I've not been updating my progress here as I was rather caught up with my day job. The work continued last Saturday for a couple of hours and Sunday for another hour or 2.
The drawbar washer was completed and the collet chuck was put into use. The bore at the gear box cover was widened due to its misalignment to the spindle end. Now I can remove the drawbar without having to open the door.
The washer on the spindle through the bore of the gear box. You can see the misalignment here which require the widening of the bore so that removing the washer can be done without opening the gear box.
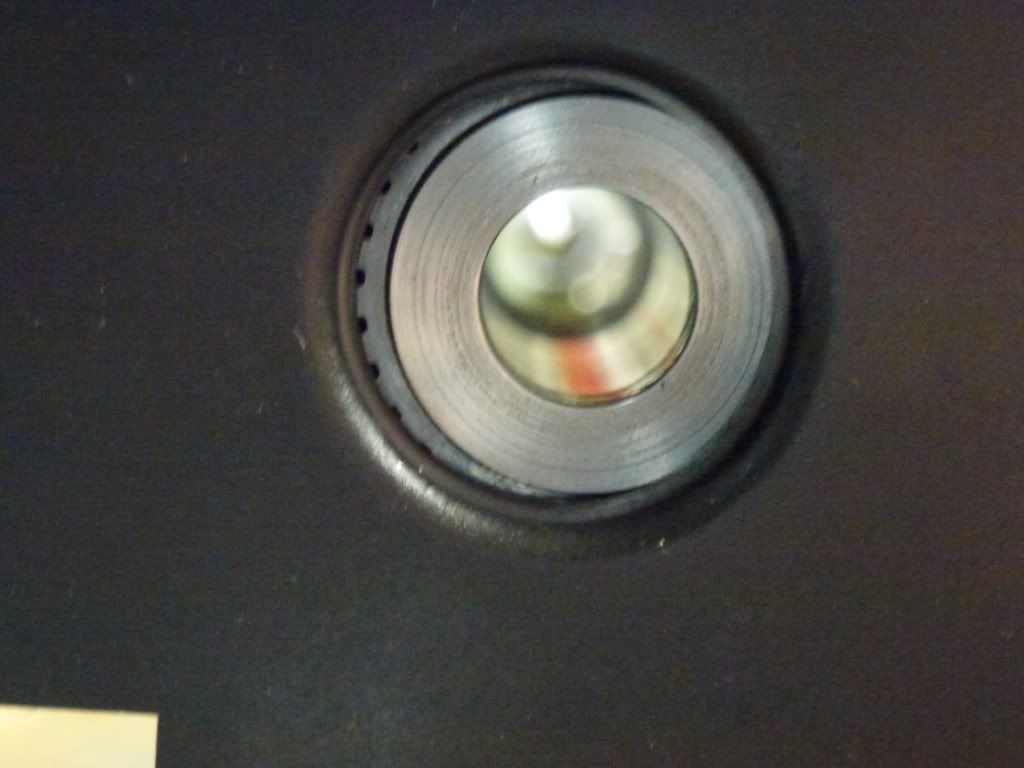
The ER32 Collet Chuck mounted.
