So.... The initial rebuild begins. With the displacer.

I
really, don't like copper pipe for this purpose. Too heavy. Too much heat absorbtion/ conduction.

Lots of handy diameters and lenghths, of s/s exhaust available on Ebay. This is 42mm......
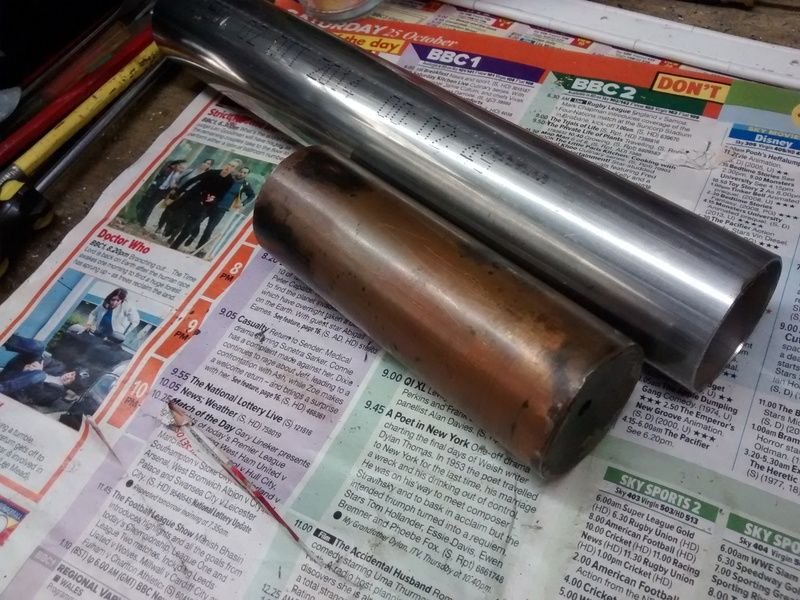
Bored out, to lighten. Now, around 20 thou' wall thickness.......
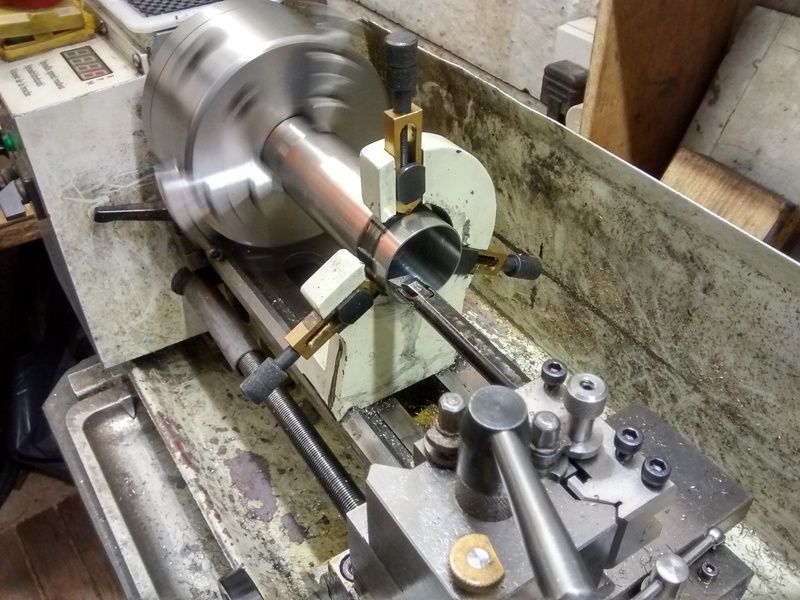
8mm thick, s/s offcut, friction turned, to slide in the displacer's bore.......
