Hi all, getting further along, I don't know why things work out the way they do, Nick, I think the "poppin" works freely because there is almost no friction with regard to the valve, as only the swivelling of the shaft in its bearings, and the slight pressure at the closing of the valve have any real "bearing" on the friction issue. I know that valve friction is important in the Duclos flame sucker, because I've tried several different valve types and have reverted to the spring pressure bronze plate with the tiny slot as the freeist moving.
On this engine, I was struck by the nature of some of my scrap, I knew I had a piece of metric ground shafting, small, and with two sintered bronze bushes which came out of a CD player, and I found the box with the scrap from that old player, and the light lit up. First, I had to get rid of the stainless flywheel, so I got to work on the cast iron one
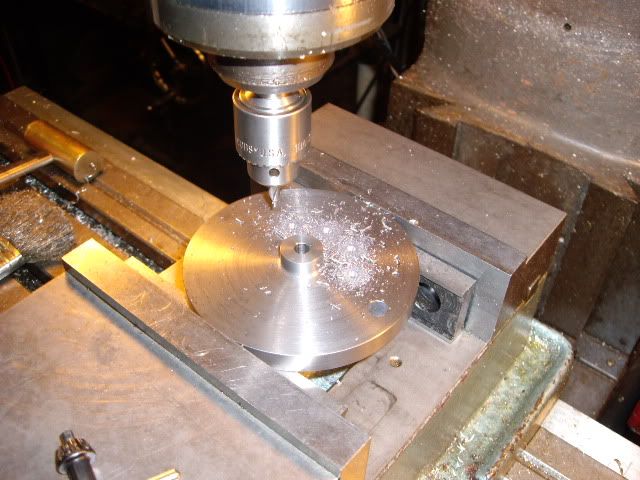
center drilling the iron flywheel for nine holes
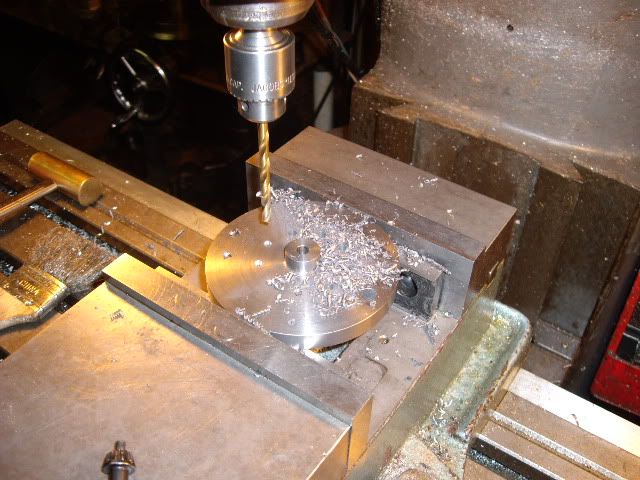
step drilling my way up to size
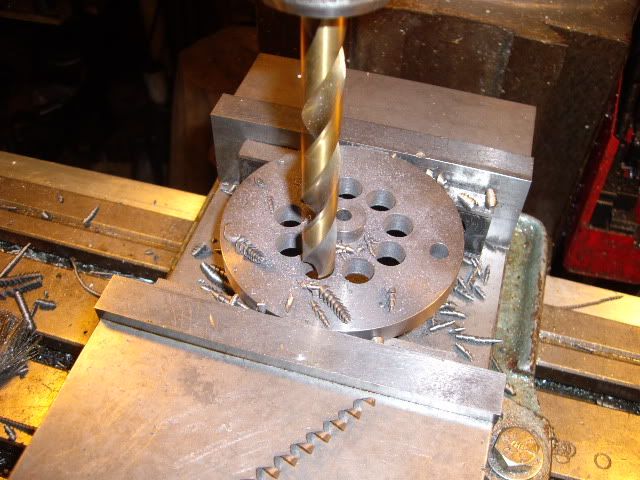
a half inch set of holes is all that would fit where I put them, but it seems like a good flywheel, on just a straight shaft in the main bearings, the flywheel stops at random, so it's pretty well balanced as is
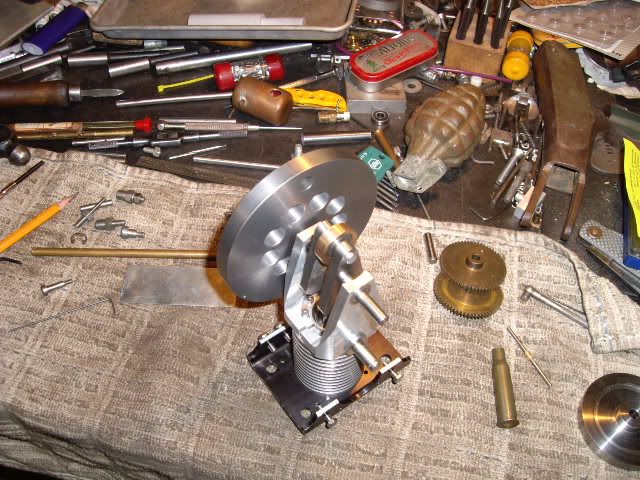
the flywheel in place
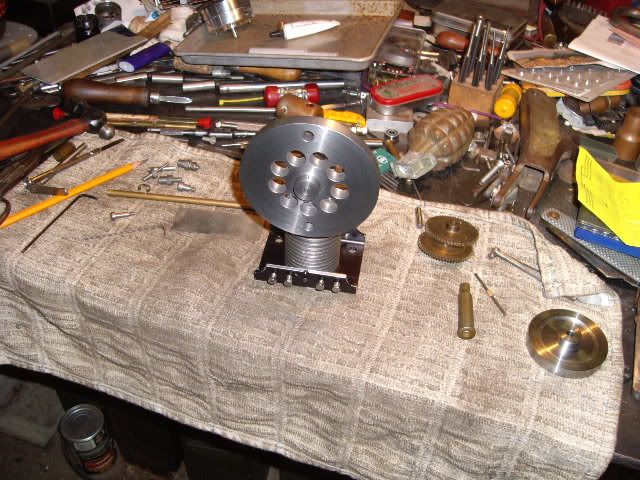
