Hi all, well, I had to put her back together and test her, but she was still smoking, and still refusing to pick up any swarf.
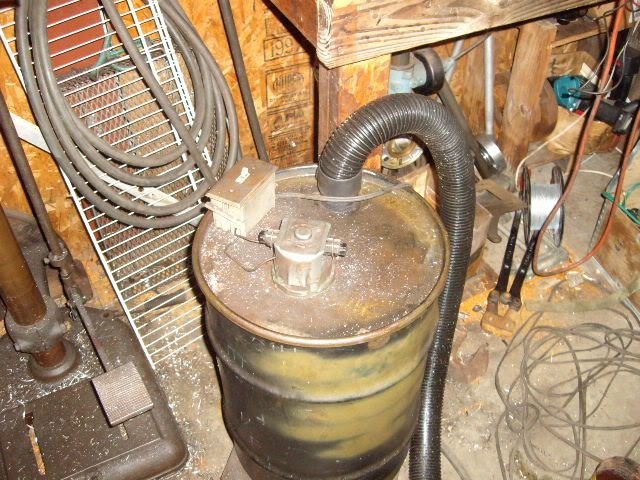
together again
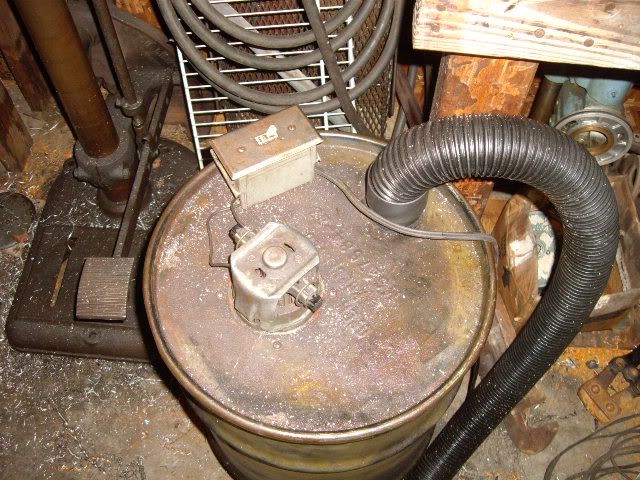
after testing, still smoking, no swarf.
I had a conference with "the boys", and some of them, knowing bertha was around long before they were, thought she ought to at least get a chance at life support, so I dug around, found another motor scrapped out of another vacuum, and pulled out the old one, putting the shop vac on life support.
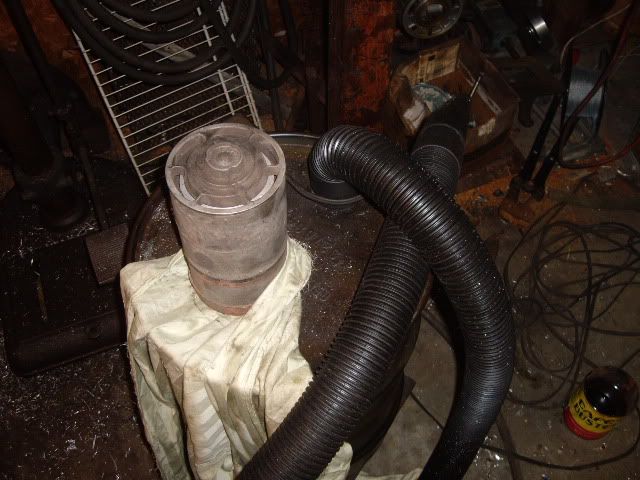
first test, passed with flying colors, she might make it back to the land of the living. With a temporary filter of a layer of rag, she'll just need a couple of modifications.
