Hi Olli, I've just done some more and am now only realising the true size of this thing myself - what have I taken on here?!

Thanks for the advice on sealant, I will have to look into it, it would certainly be an advantage to have something that'll withstand temperature, although I'm not sure what the plastic displacer cylinder will go to!

Got a bit more done today - I bet people can't believe this ... I've been in the garage a few days running!
Started off by finishing the top plate which is combined power cylinder and displacer rod guide on my version. All I needed to do was drill and tap the hole in the right position 4ba - how hard could it be?
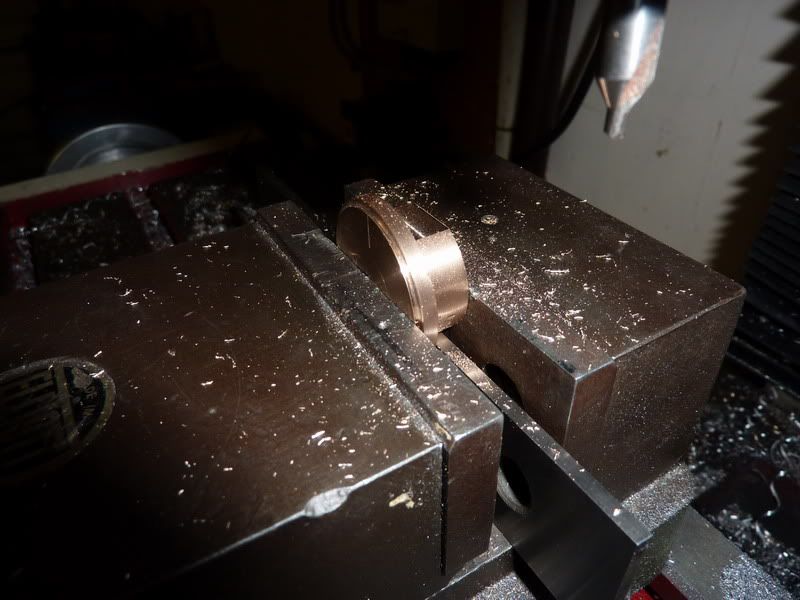
Well, for me very hard apparently - I tried to be clever and tap it in the milling machine under power- normally I do it loose enough so the tap will spin in the chuck - not this time

it stripped the thread straight out!

At one point I was just considering loctiting the bolt in when it comes to assembly but then I realised the other bolt option I had got out was slightly larger- 4mm alen key screw. Won't look as good but it'll do the trick.
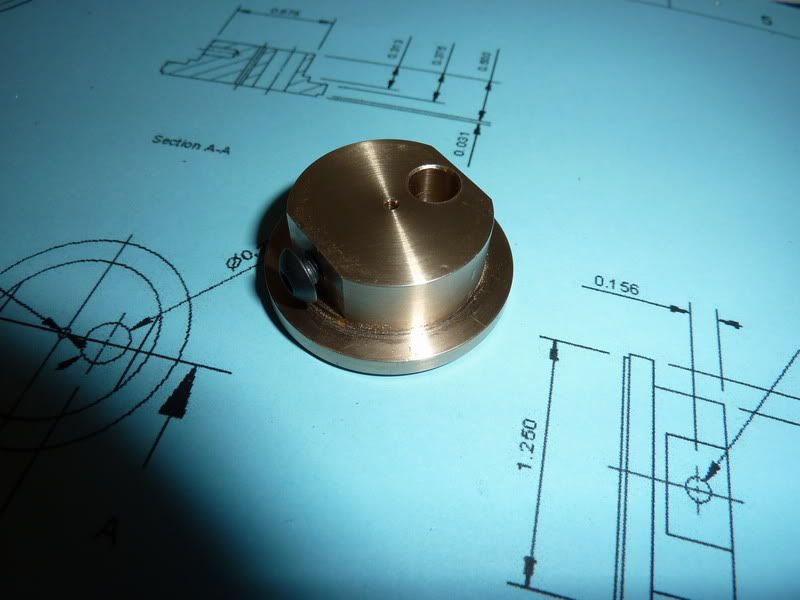
Next I cut the plastic tube to length, I gripped it in the lathe with a bit of nylon I found inside for support and parted it - worked fairly well, just needed tidy it up a bit with stanley knife, take little burrs off.

