More updates!

Having thought about the setup before going to sleep, I kind of felt like it would work out the way I thought it out. So here´s the setup.
First I clamped the cylinder in my smallest machine vice. To avoid getting odd angles, I placed a packing at the back of the cylinder and nipped up the vice.
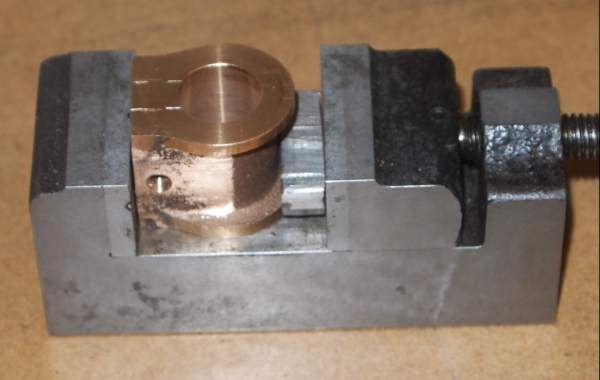
Then I placed this small vice in the big one which resulted in the small one facing correctly so I could see what I was doing, and with a 2 mm drill in the collet chuck I aimed by eye what angle should be used (and wished for the best

)
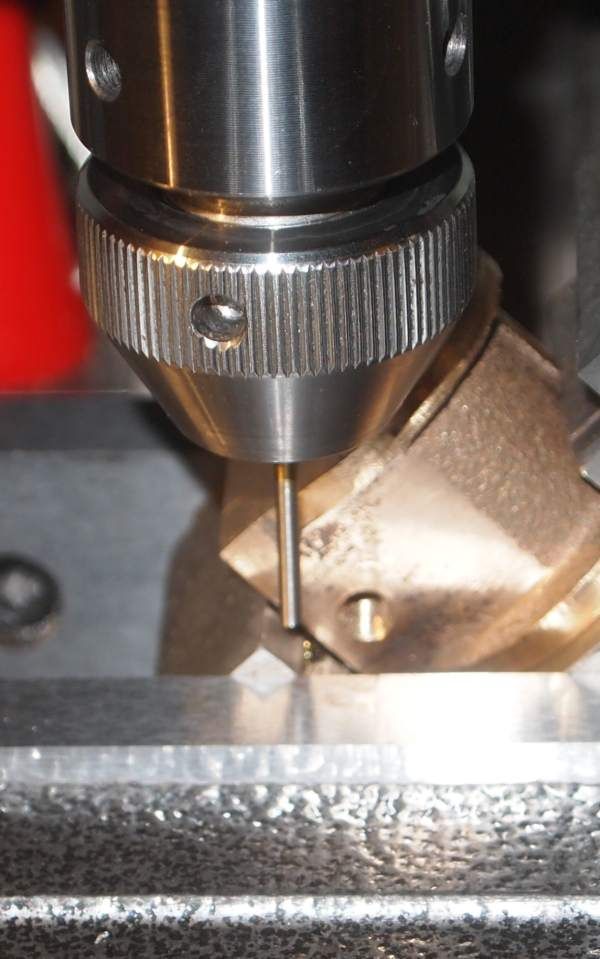
My point of aim was the edge of the cylinder bore and the front edge of the port face with the pencil line showing where the lower edge of the inlet port is.
Then secured the smaller vice in the bigger one, put a new 2 mm FC3 cutter in the milling collet and away it went.
I milled a land large enough to accomodate two 2 mm holes which became about 3 and a bit mm long and 2 and a bit mm wide. After that I placed the milling cutter a short distance from the edge and plunged it down a few mm to give the drill a good and straight start, lifted the mill and re-positioned a bit from the other edge and plunged it for the next hole.
Then change to the drill and drill through to the inlet port.
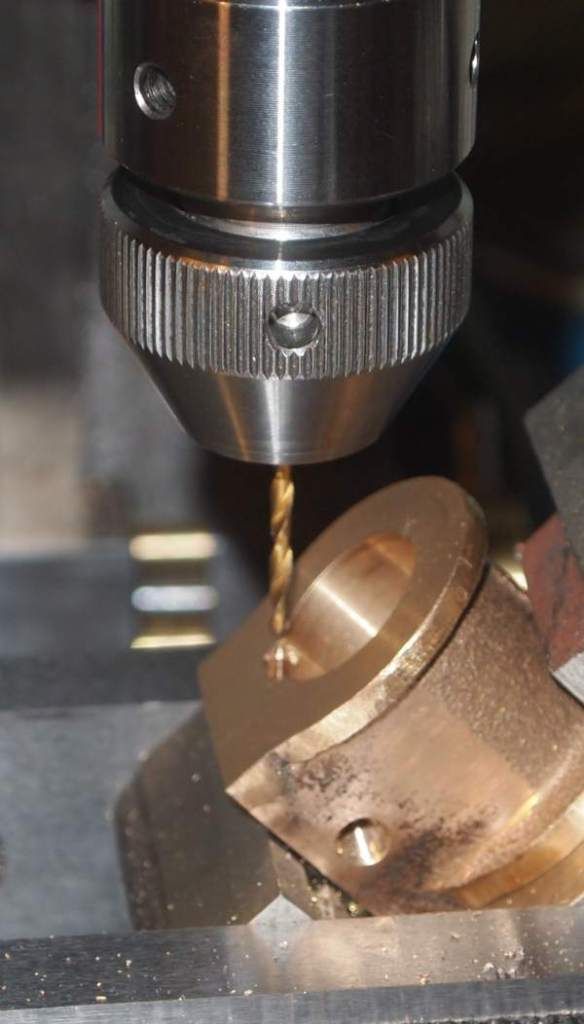
I was a bit worried that I would pass the port as the feeling was not very clear when using the geared feed on the mill instead of the lever feed, but I could actually feel enough to sense when I broke through. Up with the drill and down the next hole.
Then turn the cylinder over and do it all again for the other side. The back on the back to clean the ports out with the 1.5 mm FC3 cutter.
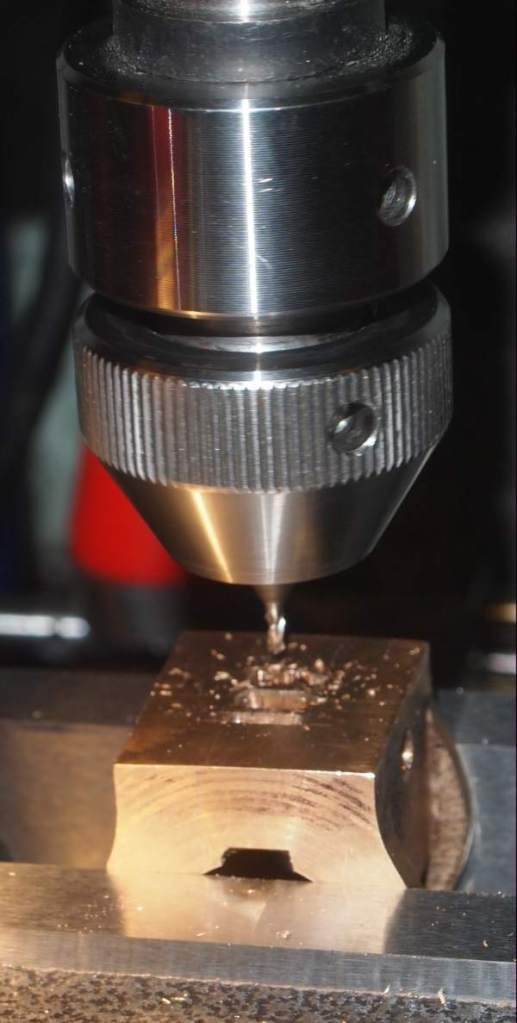
Success !

