
Thanks John. I'm still struggling a bit with steel, but it's growing on me; just some more practice needed
After the "Homer Simpson" moment last weekend, I picked up where I left off this morning.
First I set the fixed steady to size on the thickest bit of the workpiece close to the chuck:
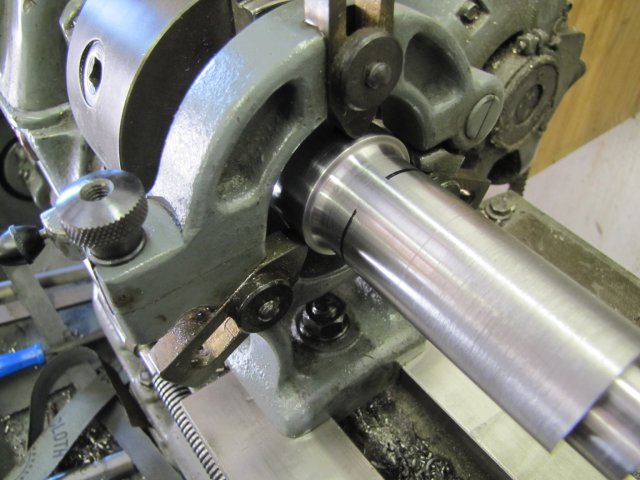
Then I mounted the 4-jaw chuck, moved the fixed steady toward the tailstock, flipped the workpiece end-over-end and carefully and accurately clocked it up in the 4-jaw - leaving a bit of run-out space for the taper next to the chuck:
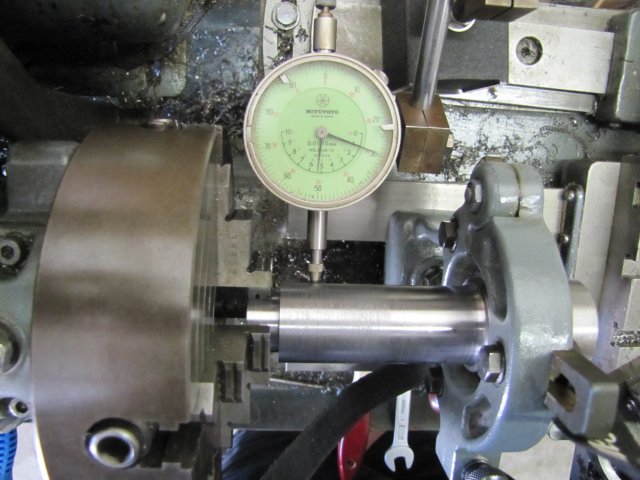
The end of the workpiece had been cut with an abrasive cut-off wheel, and silly me; I'd forgotten this is higher carbon steel than the normal crud I work with. There was a HARD spot on the end which promptly took off the cutting edge of my favourite HSS cutting bit:
