I removed the rocker arm assembly, pulled the cotter pin and rearranged the spring and washer in their proper locations.
With everything looking correct, it was time to fit the valve rotator caps. I assumed the three I had from the tractor originally were all correct -- I just needed to figure out which one went where. Wrong!!

Well, there was first a pause while I figured out just how I was going to be able to ensure the .002-.004" clearance they each had above the valve stems. I tried a few methods -- including Manxmodder's earlier suggestion of using a magnetic based indicator. But nothing I tried worked well enough to give me a consistent reading. The main problem was that the valve stem was recessed in the spring and there was nothing to compare its height to. Finally I realized that I could use a small 1/4" drive socket to serve as a spacer on top of the valve retainer. I could set my caliper end on top of that and measure the depth from the top of the socket to the valve stem, then subtract the socket height (.850") to get the height of the stem above the retainer. The depth of the caps needed to be .003" more than this height.
I got consistent readings using the socket and caliper method and started sizing the caps. Well surprise, surprise, they were WAY off!

None of these caps had been fitted properly to the valve stems. They varied from 20 to 50 thou too long. So with a fair amount of work grinding and checking many times with the calipers and finally when getting close, hand stoning them. I ground them all to .003" clearance for their respective valves.
I think that some prior owner had simply placed aftermarket caps on the valves, without fitting them. This in combination with the misaligned rocker arm may have spelled the loss of that #1 exhaust cap. I wouldn't be surprised if it (or pieces of it) are located in the oil pan.
Or perhaps the owner had simply lost the cap. I did wonder for a moment whether the warped head had been the result of the lack of a manual and/or torque wrench by this particular mechanic.
Well, no matter, that job done, it was time to torque down the head. The manual gave 65-70 foot pounds as the figure, and I followed the bolt torquing sequence in 3 stages. The I reattached the rocker arm assembly with the oil lines this time, and torqued it down to 45-50 ft/pounds,per the manual.
I blast cleaned the spark plugs, set the gaps, and screwed them into the head. It was beginning to look like a functioning engine:
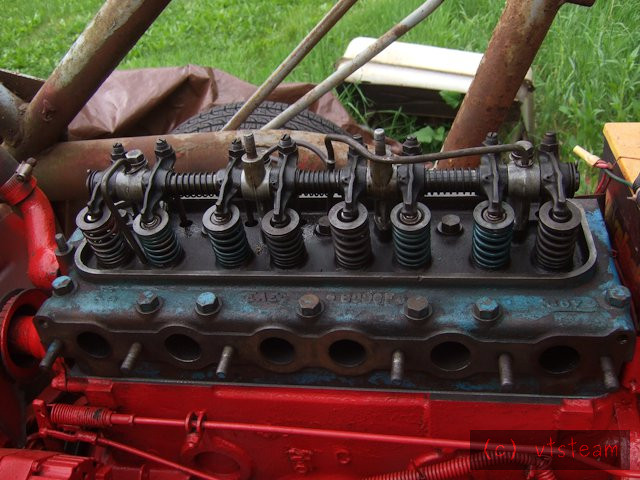