Oh well, at long last I have a bit more to offer.
Of course, my plan to strap the base to my vertical slide was as much use as an ashtray on a motorbike...the base is the same width! Back to the drawing board.

As you can see, I had to mount the base at a 45 degree angle on the narrow vertical slide mounted on a rotating base. Its funny, you get all these bits when you buy old lathes but it takes some working out how to use them!
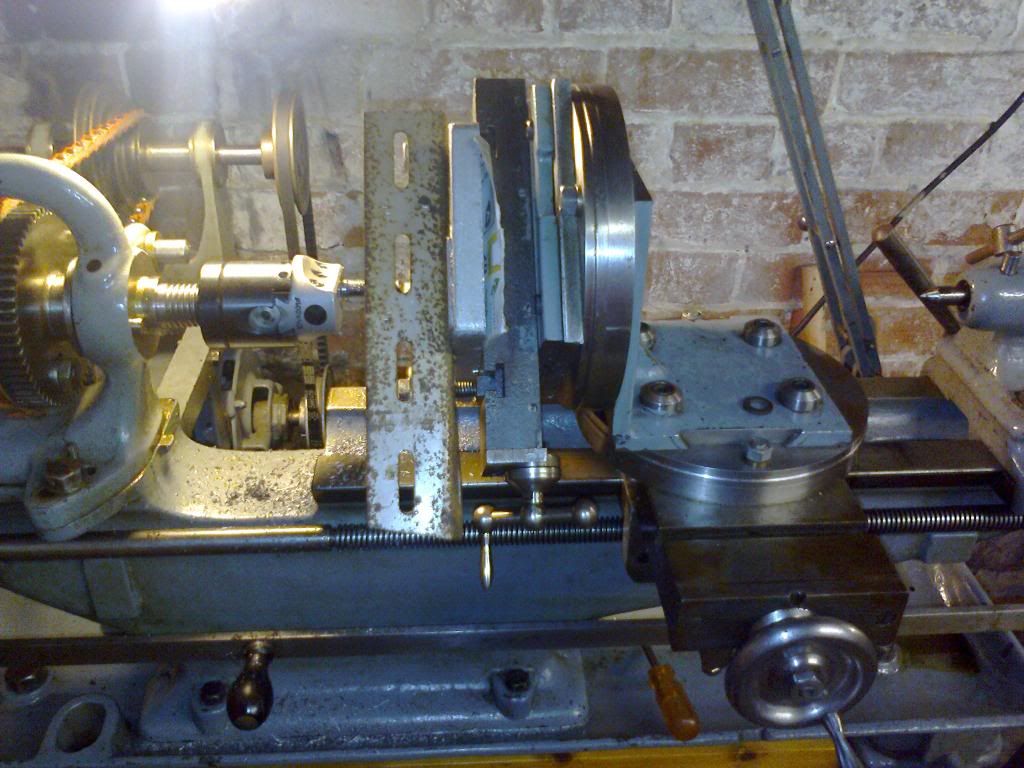
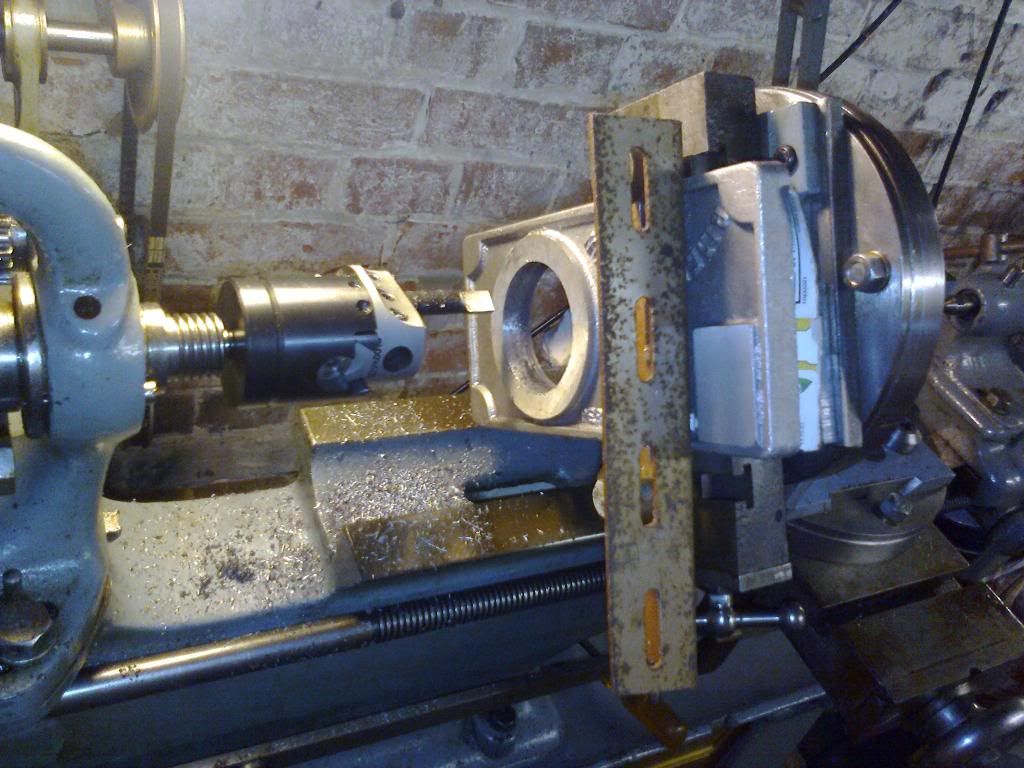
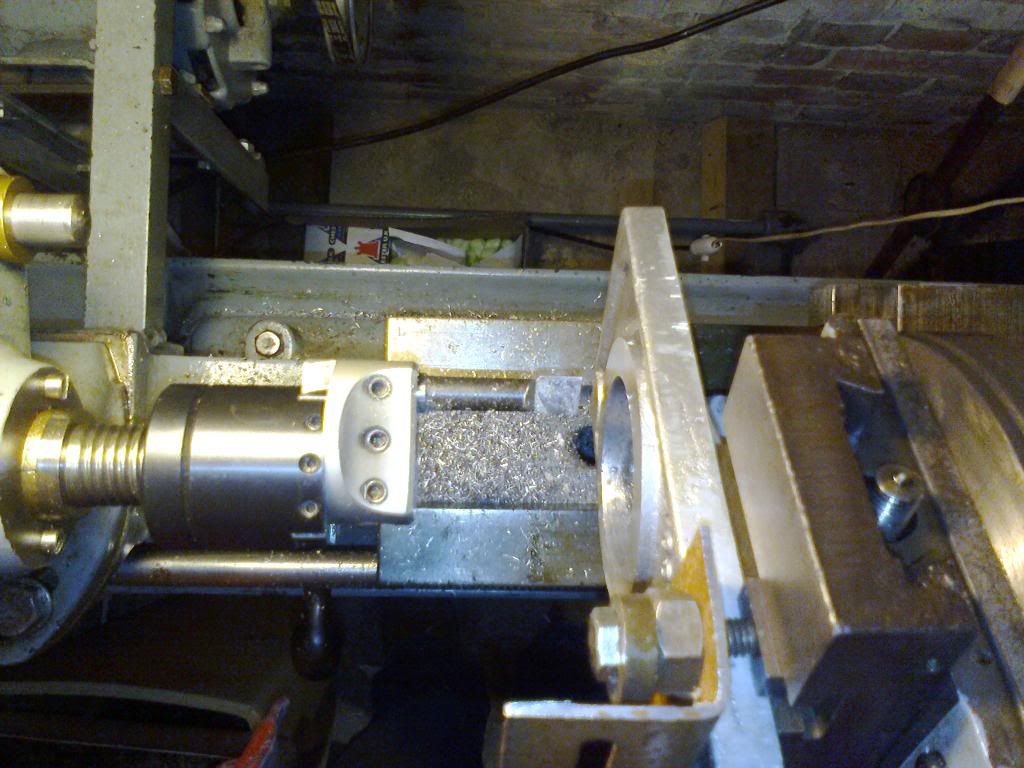
Finally sorted that.
Next trick...the cylinder wouldn't stay clamped in the 3 jaw chuck. Tried holding it inside and out. Kept coming loose.
Hmmm
Went back to the library. Oh look, about a million years ago someone thought of putting paper between metal to increase the grip!

Yes, I know, you all use the trick regularly...well I forgot!