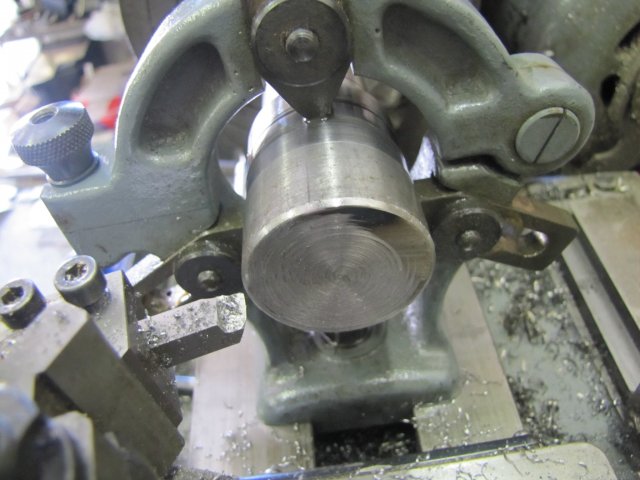
I could have tried brute force with one of my seldom-used carbide bits to take off the hard section, but I didn't want to get things out of kilter, and I didn't want to put too much of a load on the steady. So I attacked the hard bit by making an under-cut on the face - trying to get "behind" it:
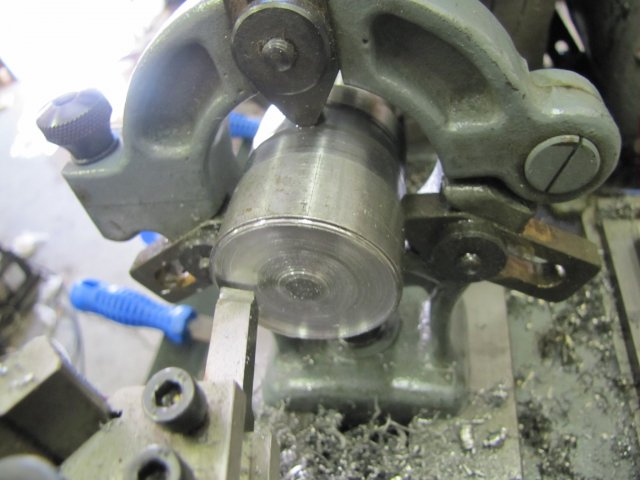
The under-cut worked

, and I got the hard section off, so was able to get it properly faced and center drilled for tailstock support. I also had to skim off the thicker section protruding between the steady and the tailstock, so that I could get the steady out without changing it's setting:
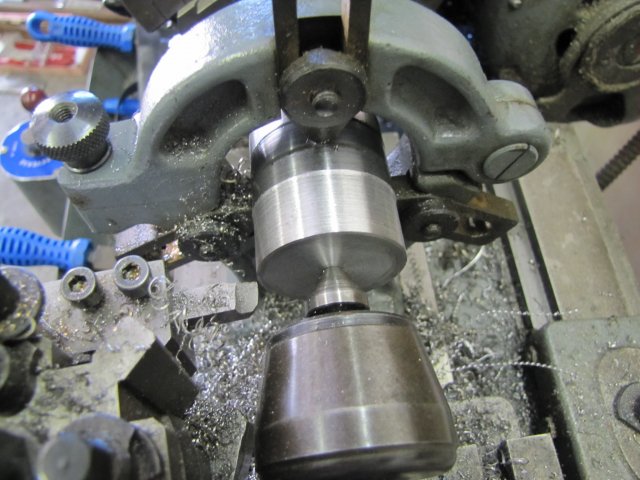