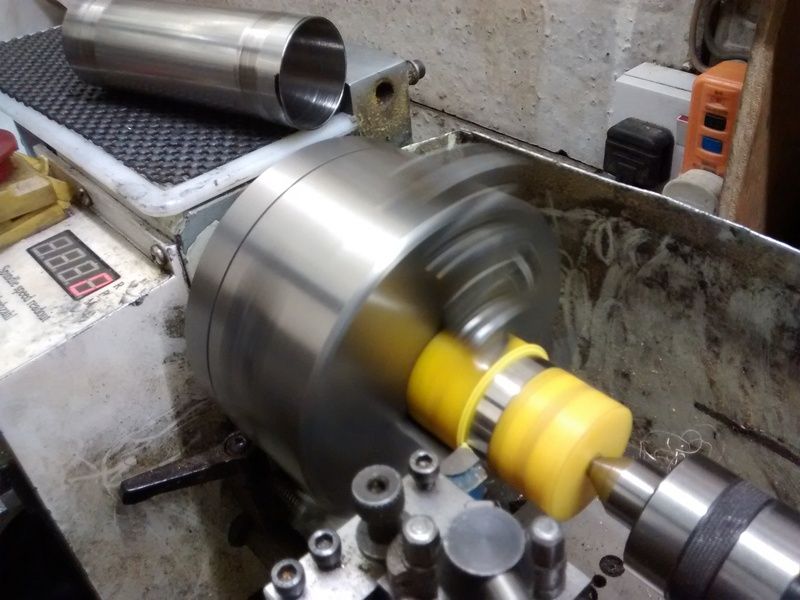
Chopped the inside away, to give 1mm wall thickness......
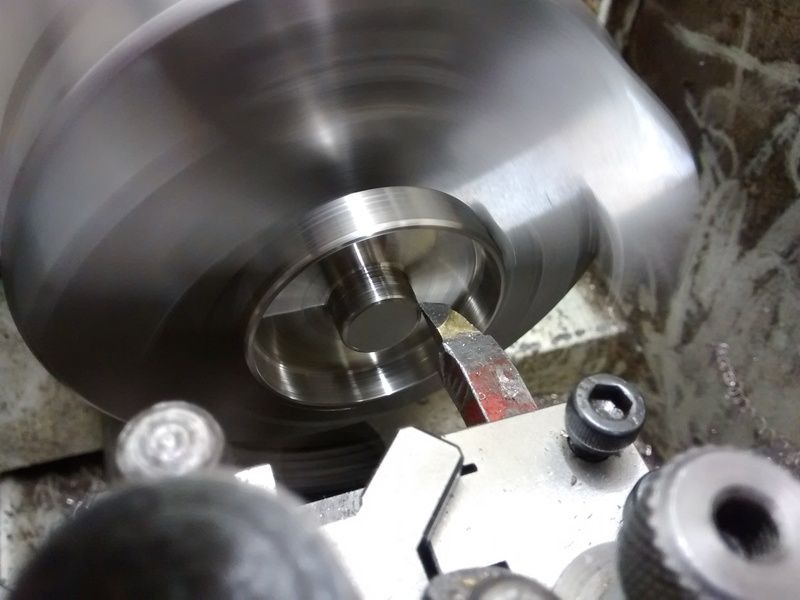
Drilled through boss. Silver soldered in, a 12mm long extension. Then drilled to spigot depth, and tapped M5.
Rough cut end cap, in background Awaiting friction turning........
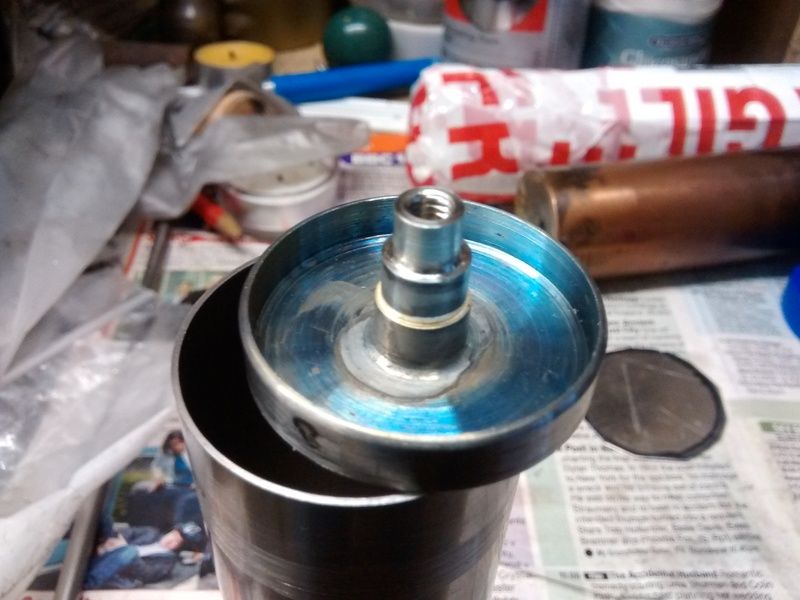
Silver soldered in, both end caps. Cleaned up.
That looks better! Even though, it will not be seen........
