Part 1
This was first done to show new guys to machining especially the lathe how to make something. Using different lathe operations and a single carbide insert tool.
This is how I went about making it. It is important to realize this is my way, it is not necessarily the right way.
There are many right ways to do the job right.
Sit back and enjoy.
This is what I am going to make, No…. the brass bit. not the callipers.
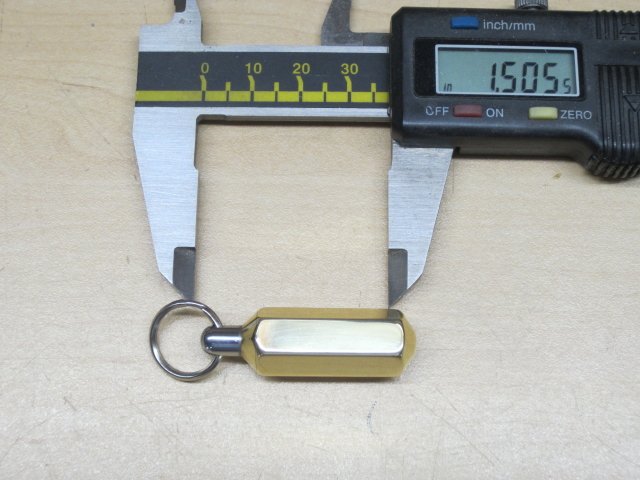
Here are the materials.
Some stainless steel (free cutting) 14mm dia
Brass hex 12mm
Round brass 14mm dia
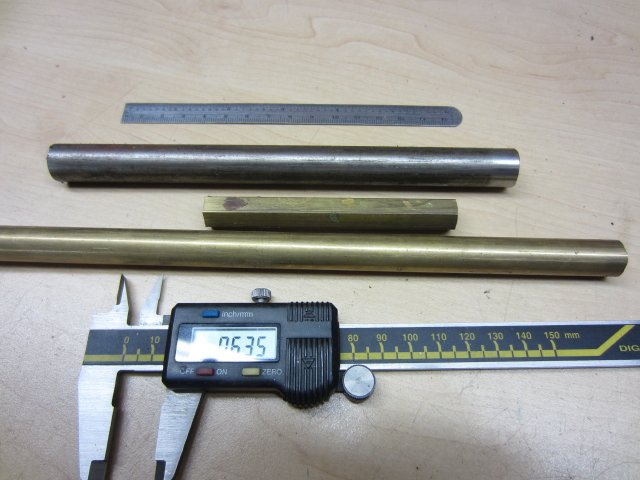
Here are the 3 components that make up the swivel keyring.
Starting at the left the ‘end cap’, ‘swivel’, and the ‘body’
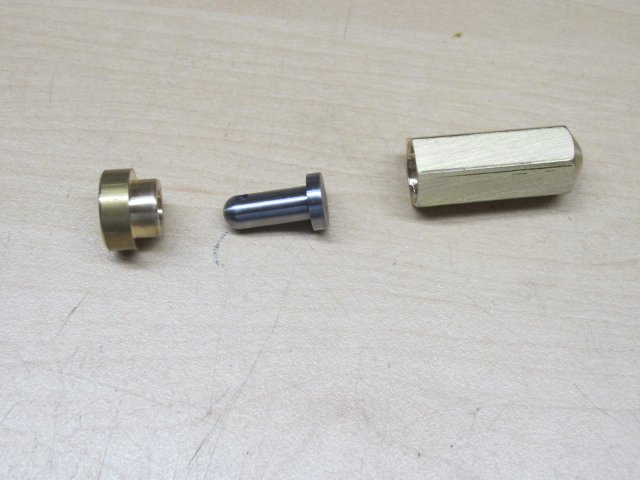
I started with the hex brass to make the body.
Faced the end.
Notice the brass shim material to protect the brass.