With the steady out of the way, and proper tailstock support, I could turn the taper:
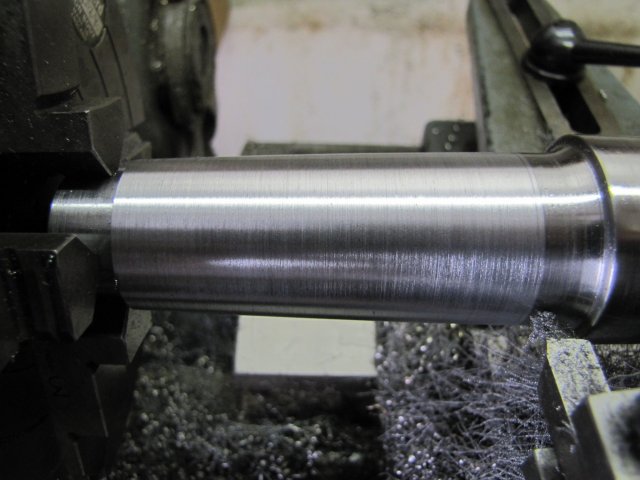
It looks like a dog's breakfast in the previous photo, but a very light rub with some scotch-brite had it looking OK - far from perfect, but good enough for here:
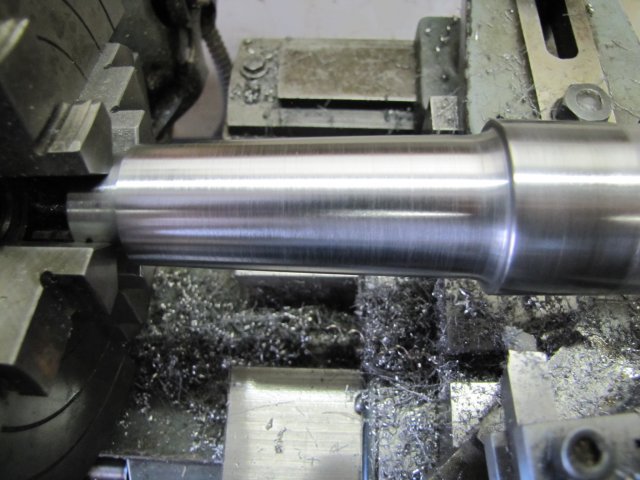
Next I turned the end down to 32mm and put in a thread run-out groove with the parting tool:
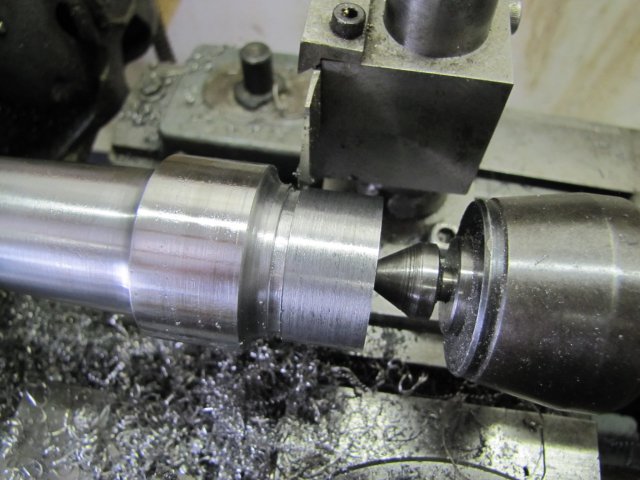
A quick hone of a 60
o threading tool, and set up using a thread gauge:
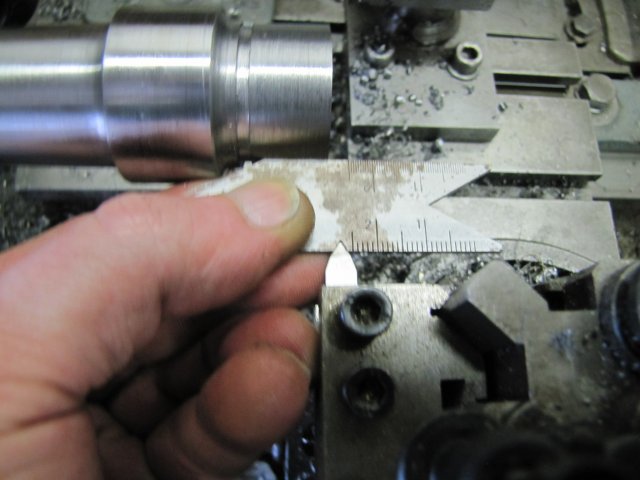
Next a couple of minutes setting up the change wheels for 1.5mm pitch and a very light test pass - checked with a tread pitch gauge:
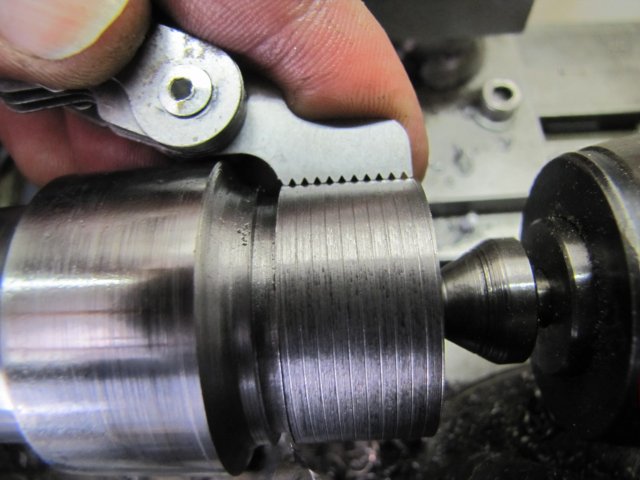
One of my favourite pastimes on the lathe - screw cutting - over much too quickly - but on size and smooth. The gritty bits in the threads are just some swarf:
