Quick update, not a great deal of progress but worth mentioning.
I started by taking a couple of snaps of the simple jig I made to drill the holes as promised. It's not really the best jig, all it does is fix the radius and concenter the cover and cylinder. The rest had to be done by eye on markings on the cylinder cover just by gluing the cover on and rotating the cylinder. Seems to have been effective though and worked well.

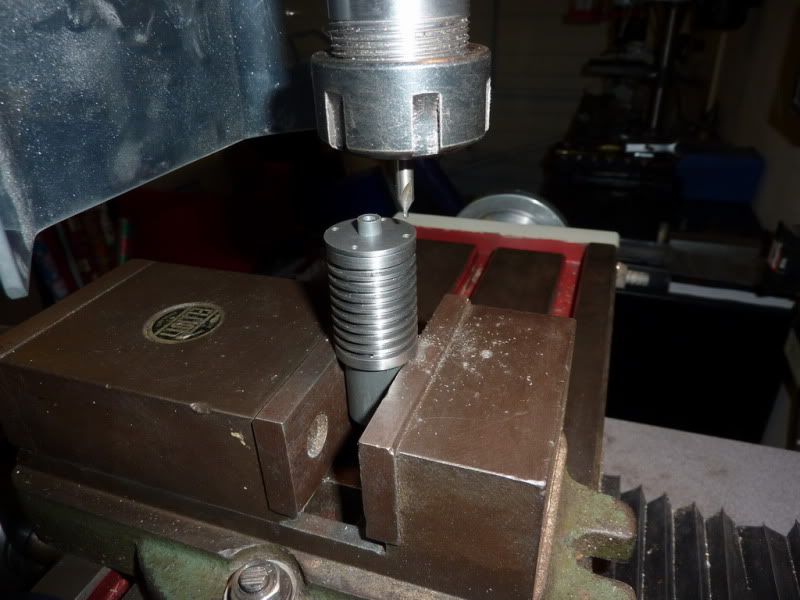
I then wondered which part to make next and pontificated on a number of methods. I had some brass large enough and enough to do 2 flywheels, also had a bit of steel to do another 2. Then I found some brass 1/2" plate which I could have used. Or, some 2" steel which would make them 1/8" under size.
Anyway, whilst on the netti, I came to the decision to use the 2" steel as I would have little or no OD turning do do if I could drill centrally, just a bit of a polish up. I decided I wouldn't pussy foot about and would try to part off the blanks from the stock. So I went out full of enthusiasm, set the parting tool to the minimum overhang that would do the job, selected a suitable speed - very slow, back gear engaged, about 70 odd rpm, slowest cross feed to keep it nice and constant and even got ready with some suds in a syringe.
Then disaster almost struck - before I could react, this happened:

