I had a project that would go a lot quicker with a bench top belt sander. A quick Kijiji search showed that there were quite a few of the Canadian Tire 4 inch combination belt/disc sanders for sale near me. The majority of the ads claimed they were like new, and they were selling them for about half of Canadian Tire's SALE price (so about $40 CAD).
This is the Menard's version of the same thing because it was a better picture and I hadn't taken any showing the whole thing.

I ended up picking one up for $30, and considering the heavy cast base on the machine I was pretty happy with the purchase. Now, the guy I bought it from did show it working, but since he couldn't figure out how the belt tracking worked, I didn't want him to demo it any further (in both senses of the word - demolish/demonstrate). From what I could tell, everything was in order so I handed over the cash and headed home with my new toy.
When I stated playing with it at home I noticed there was a surprising amount of vibration of the belt "arm". After a bit of investigation, I found that with the belt tilted in the upright position, turning the belt by hand resulted in the top moving sideways by almost 1/4"! It smoothed out a bit once running, but this was definitely the cause of the vibration.
I started to take things apart, being careful to pay attention so that things would go back together when I was done. I put an indicator on a bunch of different parts, trying to track down what wasn't right. Starting at the belt drive roller, I moved my way back to the timing pulley inside the belt cover. This is where I found the problem. Slowly rotating it by hand, I found that the upper pulley (gear, if you prefer) measured 0.015" TIR. The bottom one was almost the same amount out.
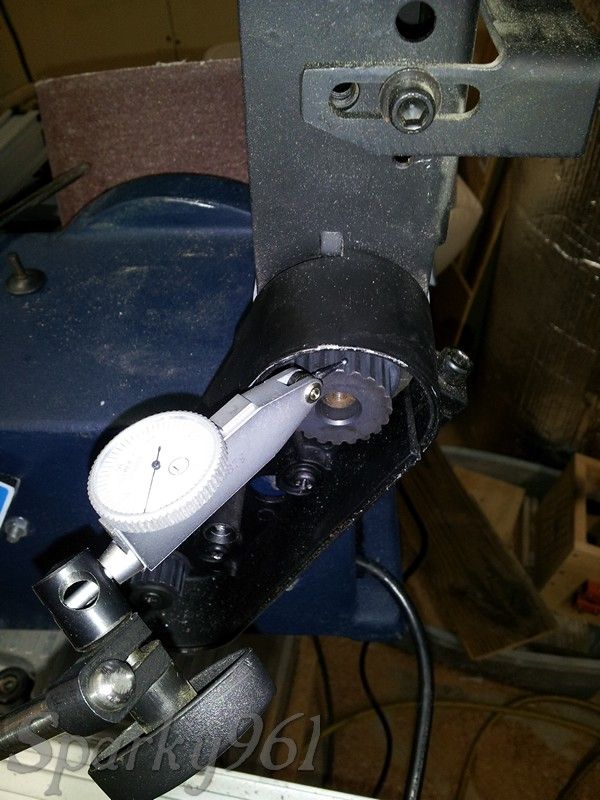
I decided to bore & sleeve them, re-machining the hole on center with the OD. My first challenge was taking the screw out that held the pulley on. It seemed like it was extremely tight and had a gallon of loctite holding it from turning. I stripped the Phillips head after applying almost enough force to snap it, and half-way through drilling it out it started to unscrew.... the wrong way. Yes, it was a left-hand thread.

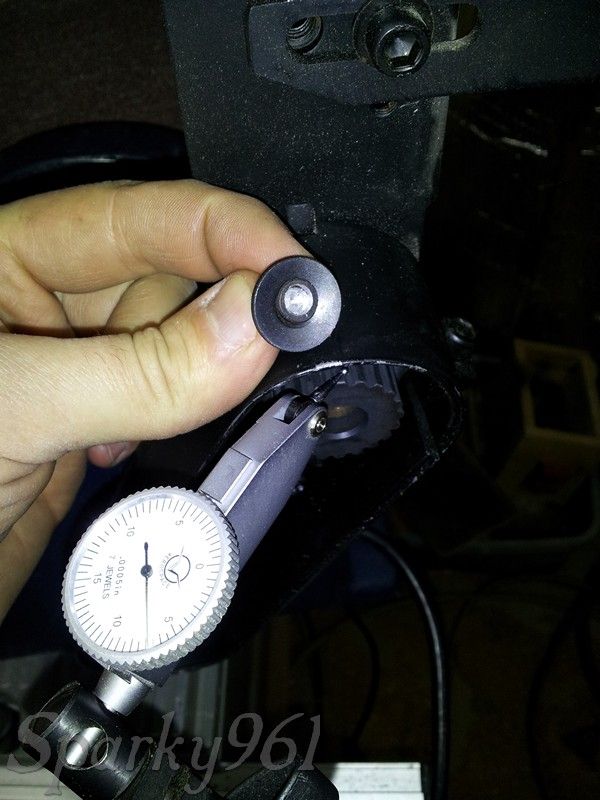
So after removing the bottom one (hey, that came out pretty easily when you turn it the correct direction!) it was off to the lathe to bore out. The upper had a 12mm hole and the lower was 13mm. I decided to bore them both out to 14mm for simplicity of setup.