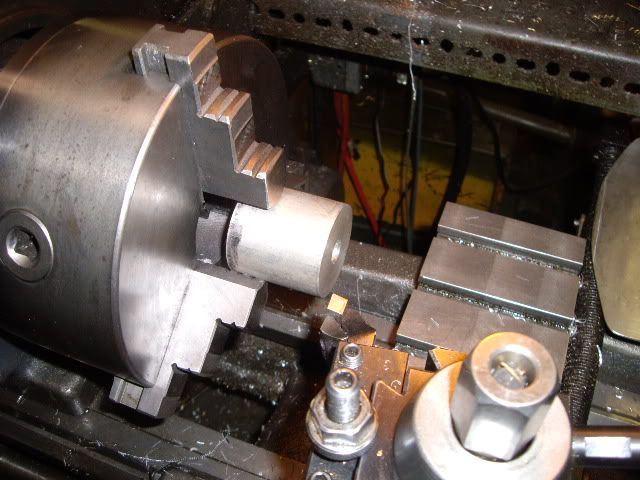
turned a plug to fit in the crank structure, so it'll hold tight in the vise without distortion
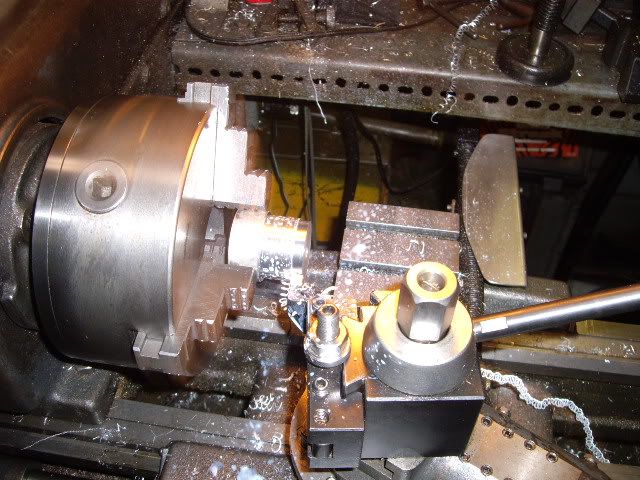
first cuts on the plug
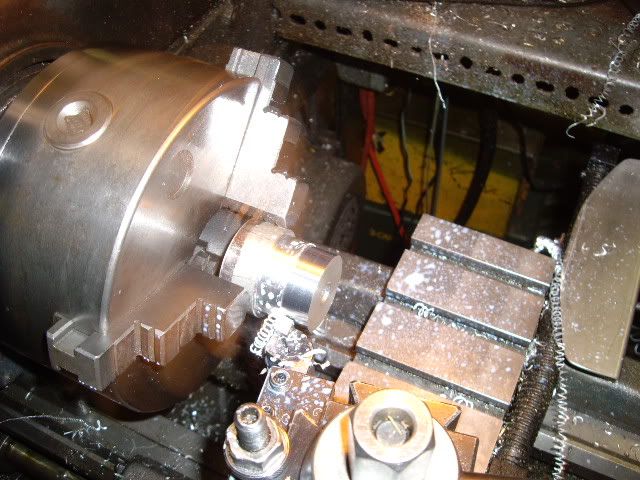
more turning, the blank is inch and three quarters, the bore of the crank support is 1.375
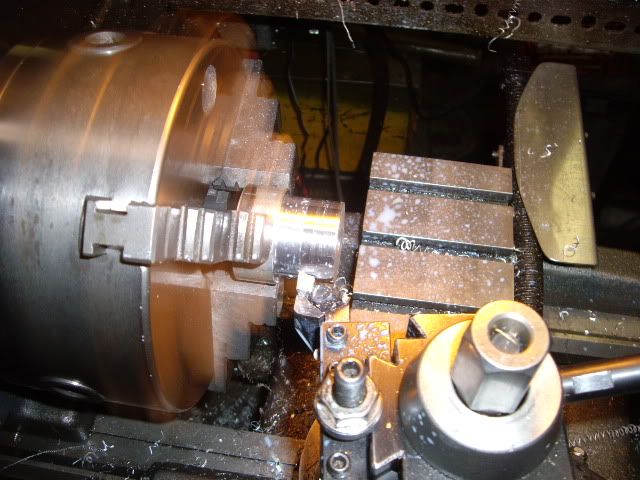
final cuts for size, the support is a very snug fit