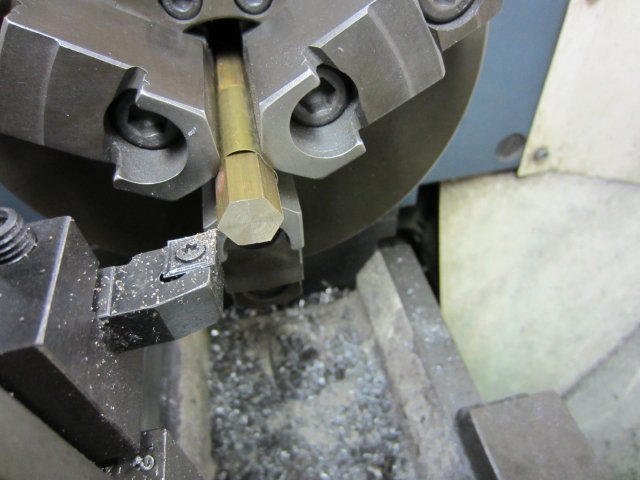
Then it was chamfered at about 45 deg. I just turned the tool around and fed it in slowly, I also reduced the spindle speed to about 500 rpm.
I didn’t want any chatter marks.
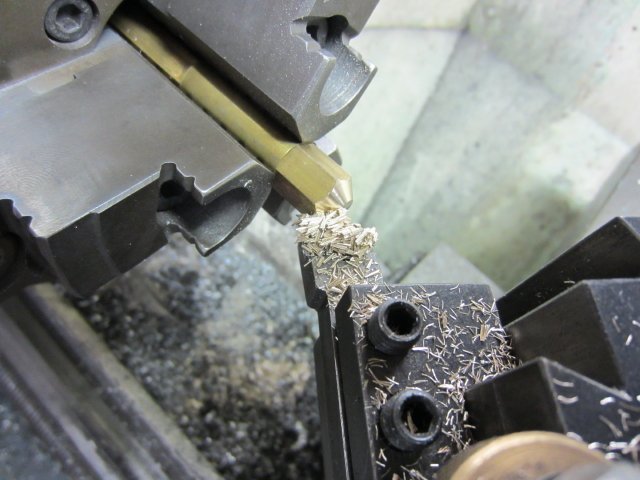
And this what I ended up with.
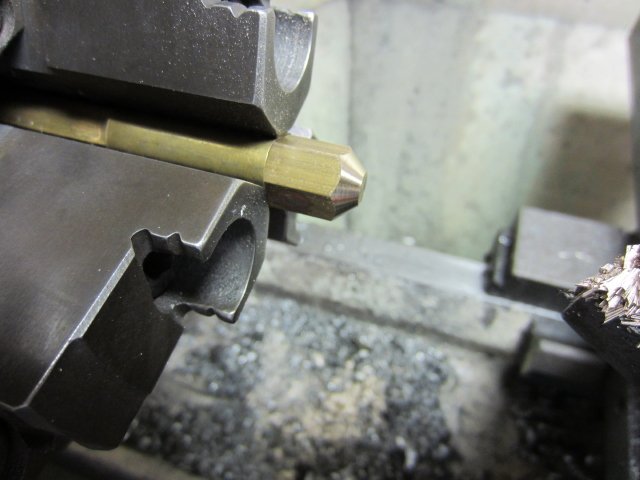
Mmmmm ….. didn’t like the 45 deg chamfer so I changed it to about 30 deg.
