[Moved from homemodelenginemachinist.com]
Guess what I found in the old fixings jar? Not one, but two 1/16" pins

The newer fixings set that I got recently from Stuart for this engine didn't have any, so I'm glad these castings came with their own fixings set.
Made some good progress today. I'd been putting off milling the exhaust steam passage, but did so uneventfully, after carefully marking out the exhaust slot, and the exhaust hole on the side (with the same center height, of course). The two inlet holes were pretty wonky in the casting, and one is a bit wider than the other, so I tried to center the exhaust as best I could between them. Milling was starting with a 3/16" end mill, and finishing off with a 1/8", then the corners were filed square.
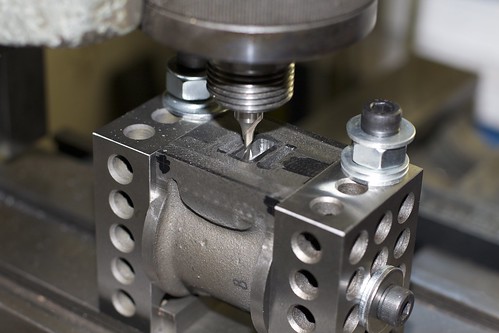
I probably should have drilled the 1/4" exhaust hole first so I could just mill down until I hit it, but did it the other way around, and it worked out OK.
Given that the steam ports aren't quite equally spaced, I wonder how smoothly the engine will reverse once complete. One possible solution would be to make a plate with accurate ports, mill a recess in the casting and silver solder it in, but I'm not keen on doing that unless I absolutely have to.
While I had the cylinder set up, I also drilled and tapped the holes for the exhaust manifold thing, and the lagging screws. Interestingly, the older models used a 5BA lagging screw (left side below), and the newer ones a 7BA (right side; the screws are in the exhaust manifold holes; I'm just trying to compare them visually here); I chose 7BA for now.
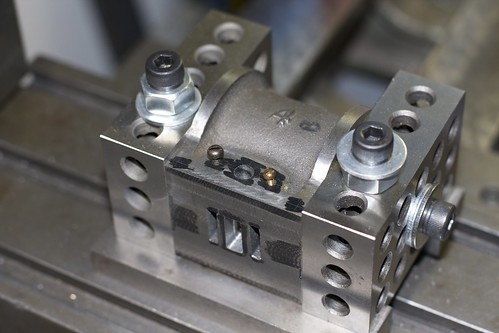
Now to drill for the drain cocks: spot-face, center drill, drill through and tap 3/16" 40TPI:

and the cylinder done except for the stud holes on each end:
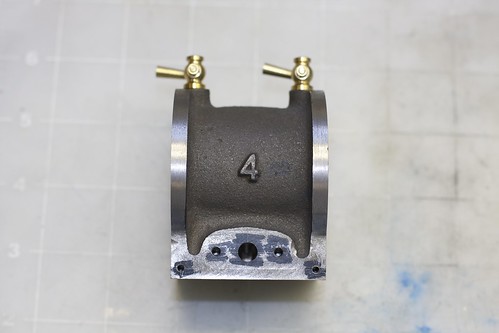
So, lots of stud holes to drill and tap: 6 on one end, and 4 on the other. I broke out my recently purchased 4" Phase II rotary table, centered the table under mill (via an MT2 arbor in the center hole), then centered the cylinder casting on the table. Boy, clamping things on this teeny table is tricky!
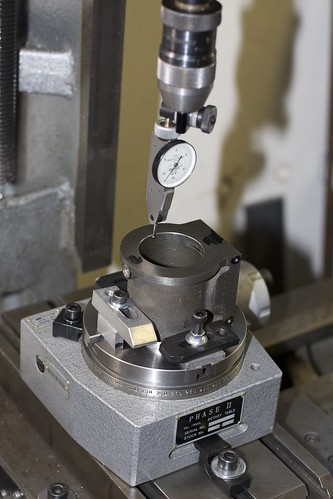
Once everything was aligned I cranked the carriage along by half the bolt hole diameter, and I'm ready to go!
I drilled the top cover and the tapping holes at the same time (the cover was clamped for drilling), turning in 60° increments, then enlarged the holes in the cover to clearance size. Then I went back around the holes for tapping; I found that the rotary table was precise enough that I could accurately return to a hole position, which is nice. I started the taps in a chuck in the mill (turning by hand) to keep things straight.
6 holes tapped, and the moment of truth: does the cover fit?

(Spot the odd stud out!) Yay! In fact it fits in any orientation, so I guess I counted the rotations right

After that I did the 4 stud holes on the base on the cylinder. 4 holes this time, so line things up, rotate 45°, drill, crank 90°, drill, crank 90°etc. I jotted down the angles, and used those to double-check my handle-turning count.
Drilling the standard really pushed the limits both of clearance on my mill, and clamping on the rotab. I could just get the drill into the chuck, and don't look too closely at my clamping job here

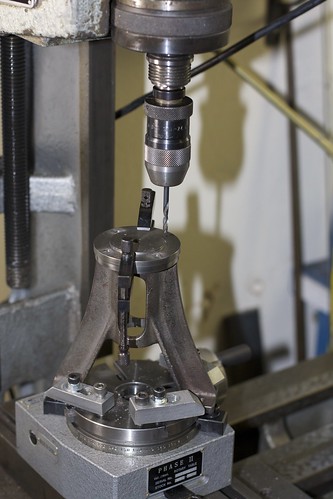
I was relieved when all the drilling and tapping was complete without any broken-through holes and broken taps. Now for the fun part, assembly:

Wow, this thing is beginning to look like an engine 8)
Next up will be the piston rod gland. I'm a bit concerned about alignment there, having read another recent thread here about that. I have the right taps and dies (1/2" 26 TPI), but I wonder if single-point threading would be something to consider, having never done it before?
Thanks for following along,
Simon