A bit of an old thread, but going on..
I needed to make a new oil catch tank for the Nissan, but wasnt sure the plate bender was up to it with its broken hinge.
The cast hinge part has broken in half, probably when bending something much thicker than 1,5mm. The casting wasnt very good though, showing evidence of a lot of air pockets. The previous owner had tried to weld the broken part with limited success.
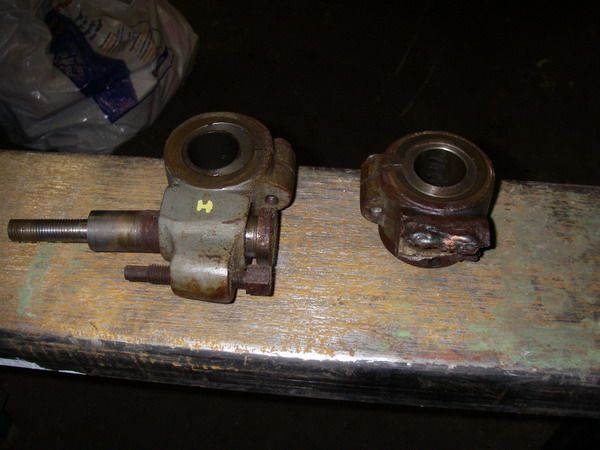
So i removed the hinged part
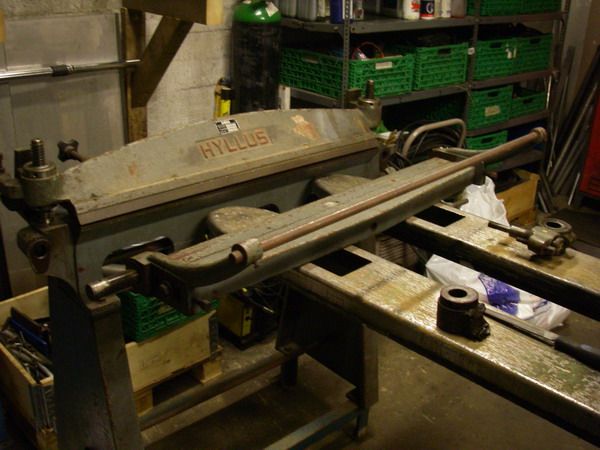
Aparently the shafts holding the hinge had been bent too

In order to get the bent shaft out of the good hinge part, i had to machine the head of it
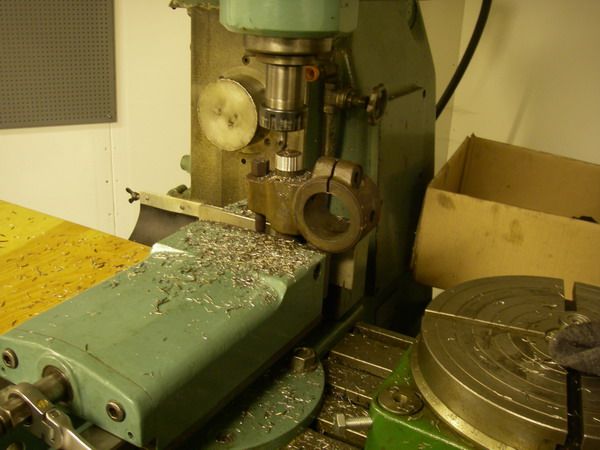
So a few new parts needed.
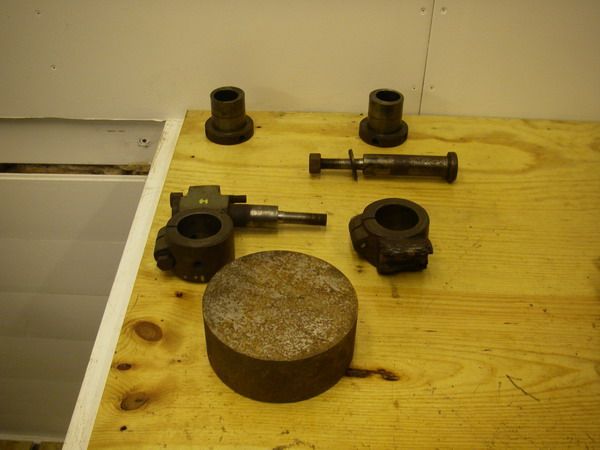
Rough cutting to size on the bandsaw, not sure this was the best sequence to do the machining in, but this is how I did it.
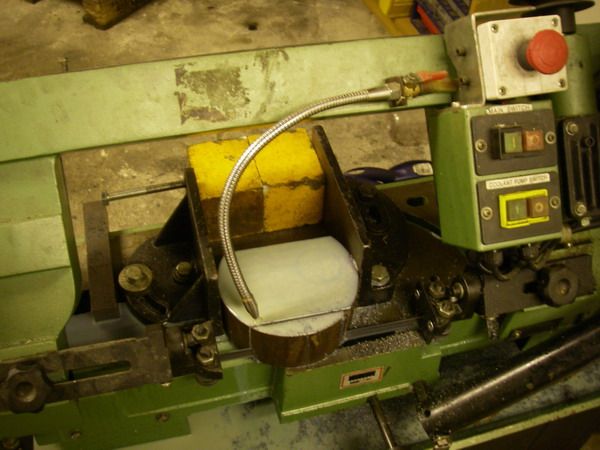
I turned both sides of the part to make it parallel, then put it in the mill and milled the sides of it
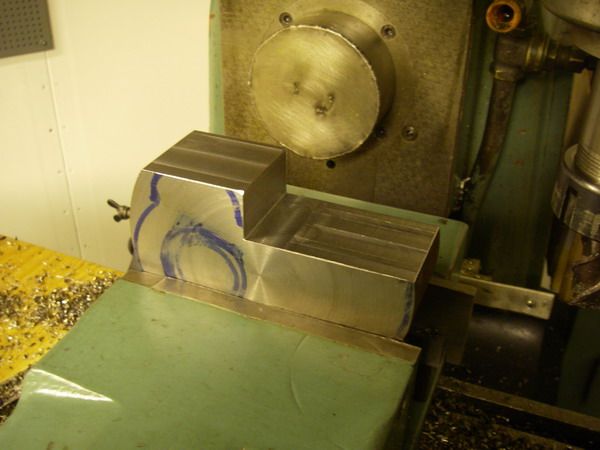
Scribed the hole to be bored