All holes came out nice and clear right into their respective port inlet as can be seen from the example below.
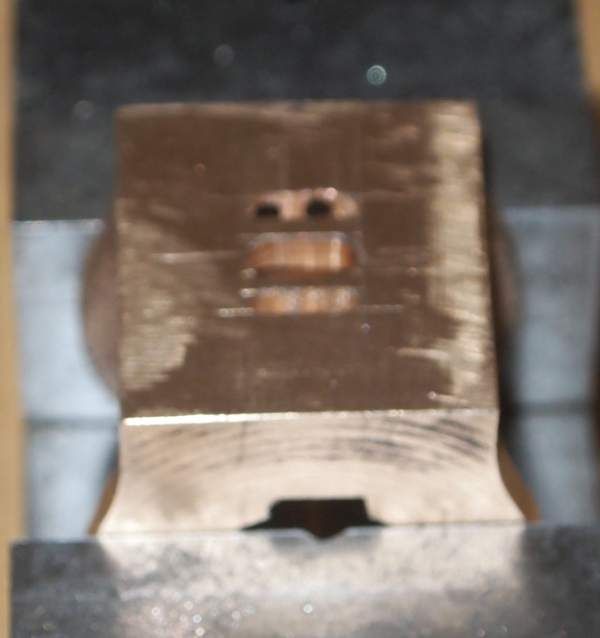
This will mean that the cylinder is done and now only requires a bit of cleaning up.
Work continues ...
BR
/Peter