Mounted the cylinder in a 3 jaw and oh look, it works

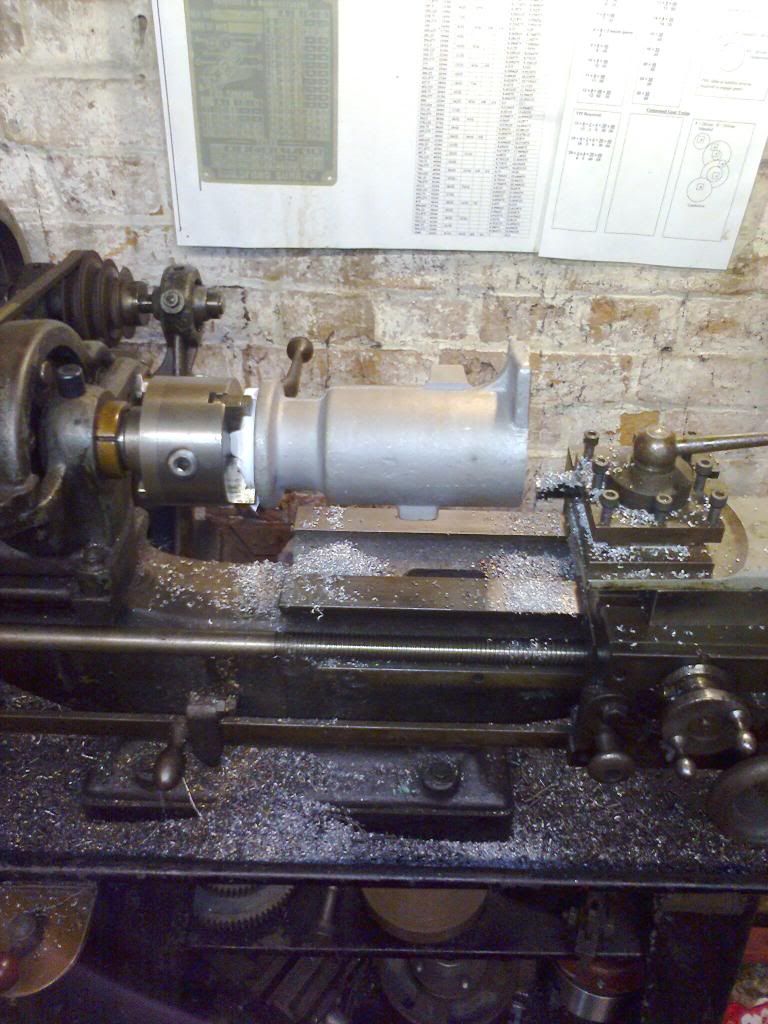
Next comes boring the cylinder. How to mount it? 4 jaw...easy! Oops! 5 inch chuck doesn't have enough space between the jaws for the table. Ok, 6 inch chuck. I sat it togther on the bench.
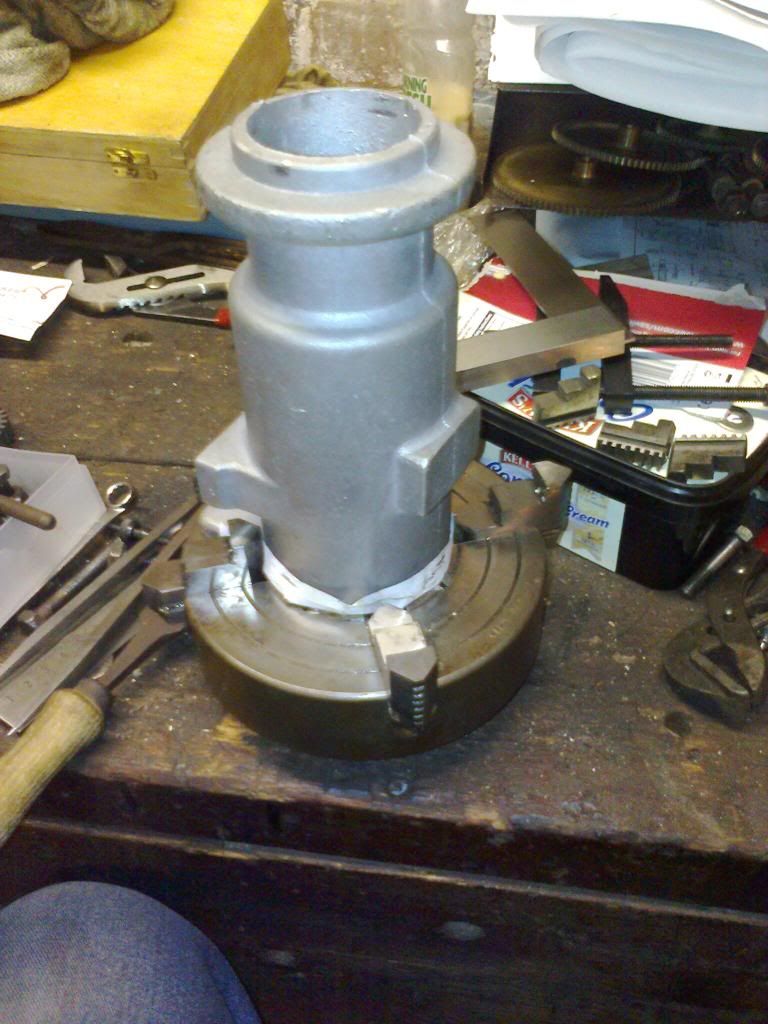