Centered in the mill and drilled to my biggest drill size Ø30mm
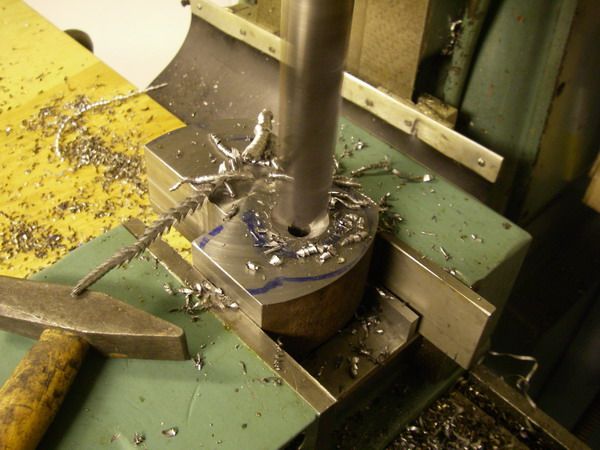
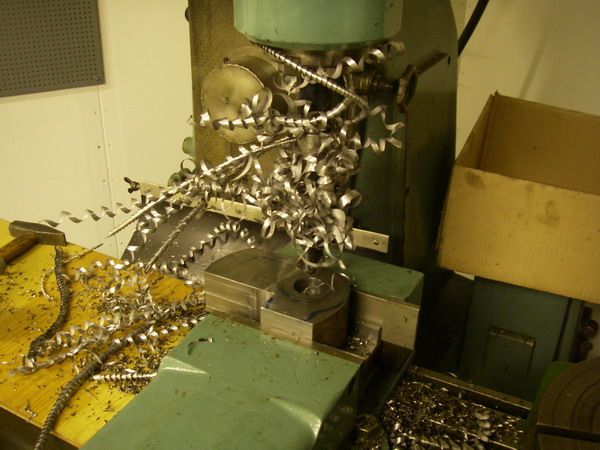
Not owning a boring head, I had to put the part in the lathe to bore it to size
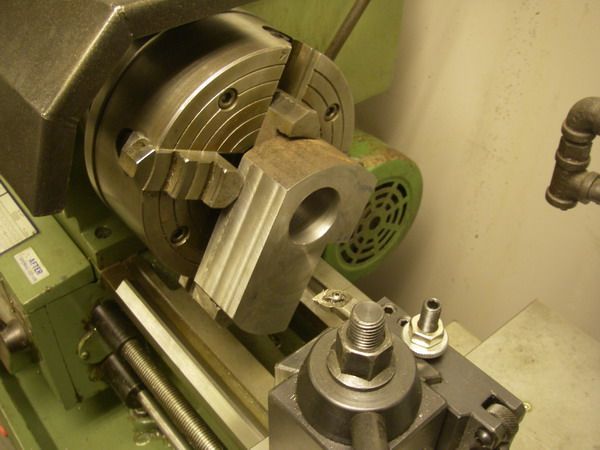
Finally got it to size

The eccentric part of the hinge fitted
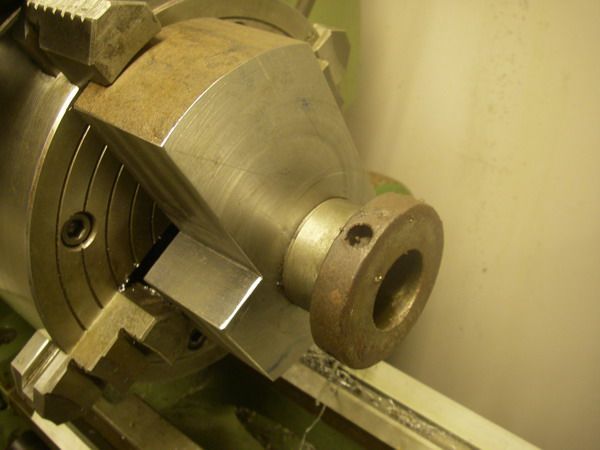
Then i started drilling the Ø28 mounting hole. The closest drill was Ø22.
Btw. i have started using a new approach to drilling big holes. I used to use sulfur based oil, but it would smoke a lot making the shop quite unpleasant. So now i have started using the coolant that i use on the band saw. Now the trick is to not bore through until you have drilled with your biggest drill, this way you can have the hole full of coolant and not have to have coolant flowing all over the machine!

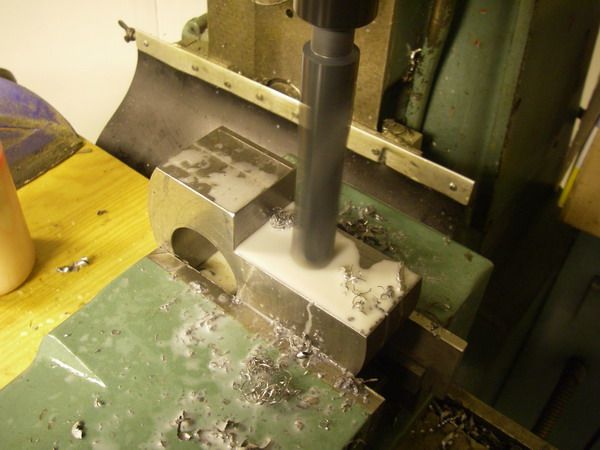
In the same setup i drilled Ø10,5 for tapping M12. Should have drilled Ø10,2 but I dont have that drill size.. yet
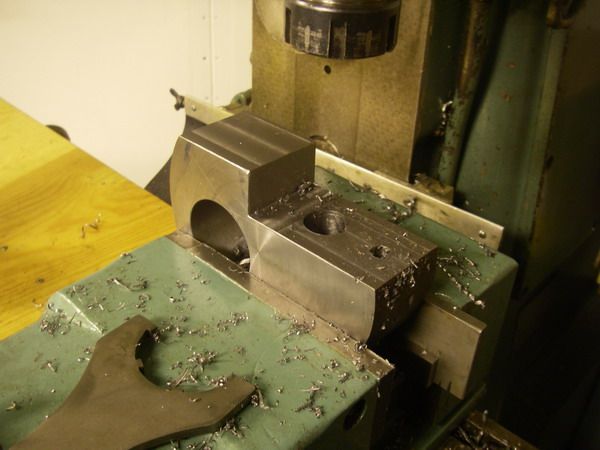
Part ready to be bored in the lathe, but with this odd shape i needed to mount it on the faceplate

