Hoookay,
Sorry for the delay in posting this item.. but honestly.. I have been deep in
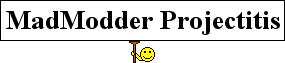
The peck drill is DONE.. and what follows is a posting of the little gem now that its done.
I have been using it a TON, and actually.. I use it for almost all holes I need to drill while On the lathe.
Granted.. I discovered using it for a big 5/8 Hole is NOT a good idea.. only because the bit caught, and it spun the thing smack against the carriage. I hold it lightly, and am off to the side of things, as well as holding the handle lightly. I don’t like forcing things.. When the drill bit caught it was out of my hand before I could blink.
SO.
Be careful!!!! I had to drill more holes, and used my 1/2” MT2 Chuck after that for the remaining hole.
BUT… enough of the health and safety speeches.. ON TO THE PICTURES!!!
First thing I needed.. was a way to hold the hex handle in the mill vice so that I could drill the hole properly on the flat. But it’s a hex… sooo how the heck do I mount it in the vice???
And as I am still new.. I thought long and hard.. and decided to make a fixture to accommodate that. Of course.. after I finished it, it dawned on me that people have those already…
Fixture to make handle pivot:Starting with a decently thick chunk of aluminum I put my dovetail cutter in the mill and decided to see how it liked aluminum!

As you can see No sweat.

Little cleanup with my tiny End Mill

Make it square

Voila… nice and square with a groove. What you don’t see is the pic of me cutting that in half to make two of them.

Tada!! New Tool in Use! Drilling that pivot hole.
Pivot Bolts, and BushingsNext up to make were all the pivot and slide bolts.
Turning a 316 Stainless rod after tapping it..

Pre-finished bolt, longer than required.

Here we have the bolt through the shaft with extra sticking out. (the additional clearancing I did in a in-between step fitting the handle and the shaft to get maximum throw. Doing this again I would have put the pivot further in and made the slot wider, as well as the bevel in the handle)


Quick spin in the lathe and the ends are trimmed down to be flush with the shaft.

Trip to the hobby shop down the road and some brass tubing was purchased that was ¼” ID. Sooo a little spin in the lathe and a little persuasion with a sharp edge file.. voila Bushing.

Handle Trimming:Next up.. the handle needed to be trimmed in the mill so that it would fit into the slot in the shaft.
The handle was then chucked into my new V-Block thing.. and I got the edges with the edge finder, got the middle with a little math, and then I figured how far to mill into each side of it. (of course accounting for slop in things since I was cutting from two different sides, and measurements were a little fun)


Final pic of the handle with the bushing and bolt made for it.
Main body bushing:The next thing I figured I would need, Was a bushing for the main housing. This is what I was thinking after reading about Bogs repairing his tailstock etc. I figure any vibration etc will result in wear at the end of the housing.. sooo Making a bushing long enough to support the shaft would be critical as a wear part, and also to prevent galling between the shaft of mild steel and the body that is stainless.
I started with a .99 Cent double ended gas fitting I chucked up and turned on the lathe.

After measuring the outside diameter of it I bored the main body out to slightly smaller than the diameter of the brass bushing… and to be 1/8 inch or so too shallow depth wise.


I made 5 or 6 passes without changing the lathe settings to make sure any deflection in the boring head and or lathe carriage was not leaving the hole tapered. The second pass brought our a small pile of stainless on the boring bar, and subsequent passes resulted in less with each time, until the last two were clean.
A firm press by hand got it in about half way. From there I used a 28oz persuader to help it seat properly.

Little clean up of the face and she is ready to bore.

Boring.. boring.. boring… Man I have the cross feed at its SLOWEST.. it does cut real smooth.. but it takes forever.
Result??Ohhh SHINY!
Taper Time!!Sooo I needed to bite the bullet and figure how to cut a taper.
SO I listened to the posts and advice.. and did what was suggested.. Mount a dial indicator on the cross slide and adjust till you have 0 deflection.

Result?? JT-33 Taper on the shaft!

I also did the same for the tailstock MT2 taper. As the original was/IS crooked.
BLINGIFICATION!!!!Ok could I leave it a cylinder of stainless? Of course!! But I have some neat tools.. and here is a perfectly good excuse to use them!!!
SOo a quick change of tooling.. and the ball turner goes to work!
How about a little radius?


And lets round out the snout!

Not bad…

A little work with the polisher and here we are:

Retracted:

Extended:

NOW.. what you
don’t see is my utter frustration when I tried the damn thing in the lathe… and the threaded store bought MT-2 to 5/8-16 arbor was so badly off.. that the drill chuck was off by a HALF INCH at the chuck end when retracted!!!
I then took the next day to make my own arbor, and Point thread it myself. Yep.. the first time I ever point threaded anything. And it worked.
Here it is in the lathe…

Think its Accurate enough?? That’s a ¼” chamfer with a sharp point.. and a small spotting drill. I let them touch with the cross slide not locked down and moved the lever and they stayed point to point.



End result sitting on the lathe:

I will try to compile a video clip of it working. THe shots on the mill are DARK as I didnt have a light for the mill. (Im working on that one too)
Scott