a frontal view of the flywheel on the engine, note the second "extra" hole, put in to balance the hole that was already in the gear. that 7.62 by 54r casing isn't just there for looks, it is what I used to press the bearings onto the mainshafts, with the pressure entirely on the inner race to keep from damaging the ball bearings
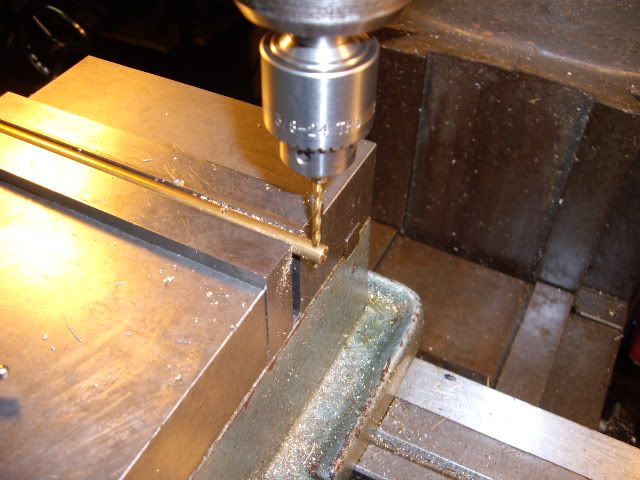
drilling the cross hole in the valve shaft stanchion for the 2.5mm valve shaft, the other cross hole is to the left, in the shaft in the vise jaws
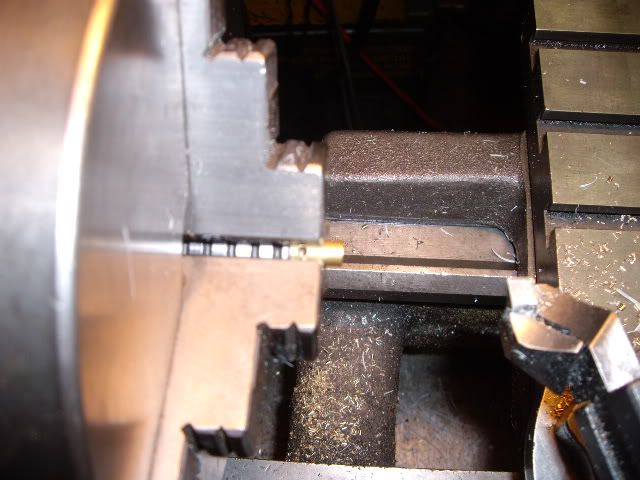
facing off one stanchion to length, measuring from the "bottom" of the shaft hole to the base of the stanchions
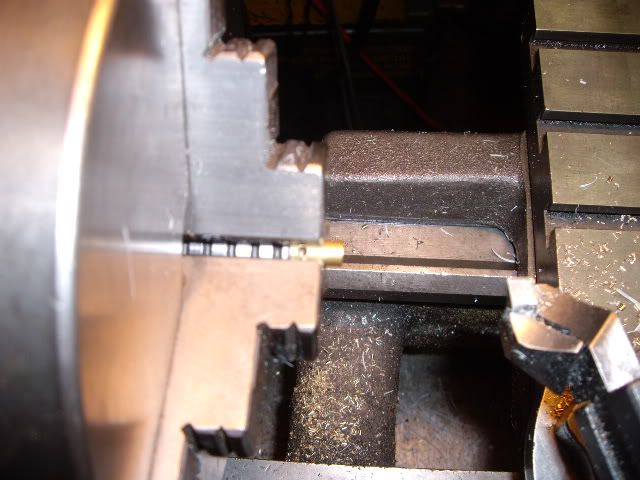
facing off the other to match, both have been drilled and tapped #4-40