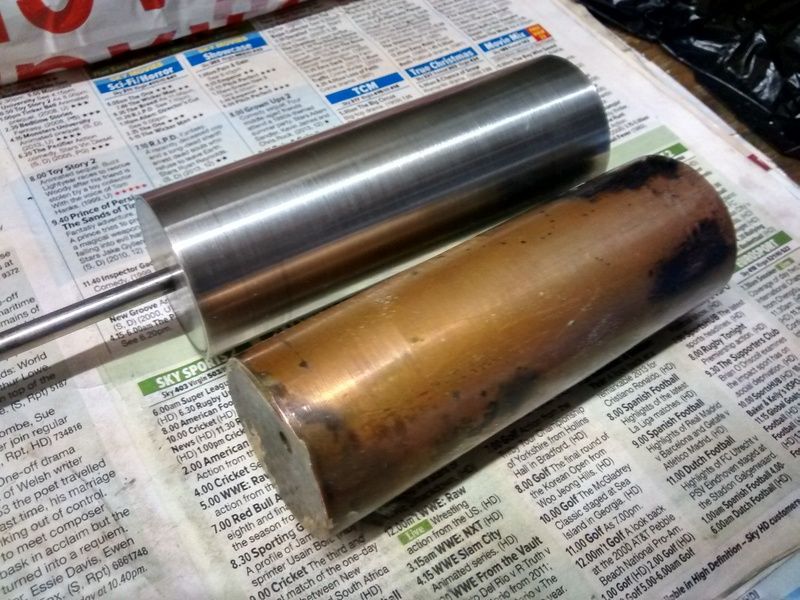
Next up.... Reducing the power cylinder bore. From 35mm to 29.5mm.
I used two more lengths of s/s exhaust pipe. They have very accurate and consistant, bores and o/d's.
A couple of thou' removed, allowed two to be sleevelocked together.
Topped to just below original bore size. Then bore opened out to 29.5mm.
Lots of time spent
oscillating, to achieve a decent finish, and remove the 1 thou' taper.......
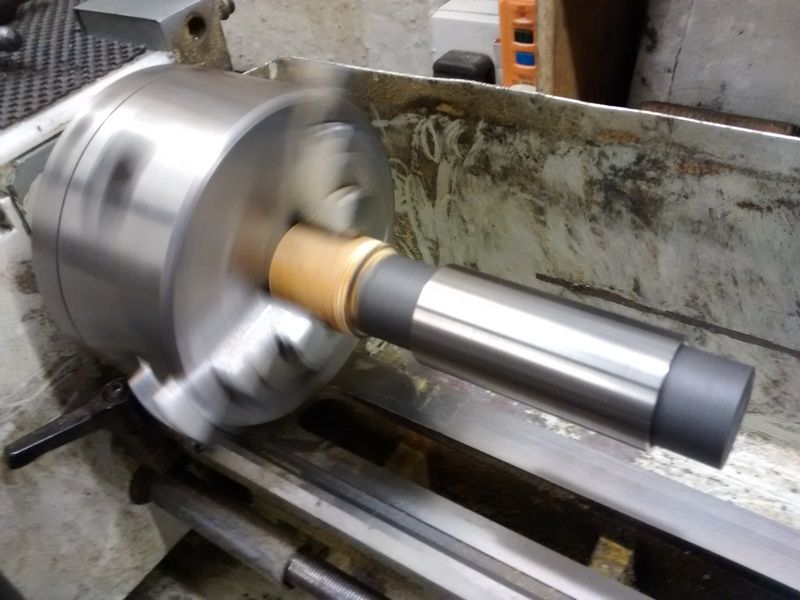
Looks ok, I think! The joint can
just be seen, at 10 and 4 o'clock positions. close to the bore's chamfer.......
