Hello again,
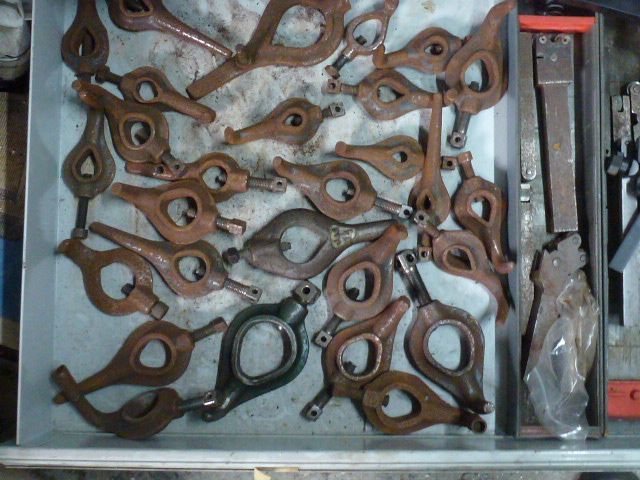
I should call this drawer my kennel, the dogs came with a cabinet that I bought from a machine shop closing down.
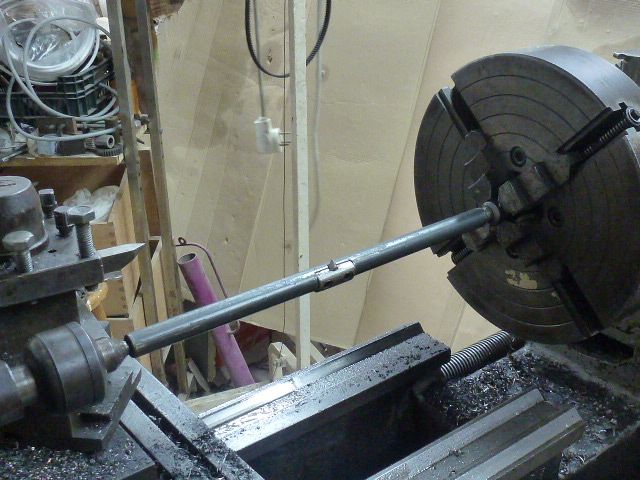
I made this boring bar a long time ago, before I had either a mill or a shaper, I haven't used it for about ten years, I had my doubts about it when I dug it out! Well it's too short, so turn a cone on one end to weld a bit on.
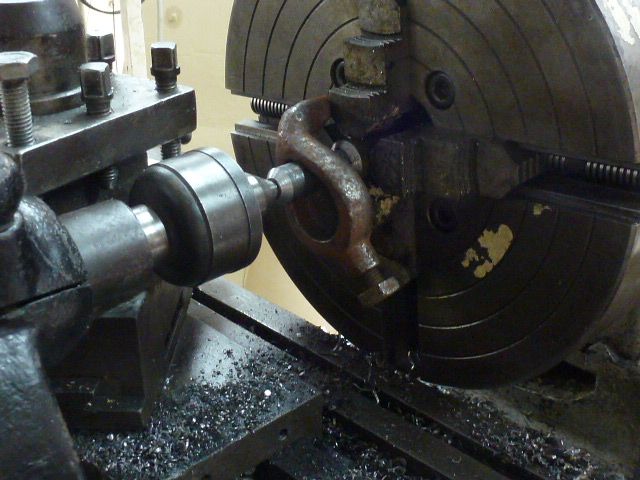
Turning a stub extension. I love working between centres.