Having never used the faceplate before, I washed of the dragon fat it was covered in and put it on the lathe to check it for runout. It had 0,07mm of axial runout
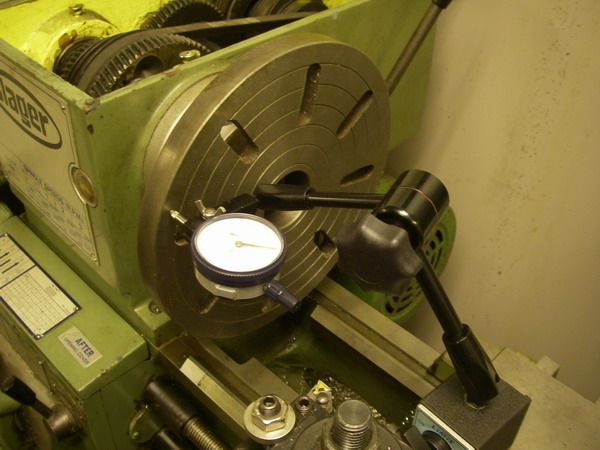
I figured I could do better, so i ground a HSS tool and started cutting the surface. After 3 passes i got the runout down to 0,02mm.
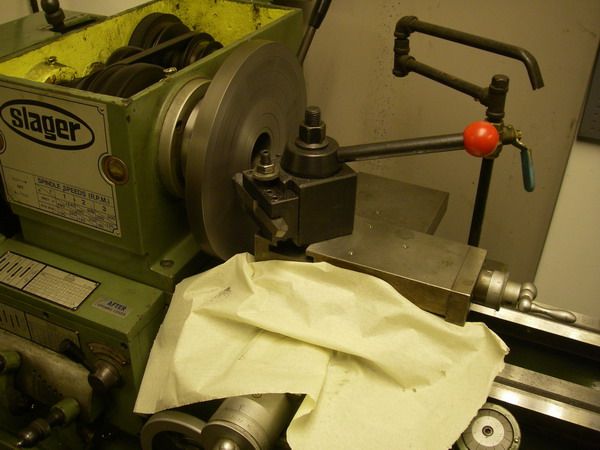
Made a setup to mount the part and dialed it in
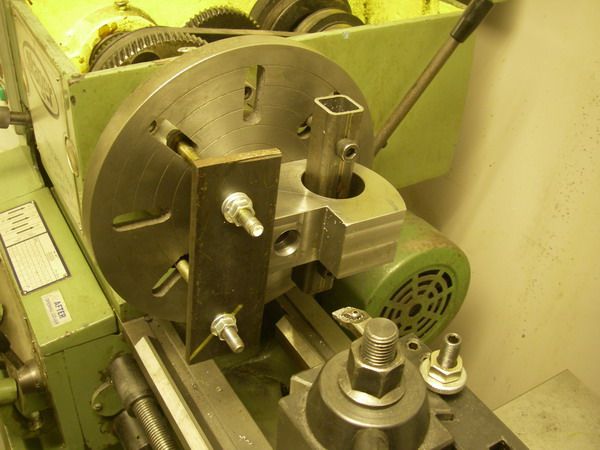
This is when things went south. I got out the longest boring bar i have and started to turn the ID
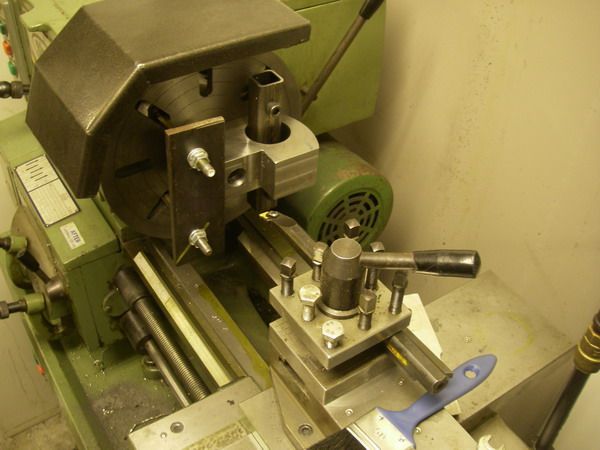
On the finishing cut, something went wrong and the bore became full of steps, going far over the desired Ø28mm
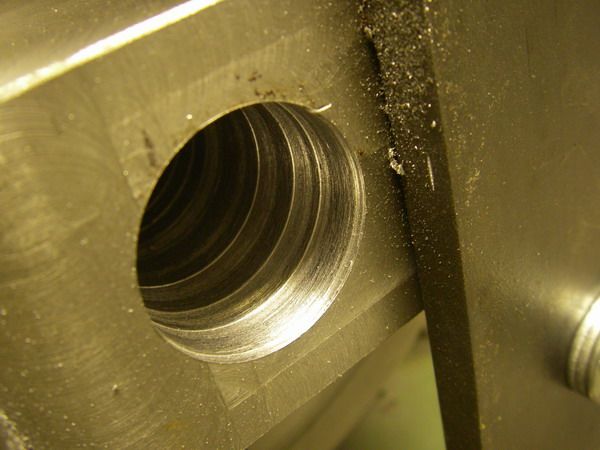
So i got out a HSS boring bar instead and bored the hole to Ø32,01

I removed the faceplate, put in the 3 jaw and turned a bushing
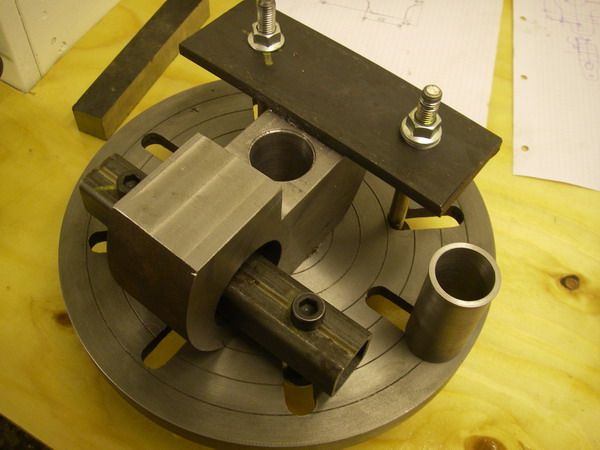
Made a small lip on the bushing and on the hinge part to locate the bushing.
I made the OD of the bushing to 32,05 (0,04mm press) and the id 27,50 to allow for a finishing cut once in position.