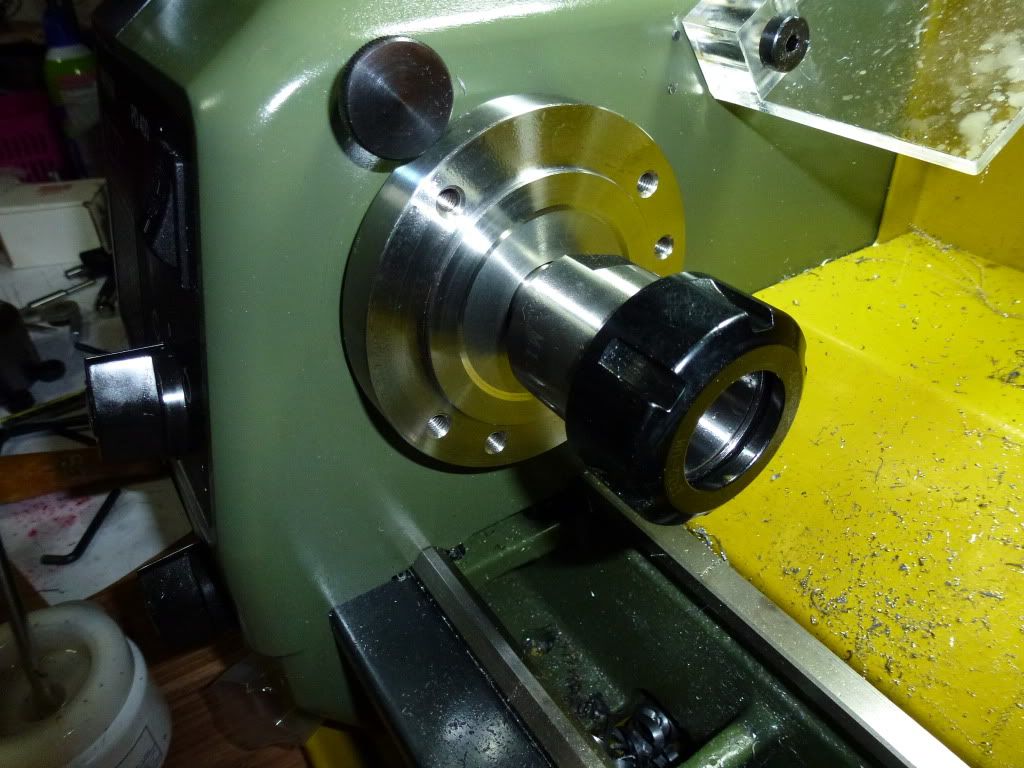
The drawbar which is basically an M12 socket head screw/bolt.
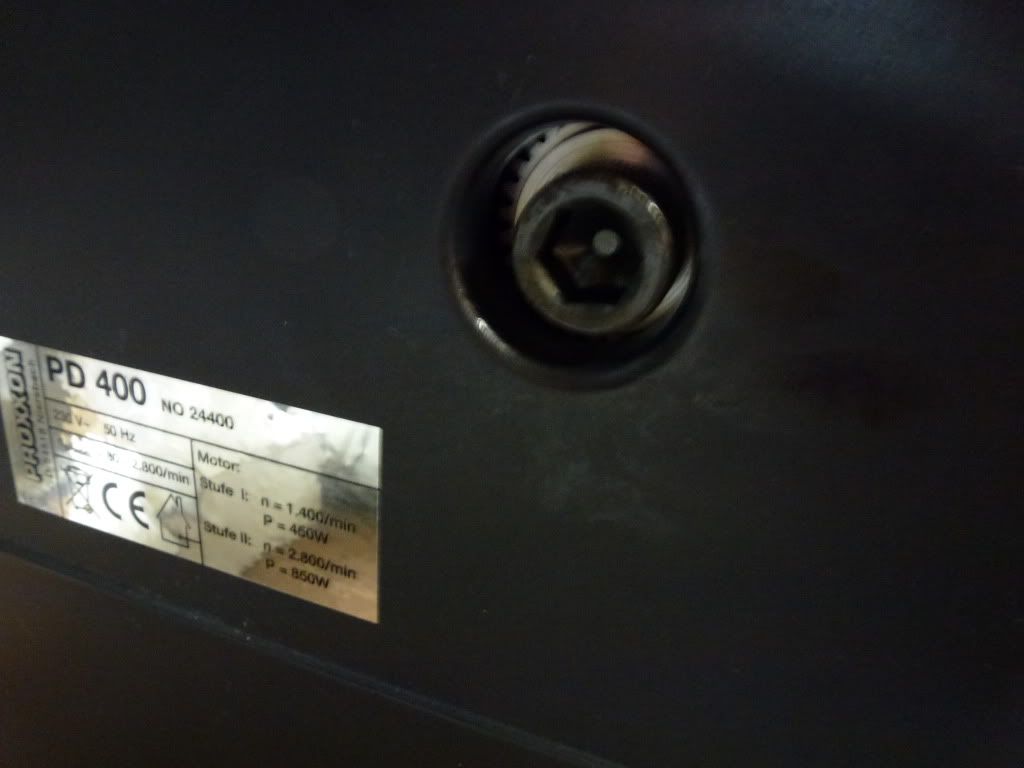
The silver steel chucked up and turned to accept 5/16 BSF.