Did it again
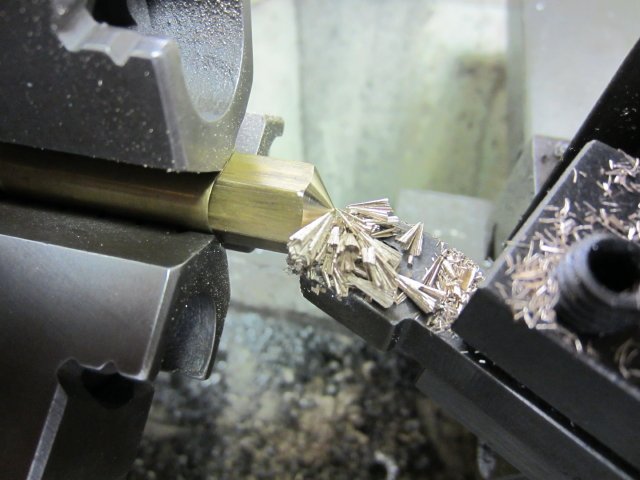
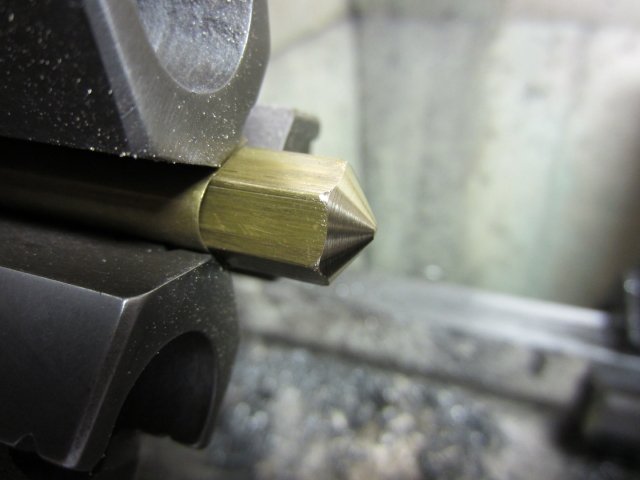
I didn’t want a pointy bit on the end so that went.
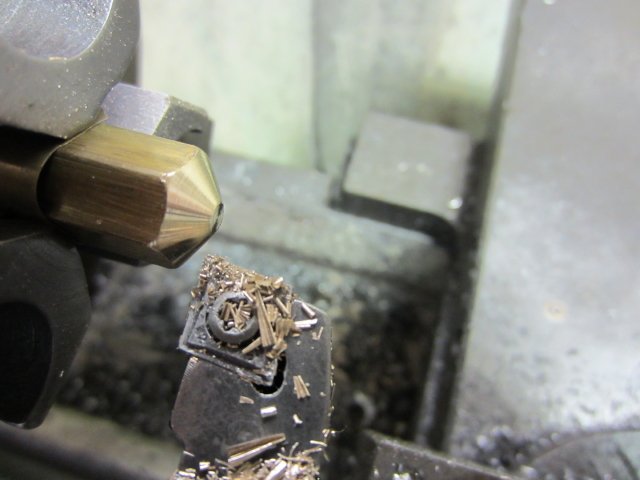
A bit of gentle use of emery cloth (fine).
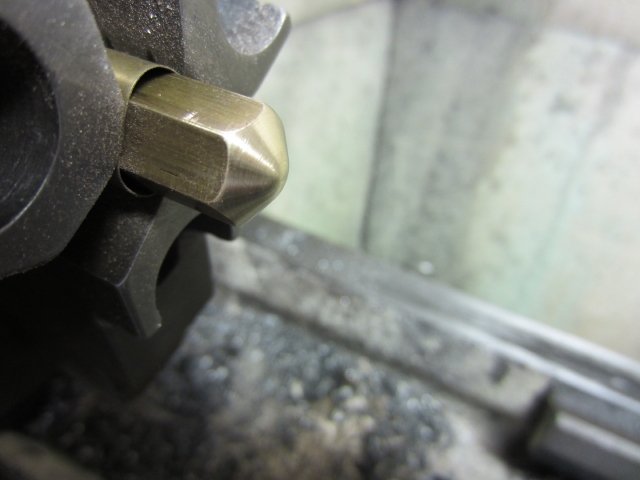
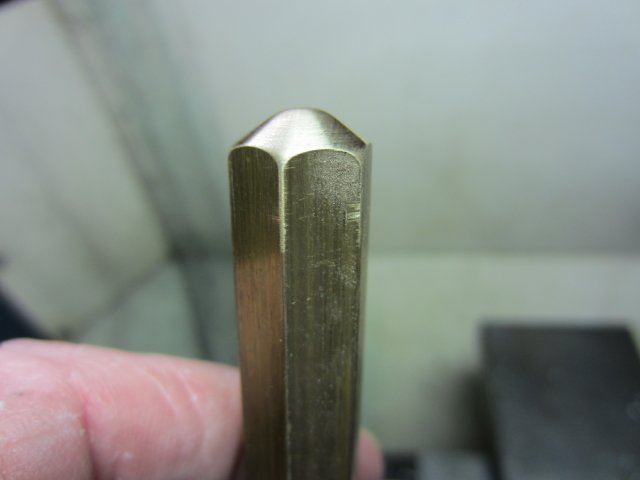
Now we cut it to length
A quick estimate, and mark.