I used the parted-off part of the bushing as a press tool
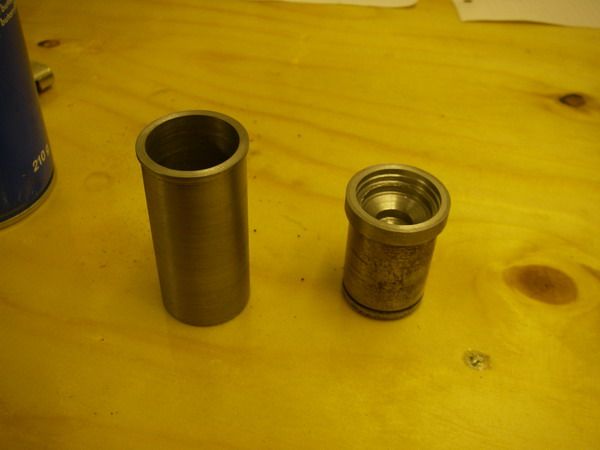
Then I pressed the bushing in, while still keeping the part on the faceplate. I made sure to distribute the load on the faceplate to avoid damaging it. Then i put the faceplate back on the lathe and turned the ID with the HSS boring bar to Ø28,02mm
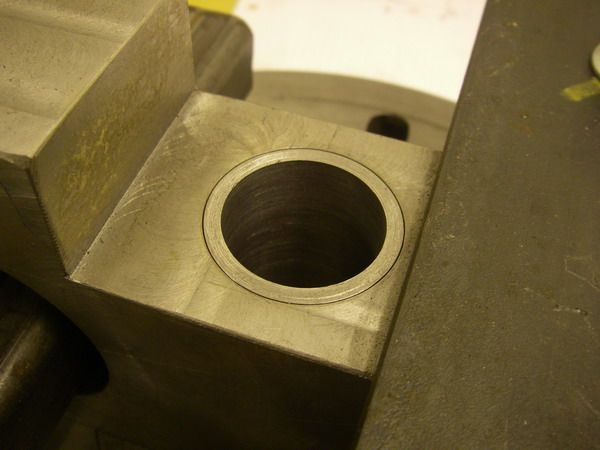
