Aluminum needs chip clearance in the flutes. The most common failure of four-flute end mills in aluminum is chip packing in the flutes.
I don't necessarily advocate solid carbide, but it can be nice. The reason is that on most home shop machines you can never reach even 10% of the recommended range of cutting speeds. I do agree that 3-flute end mills can be very good, and there are many that are developed specifically for aluminum. Weldon (brand) "Ski-Kut" are an example of good parabolic flute HSS end mills, the first on the market with aluminum in mind.
I have some Cleveland (brand) HSS-PM (High Speed Steel-Powdered Metal) 3-flute end mills that were also made for milling aluminum. I believe that's PM T-15 steel they are made from. Wow, is all I can say! They PLOW through aluminum and I can't clog them if I tried. I have some carbide ones too, but I'd feel much worse if something happened to those. The carbide ones want to run at 10,000rpm and up, my Bridgeport tops out at about 2750. ;) Strange though, because the PM HSS end mills cost almost as much as good carbide, and are more money than cheap Chinese carbide.
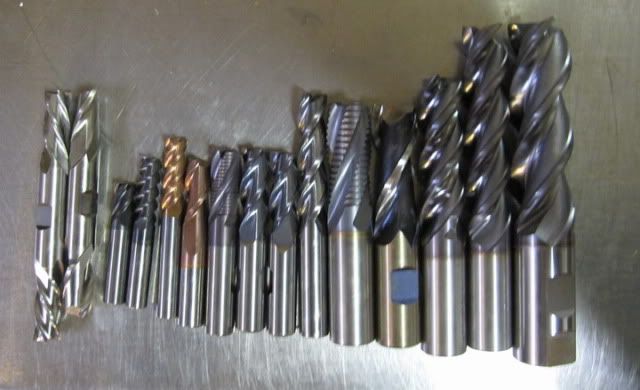
The TiCN-coated PM-HSS Cleveland's are the 3 on the right. The longest is a Ø3/4", then 2 different length Ø5/8", all 3-flute and in the middle of the array are two 1/2" 2-flute ones.
One thing I would be wary of doing is to buy the "weekly special" kits from Chinese sources. One of those top-quality made-in-USA HSS-PM end mills may cost more than a 7-piece set of TiN-coated carbide, but it will outlast and out-perform the whole set.
Three-flute end mills can indeed plunge, and do it quite well. Look at how the end gashing is done on this 3-flute solid carbide end mill I have is done. Notice that ONE flute is coming across the center and will do most of the cutting on a plunge. Works GREAT! Not cheap!
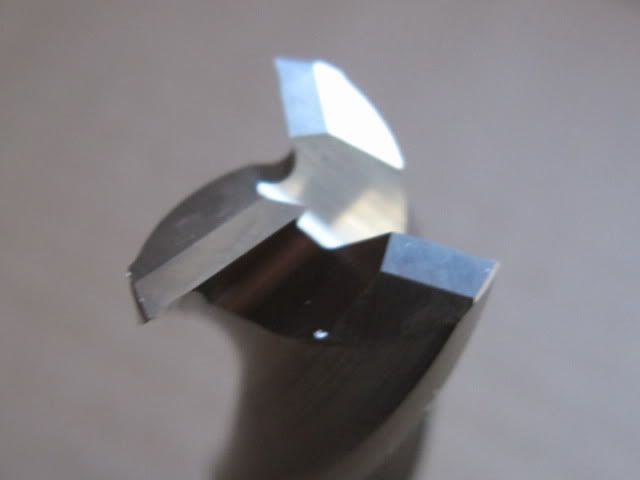
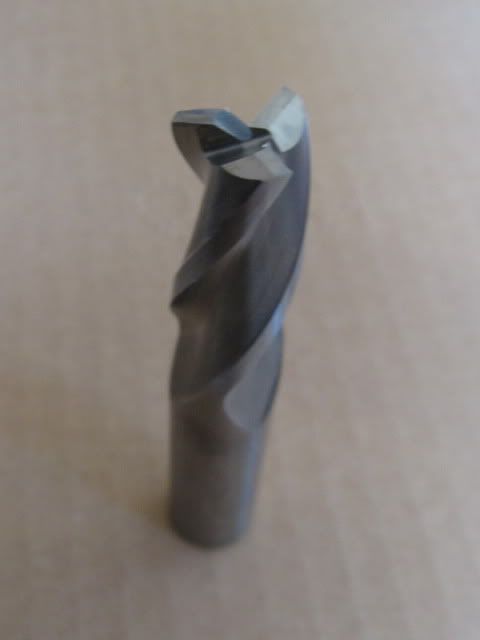