Here are some more Thiel photos.
Firstly a decco into the top of the main spindle feed gearbox. There's a lot of gears in there! A nice detail is that the Y-axis feedscrew in also in there so benefits from a constant oil spray. The Y-axis ways are just visible at the top and bottom of the photo as well as the feedscrew inside the gearbox.
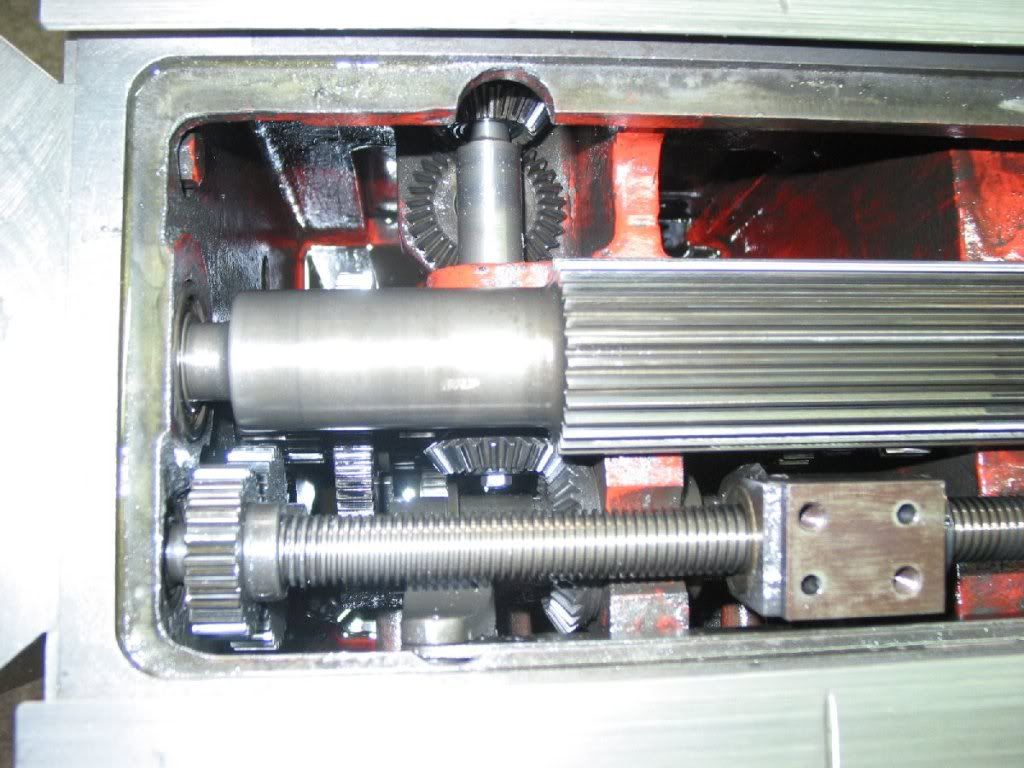
We stripped all of the slides apart and cleaned the dovetails as they were full of swarf and general filth. One aspect of the machine is that all the ways are oil lubricated, but it must be administered to 18 individual push on oil nipples scattered around the machine with the inevitable consequence that it was rarely if ever done. A strange contrast to the excellent scheme for the feedscrew noted above. We have now converted all the oiling points to use modern clip on grease nipples and will use a converted grease gun to oil regularly.
Another problem was that the each of the two gearboxes were both empty of any oil. They are built into the main body of the machine, but are in separate isolated chambers. We obviously filled them to the correct level and it was instantly obvious why there was so much oil in the suds tank, the oil ran out almost as fast as we poured it in so we stripped the side panels off to investigate. This is not as simple as it appears because the gear selector slides overlap the lip of the hole preventing the cover from coming straight off. However, the cover cannot be moved sideways to let the selector slides to clear because of the rapid feed actuating shaft passing through the cover. That shaft cannot simply be removed either....