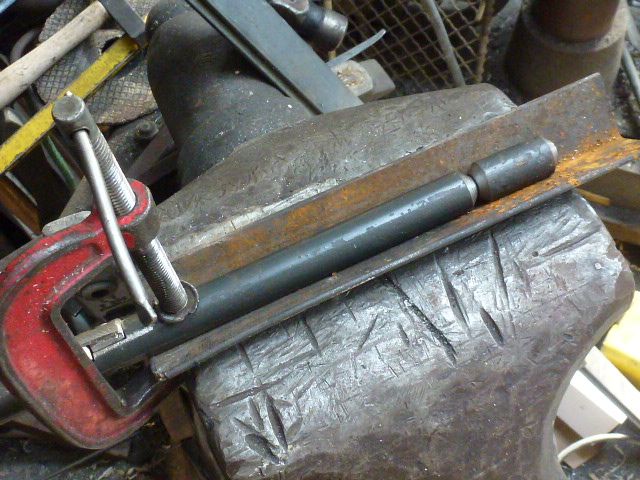
Ready to weld.
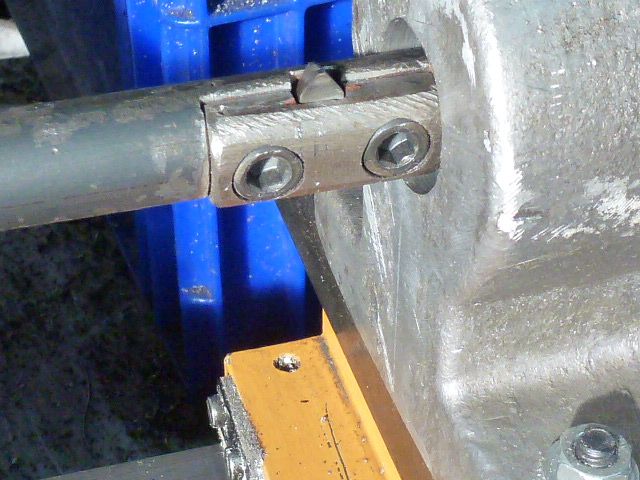
I would not recommend this construction, it chattered at all speeds, I think I last used it with one end in the chuck, but it was so long ago I just can't remember!
To make things clear, I started machining about twelve years ago, I hadn't done any since I was 14 years old, I made a centre punch and a hollow handled big screw driver on the lathe. So my first machine tool was a home made lathe that looked as though it had been made in the 1950s. I bought a shaper as I thought I could learn to make parts for the not very rigid lathe. I started getting the hang of the Elliot M10 shaper which was nice and tight and produced use full bits. Then nine years ago I bought the building I now live and work in, I bought a slice of an industrial building, 12m x 14m 6.25m to the eves with a nearly flat roof. I built my home on a 70 square metre "upstairs" that built. The building work and life have taken up a lot of my time and I'm only just getting back into machining. I've bought machines since I've been here, A 1944 Colchester Master on eBay UK, a H. Ernault SOMUA mill, a Clarkson MKI tool and cutter grinder (the only tooling were a pair of centres) a Denbigh piller drill (a camel back of 1960s construction) and relatively recently an Emco 8 x 18 Compact 8 brand new (1989, still had the protective gunk on it) but missing the motor and drive pulley. I've been working in metals most of my life, ten years as a mechanic, steel construction, building, trained as an electrician, the list is long. Anyway, this is why I have tools that I've built but can't remember much about them! I have only had thread cutting capacity a few months!
So it's time to build a real boring bar 40cm 25mm hot rolled was cut off and centred and centre drilled on both ends in the four jaw on the Colchester.
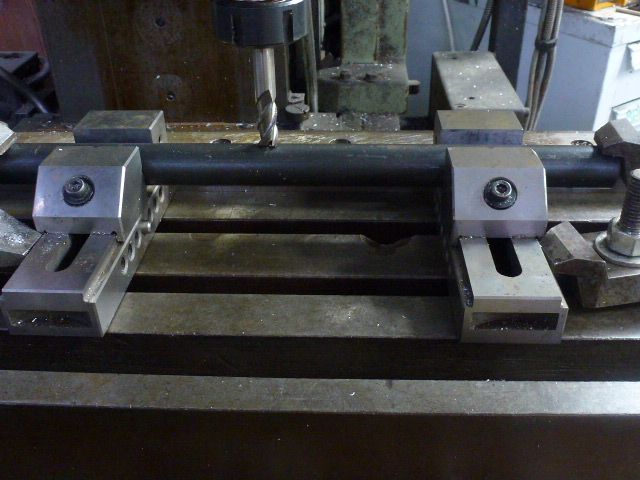
I milled a flat in the middle.
