Stew’s plans (THANK YOU!) were too tempting to be left seasoning into the to-do list and that lump of C.I. has been sitting on that shelf for
so long it had already started to bend, that I could not spare myself from thinking about them while machining parts for another project I was working on.
Results were I planned them wrong, and performed so worse I ended with being thrown a workpiece at by an angered lathe.
I’m OK, it missed. But...
..where’s the point into spending precious shop time without enjoying at full what I’m doing?
A quick glance at the “current projects” boxes on the shelf and the contents of my double sized Elmer’s #3 went back among the raw materials.
That 'doubling' idea was never good, btw: that little thingy was nice because it was little, when doubled it was losing most of its appeal.
Hope You will enjoy this e-travel as much as I will do, wherever it will take.
The Cylinder BlockThat’s the only piece I have in suitable sizes, I’m not even 100% sure there will be enough meat beyond the crust to get the job done.
What I will find inside of it, I plainly do not know.
First problem I had to face was about holding it into the vice: the jaws were not deep enough to hold it above its centreline, no parallel lines
(let alone surfaces) to ease the job, and one only small almost flat area where it was sawn off from whatever it was attached to.
Put it lenghtvise into the vice, enclosed between a couple of clamps used as additional jaws, then machined a starting flat on top of it, using the oldest,
dullest, roughing mill I have, 20mm dia. IIRC.
Did not want to risk the precious carbide inserts of some other mill more suitable for the job.
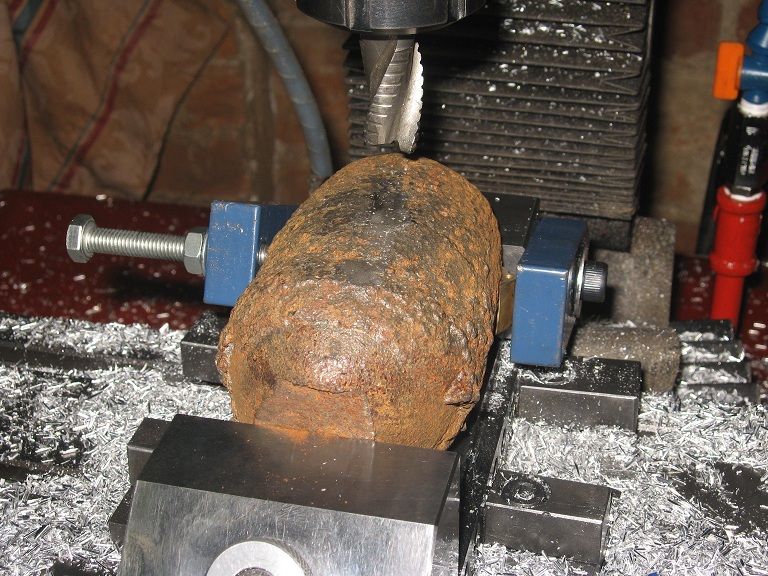
The HSS mill didn’t last long, the glazed crust having quickly had reason of what was still in its cutting edges.