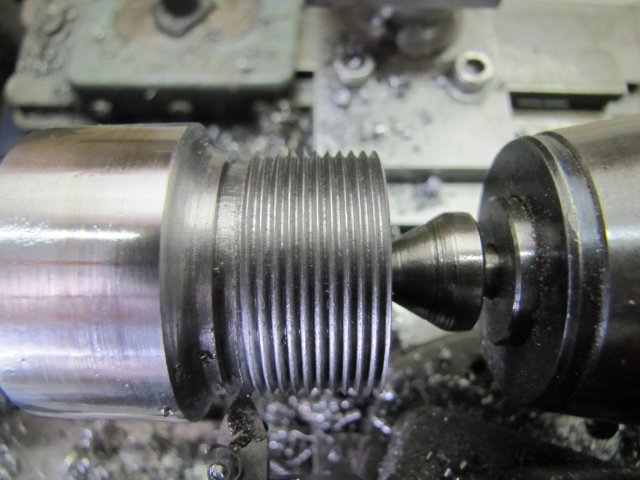
The closer nut spins on easily and smoothly, with virtually nil free play in the threads:
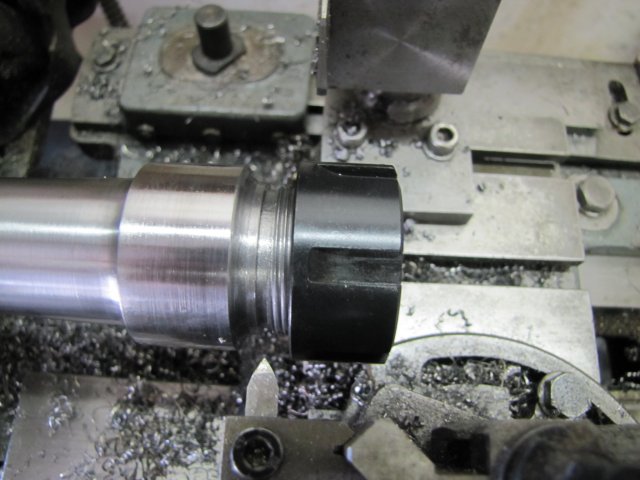
Next, the steady back on, and some drilling - about 90mm deep, and 16mm diameter; it should have been 18mm diameter, but I don't have an 18mm drill:
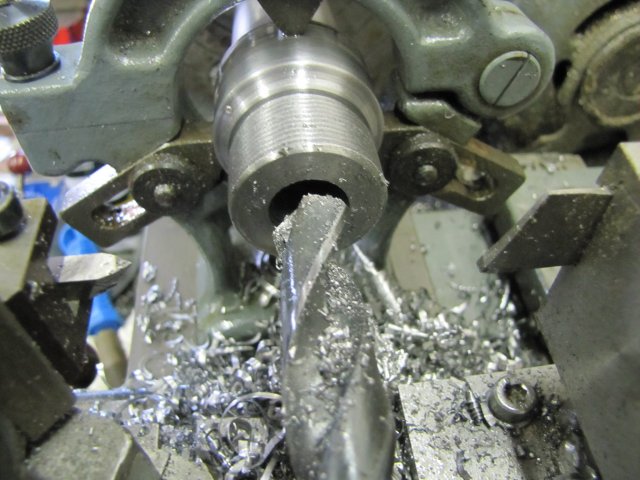
On previous ER chuck builds, I'd simply set my lathe's top slide to 8
o with the cutting bit spot-on on center line, and have not had any problems, so that's exactly what I did next, and then bored out the taper:
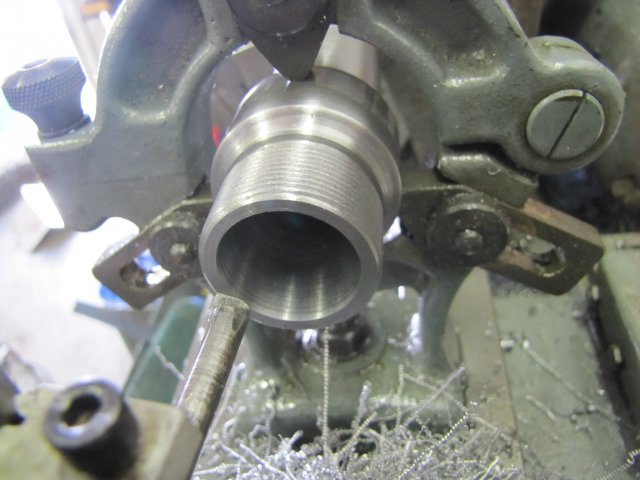
The finish looks a bit rough, but it is in fact very smooth; the banding that's visible is streaks of cutting fluid.