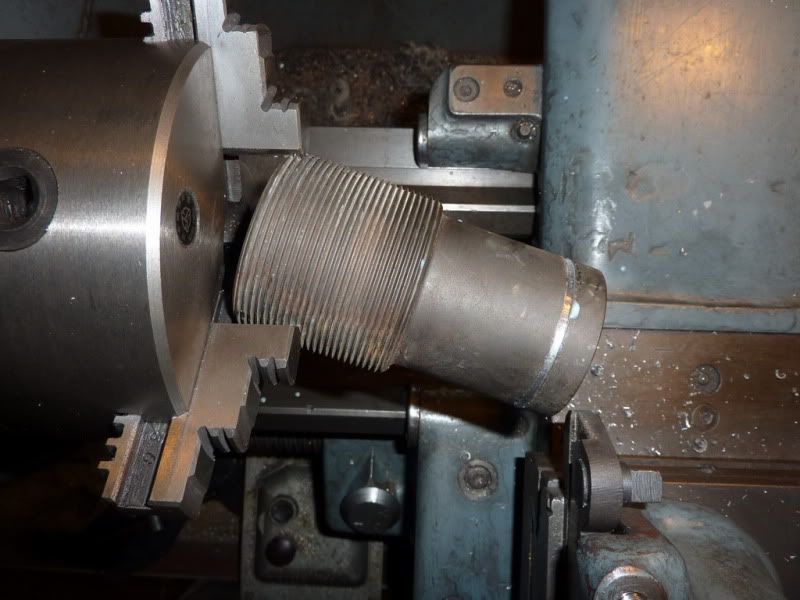
I’ve moved the saddle a bit in that photo, the blade dug in shattered, and sounded like it hit all 4 walls, floor and ceiling but luckily missed me.
This was my thought process immediately after switching power off:
1. Oh ****, ******* ********.
2. I’m ok.
3. That could have been worse.
4. Actually I might have mangled the chuck and caused damage to the machine.
5. I think I might give up this hobby.
6. Take a step back and calm down a bit.
Seriously, it scared me. I’ve never parted off anything that’s steel as the feeling I get and noise have always put me off. This time I went for it as I thought I was being soft in the past, I thought I was doing it correctly but obviously not.
When I did calm down there seemed a tight spot on the chuck jaws, something has probably got bent. I took the jaws out, cleaned and reinstalled and it works, but there is a slight tight spot at some point so I must have done some sort of damage. It still grips and seems concentric though so hopefully I’ve got away with it.
Here is the damage to the metal:
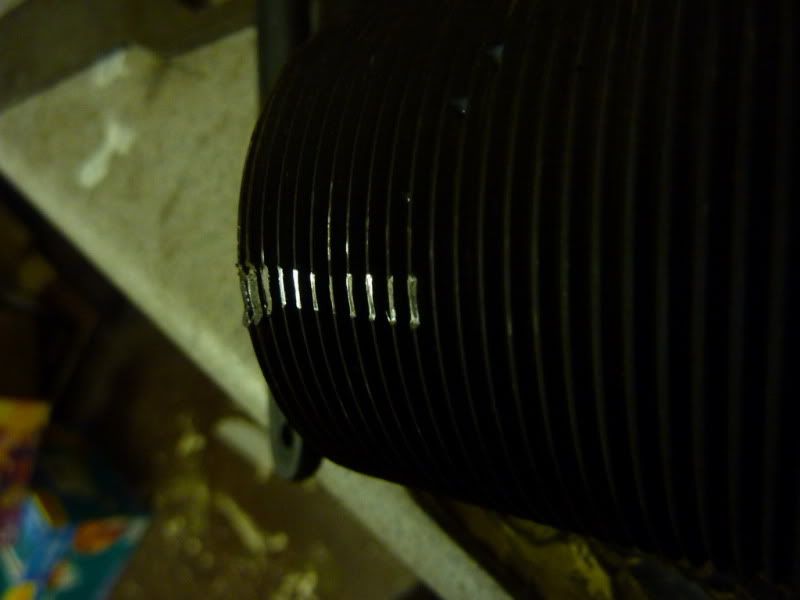
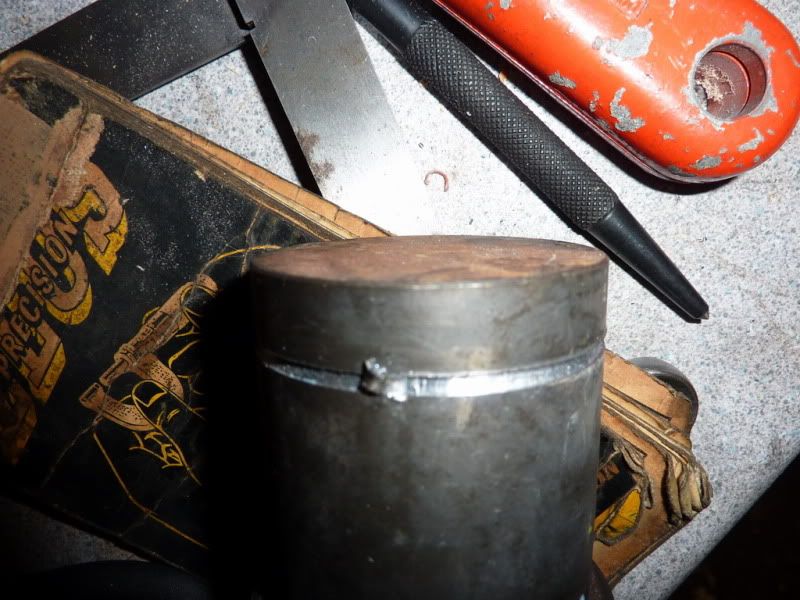
There are a few major safety points that should go without saying:
1. Always wear eye protection – make sure you have eye protection you can see out of and are comfortable wearing and make sure you always wear it. I could easily be lying in a hospital bed wondering if I’d ever see again rather than writing this.
2. If in doubt, stop, I had a doubt in my mind I would be able to part this off but was trying to save time. I should have reached for the hacksaw at that point.
3. If you have a chuck guard you should probably use it. That piece of steel very nearly came out of the chuck – at the speed it was rotating it wouldn’t have been flung and I’m not saying the guard would have stopped it but it could only have helped matters. I’ll be using mine more in future that’s for sure.
I didn’t think there’d be an issue with me gripping on the threads of that bar, but with hindsight it may have been part of the problem. They were probably the weak point, deforming and allowing the stock to move.

I did consider turning a parallel section to grip on but then I thought, it’ll grip tight on the threads and they will probably let the chuck jaws dig in a bit and get better grip.
So, I’ve calmed down a bit and the following hour and a half was spend with the hacksaw for punishment – aching now!

:
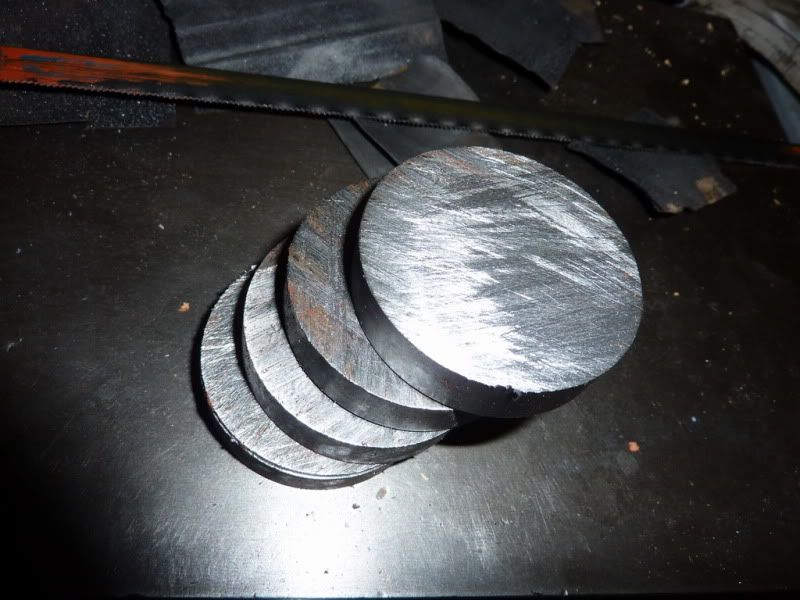
I did face the stock between each hack saw cut so at least 1 side of each blank is faced. Got a nice finish using the suds too, very good.
I could have not mentioned this mishap but I think it’s worth sharing these near misses just to give people a prod and make them think about things twice.
Nick