Todays offering to the machining Gods is a piston. Granted, its a rather strange looking piston, and I have never built one like this before, but remember, we are in the wonderful world of prototype here. The top section of the piston extends up beyond the split between the combustion chamber and the cylinder, so we don't want it to contact the wall of the combustion chamber in that area. Additionally, there is more "hogging out" of material in the rod end of the cylinder than is usual. That is to accommodate the 1/4" sealed needle roller bearing, which is the smallest size I was able to buy. I'm not even certain a needle roller bearing is going to give us any great benefit there in terms of reducing friction, because the rod only swings in a small arc, not a full rotation.
I have to contact the manufacturers of the needle bearings on Monday, as I remember reading somewhere that needle bearings are made deliberately oversize, both on the outer diameter and on the inner diameter. They are intended to be press fitted into a housing, with a hard enough press fit to reduce the bore to the correct size.--That could be quite a trick, when they are going into an aluminum rod with only a thin band of material enclosing the bearings.
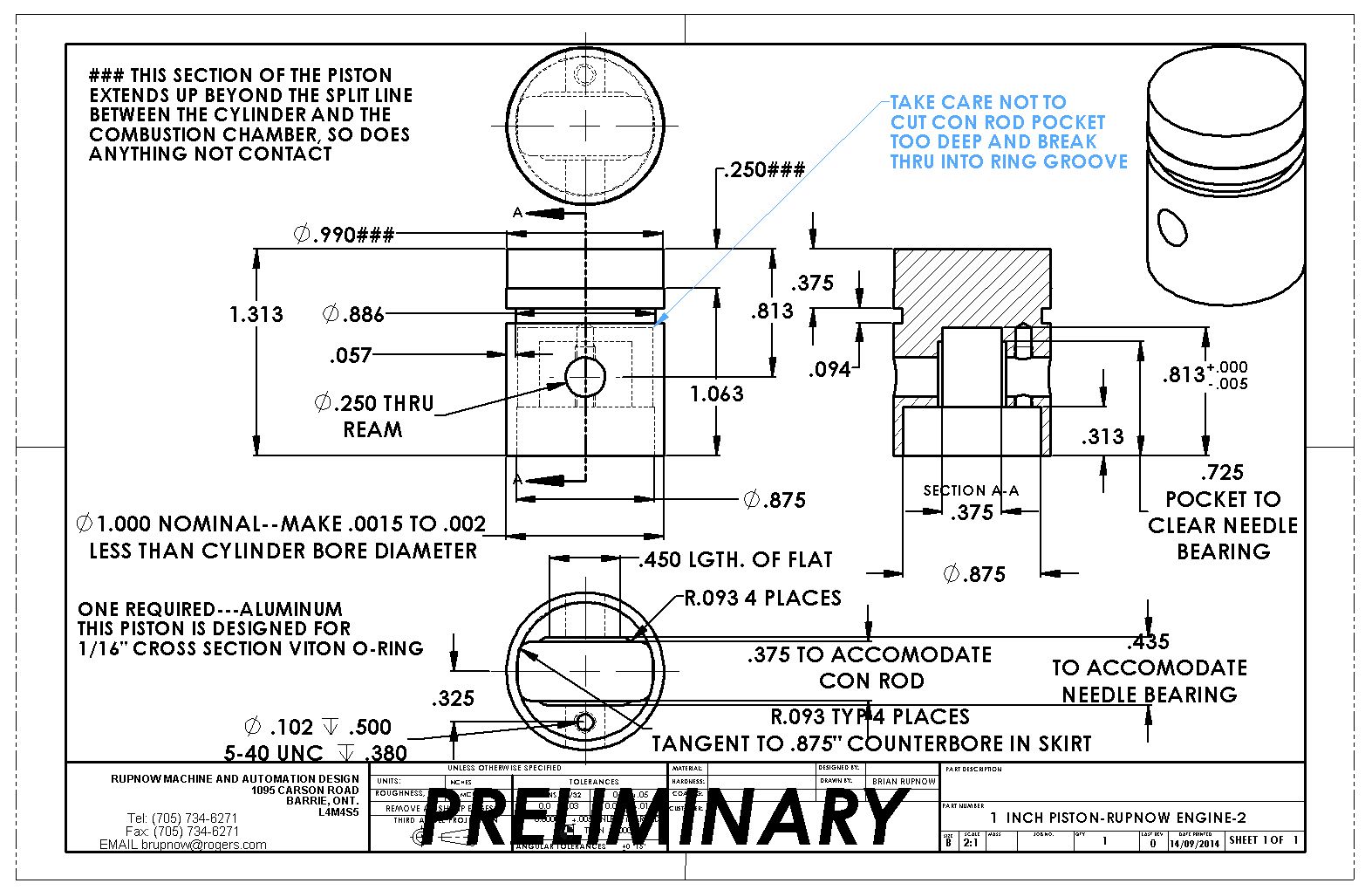