Having never used the rotary table before, I made some mounting clamps
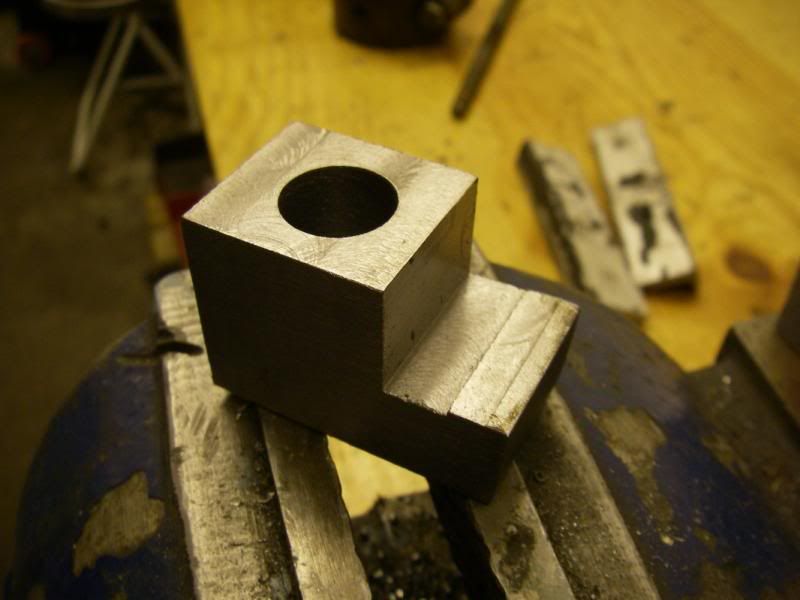
Clamped to the table
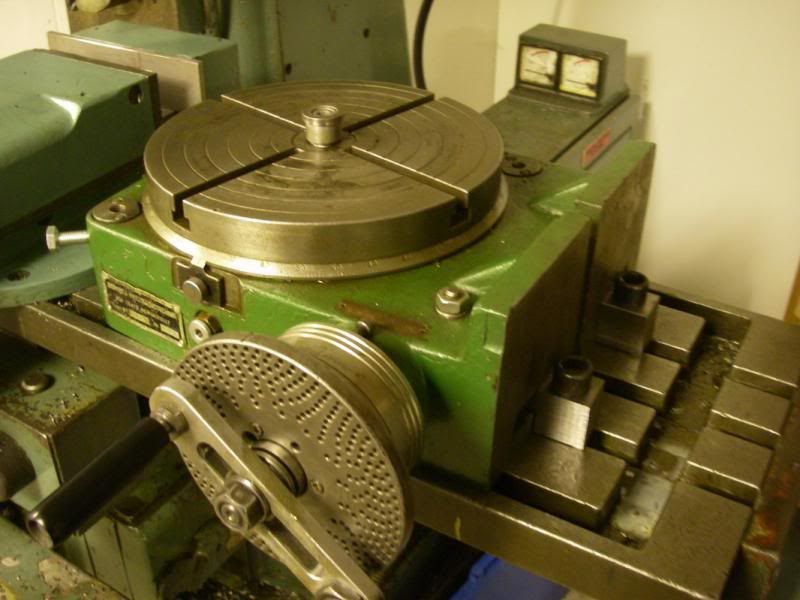
Finished milling
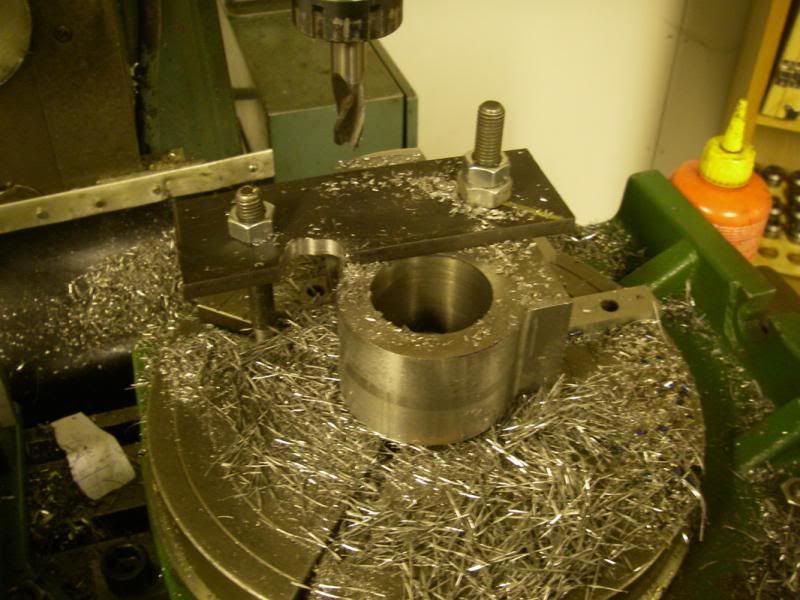
Machining recess on back side of part
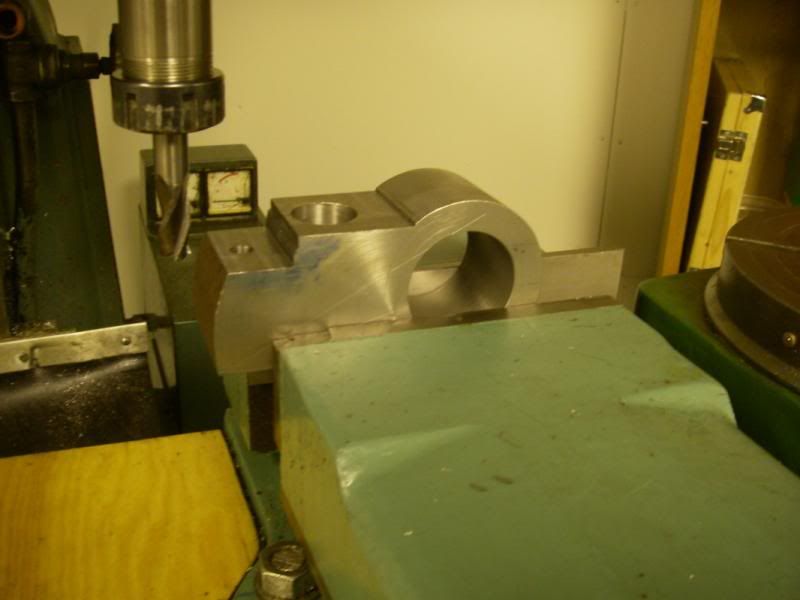
Finished milling
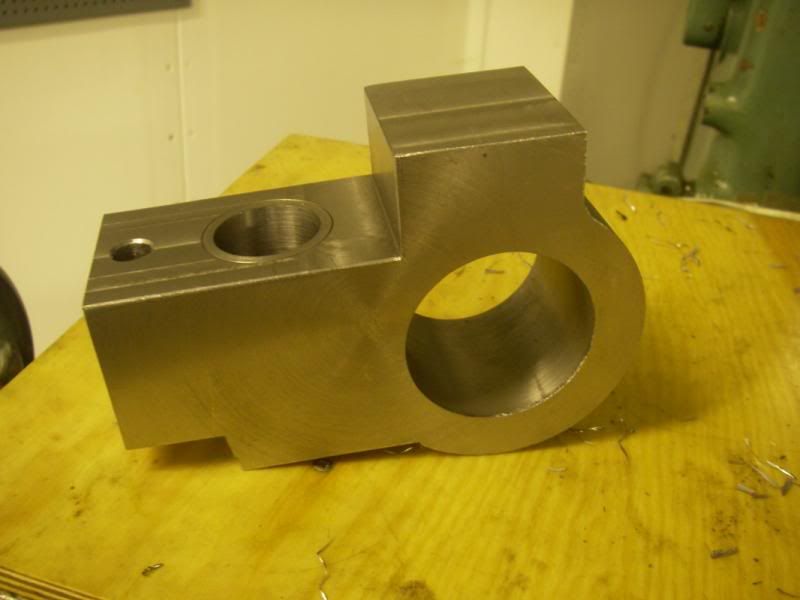
Drilling the Ø10,5 hole and counterboring to Ø12,5 to half depth