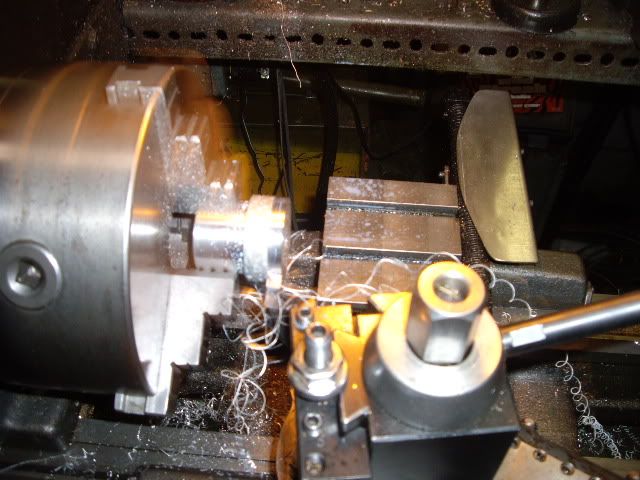
Flipped the plug and reduced the o.d. so as not to interfere in the vise
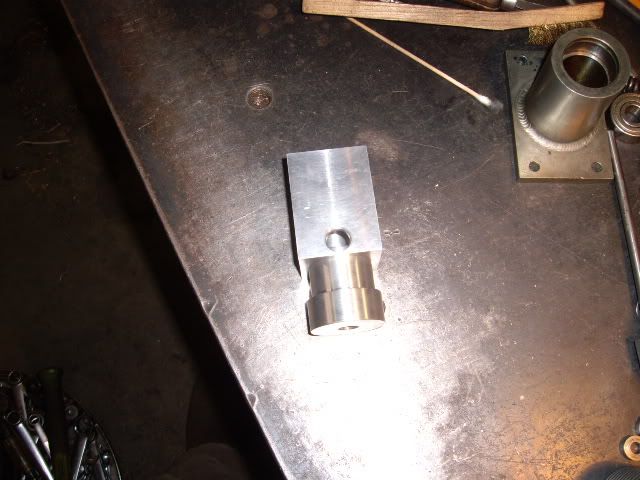
plug in place, should support things just fine
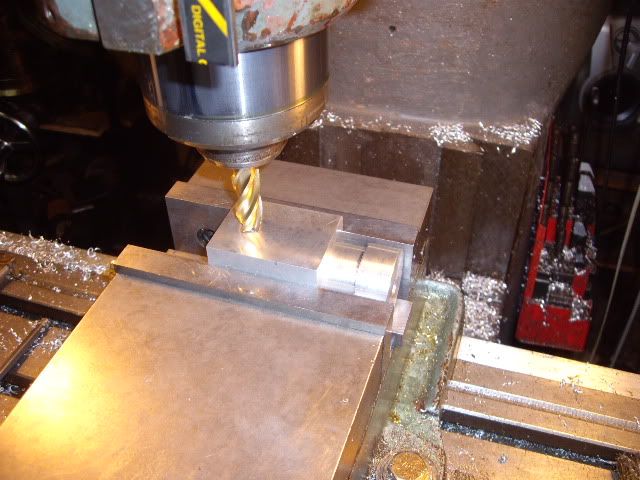
first cuts on the first end face
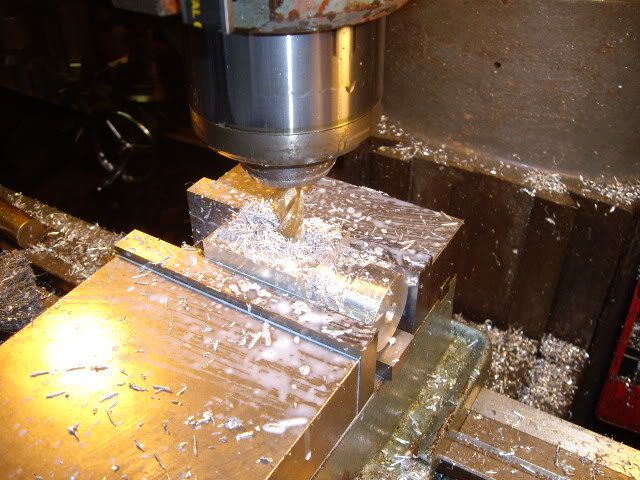
plunge cutting, all the way into the interior with a 9/16ths in end mill