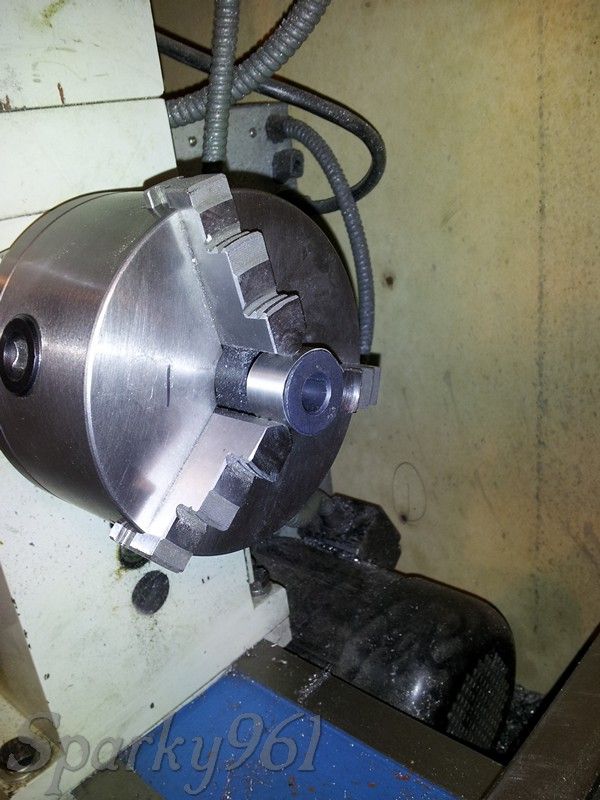
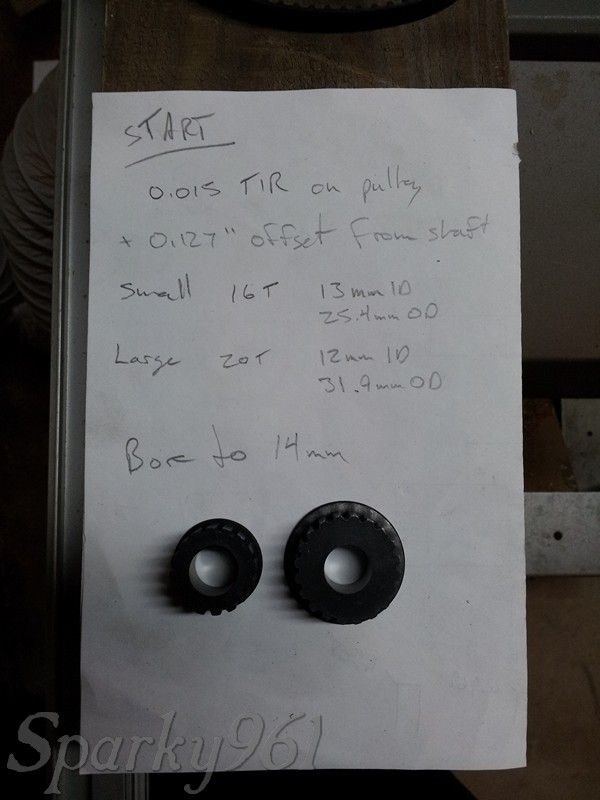
Since they're cast iron, the machining was very easy. When I had a nice 14mm hole, I turned down a shaft to a light press fit and loctited them both onto the shaft. I've had this huge bottle for years, and there will probably still be some left to pass on when I'm gone.
