vtsteam, you raise some interesting questions. Number one PLA is a consumable, whilst I hate throwing things away at least this one is biodegradable, eventually. One ring gear and pinion weighs 9gram. Printing with wax, I guess the problem is wax has a low viscosity when fluid and would be harder to meter from the head, it just doesn't behave like molten plastic. That said you could do a rubber mould of the printed part then shoot wax for lost wax casting, just seems a lot more work unless you plan on making many of them.
Now the tricky bit. Printers... The technology has taken many years to reach the point we are at now, yes there has been obsession with getting the machine to make itself. I am not at all interested in that side of things, I am an end user with applications. The printer for small parts usually has to be an order of magnitude more accurate than a hobby cnc router, but at a push you could use one. Having an enclosed cabinet helps the consistency of layer building no end, it keeps the heat in and the drafts out that can cause warping and delamination. Again the printer is a huge compromise, you actually want a very light weight printhead so you can move it about rapidly without shaking the machine all over the place. Add to this the need for as close coupling of the feed motor to extruder. Bowden fed extruders are a lot more difficult to control than a direct drive, especially with flexible filaments where they easily compress. Printing has loads of variables that must be balanced to achieve good printing, it really is juggling with jelly that we tend to take for granted now the hard work is done. Hit a snag and you are back on the learning curve of how this all works, this is why I concentrate my efforts on PLA and work within its constraints for now. Printed nylon does not have the same characteristics as moulded or machined nylon, it may be touted as stronger but it ultimately depends on your end use and understanding of its limits, and we are back at compromise.
picclock, the results of my morning in the workshop.
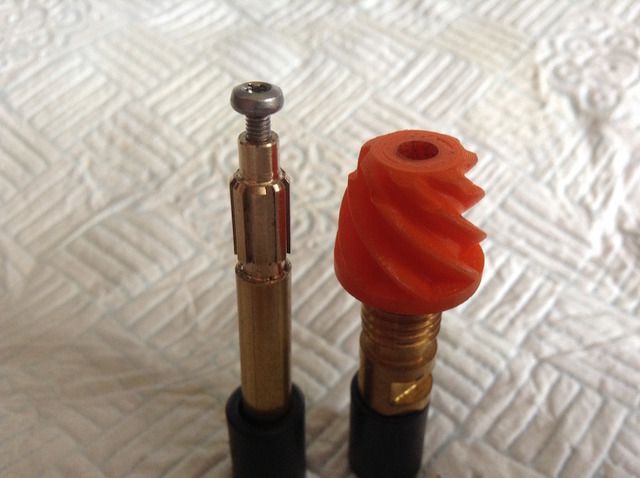
Brass splined shaft made ready to fit pinion.
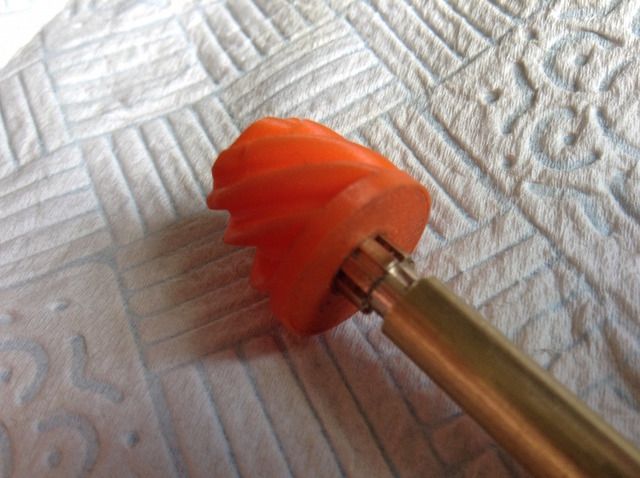
Partly mated, they are a tight fit, I can remove the pinion without the printed splines being torn out of the pinion. This is a test part and something new I am trying, I am very happy with the result so far. The gear is centred with no slip on the shaft. Next up is design the bearing carrier for the two gears and then start load testing them.
I have about 2 years 3D printing experience with current hobby machines, about 10 months on my Createbot mini. In my collection is a deltabot that I play with, but it is a whole different beast to this current one.
Don't fret over some of the details in printing. That first layer is usually your most inaccurate as you are trying to lay a foundation layer that is usually thicker than those to come. A microswitch is adequate for sensing the bed home position. Granite slab, great idea that should be standard for ALL 3D printers and bolt them too it. Always plan how you are going to print something before you print it, each print in effect has grain that can work against you or for you in some applications. Don't be afraid to print something at an angle with support material, or break up a model into parts and weld them together at the end with a soldering iron.
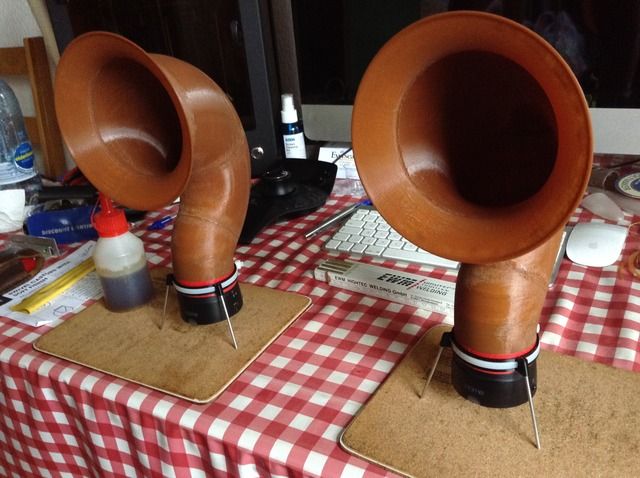
Like the above example. Guy's this is what I have learn't about printing and printers. It's my experience and my journey, yours will be different, always happy to answer questions where I can or just comment on what you see.