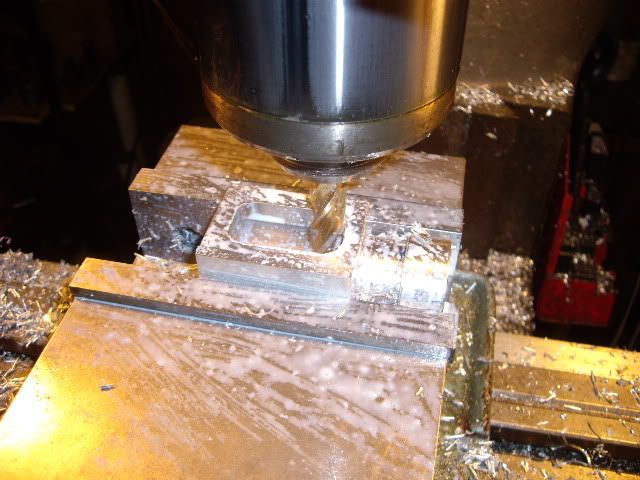
using the end mill, cutting out a rectangular opening

having flipped the support, milling the other end, cutting the rectangular opening
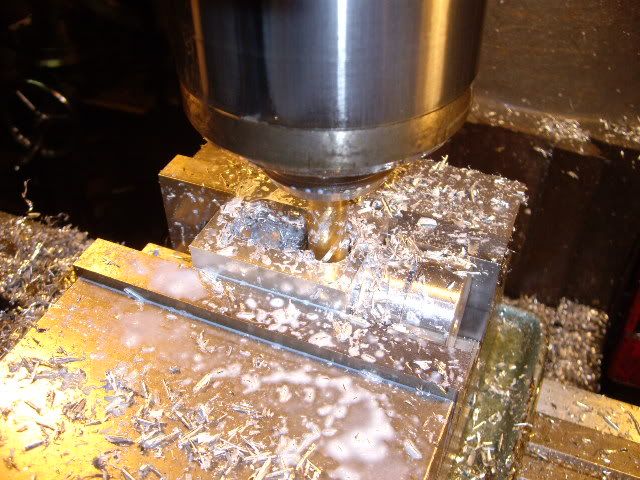
flipped back, final cuts for the first end, opened up fully
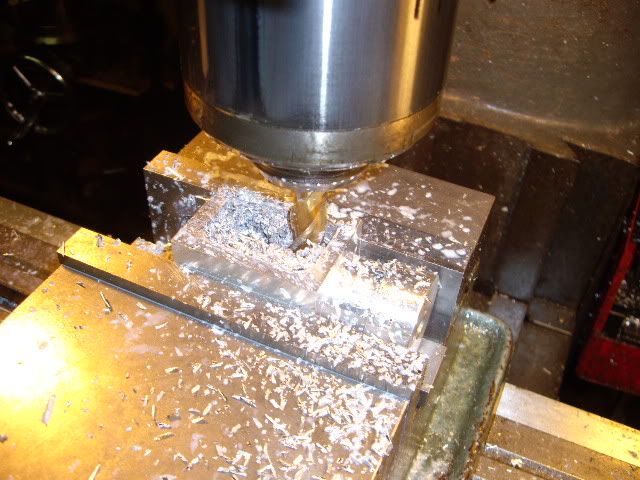
flipped again, final cuts on the second end, fully opened up now.