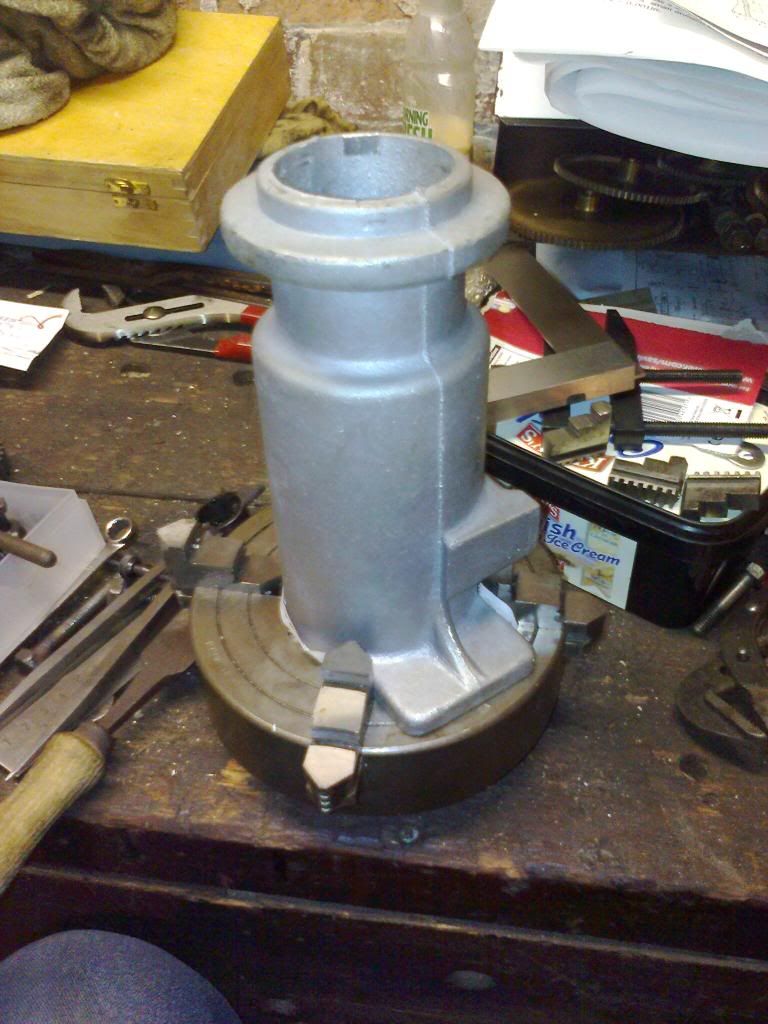
Looks good...er... no. The jaws close on the table by about 1/32 of an inch before centralling.
Ok, try the other way... spent hours looking for a piece of soft metal a the same thickness as the jaw step. Finally found an old copper electrical strap.