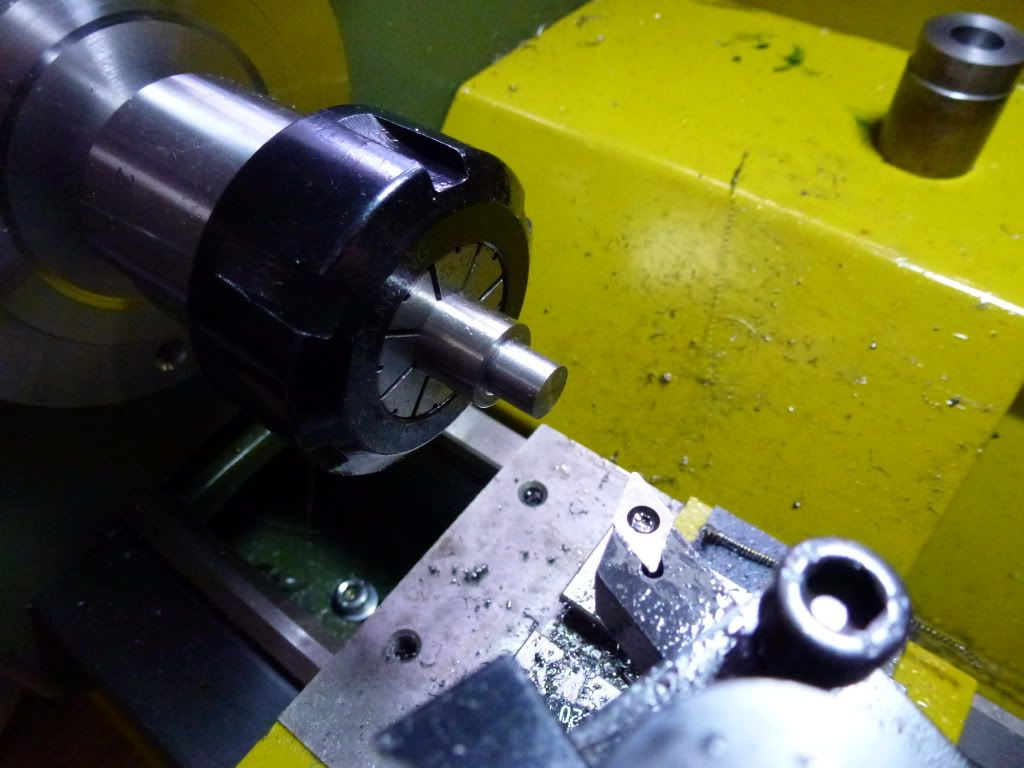
Adding a little chamfer.