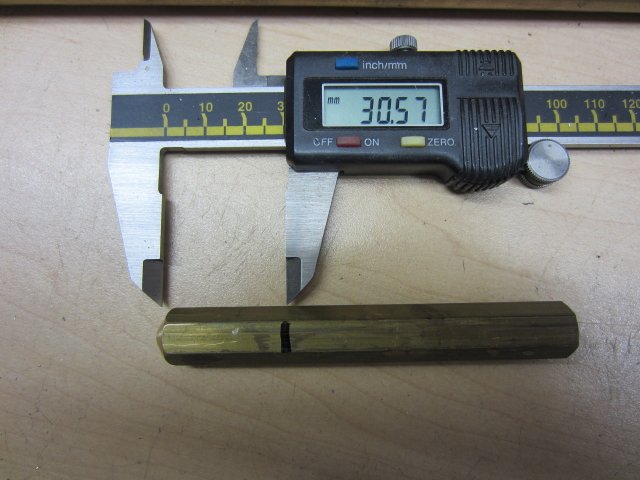
Cut, that’s the finished body length – roughly.
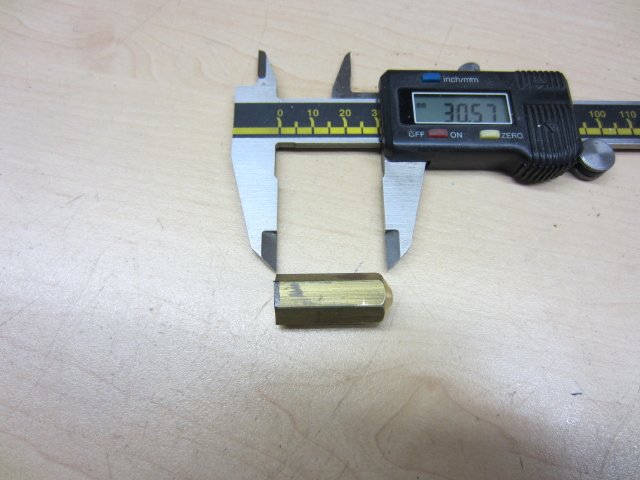
A quick rub on some fine emery to get rid of any burs.
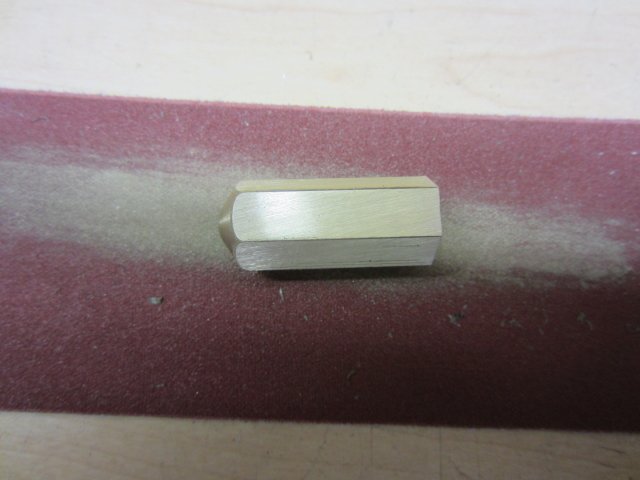
And it’s back to the lathe to machine the other end.
Faced and ready to be spotted.