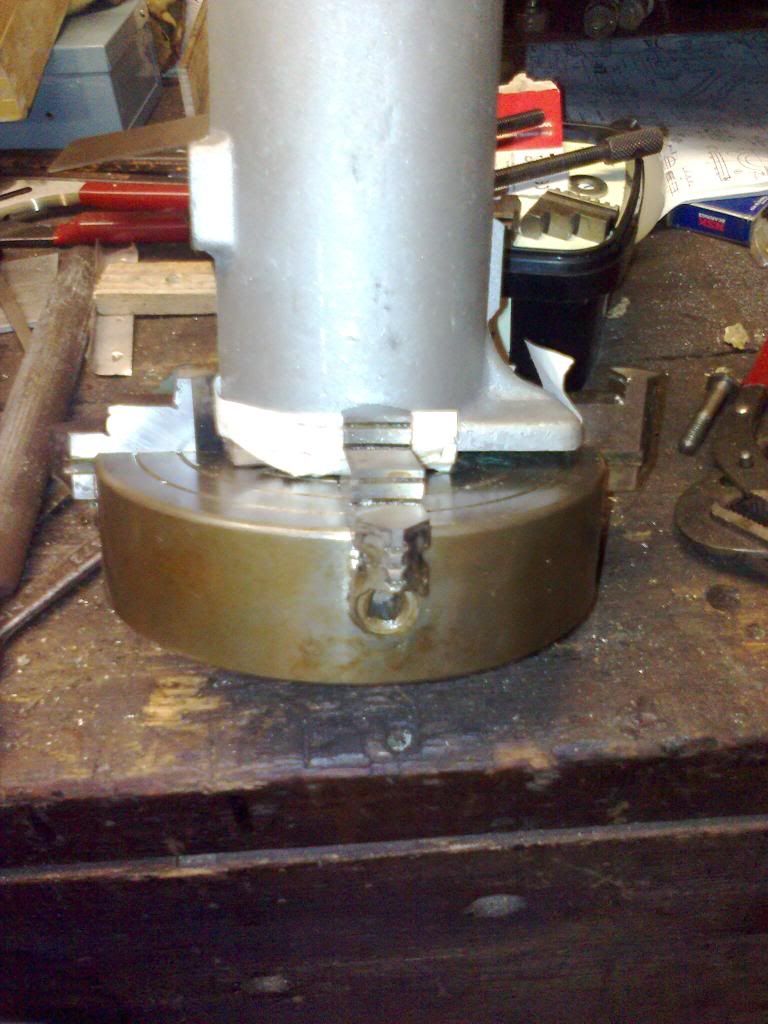
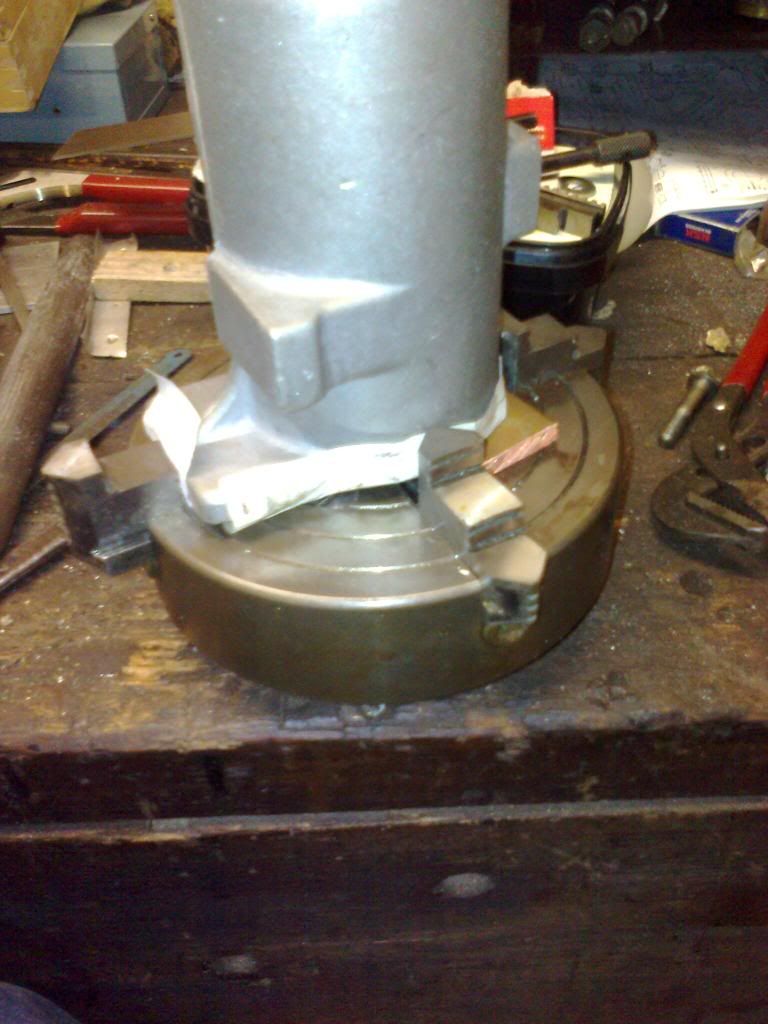
I have put the chuck onto the lathe but ran out of time to set it up properly.
I see now why it takes some people 25 years to build a locomotive or traction engine!!!

Sorry about the slow progress people, I will try to follow what my old school reports complained of...'could do better'!!