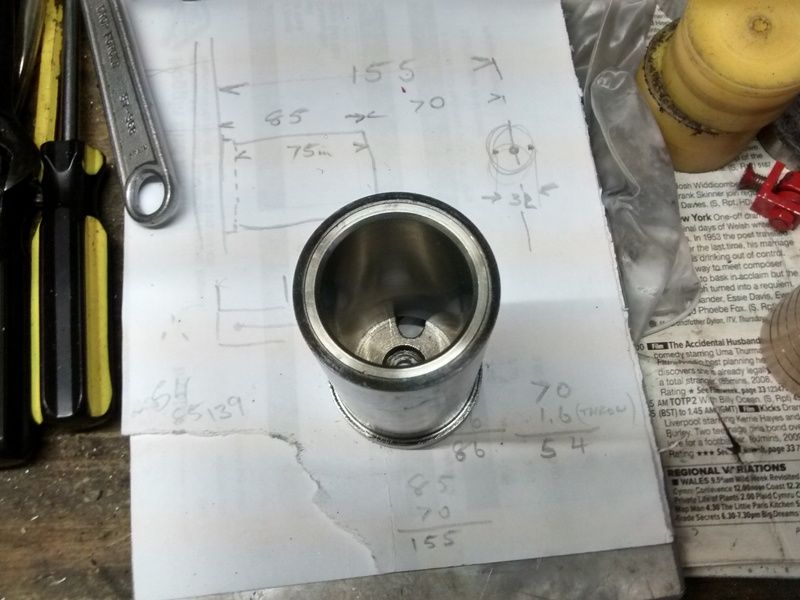
Frankly..... I'm not impressed by the little end's arrangement.......

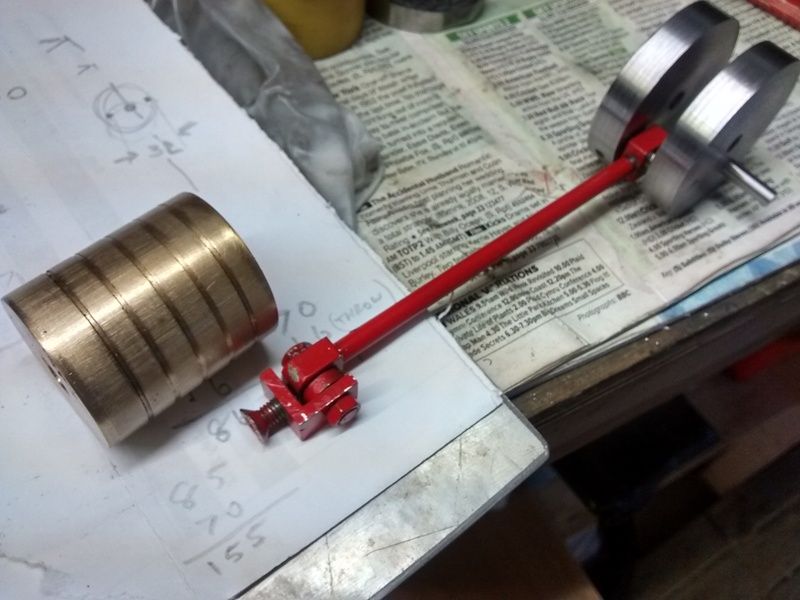
There's only poverty, holding the big end in place........

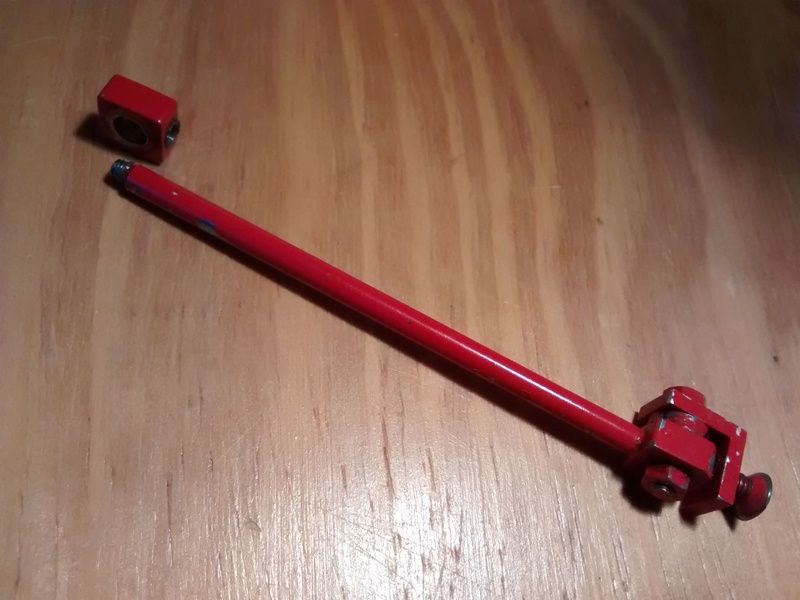
Guess, we now need a new conrod!

Thanks for looking in.....

David.