I was wondering how to make the split in the part. Cutting it on the saw would be simple, but it could become a bit too narrow and possibly not end up at a perfect 90 degree angle, so I wanted to try using the shaper. So i started making a holder for a parting blade in the shaper.
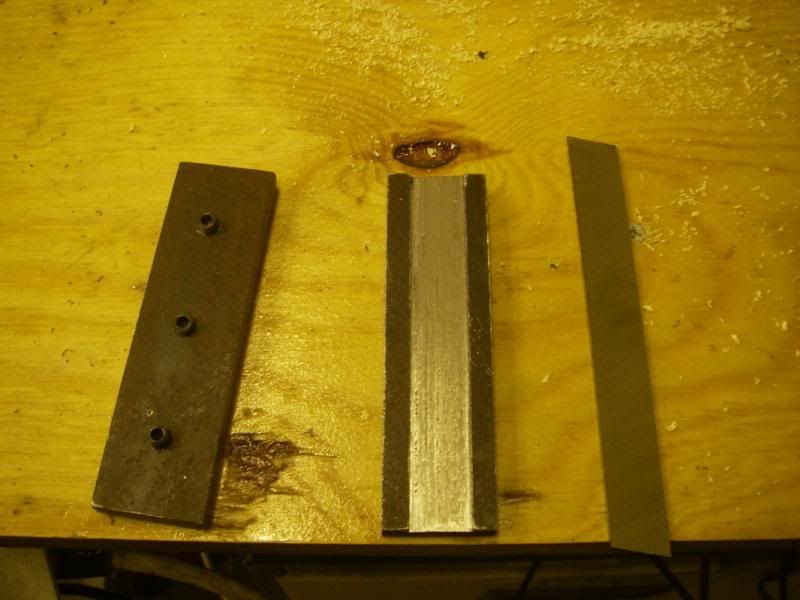
On the shaper i cut a groove in one of the parts to fit the parting blade
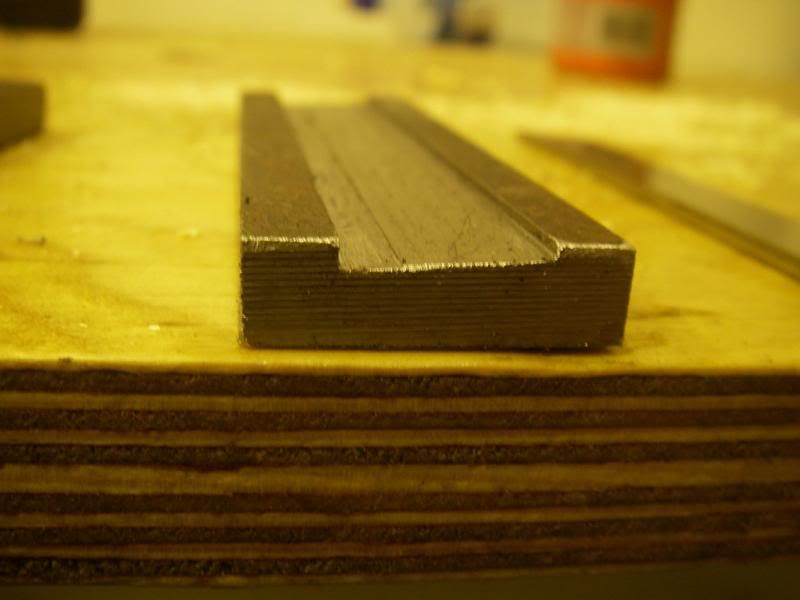
Mock up with 3x M6 setscrews
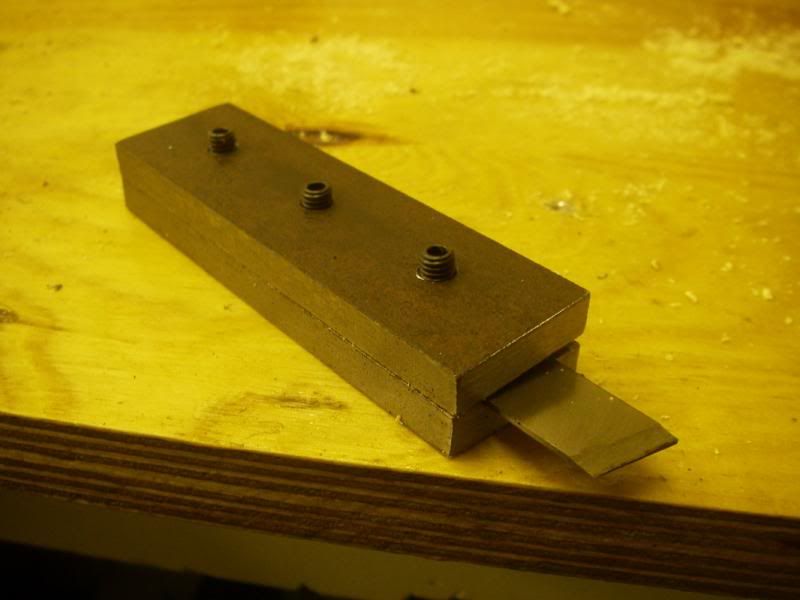
Then i ground some chamfers on the parts and welded them together. I used a 0,1mm shim to ensure that I would be able to get the blade out later