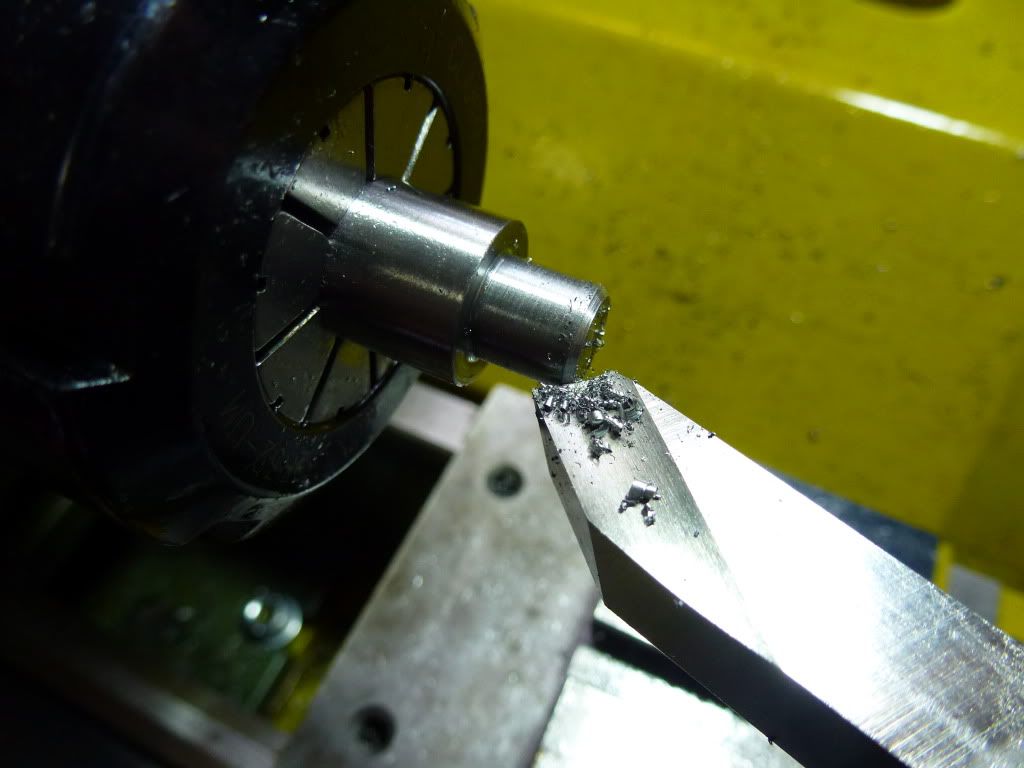
Using the die holder I made for my Sherline lathe with the tailstock live centre pushing against the 3/4-16" tapped hole meant for the 0MT to 3/4-16 adapter. Turning it is so tough with those little SHCS.
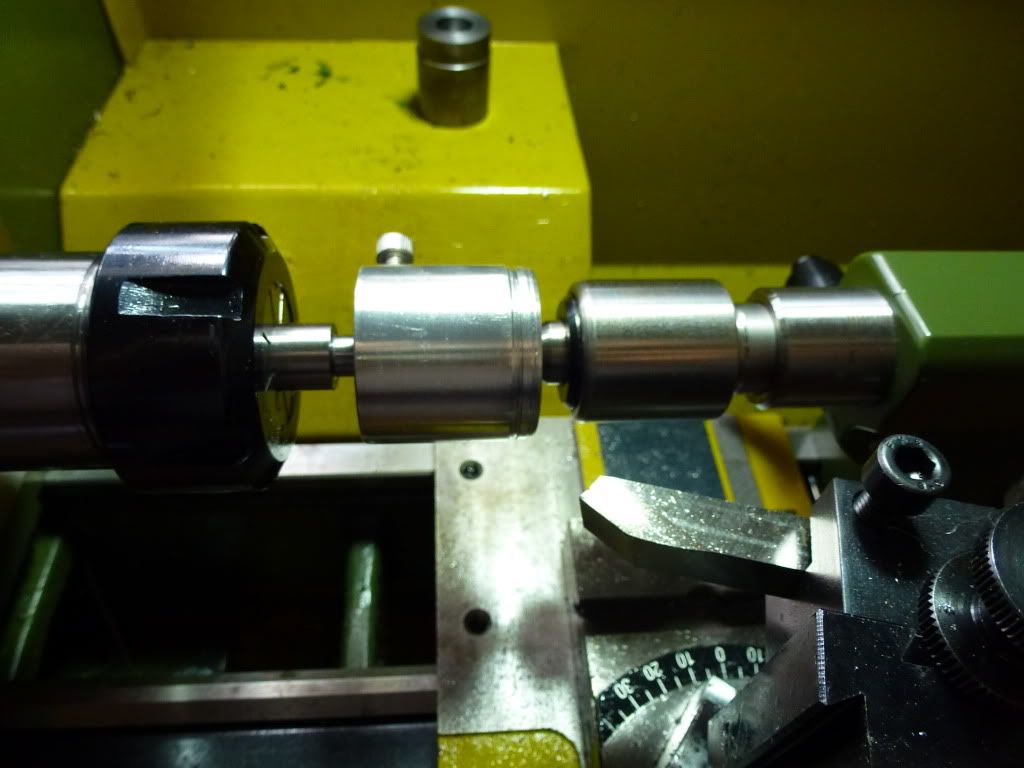
Swapping it with the die handle I bought. One handle was bearing against the bed way while I turned the collet chuck with its wrench.