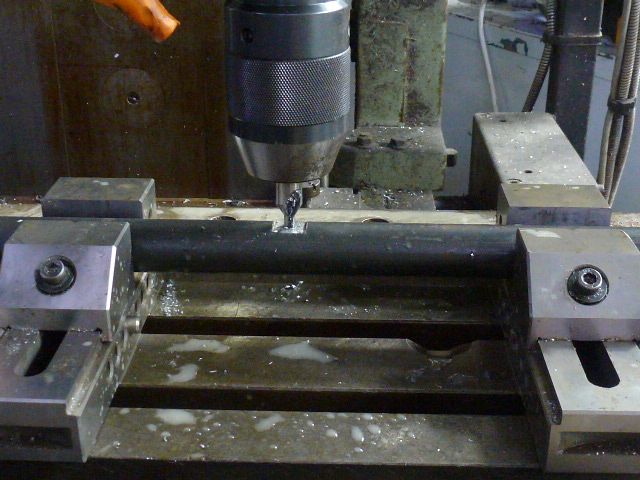
Centre bored it and drilled 6mm.
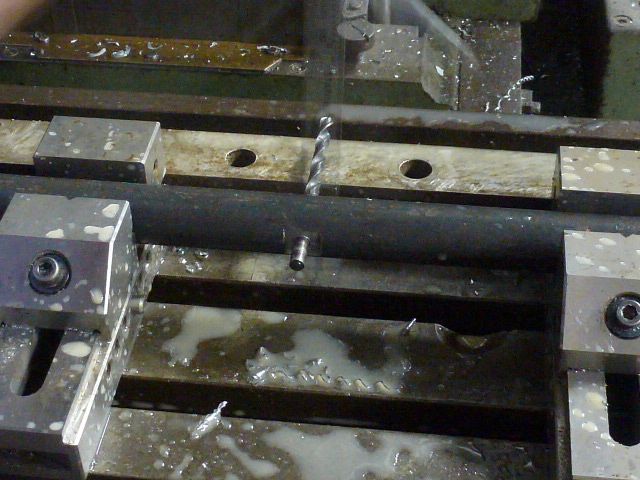
Using the the 6mm bit I eyeballed it 90° to the first hole to drill a 5mm, m6 tapping size hole.
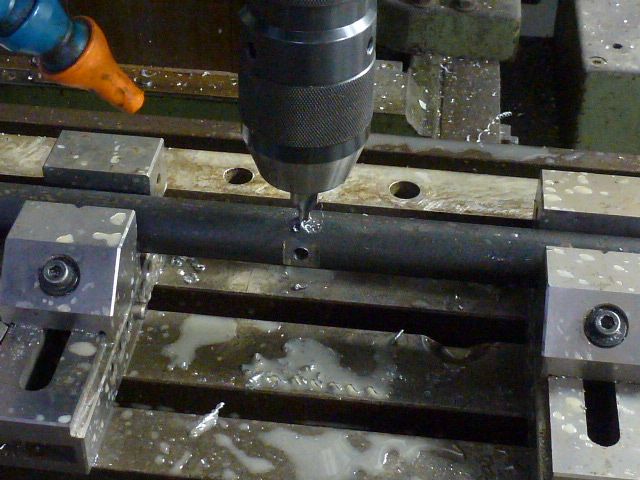
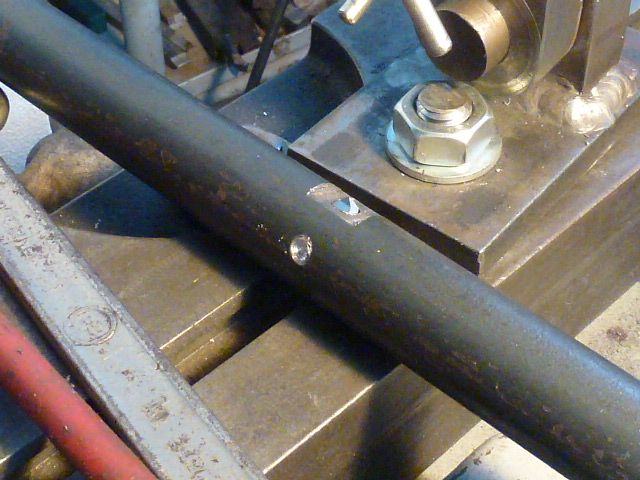
I didn't get past centre drilling, I forgot to tighten the vices, Ooops, so I drilled it from the other side.