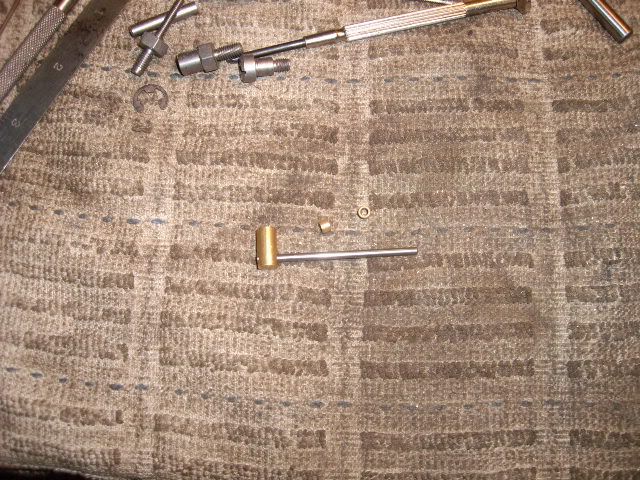
stanchion with valve shaft pressed in place, sintered bushings along side
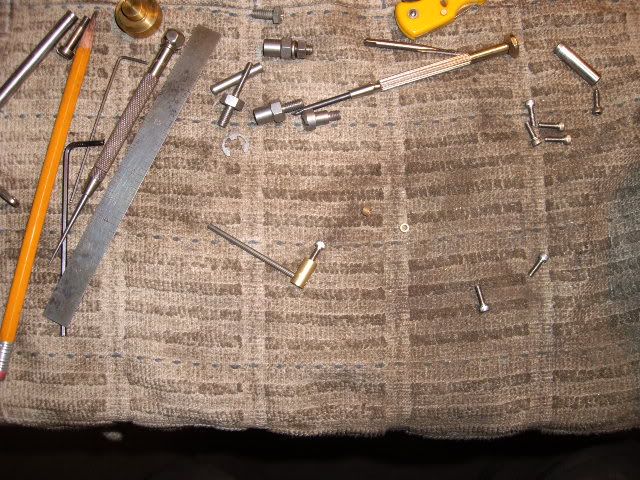
stanchion and shaft with allen screw in the base of the stanchion
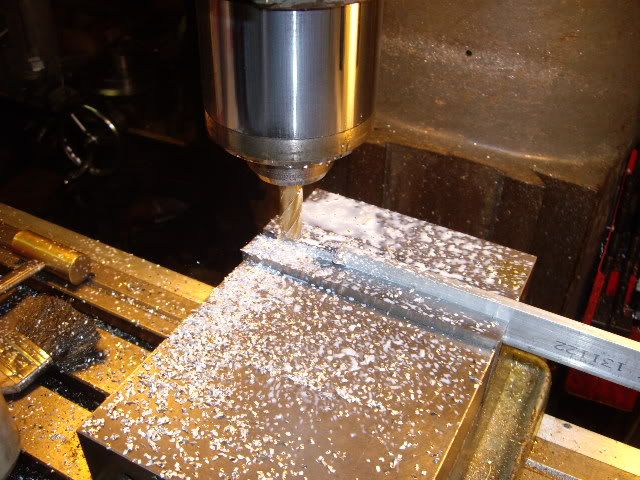
making the valve carrier, narrowing it for clearance

more milling, started with quarter by one inch 6061-T-6 bar, reducing end to 3/4 inch
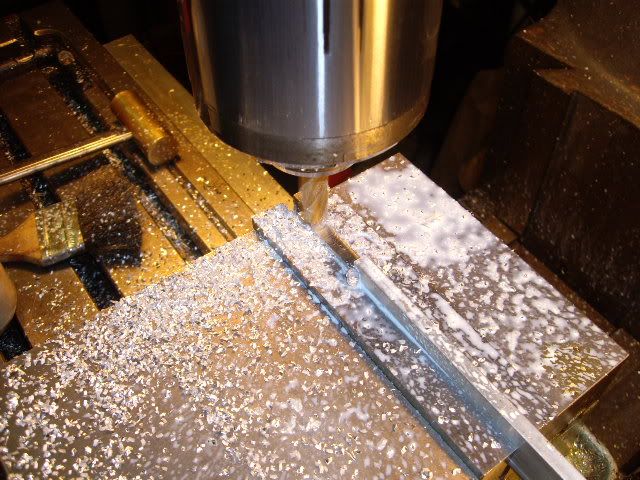
final cut to size, time for drilling for the valve shaft
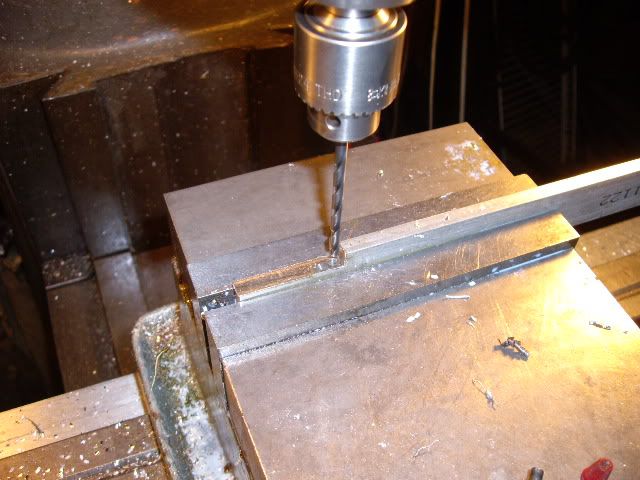
after center drilling, drilling through with an undersized hole
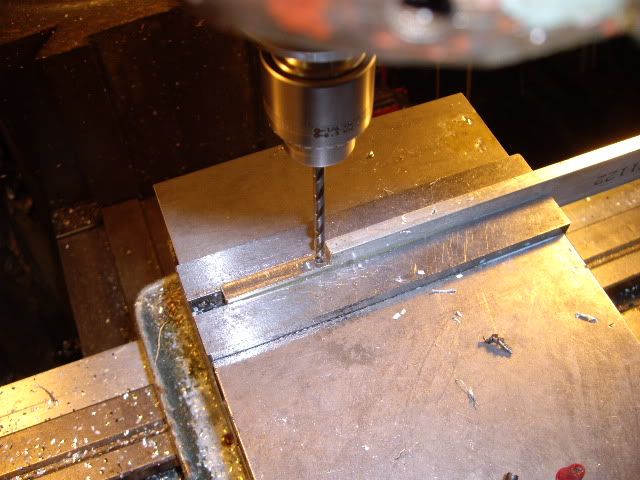
no reamer that size, finishing with a sharp drill on size
