
with the table tilted you see the end cover where all the working parts are accessed
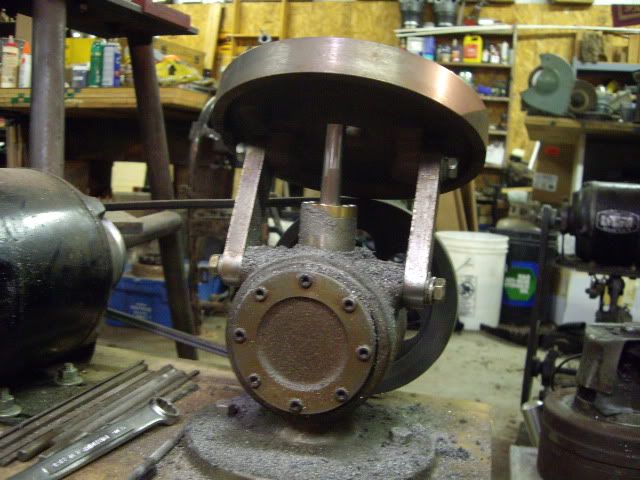
another end view. Inside, the crankshaft is .750 with a cut away wheel with a .250 pin at .500 radius from the center. Facing it, a block of cast iron, with a half in reamed hole vertical, for the main filing shaft, which runs in a bronze bushing above the block and into a bushing below as well, in a blind hole. A half in wide, quarter in deep slot runs sideways across the face of the iron block with a bronze block half by quarter by one in long with a .250 reamed hole in the middle for the crank pin to fit, so it moves the filing shank up and down, while sliding the bronze block back and forth in its slot. the filing shank has a hole drilled in it from the bottom, with a cross hole intersecting it right about where the crank meets the iron block, the blind bushing hole is open to the oil, which is pressure fed up by the downward movement of the filing shank, and oil squirts out the cross hole, aimed at the crankpin, and oiling the scotch yoke with fresh oil every stroke.
The main shaft runs in bronze bushings pressed in the bored body of the machine, and reamed in place, with a shaft seal to keep the oil from leaking out onto the pulley. The table is about eight inches in dia, about half in thick cross section, with a sturdy edge about an inch wide and half an inch deep. The table supports are half in by in bar stock with three eighths in bolts allowing tilting and adjusting the table for optimal file position.
I've used it well for more than ten years, never got to cleaning it up after testing it, so it didn't get paint, and it got its first bit of cleaning as I brushed away the filings to show the cover plate for the felt washer. The main shaft is a piece of scrap shafting, the file shank is a distributor shaft from a Chevy engine, with all the hard to find parts coming with the kit. It's most useful work is filing and profiling in pierced work, where only a die grinder could get in, but it has better control, while removing less meat per minute, and giving a better finish, and easier to straighten out a crooked line. It does a great job cleaning up the spokes of a flywheel, or filing off the casting lines on a cast section, as well as doing quick work with sheet metal piercings, working very well with very fine files for removing cutting marks left behind. It goes for about eighty or ninety dollars plus shipping, but I feel it is well worth the money. I'd have opened it up and shown the workings, but then I'd have to wash it all out, take it all apart, and replace the main shaft seal. It could hardly be simpler, yet is very effective for what it does best, one of my better deals in tooling, worth every penny. Cheerio, mad jack