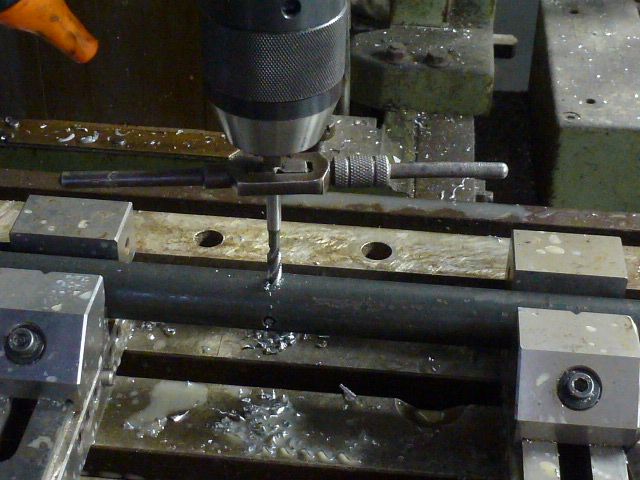
Tapped M6.
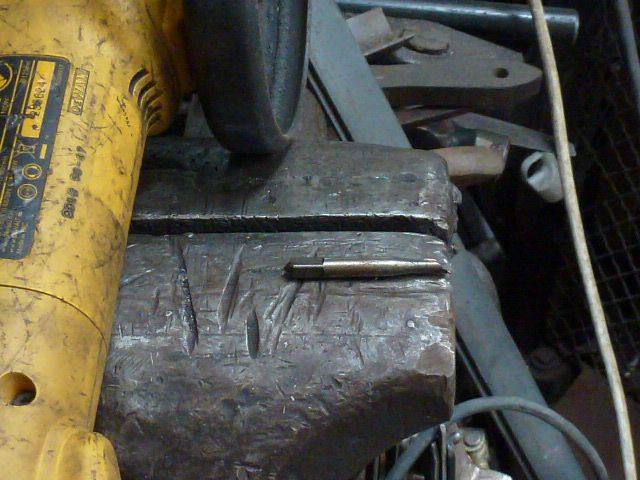
I cut the ends of a suitable broken 6mm Ø tap for the bit.
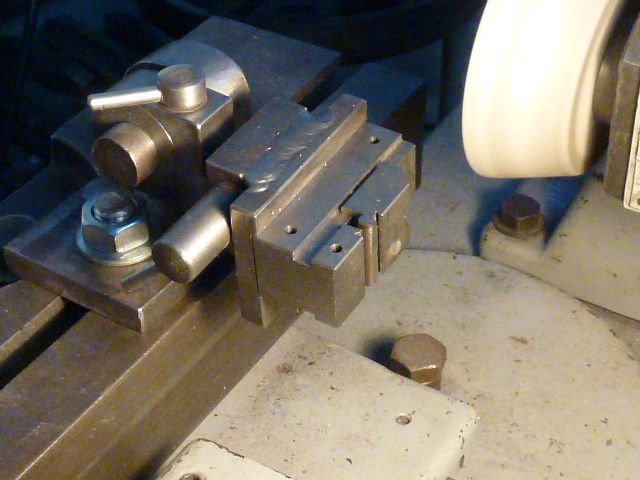
Mounted in the universal vice on the Clarkson Cool & Tutter grinder to grind a flat face that will serve as a reference to grind the tip and orientate the tool in the boring bar.