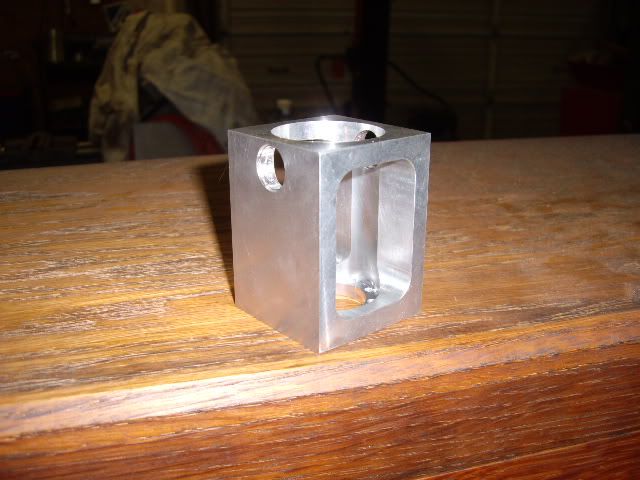
the support, open now, ready to be profiled to shape
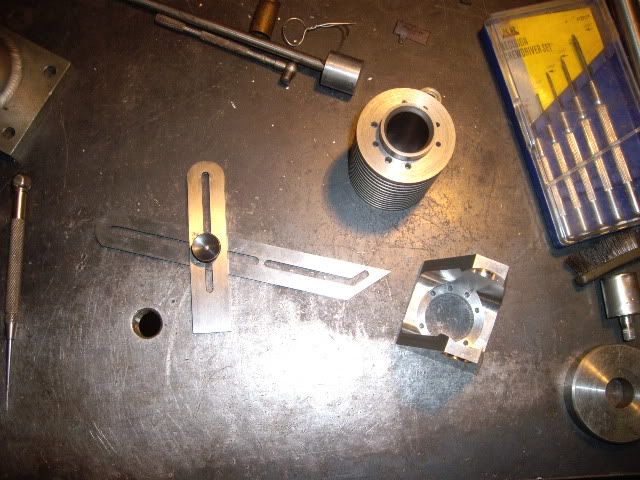
I want to lay out the sides, no special angle, just connecting one point to another, with a gauge so both sides are the same.
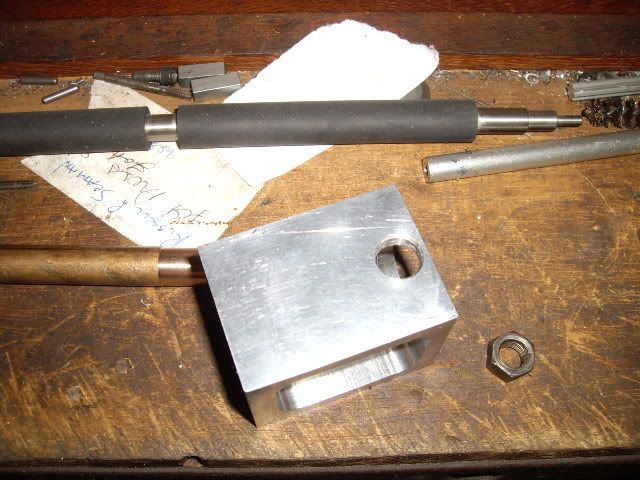
with the angle scribed on both sides, the set up in the mill is by eye, setting the slitting saw right on the line
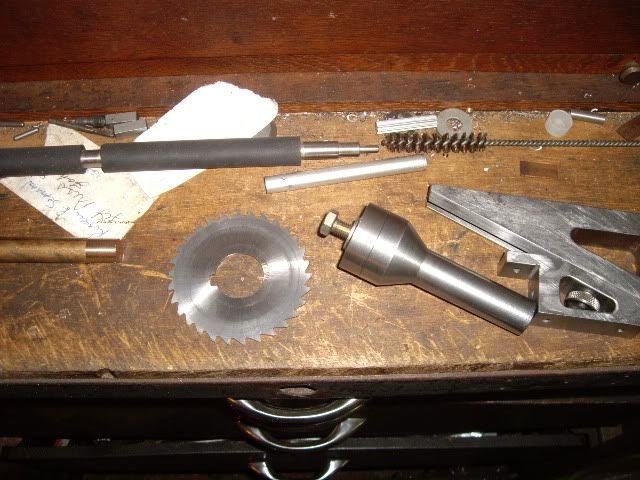
the slitting saw, .062 thousandths, and the arbor, with a .750 inch shank