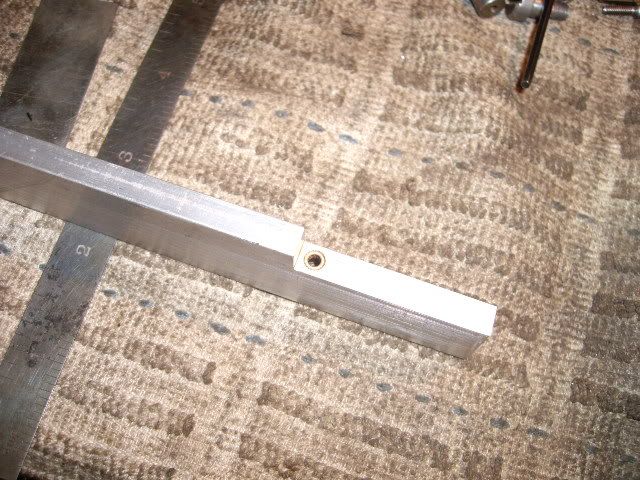
the valve shaft hole with bushings pushed in place with loctite
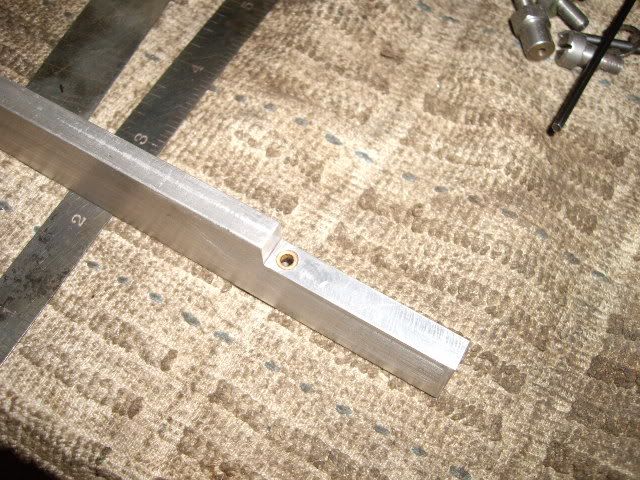
another view of the valve shaft bushings
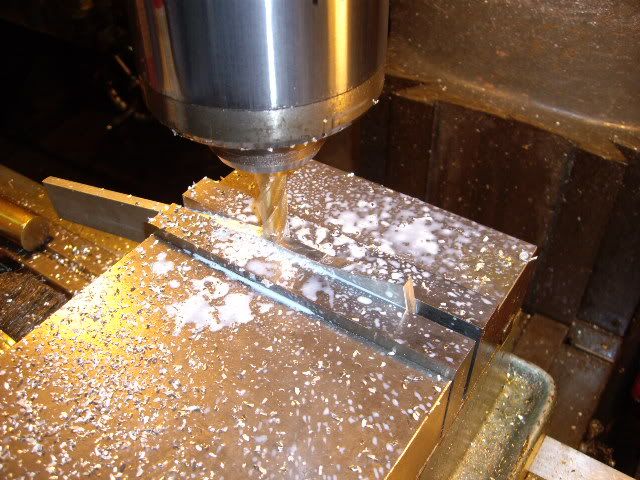
machining clearance in the top of the valve carrier
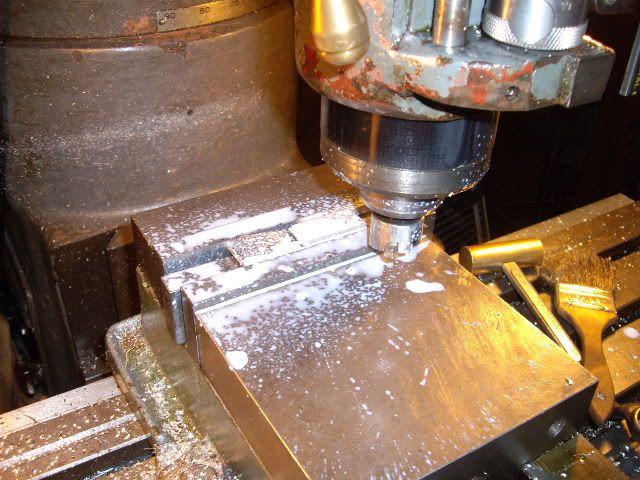
machining down the carrier, making room for a valve between it and the head
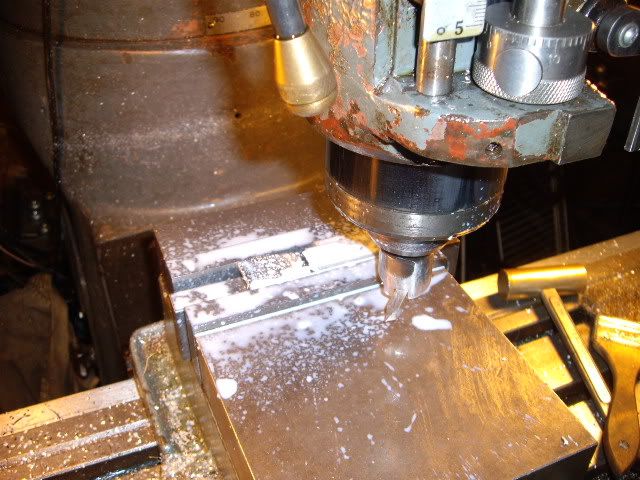
more trimming, with a flycutter, holding the carrier by less than an 1/8th inch in the vise
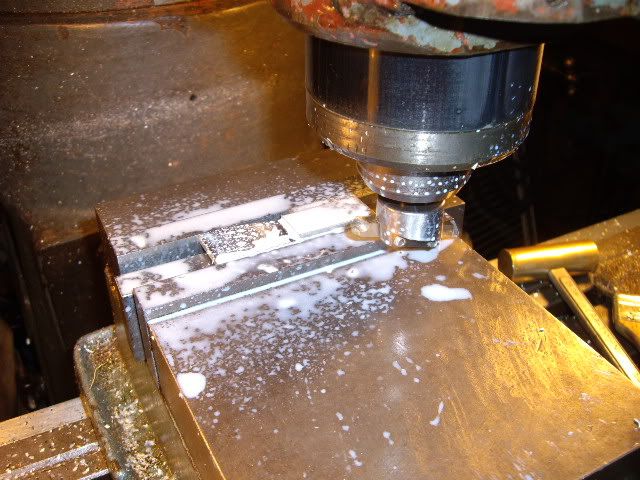
taking finishing cuts, checking for clearance against the stanchions and head surface for reference
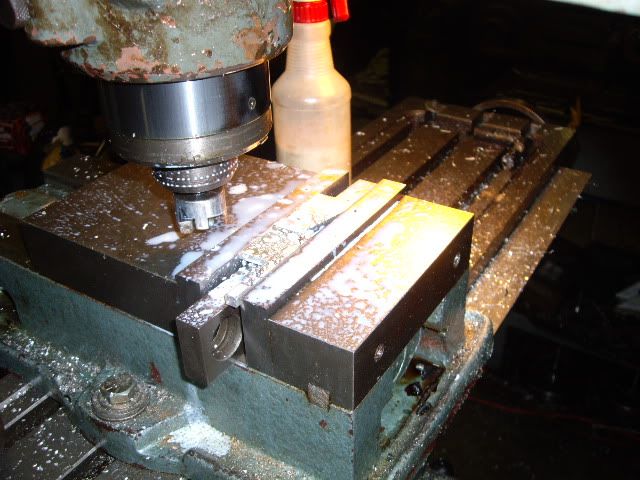