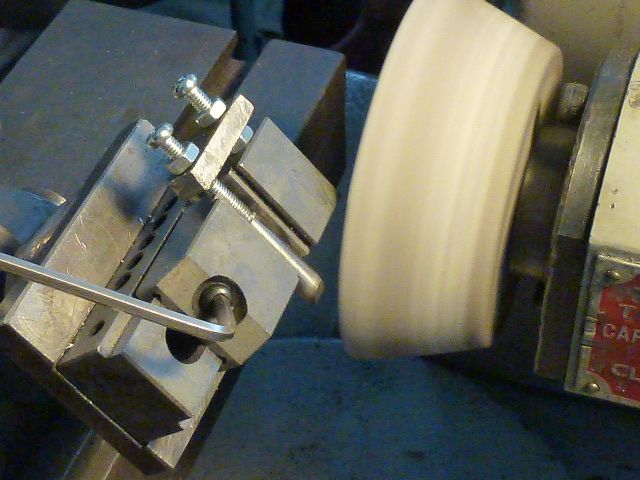
Grinding one side of the point. I seem to have forgotten to take a pics of centring the point and giving it some front rake.
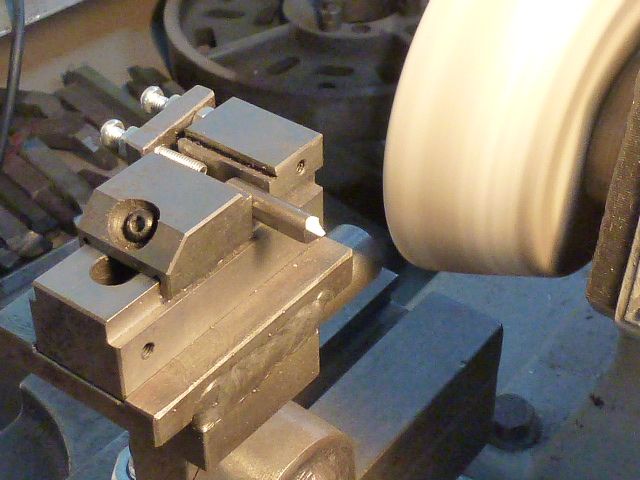
Grinding the top rake.
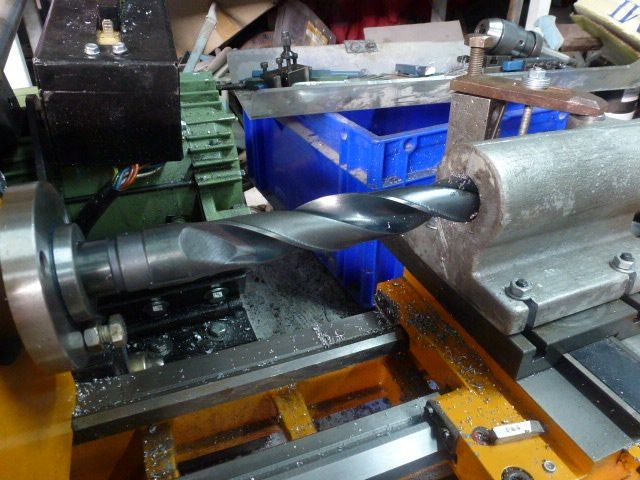
So far, I'd bored out to 25mm, I wasn't going to be able to fit a 25mm boring bar in without some drilling. A 27mm to see how it went through the cotter. No apparent deviation and a very nice finish.
