I did this repair a few years ago, but happened on the photo's I took whilst looking for something else

The plane had crashed and ripped out the exhaust manifold.
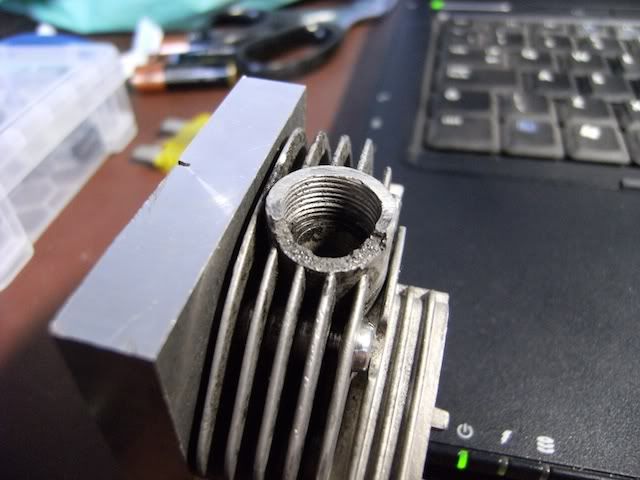
First job after getting it cleaned in the ultrasonic bath was to mount the head on a lump of something I could grip and act as a heat sink when I did the repair.

Once mounted I could clean up the damaged areas and prepare the casting for alloy welding/soldering.
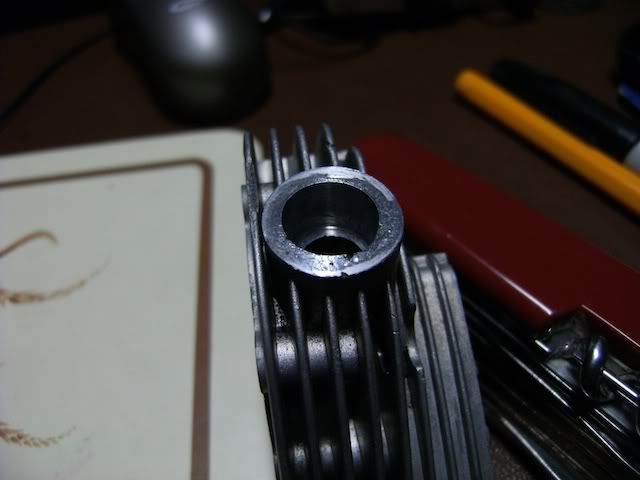
I jammed a thermocouple in the part as I did the weld to monitor how close I got to melting the casting as a fraction too much heat from the blowtorch would cause the whole casting to slump and melt. I used plaster of paris for dams around the casting and in the exhaust port so the molten metal stayed where I wanted it and played the torch around the casting rather than just at the port. The above picture is after I re-machined it ready for thread cutting, you can see some porosity in the metal I added.
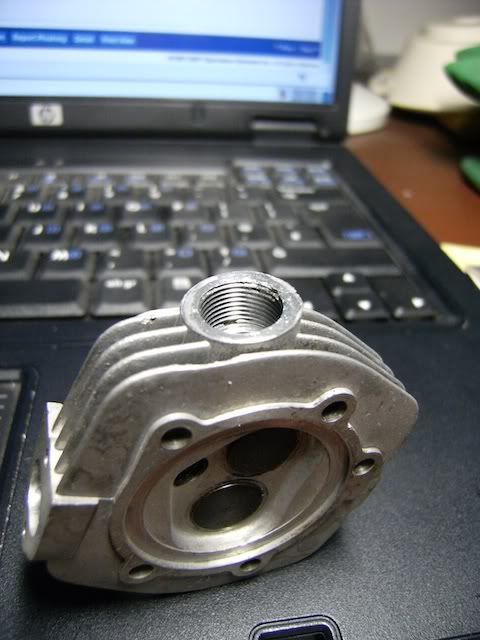
Part re-threaded and cleaned up. The welding process burned all the gunk off and left me with a lovely clean part. I didn't have a means to cut metric threads at that time so the thread cutting was done on a friends lathe.

Finally back together and you could hardly tell it had been repaired from the outside, just cleaned it up with a needle file. I was happy with the repair and so was the owner who had this engine flying again. This was the first time I had really used the alloy welding rods in a real application so pretty impressed. Didn't work so well on the next engine I tried to repair, and of course didn't bother taking photos that time...

Joules