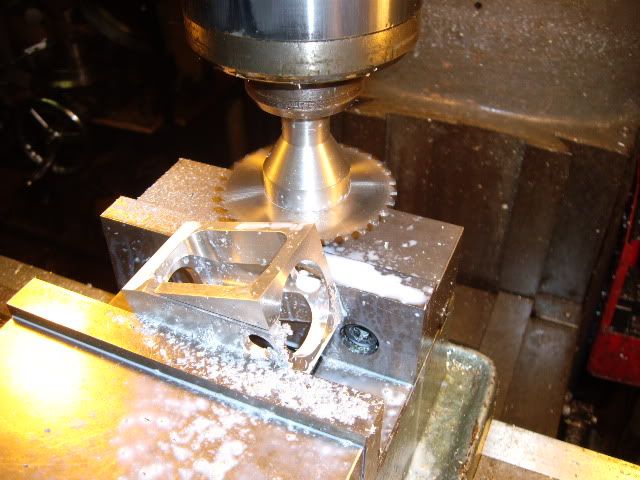
having taken two cuts on the front side, I'm taking a cut on the back side, two to remove the meat, a last one to take out the smallest bit holding the scrap in place
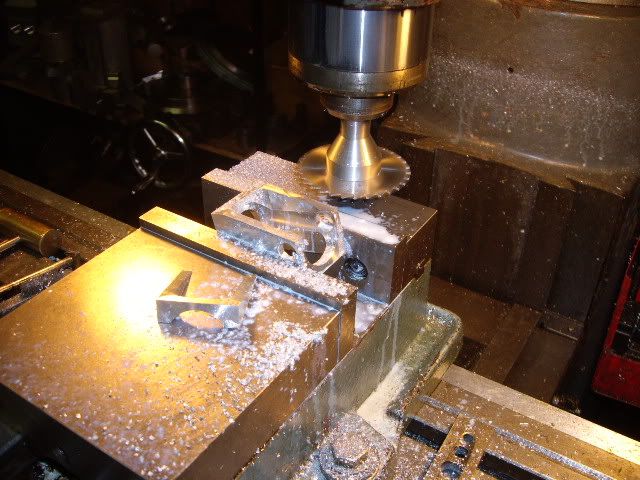
the last cut on the back side, the scrap piece flips onto the vise, just right.
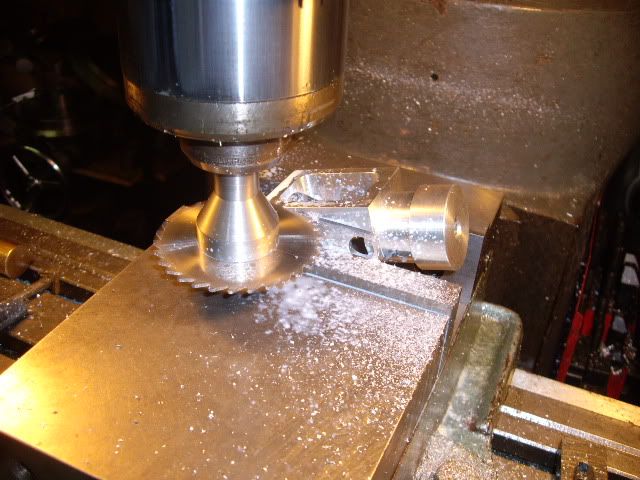
having added the plug again, starting to cut the second side out, no support except the plug for this side.