finishing the other side beyond the bushings
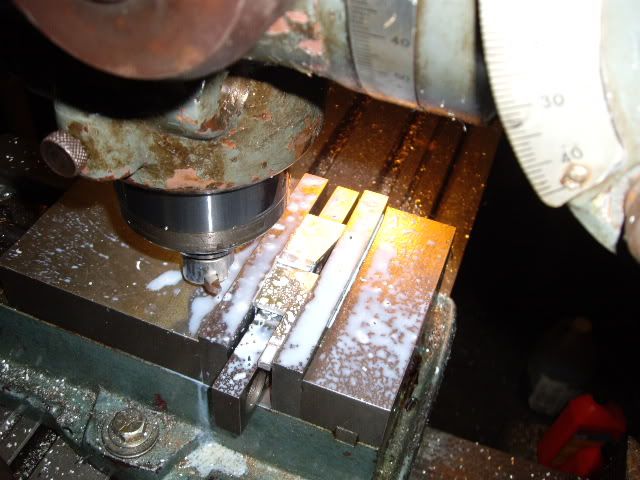
final cuts over the bushings, to ensure they clear the head in action as well
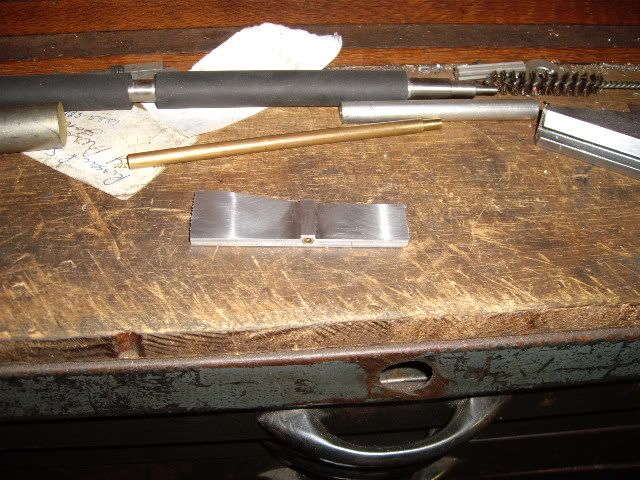
the valve carrier blank
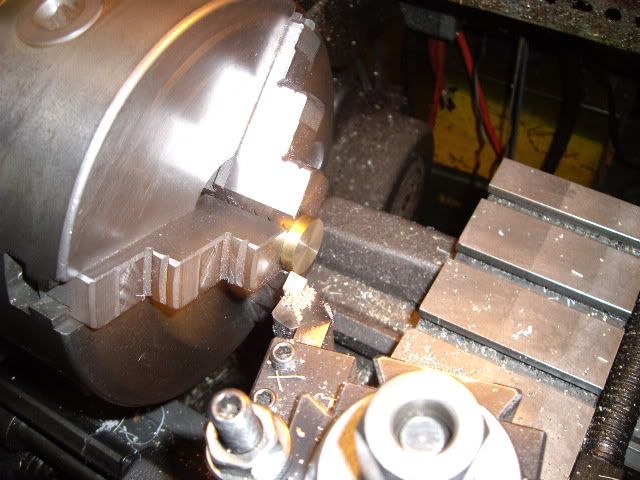
finding a piece of bronze .875 in diameter with a spigot on it, I turned down the spigot to a quarter inch, and chucked on that spigot to face off two thirds of the thickness of the valve
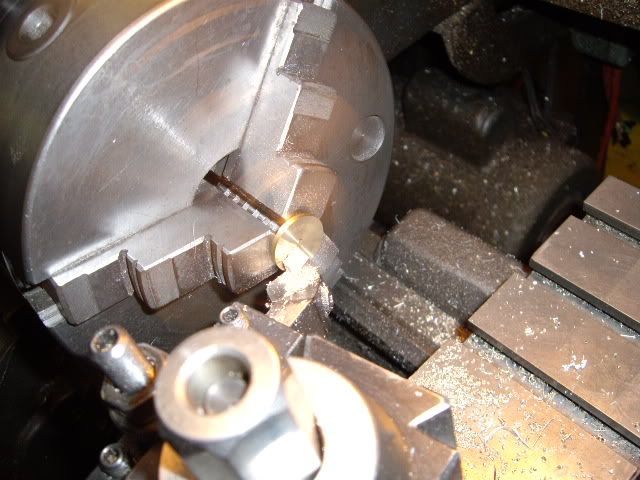
more facing, final thickness will be .090 inches
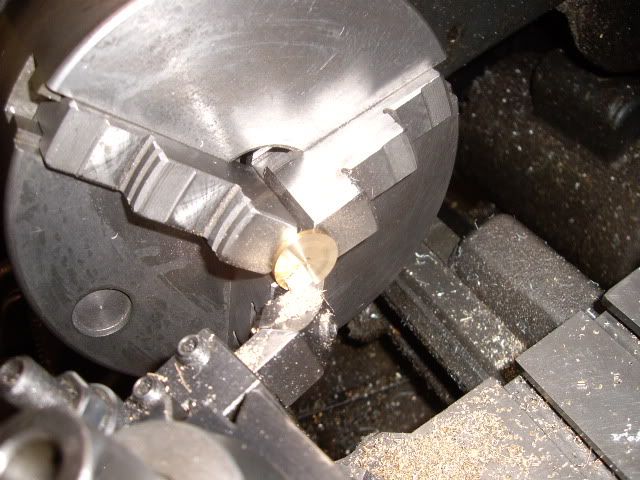
with the valve to size, taking a cut to "hollow" the center to reduce the area of contact leaving a good .200 rim laying flat on the head surface for sealing. the hollow is about fifteen thousandths deep, just enough to relieve it.
