Evening,
Not much pysically produced today but my learning has improved tenfold.
It was time to countersink the 4 bolt holes on the base. Realising that I didnt have a datum nor two square adjacent edges I was in trouble right from the start and just couldnt get the piece lined back the same position I had it yesterday - needless to say the countersink effort I made using a knackered 3/4" slot drill was unsuccessful and produced a far from concentric result. I tried to recover with a boring bar which worked but by the time the holes were concentric they were too big and looked stupid.
I decided to get the hacksaw out, start again and not make the same mistakes.
After hacksawing another approximate sized block of steel I clamped and faced one edge in the vertical mill parallel to a 'good' side. Realising that each of the 4 holes was going to need piloting, intermediate and then final drill, intermediate and then full countersink I made sure the piece was square to the milling head on the side I faced earlier and at 90 degrees on both X and Y to the head. Neither hell nor high water was going to make me remove the piece from the clamps until all drill/mill operations were complete.
I did my stuff.
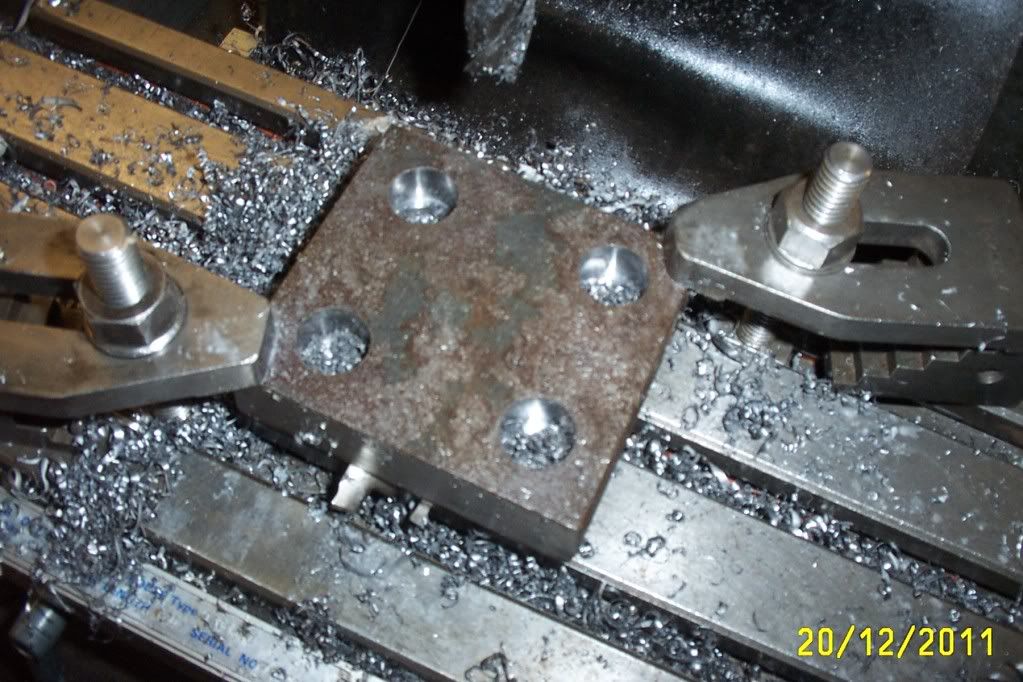

It needs finishing and squaring off but I have produced exactly what I was after and worked to a level of accuracy I am happy with.
The lessons learnt today?
1. Spend as much time as needed to setup the piece
2. Make a note of your datum, preferably a corner of the piece rather than the centre of a hole(!)
3. Work out what operations are needed and try to do them all while the piece is clamped in position
4. Make sure all your tools are in the same place - I used a knackered slot drill when I had a brand new, unused one in another cupboard
I know this is probably 'old hat' to some of the pro's out there but i'm sure it will be of use to other beginners.
Nick
@Ralph, thanks for your comments. I bought a double-ended tip from the local toolshop for £1. It 'looks like' one for use with steel. Either way I intended to use a double ended one because then I can just spin the toolpost round to a cut concave radius and vice versa.