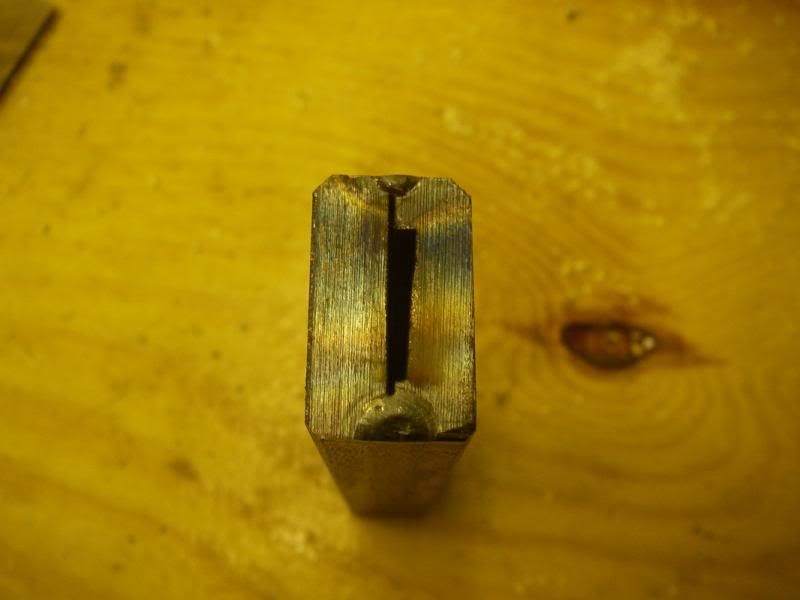
To make it look nice, i put it on the shaper and cut both sides of it and added some chamfers.
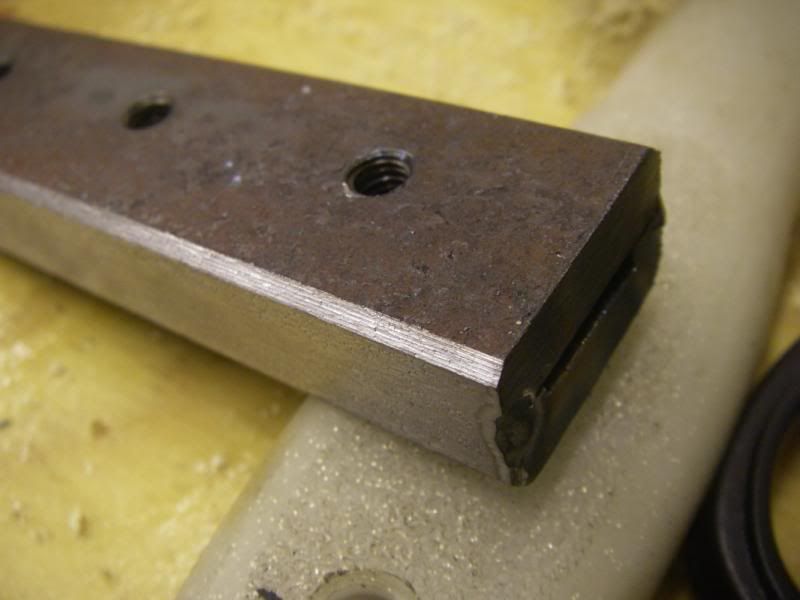
Ready for use
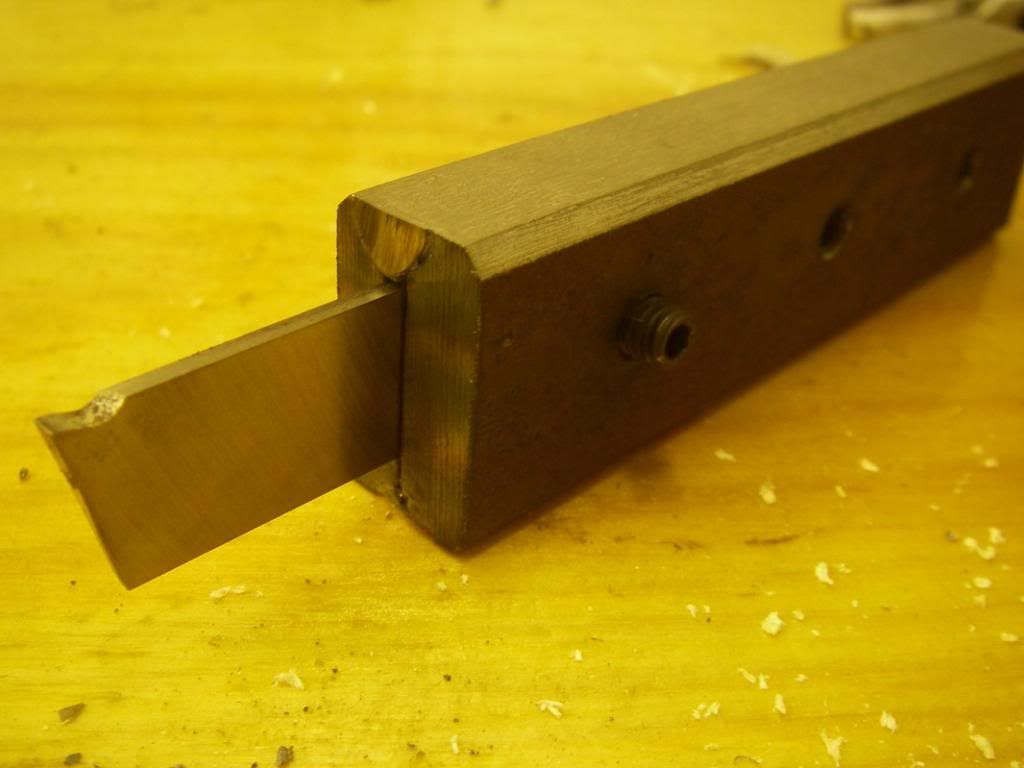
I made a test cut on a piece of scrap, but I struggled a lot with the tool digging in and creating a lot of chatter. I tried aligning the tool vertically, tried changing the tool geometry to make it dig in less, but in the end it dug in so deep that the shaper pushed the vice of the table and the blade broke. So parting on the saw it is..