But the setup was firm, and that was what I wanted to know for sure. Time for a change.
Now on the opposite surface, as parallel to the first as I can get it. Parallelism is not an issue, at the moment:
I will choose later wih one of the two will be used as reference surface to machine the others.
Made my choice. From now on, all machining will be done between fixed jaw and dovel, with parallels (if HSS blanks can be so called) on the final cuts.
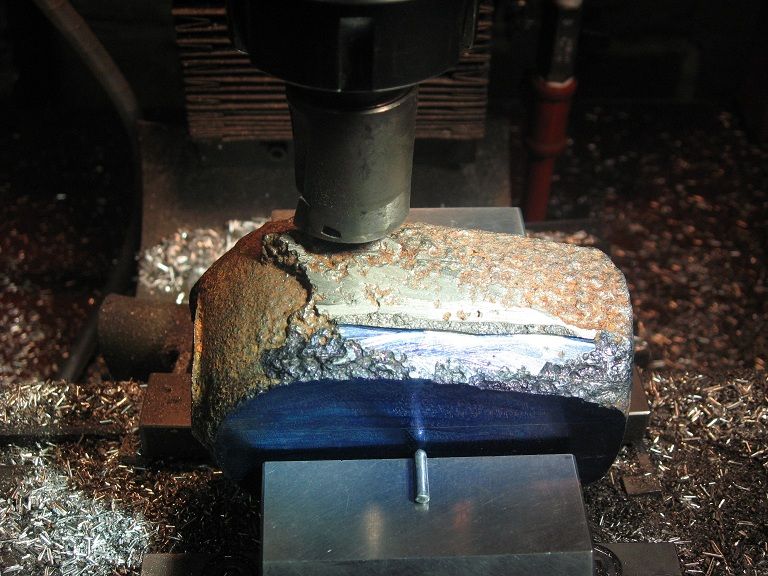
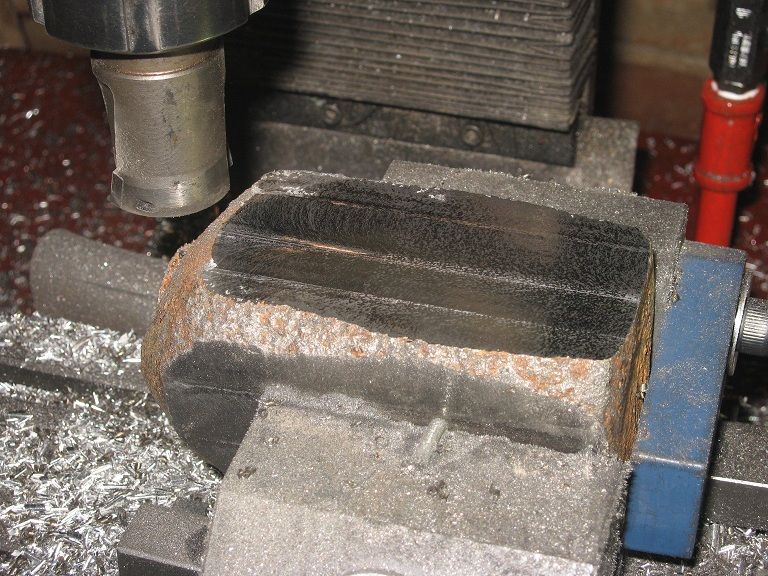
No climb cuts were taken while using that 2 inserts 30mm mill, unused axis locked, max depth I could gain was 1.1mm
(above that, the quill raised by itself during the cut, however tight I locked it), speed around 1300rpm, cuts maximum 12mm wide (if not for some operator’s errors),
feed.. eh.., feed was just cranking like hell: the faster the better (the less the machine was complaining, the better the finish).
Several hours of that, rather tiresome in the end.
I wished I had a suitable arbour to put this 63mm monster to the test.
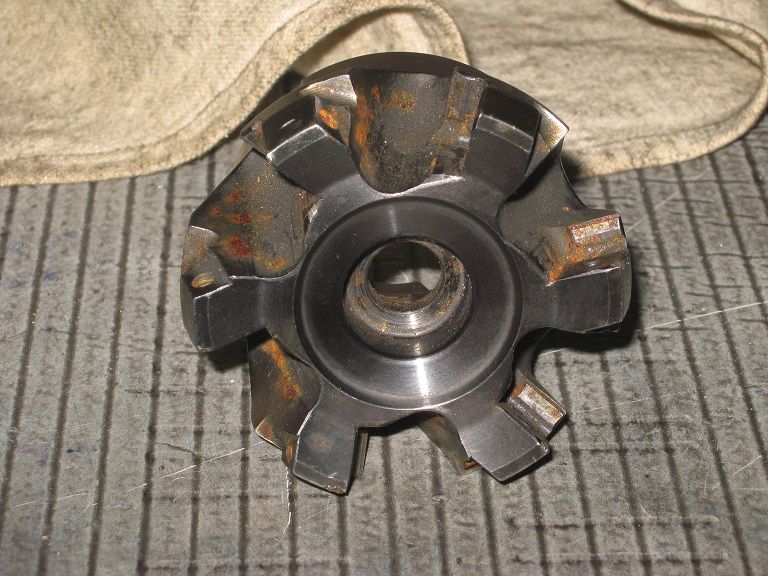
End of the day, if not of the job: the piece is to size within the limits of my measuring tools, a few voids are starting to show - that’s not good news, we’ll see.. –
As for what I’m planning for next, recent experiences taught me to begin with drilling a hole somewhere in the material I’m gonna discard and test-thread it:
don’t want to risk ending with a finished cylinder I cannot tap (though I would probably find press- fit or loctite the studs, if that were the case).
The eventual behaviour of my boring head on C.I. in general, if not on that workpiece in particular, is a mystery, too.
We’ll see.
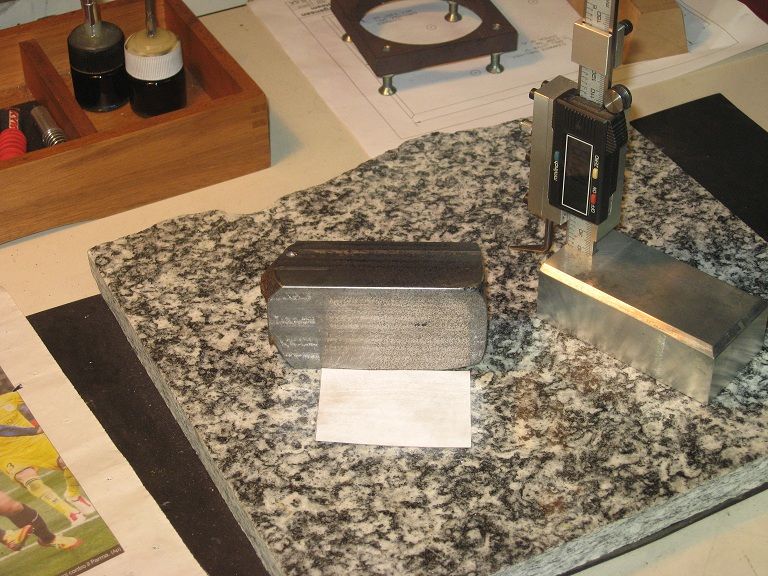
Marcello