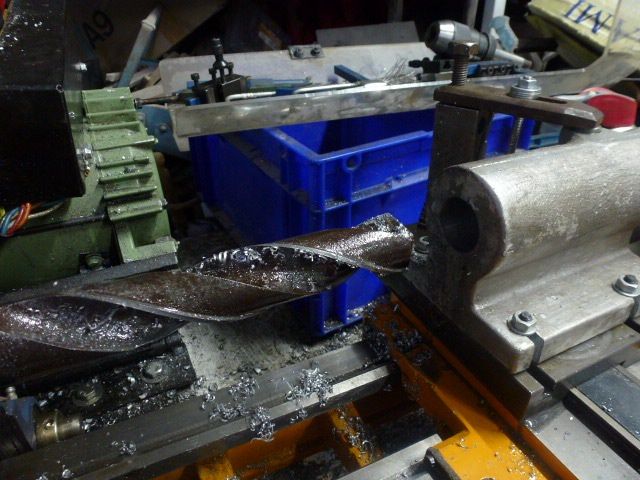
All's well, so I thought I'd run a 28mm through to give more room for chip clearance.
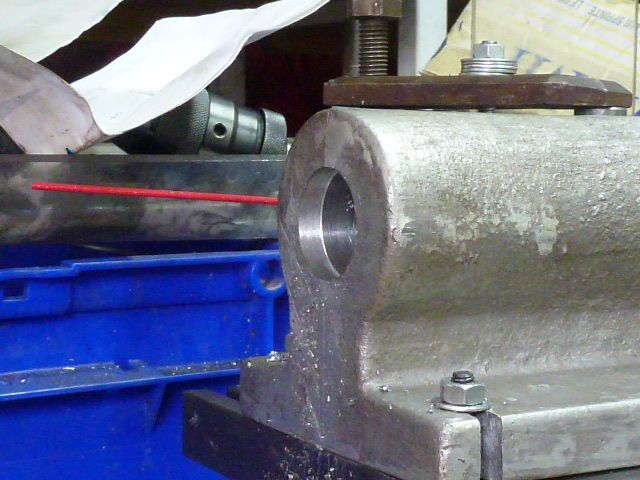
First test cut.
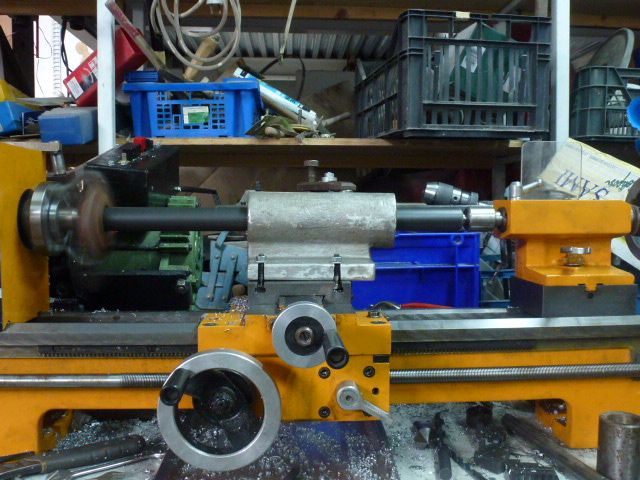
In use.
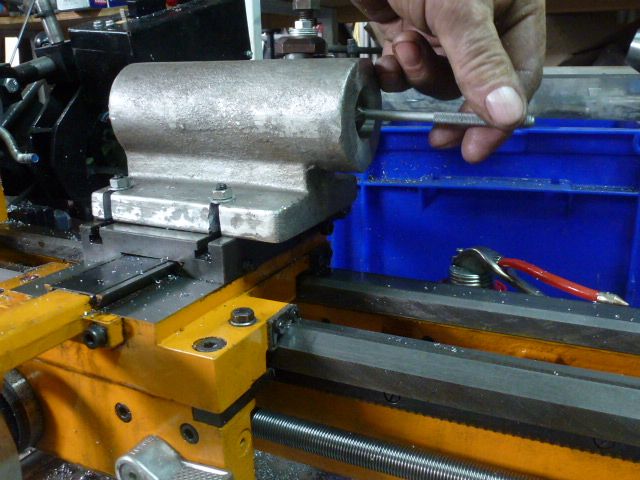
I don't trust my cheepo digital callipers, so I bought myself some bore gauges.