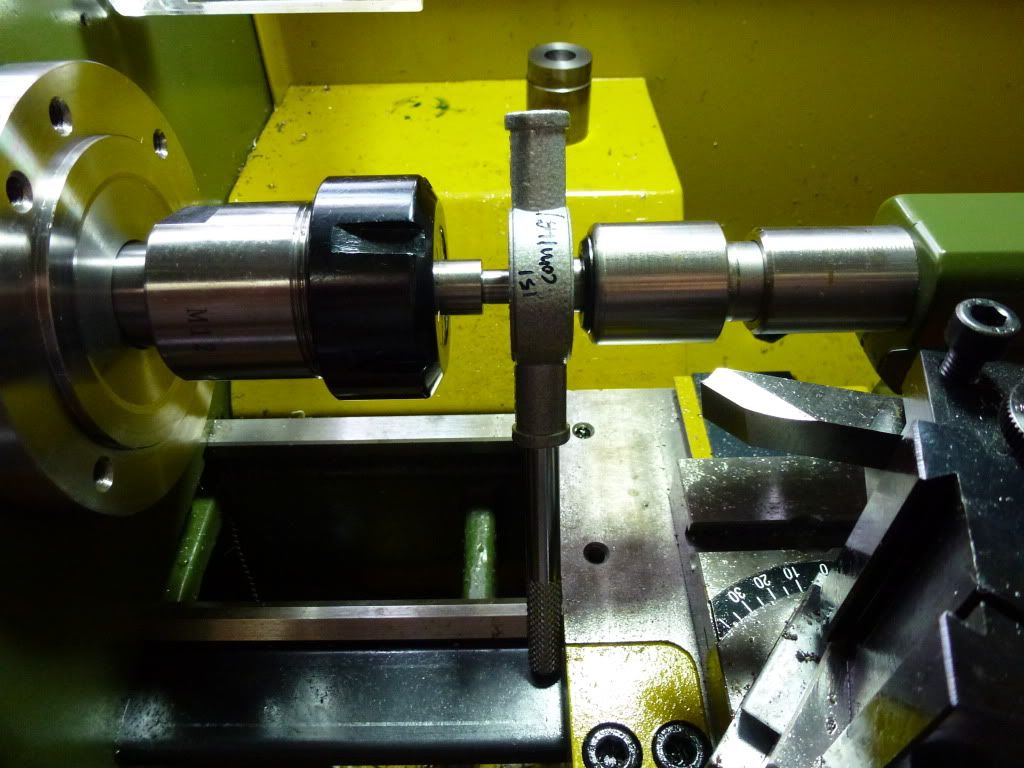
The tailstock removed so that I can finish threading without the carriage in the way.
