Hi Madjack,
I did the same as you, but at least you didn't just think sticking in packing the thickness off the desired offset would work!

The drawing package I use is called Alibre Design. It's free to download a trial version but there are limitations, then about a year or so ago an offer came up to get the full version for £99 so I hmm'd and arr'd about it for a while and then bit the bullet. I am a design engineer by trade (although we don't actually do that much new design as such at present times) and at work we use a similar package called unigraphics which costs many thousands of pounds, but this little one seems to do all the basics just as well, and in fact it's more user friendly so for £99 it was somewhat of a bargain.
It is a 3D CAD package - not sure whether you have come across these before but essentially you create each individual part in 3 dimensions (models) - starting with a primitive solid (cylinder or cube) or a sketch which is extruded, then adding bit by bit all the features to it. Once you have done all of the parts you then create an assembly or sub-assemblies if required and give them mating constraints to put them together - this comes easy for us engineering-y types because you think about how the assembly works and it gives you a clue as to what mating constraint you need. Doing this correctly has the advantage that the final assembly will be left with the correct degrees of freedom the actual model would, which means you can animate it - for example I can grab the flywheel on mine and turn it over, all the other pieces will turn over with it as they should in real life. This can show up if you've made a boo-boo and get contact, you can get pretty complex with it but I'm not a draughtsman so I try to keep it simple.
Anyway, once you've got the 3D model of each part, the package will then generate 2D views of that part and will automatically dimension them if you wish, I usually dimension myself as the system will probably do it any old how (probably in line with some convention or standard actually but not the way I would do it necessarily). As I said, I've kept my models simple, I haven't put any chamfers or radii on as all this transfers to the drawing and takes up more memory. Also, I don't have a plotter, only an A4 printer so for clarity I can't put mega detail into the drawing.
The reason I got the package is that my scribblings are just too scribbley for me to understand - I'll forget what I have scribbled! When I first got the package I ideally wanted to fully tolerance all the drawings so that anybody could make any part and it'd still go together and work - but that turned out to be a huge job and is not generally seen in model engineering.
Back to the tiny stirling, that was the idea with the thick top plate - the displacer rod guide is relatively long - as you say, helping with sealing, but the rod I had was not ground - just stainless I think and the hole was just drilled with the nearest number drill which I don't think was good enough. On my other stirling I just drilled the guide but It had a screw in bit so there was provision to put some graphited yarn in there and it was ground because it was 1/8" rod rather than 1/16". I'll have to see whether you can get 1/16" silver steel - can you get 1/16" reamers?
My dad just lives around the corner and I know where it is, in his glass book case so your idea is entirely possible!
I think I want to get back onto my poppin flame sucker / licker / gulper next and get those done which are not that far off - the broken machine vice stopped them, then I got
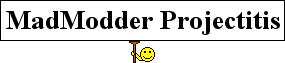
and started jumping about. Then I'll re-visit the stirling as I think it's a nice design (if I say so myself) that other people could do if I iron out these bugs.
Thanks for the interest,
Nick