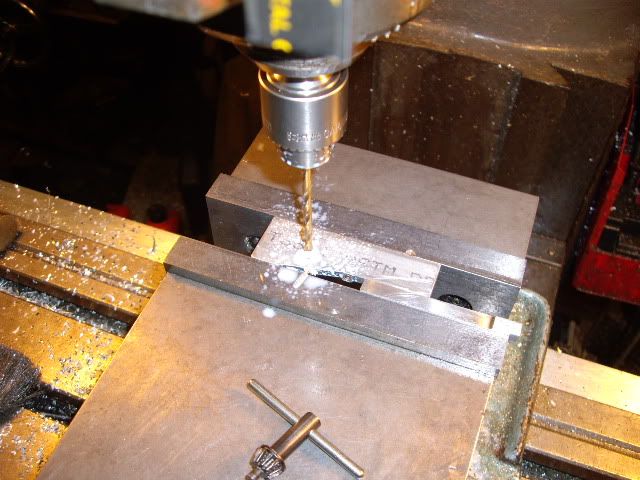
after center drilling on the marked spot, drilling through the valve carrier
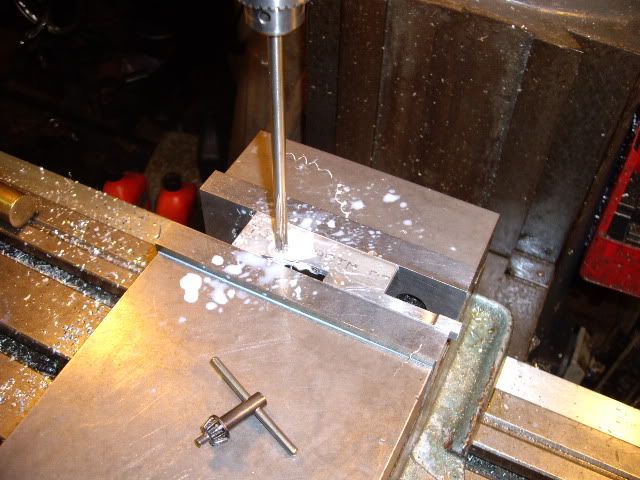
with the spigot on the valve turned to .248, reaming the carrier hole at .250
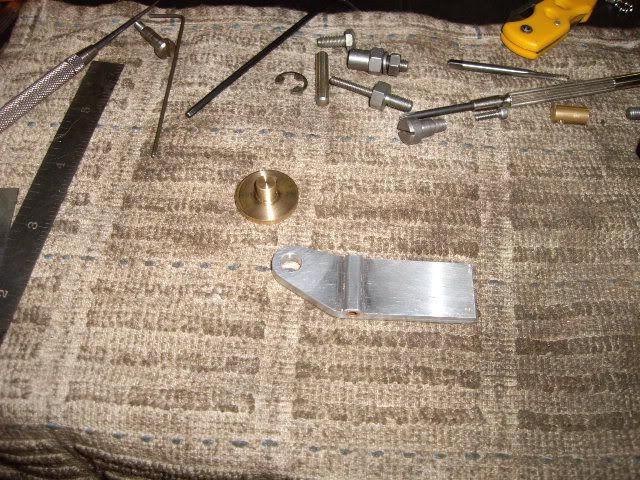
some bandsaw profiling, and filing to a fine finish, the carrier end finished
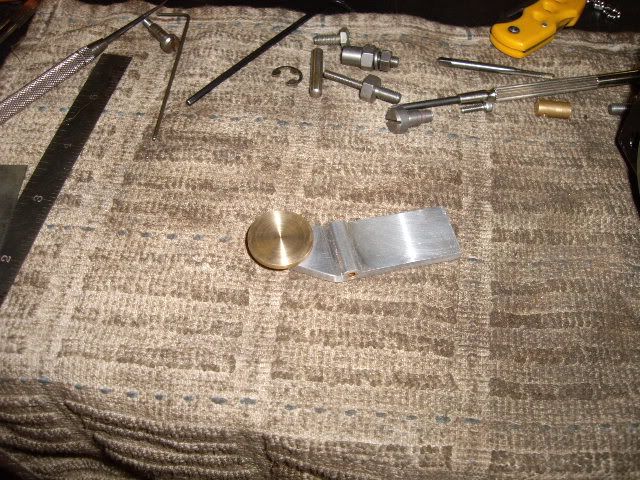
the valve sitting in the carrier
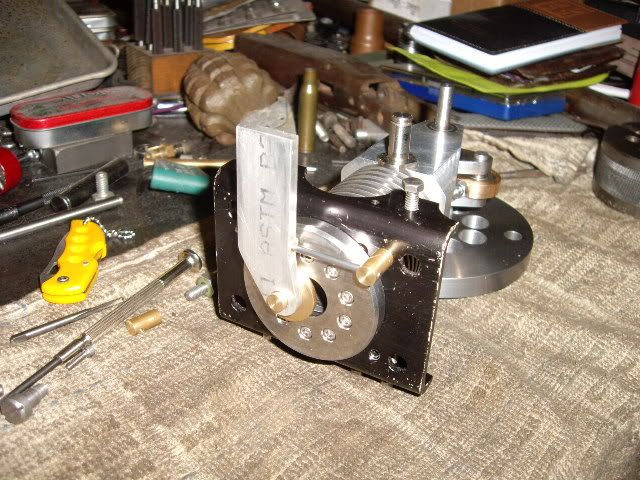
the carrier with the valve, mocked up on the head
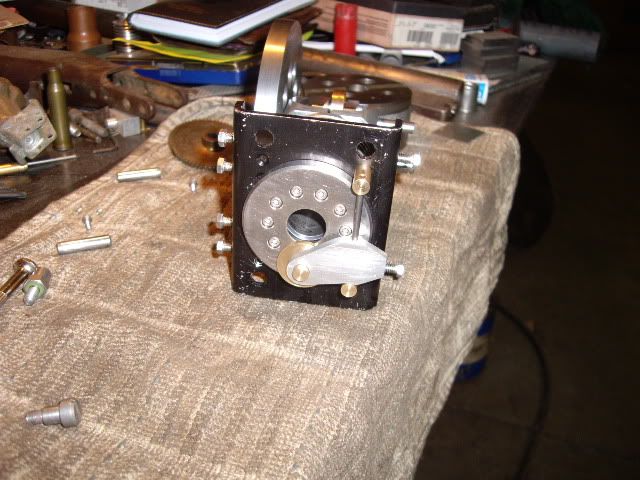
with both stanchions pressed on the valve shaft, with the valve carrier cut to fit, the valve gear fit to the bracket and the valve in place against the head, fitting nicely, freely moving, with a good vacuum seal being the final test. This wasn't exactly what I thought I was going to do for a valve, but it turned out nicely, and fits well, funny how those lightbulbs sometimes don't exactly end up making parts you thought would be there. This valve is inspired by Herr Bettinger and his #2 Flammenfresser, which runs too well not to copy from. Next, I will have to make the operating lever and cam to move the valve in time and space, and maybe look at some sort of frame or something. Thanks for watching and all the comments, I'm having more fun than a human bean is supposed to

mad jack