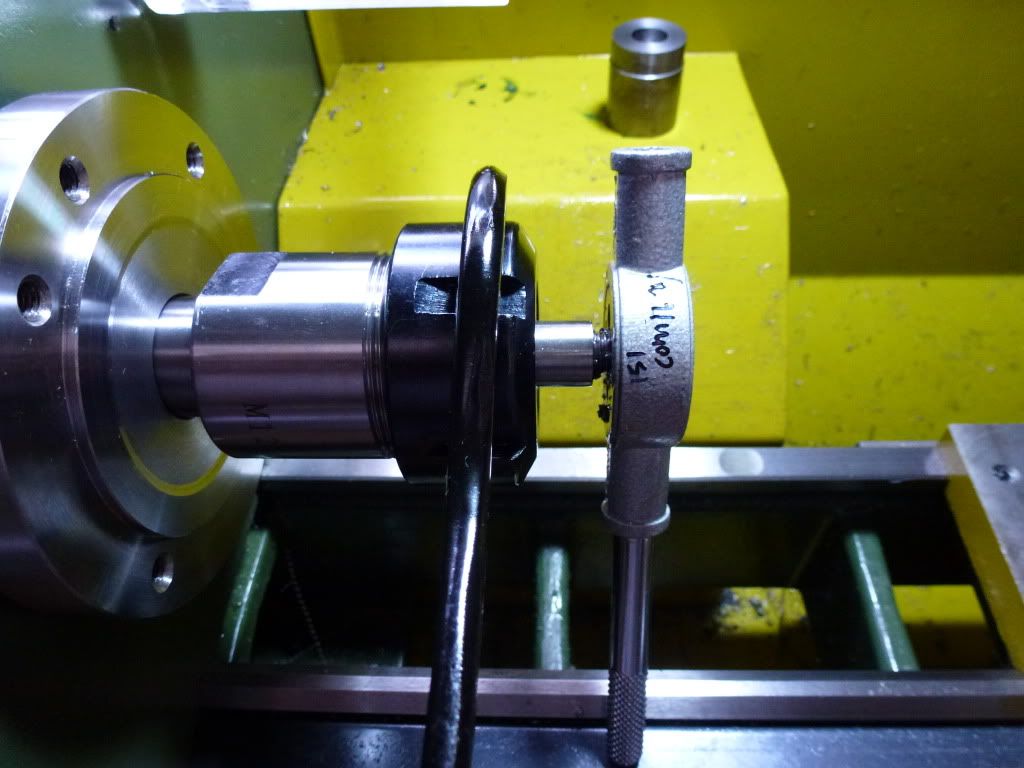
Testing the fit. The part test was supposed to be the Slide but since both the Base and Slide have the same tapped hole, it doesn't matter as long as it fits one of them.
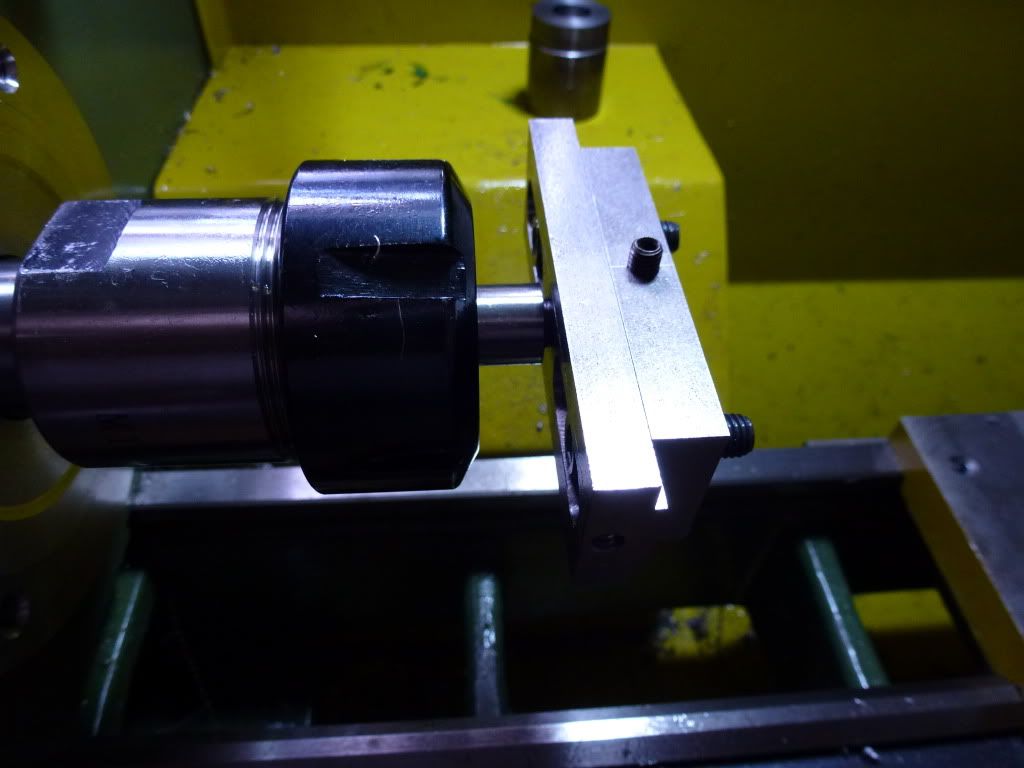
The part was cut off to length with some allowance for cleaning up.
