Wong, the problem you had with the tool suddenly cutting too much sounds like you had a chip welding problem. When
this happens, a small chip gets stuck to the tip of your tool, and the tool doesn't want to cut. After you get into the cut
a little more, the chip comes off and suddenly starts cutting what you had dialed on all at once.
For getting the holes in the right place on your die stock, you can use simple chuck indexing. The jaws of your three jaw
chuck are spaced just right. Check out the pics.
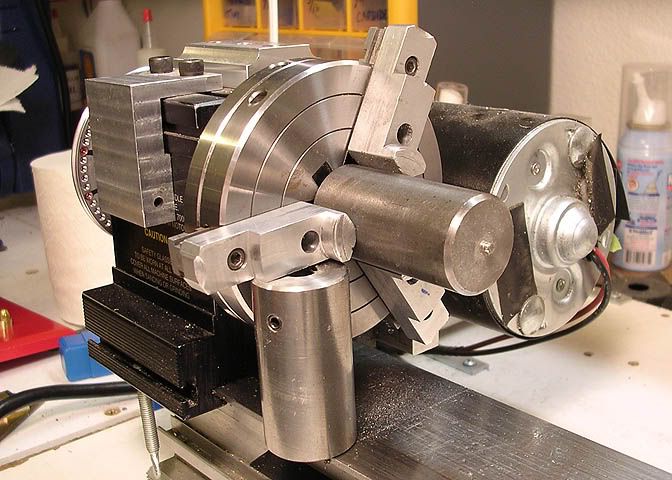
Find or cut a piece of stock that lets one of the chuck jaws rest on it while the piece of metal rests on the lathe bed.
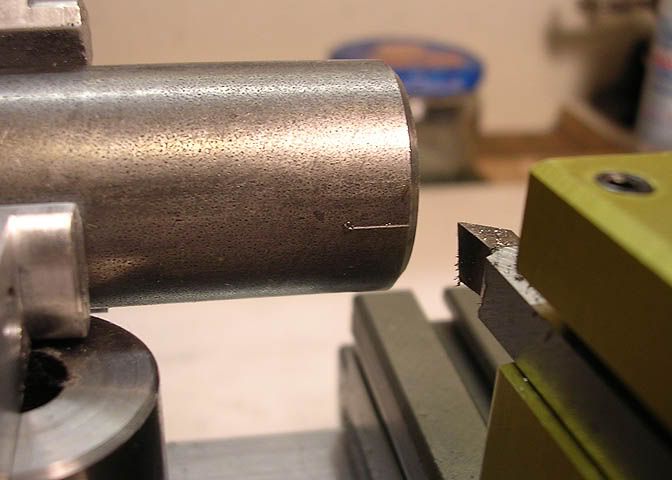
Then use the cutting tool in the tool post to engrave a small line. Just crank the cross slide in until the tool bit touches
your die stock and use the carriage to run it in and make the line.
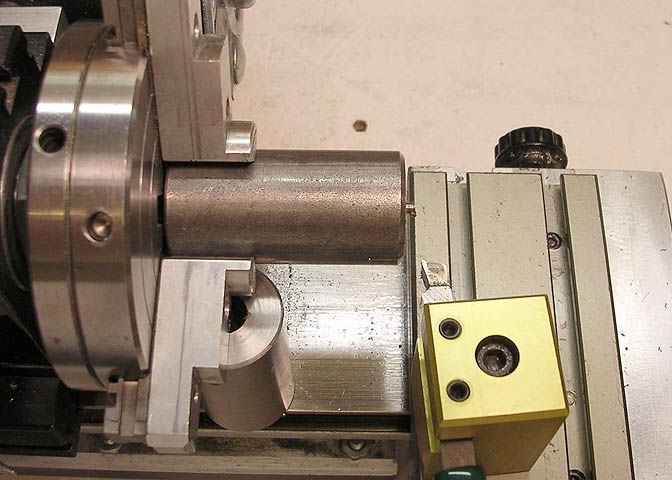
Here's another view.
After you make one line, remove the piece of metal from under the first chuck jaw, rotate the chuck a bit, and do the
same for the next two lines, until you have three lines total. Now you have three perfectly spaced lines.