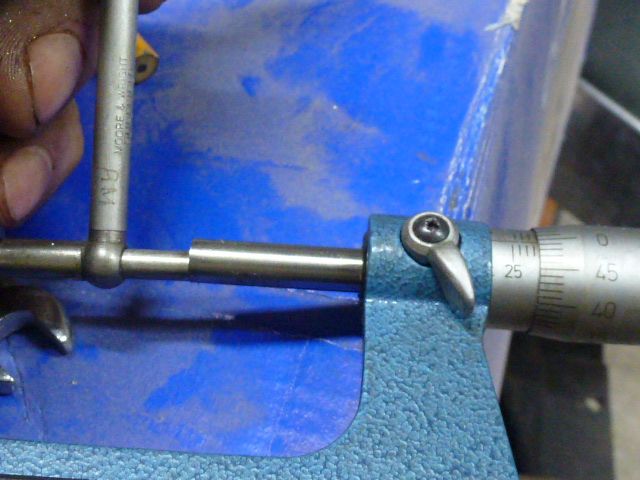
Without trying I hit 28.5mm.
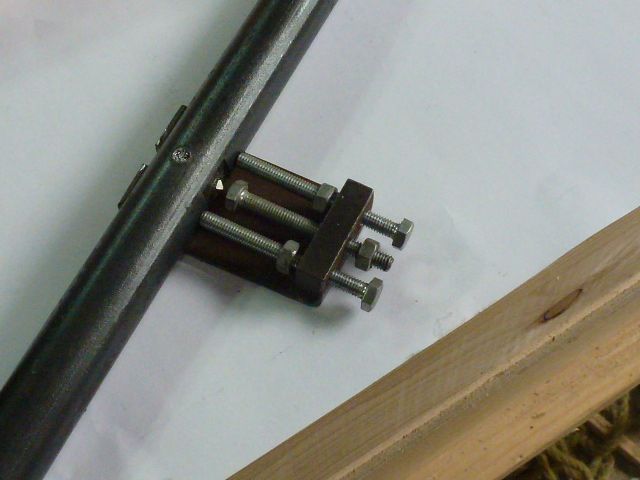
To adjust the boring bar I used this tool that I think is in the Gingery Lathe book.
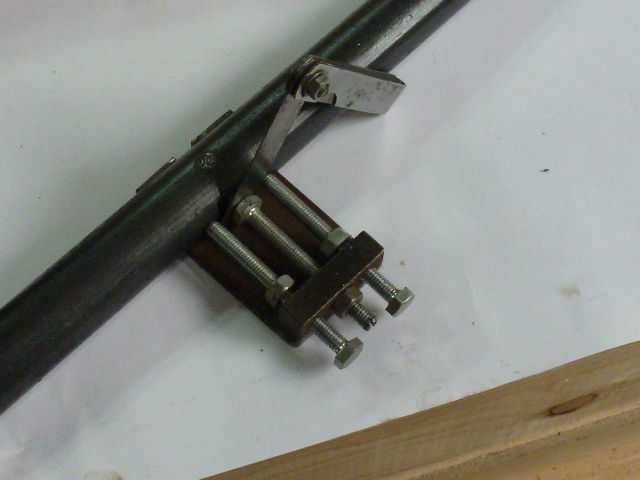
The feeler gauge is put in the tool and the set screw, once the tightened, you take out the feeler gauges and adjust the tool up to the set screw.