A quick test with a bit of 16mm silver steel chucked up in the 16mm collet, and there's less than 0.005mm of run-out; plenty good enough for me

:
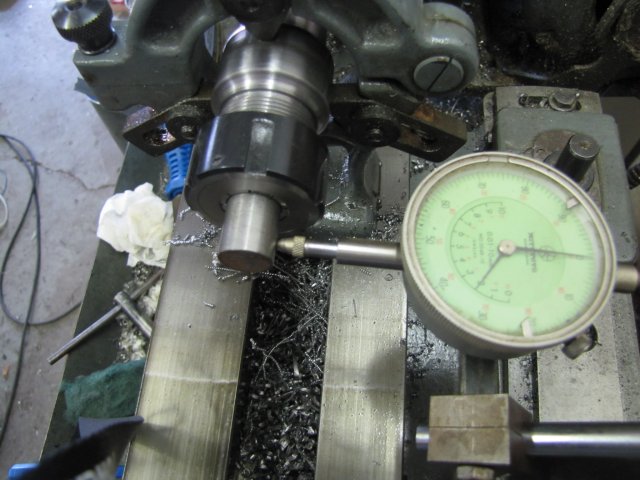
I still had to drill and tap the end for the M12 draw-bar - so I just chucked the new collet chuck end-to end on the lathe's collet chuck using that same bit of 16mm silver steel, then set the fixed steady to size to run on the short thin section I'd left at the end:
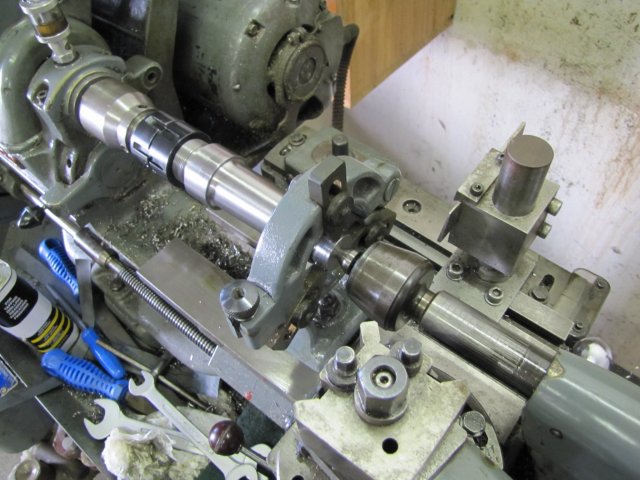
Then I had a thought; I'd obviously need a way to hold the chuck with a spanner/wrench! - So I took the lot off the lathe, set the dividing head with it's tailstock support up on the mill, and plonked the lot in there:
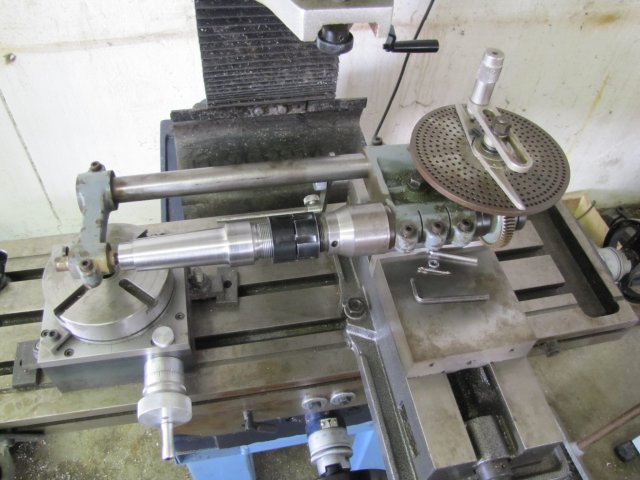
Then milled out six 2.6mm deep grooves for C-spanner use:

Back to the lathe and set up as shown in the third last photo, and drilled and tapped for the M12 draw bar:
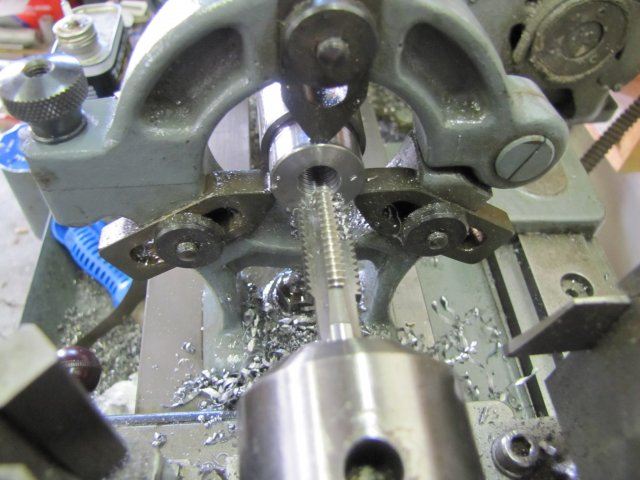
A bit of deburring, and the chuck's done:
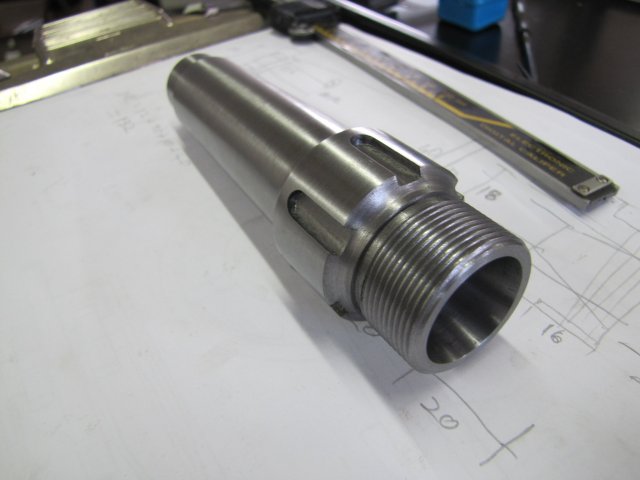
Compared to the "non-ER" Eastern chuck I've been using till now (on the left in the photo) - it gives me about 25mm more headroom, and as it's not using a MT reducer sleeve like the old chuck, a bit more rigidity and hopefully some more accuracy as well:
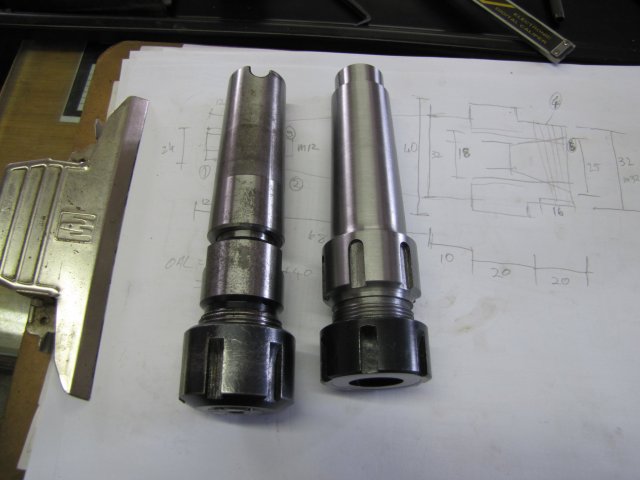
Installed in the mill spindle - the taper fits a treat:
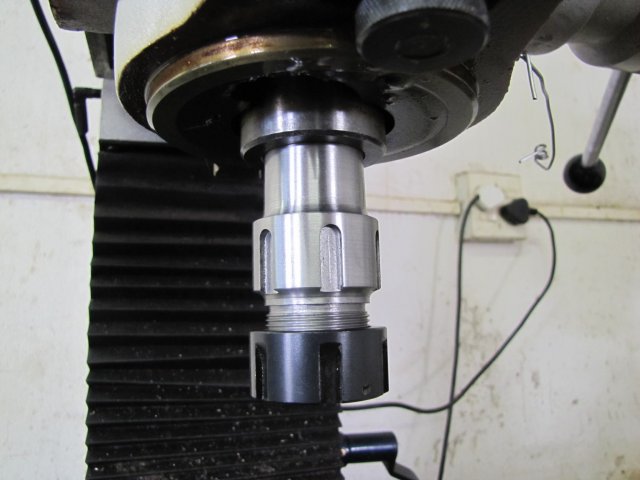
A quick try-out in some aluminium; I'd used the flycutter to face the lot, and then ran the 16mm mill 4mm deep through there at a good clip; the finish is OK - definitely better than what I'd been able to get with the other chuck:
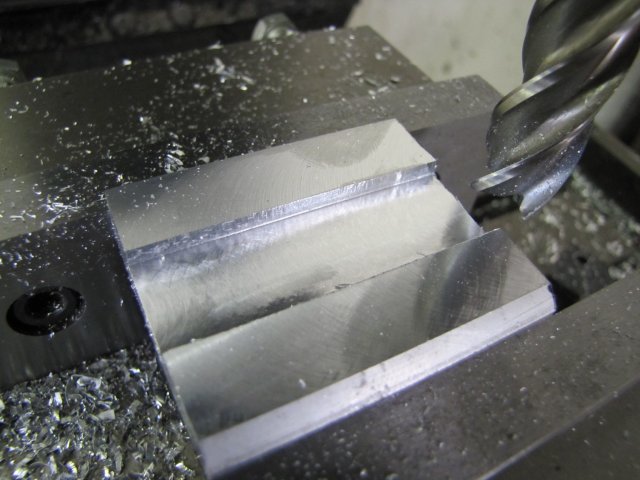
And the best part - no heavy-handed hanging on to spanners to tighten or loosen the closer nut; it works a HECK of a lot better

, Arnold