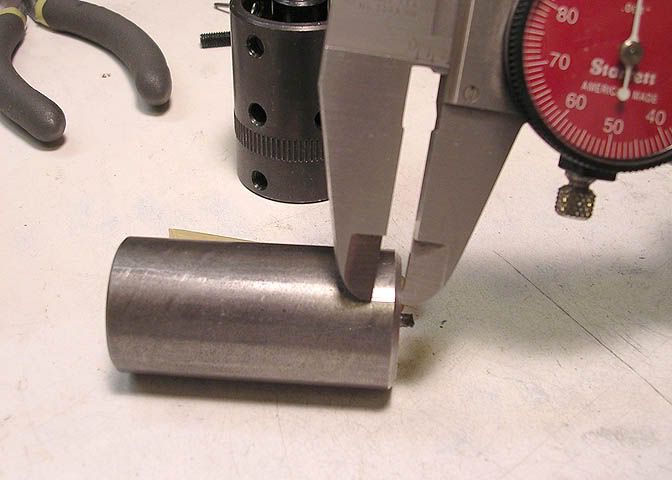
To finish the line, use a divider or your dial caliper, set it to where you want the hole distance from the end of the
die stock, and make a scratch over each of the three marks.
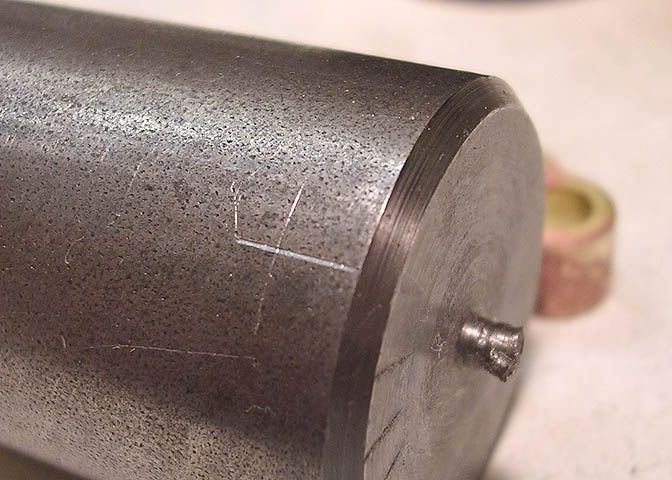
You'll have cross marks like this, and you can use a punch to mark for drilling. Set up your drilling operation carefully
and you'll have the holes done in a minute, and you can tap them.
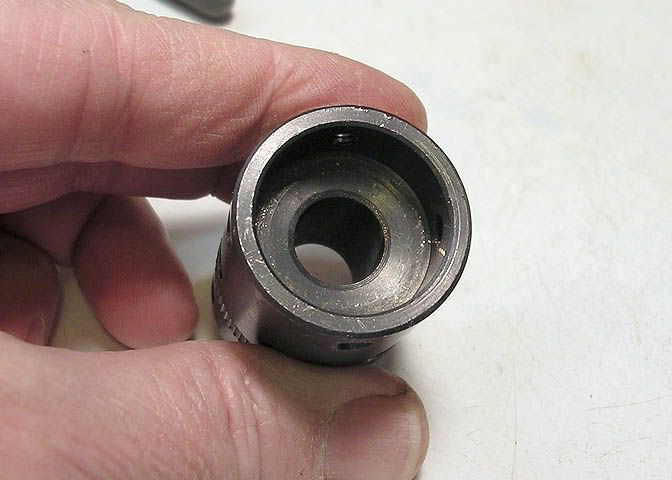
The die stock I have for my Taig lathe has the setup that sonuk mentioned.
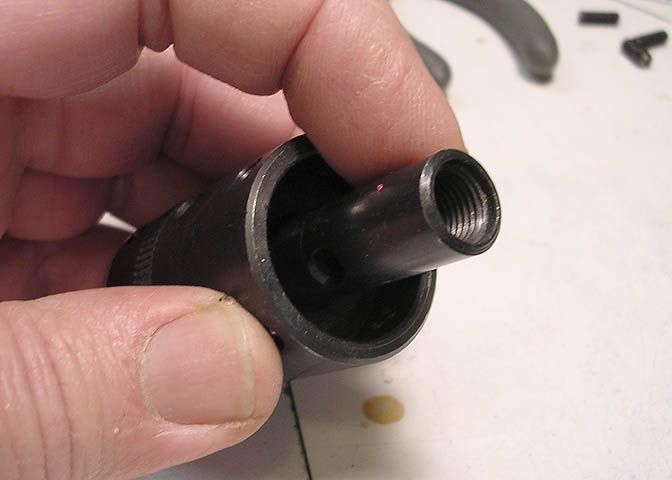
A pin goes through the center and turns freely. The pin can be held in a drill chuck.
I think you would do best not to try to tap a hole in the die stock for the pin. You have a good chance of getting
it slightly off, and you'll have the same problem you started with in getting a good straight thread using a die. If
you let the die stock float on the pin it will be in line with whatever you are using to hold it, like a drill chuck.
Good luck!
Dean