So it's actually a matter of starting from the other side of the machine, remove the plain cover,
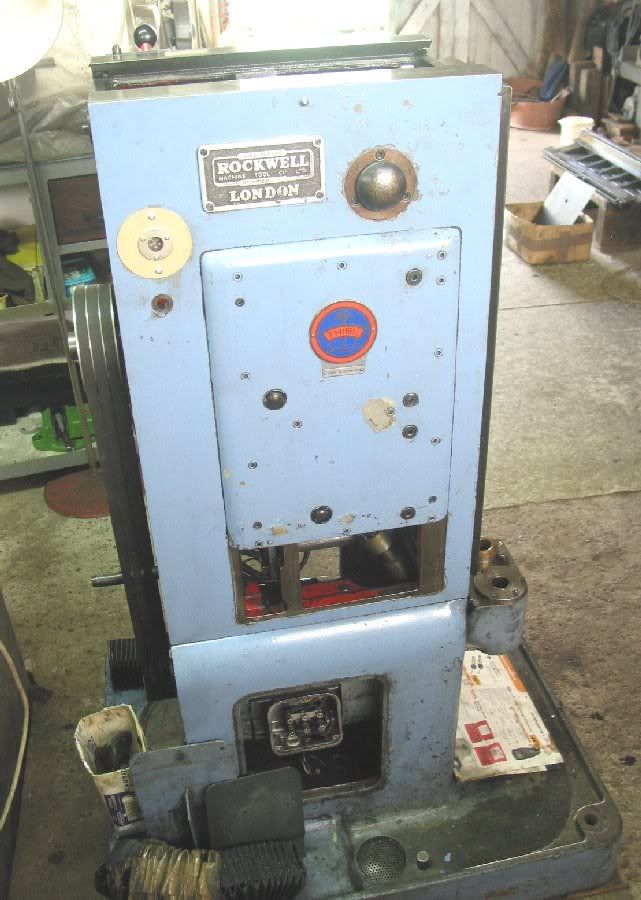
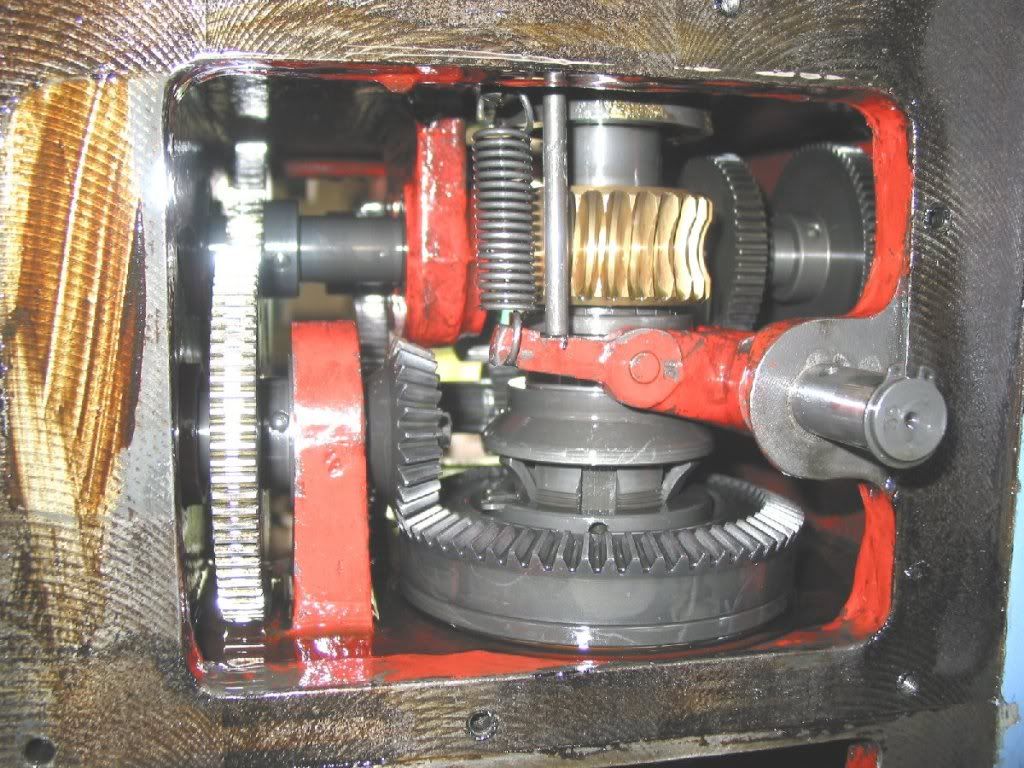
remove the cotter pin that locks the power feed actuation shaft to the clutch yoke and withdraw the shaft, making sure not to pull it all the way out or the clutch falls apart into the sump - oh joy!