While I was doing the last cut, over confident, I wrote down the figures, calculated a it less than half the diameter I wanted, remounted the bar and didn't do a test in the bore, over confident, I bored away until a little before the cotter, took out the bar to make sure there was no chip build up before cutting the steel, measured, oversize! ****! Reset the bar, took a small cut, remeasured, another cut, and the last third was perfect! I still don't see how I did it, The only thing I can think of is I absent-mindedly set it twice. I can always make a sleeve so it'll be OK.
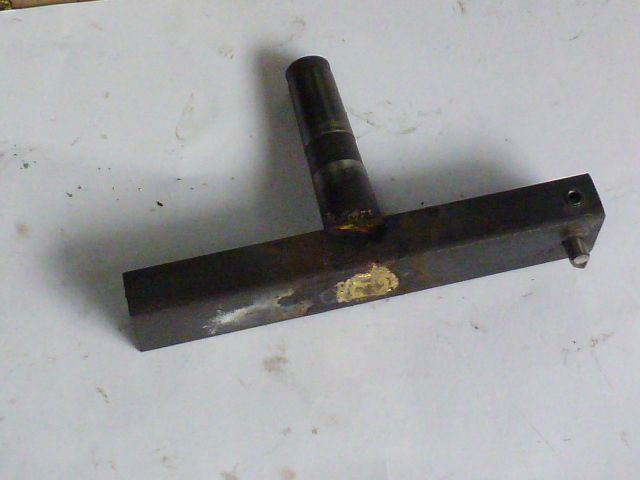
I didn't have a Morse 3 fly cutter, so I threw together a quick one, A piece of cold rolled brazed to a broken milling cutter shank, a grub screw and the tool from the boring bar.
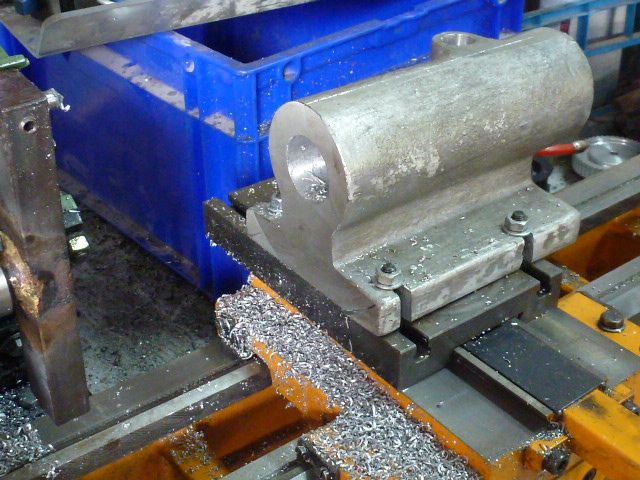
The first cut revealed that when I set up the casting on the boring table I didn't put it far enough back so it misses the the front bottom corner of the casting. I decided that as it wasn't critical I'd just file that off rather than move the part.
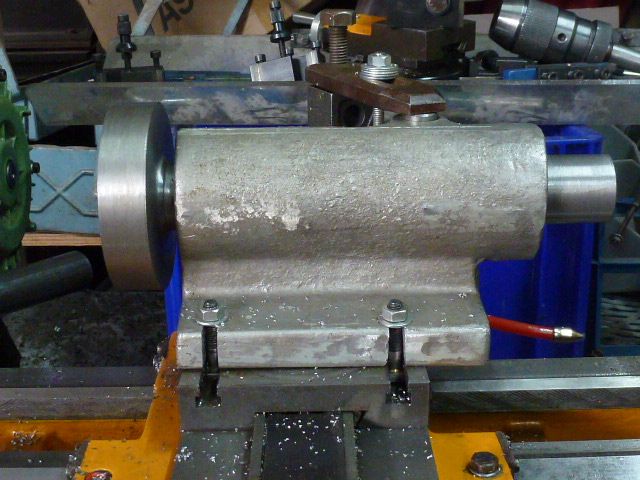
Here it is spindle in place, I'll do some more work on the spindle before I sleeve out my mistake!
Cheers, Matthew