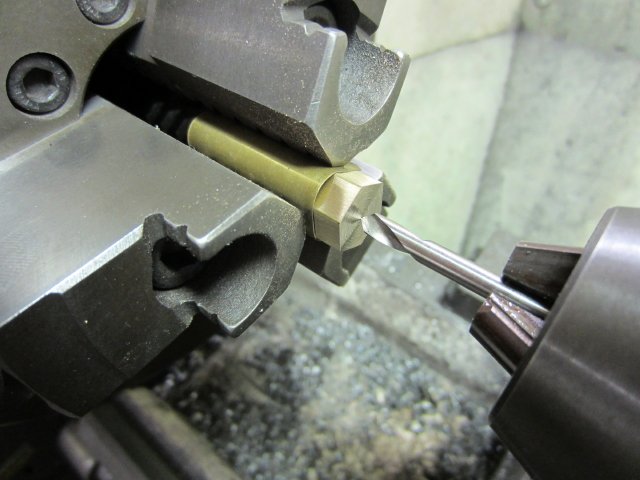
A hole was first drilled (6mm dia) then a 10mm dia hole with a 10mm end mill about 6mm deep.
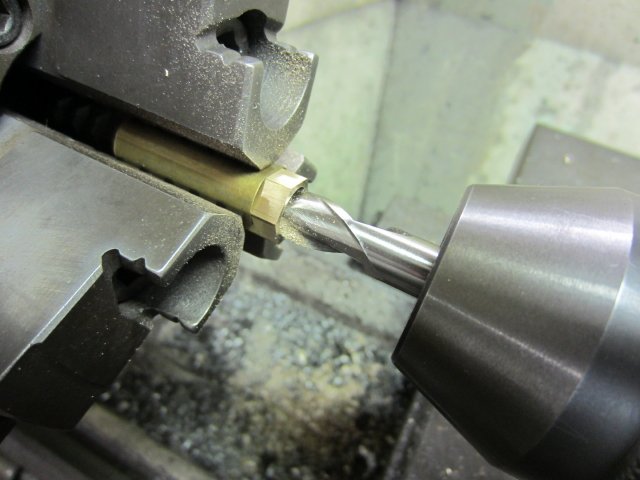
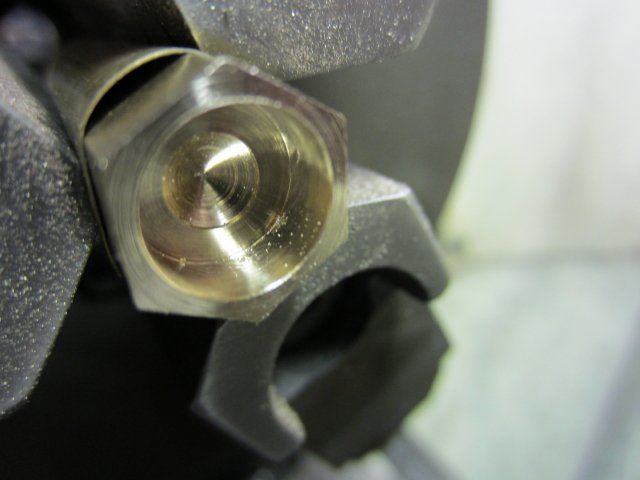
So that bit is finished for now and can be taken out of the lathe and put on one side.
Still needs a bit of cleaning up, but I’ll leave that until later on.
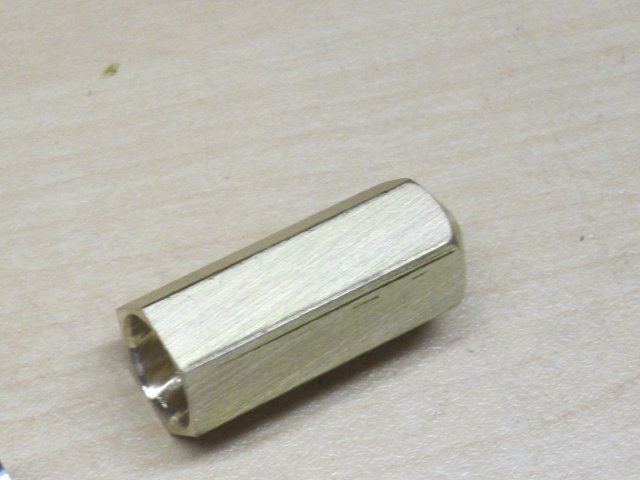
Part 2 to follow.
DaveH