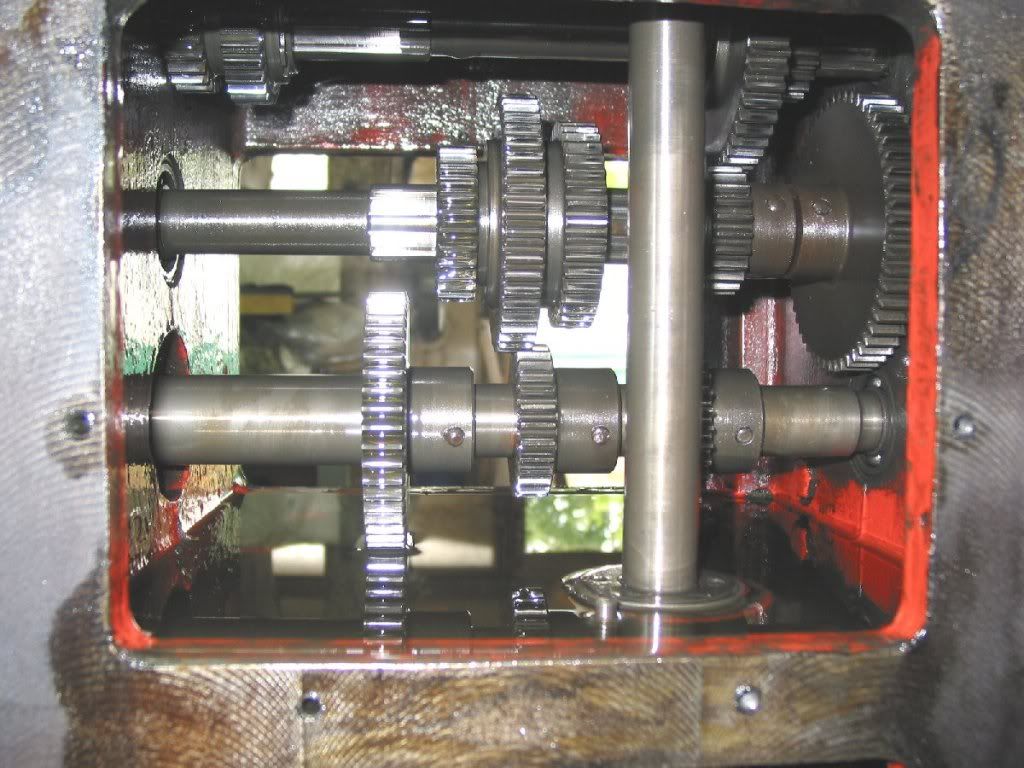
This the main drive gearbox, the vertical shaft is the output from the power feeds clutch to the Y-axis.
Once we had the covers off, the reason for the leak was obvious. As well as the twelve screws holding each cover on, the designers had thoughtfully added an additional screw in each corner tapped into the cover to jack it away from the face to aid removal. A job that would otherwise be very difficult especially when the face had been sealed with gasket sealant. The trouble was, of course, some clown of a grease monkey had tightened ALL the screws and thus broken the seal, the tighter he made the screws to 'fix' the problem, the worse it go. A quick clean up of the mating surfaces, a wipe round with some Hylomar and it's sorted.
The machine is now just about all back together, just need to sort the wiring which had suffered the less than tender butchery of some psychotic electrician with a machete and a roll of sticky tape.
Cheers
Richard