Unfortunately it's probably not as clear as it appears in the photo, it also has picked up a scratch on 1 side. On the plus side, it is a really good fit on the little registers on top and bottom plate and is actually just about air tight with no sealant at all, but think I'll use something at least on the hot end.
Next I decided to have a look around for some material for the con rods - I couldn't really find much, I had designed it 1/8" wide x 1/32" thick. I found some 1/8" x 1/16" brass strip and thought this would do. The little ends have a slot in them 1/16" wide so there won't be any clearance there - will just have to make sure there is a little. The big end journals are 1/8" wide so plenty of clearance there.
This was the point when I had to double and triple check my dimensions as it all seemed stupidly small!
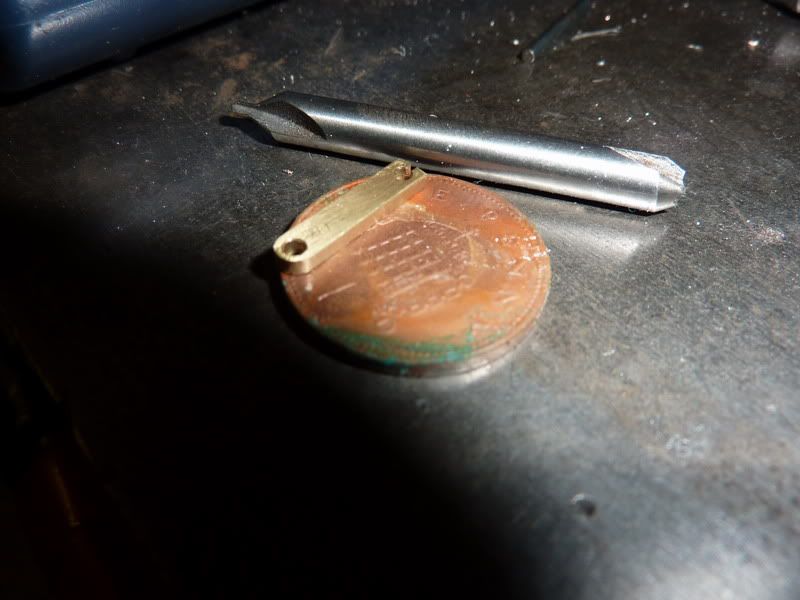
That is the shorter displacer con rod, I have made the other too (see last photo). The only problem I see with these is whether I'll be able to get them over the crank or not - I was planning on turning that from solid. Hopefully they'll bend out enough to slip over then nip back with pliers. I annealed them before I made them to straighten them but may do again to be on safe side.
Here are all the bits so far:
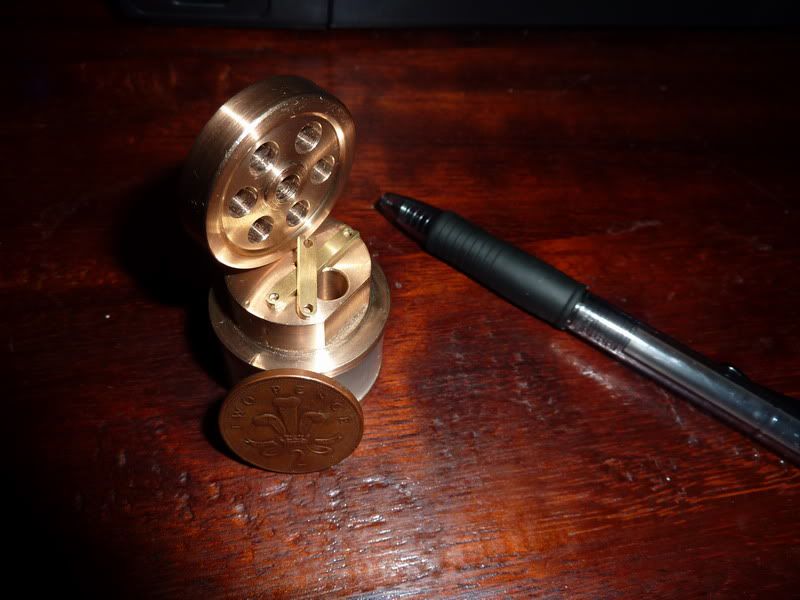
Still got uprights, all rods and pins (they are just cutting to length though), crank, displacer and pistons to do.
Nick