Really mad at you not showing this stuff before
See the problem is that this sort of work is addictive, which is fine, but I only got into CNC to help make more rocket bits:
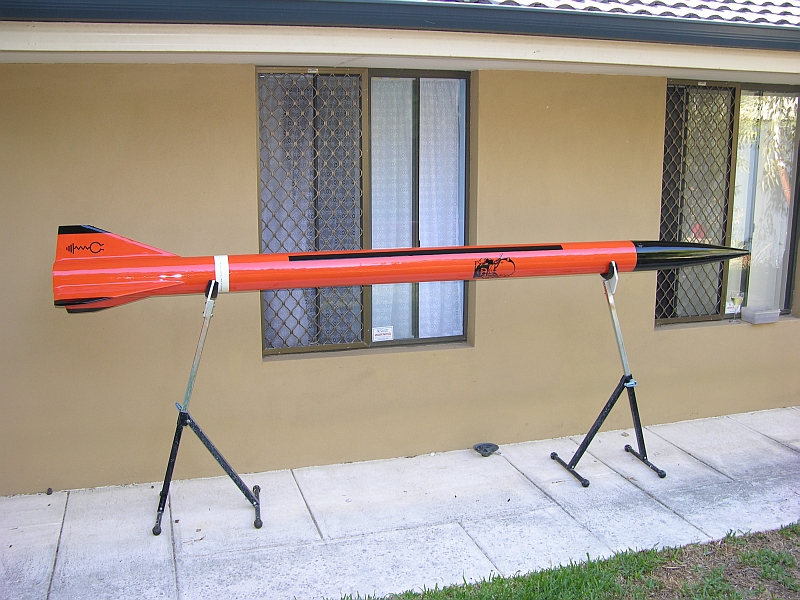
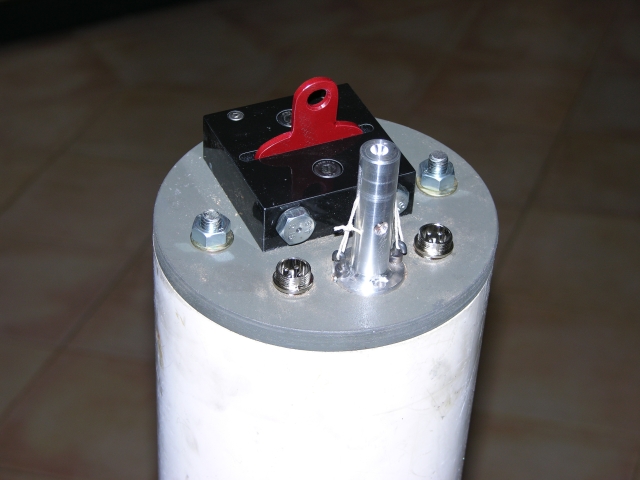
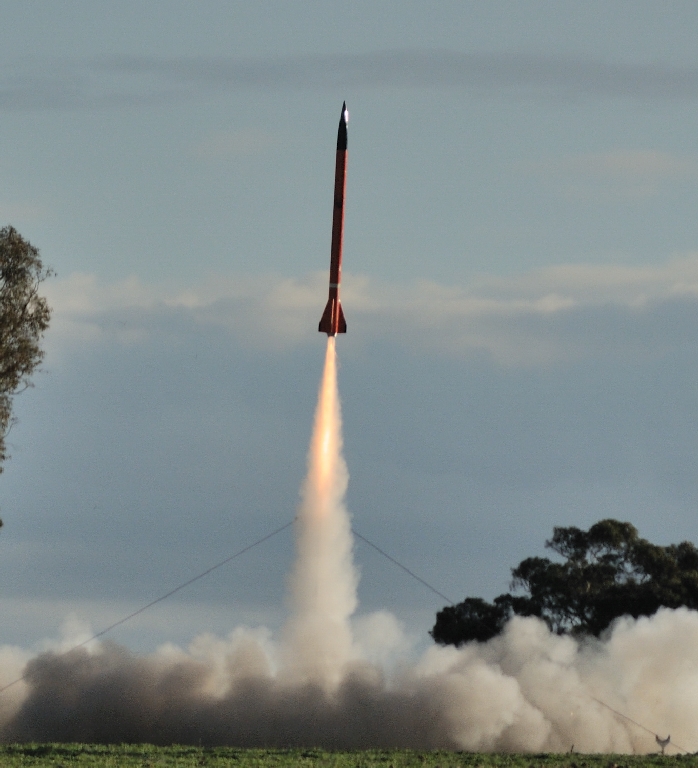
But I got hooked.
Years later I finally plucked up the courage to admit I had a CNC addiction and went cold turkey.. I left the site idle for years and it expired.
But I could calmn down fast if you would tell me more about the gripper on this page:
http://www.caswa.com/cncathome/spindles.html
Got some anecdotal information, but few things were not evident to me.
* Is that taper more or les SK15?
Its just an 8 degree taper, no idea who else uses it.
* Can I have dimenssions of the gripper collet and pull stud?
Tough, I don't use that spindle any more. On a scale that small, I found the plain shank toolholders worked better.
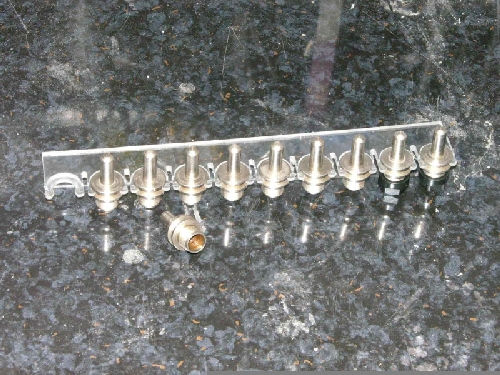
Those are 8mm shanks.
re the studs:IIRC the heads of the studs were 5mm diameter.
* How does it work?
There's actually some deceit on that page (not everything you read on the interwebs is true you know).
The cad model shows a complex arrangement with three leavers and an o ring opening them.
With that spindle being so small, I got better results by making the claw look a lot like a tiny R8 collet with a groove just inside the nose to grab the stud. Then I bent the collet open and hardened it. Pulling on the drawbar would then close the thing around the studs.
* How much is the griping force? You probably had some some figures in mind when you were planning taper/force. Care to open a process a little?
Short answer, not enough. When you get that small, the overhead bits (pull studs, claws, springs etc) start taking up disproportionate amounts of room. That room comes off your friction surfaces and you loose grip.
Another bad bit is that the pull stud setup requires quite a lot of precision and hardened, high strength parts. I ran the plain shank ATC for about a year with a soft collet.
Finally though, when we started using the little router for production work, and employee cooked the magnets off the servo motor driving it. This triggered us getting our first water cooled, 24KRPM spindle. For a small machine, with a high resonant frequency, these are just the ducks nuts. I'm talking 6-10 times the metal removal rate. I'll be putting up a page specifically on them.
Really liked the stuff you do. Enjoyed reading about X3 and ELS. "Spindle speed control for the mill" did not reveal me of it's secrets.
TA, not much to say on the DC motor drive, you can just buy them for next to nothing these days...
Cheers
PK
[/quote][/quote]