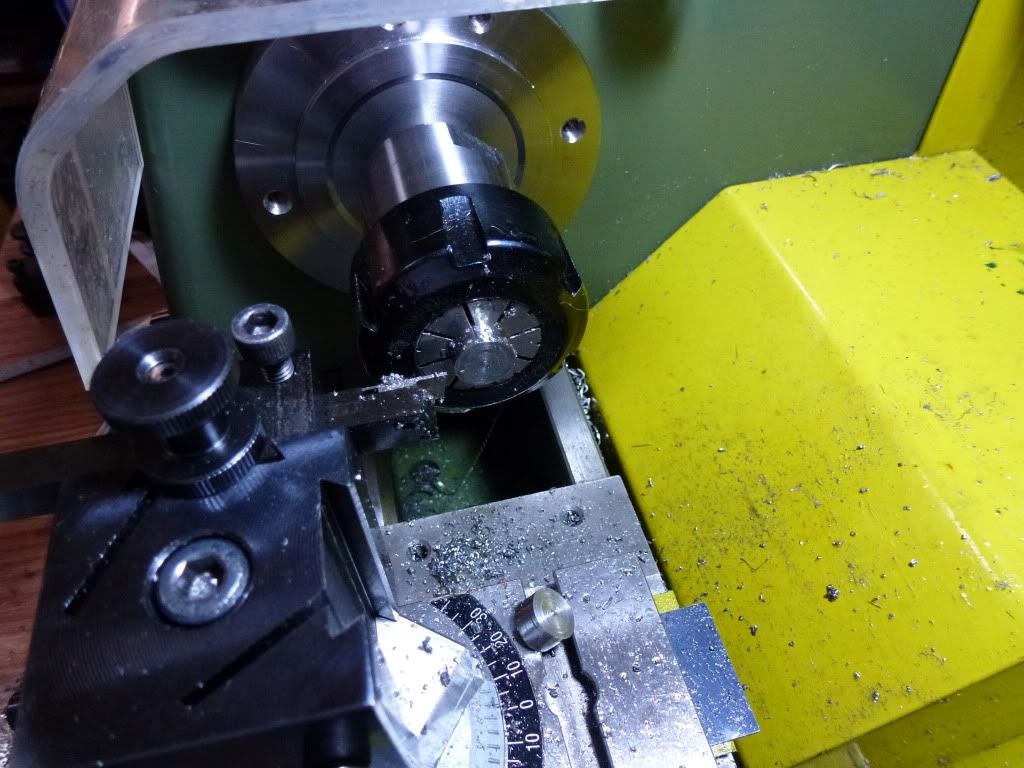
The partially completed 1/2 centre was removed from the chuck. See the gap between the 2 parts? I chased the threads with the die flipped over but realised that both sides have taper on them to help start threading...

Next was to make an arbor with a threaded hole to mount this for the turning of the 60-degree cone. I found a piece of steel that was actually a tap guide I made when I first started.

Finish was rather bad when I attempt to true up the part though it is not required but to remove the rust.

I was told by a reader of my blog that this was due to tearing and not cutting. His post: "...problem of the rough finish it appears to be tearing, not cutting. Check the tool for a good sharp well honed cutting edge and that the geometry is correct for the metal you are cutting. I can't see just how the tool is shaped, make sure you have enough back rake to make it shear off the metal not scrape and tear."
I didn't have the problem when facing it. I'll try again to see if I can solve that.