Cutting the split. Note to self, dont saw all the way through with a BAND saw, it could become difficult getting the saw blade out afterwards!

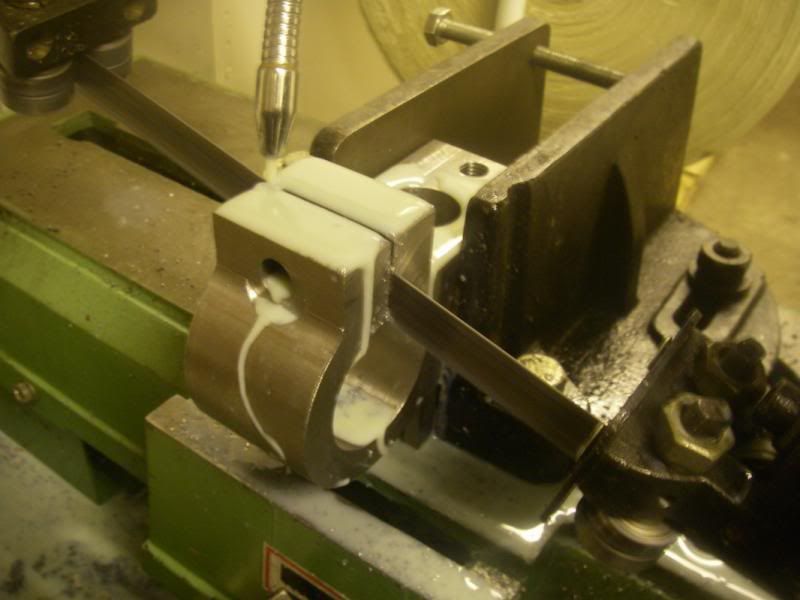
Finished part

Then I started turning the mounting shafts, got the OD to Ø27,96

Cutting the threads M16x2,0
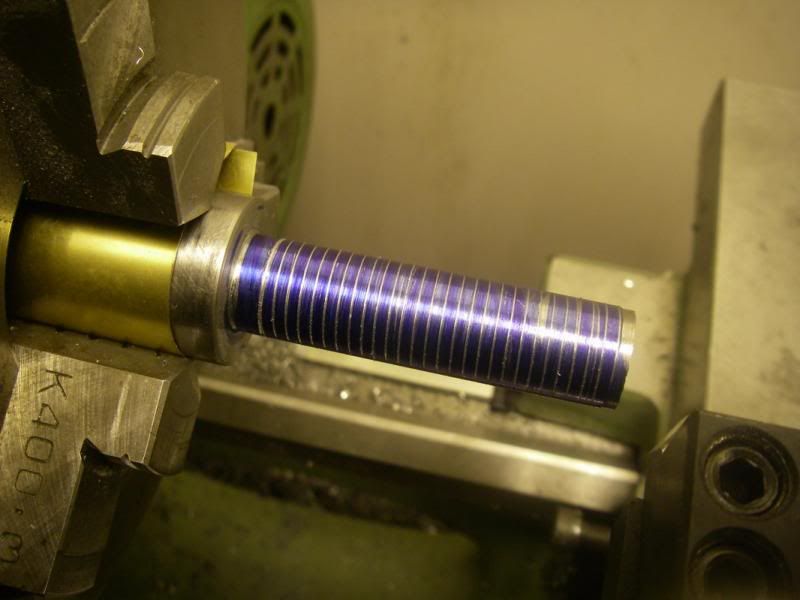
Finished parts
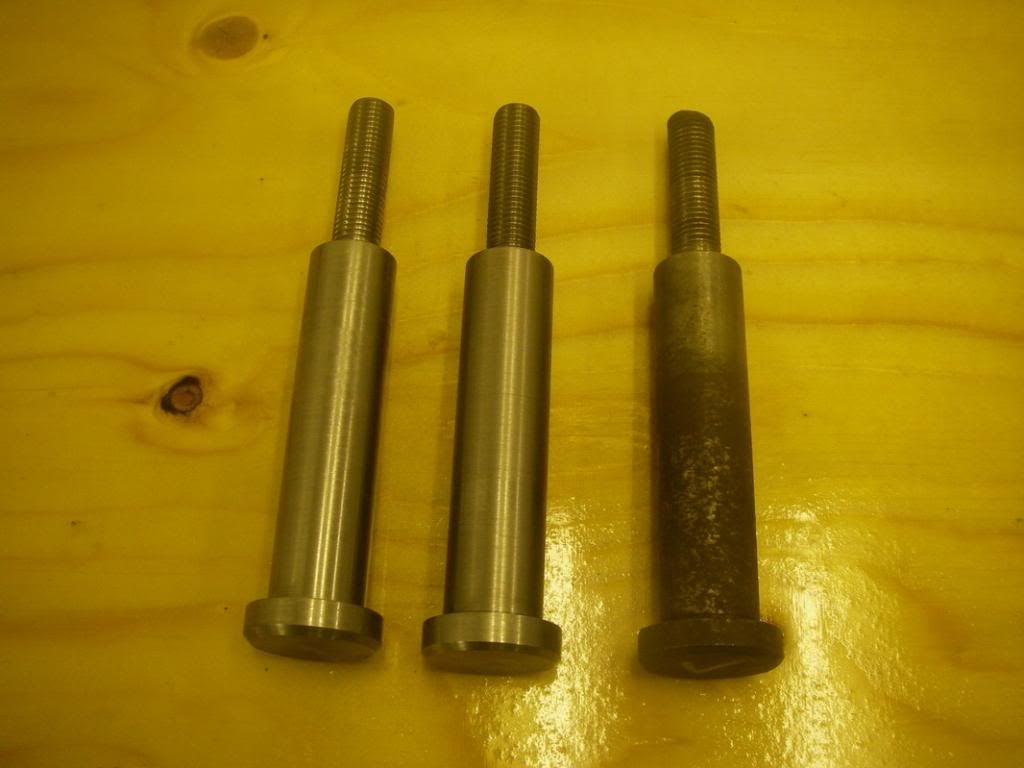
Started assembly

New shaft in old part
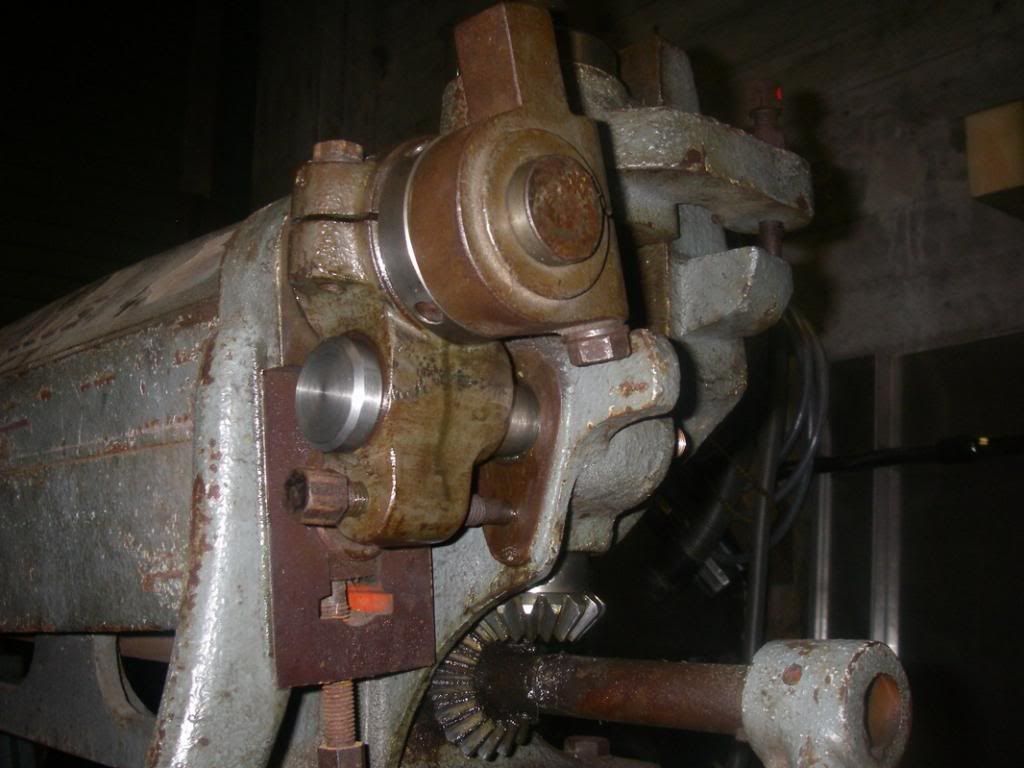
Left hand side
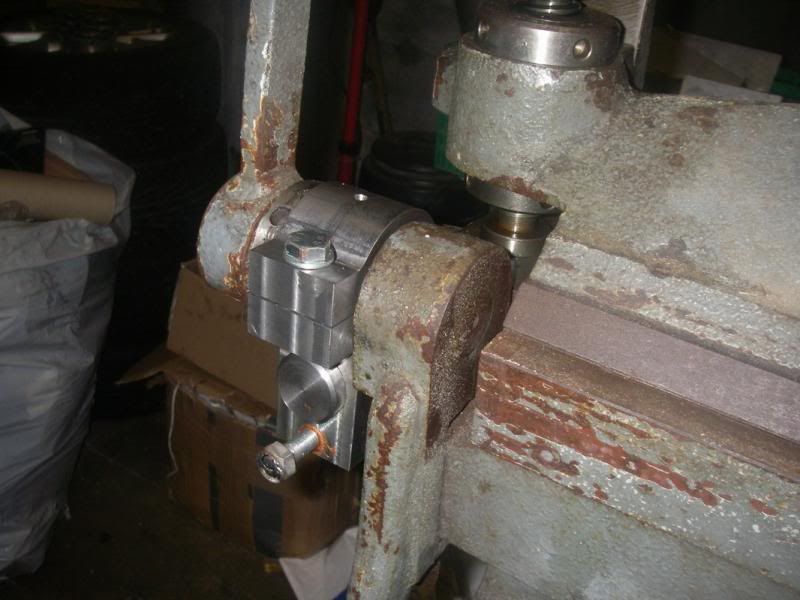

Finished and test piece bent.

Now im ready to start making the cath tank