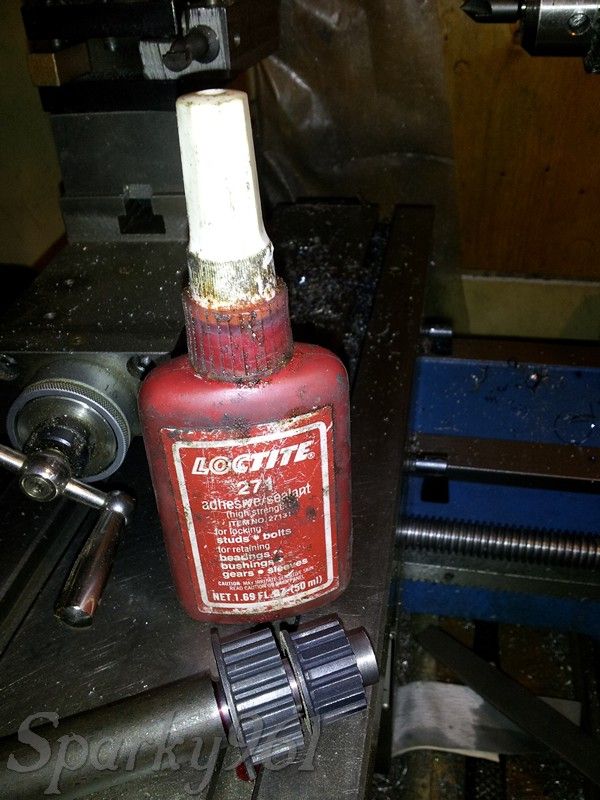
I'm not sure how long this is supposed to take to set, but since there was a bit of a press fit and I was taking light cuts I wasn't too worried about the sleeve coming out. After cutting them off with the band saw, I drilled and bored to size, being very careful not to go over. I made up a gauge rod to check the fit along the way.
Back to the lathe for facing and drilling.
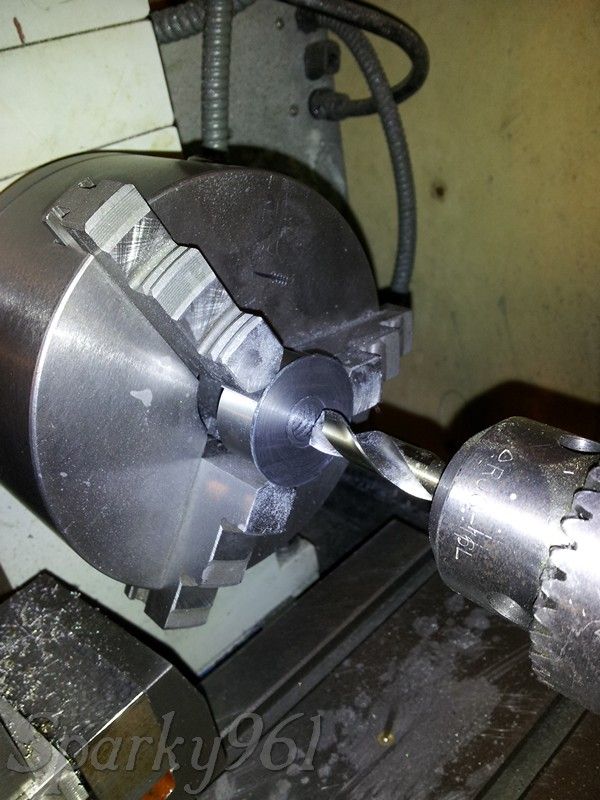
A bit more work cross drilling and tapping for grub screws, and everything is ready to go back together.
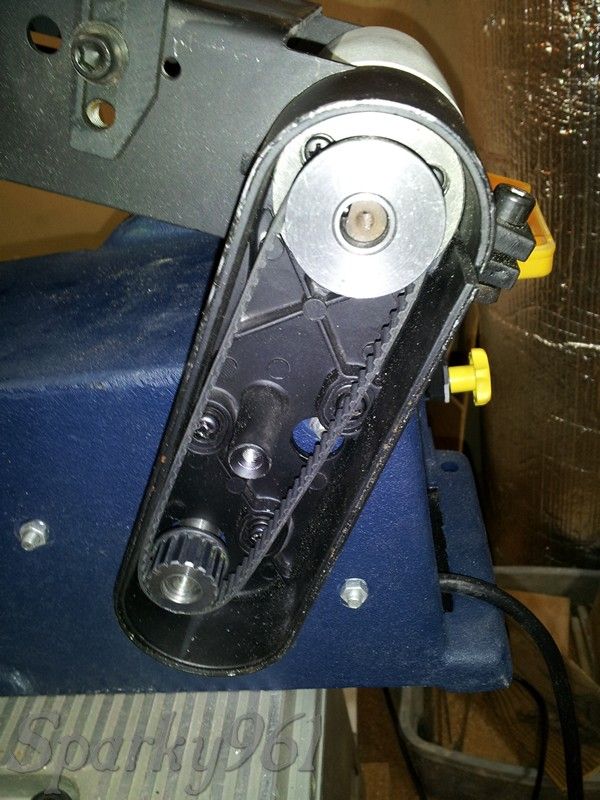
If you have one of these sanders and it shakes all over the place, you might want to consider this fix. When I was done, I re-checked the pulleys and smiled when I saw that they were both within 0.001" TIR. The whole thing runs much smoother and quieter now. All of this took only a few hours tonight (not that I would have minded it taking longer). When I was done, I was reminded of why I like having the capability to make and modify parts.