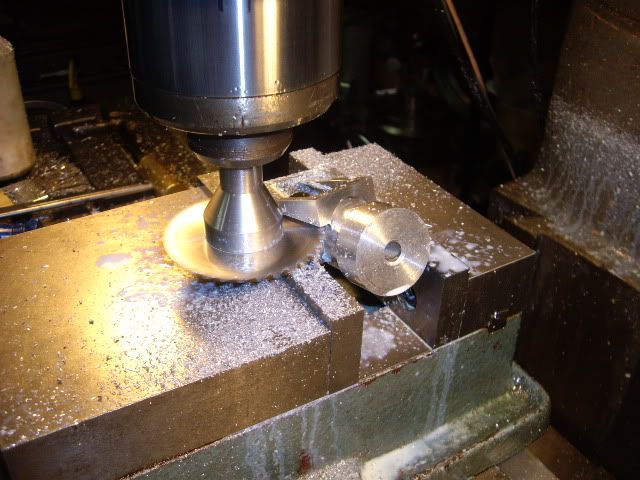
working the same as the first side, taking the final cut to take off the last piece of scrap
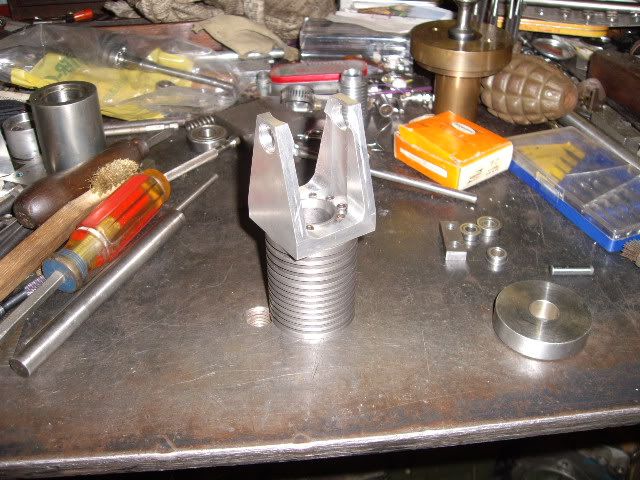
the partially finished crank support, sitting on the cylinder, side view
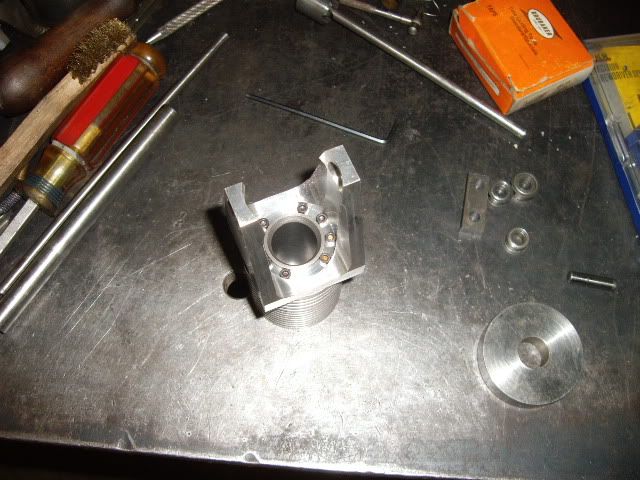
another view, from the top
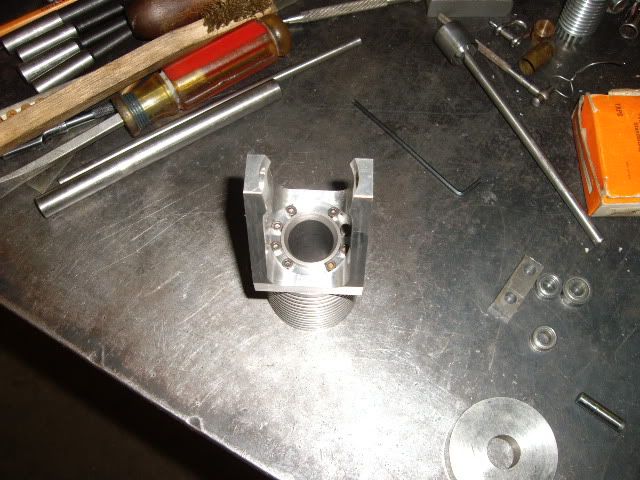
With the crank support bolted in place, you can see the space for the crankshaft to turn in, the next step will be to cut the support in two, so the two sides can have bearings put in place and slid over the mainshafts, then bolted in place to connect with the connecting rod. Maybe today will bring a crankshaft to a workable state. I'm still not too sure what the stroke will be, hopefully my guestimate worked out, and an inch and a half, double the bore, will clear the cylinder with the rod, even if I have to beat (forge) it into submission, I mean into shape.

mad jack And remember, only mad dogs and Irishmen go out in the noon day sun
