Hi Ned,
That's what I thought, although I have a fair amount of space under my mill if I drop the knee right down. I was hoping to fondle one at the Midlands show but it was not to be...
Accurately finding the centres of bars and bores is what attracted me to them, what methods do you know of for those using a DRO?
I have one and hate it, you spend all day winding up and down. also if the head isn't trammed in precisely so and with a Bridgeport that's all the time with the licorice head 0,0 at 8" reach isn't the same 0,0 at 2" reach.
Find a centre of a bore with a DRO.
Insert cutter [ any size within reason ] into collet backwards, shank sticking out.
Centralise in bore by eye [ preferably good eye ]
Wind in one axis only, say x so cutter shank just touches bore, spindle not running and use fag paper if needed, zero DRO.
Wind to the opposite side and repeat but don't zero, instead press X then the 1/2 button and you will bet the central reading, travle so it reads 0.00 for that azis and lock off.
Repeat on Y axis
Remember to turn cutter round the proper way.
Find centre of a round shaft for drilling or keyway, no tooling, DRO's gauges, etc needed.
Fit cutter into collet, centre on shaft by eye, good eye again, then bring down with spindle running so it kisses the work, retract and look at the tool mark.
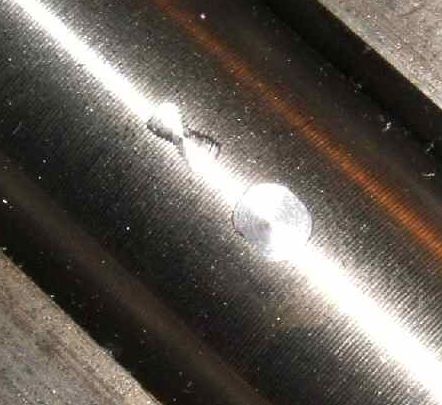
That pip on the left has been put on the shaft using gauges, DRO, Joderell Bank telescope and a Kray computer so it's spot on.
The pip on the right has been put on after the axis has been moved sideways by 0.001" and you can see it's off centre.
Sooo the MK1 eyeball CAN work to a thou.
John S.