Well, i have done a few more things.
After a lot of procrastination, cunningly disguised as "design process" i decided to get a move on yesterday after having sourced some parts on friday.
A little thinking, drawing and figuring out later i produced a scheme for how i wanted it to look and work. I then set out to start on the pipe and hose side of things.
I figured a tank would come in handy. A rummage around in my friends barn produced several different variants, and after a little thinking i took off with this:
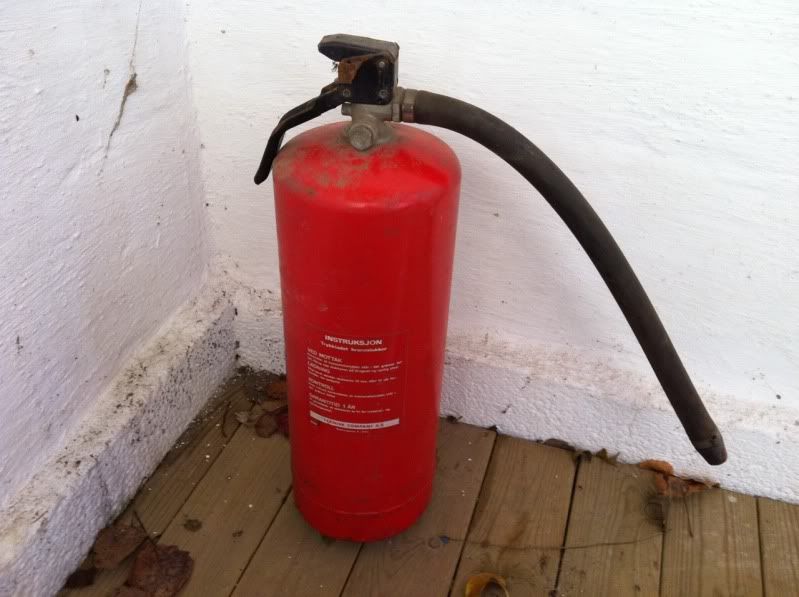
Taken apart and emptied it looked like this:
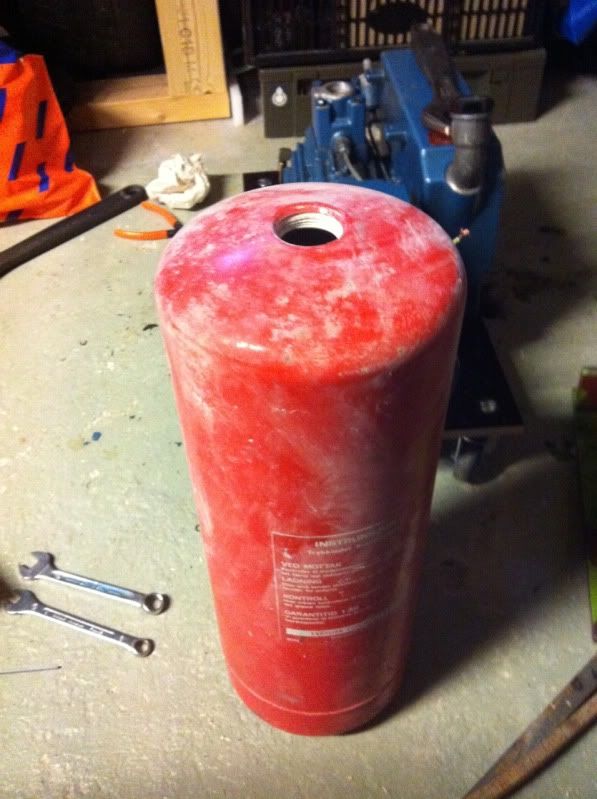
Now everything that passes my bench which i haven't seen or otherwise learned how works before will be picked apart and inspected until i fully understand how it works, why it works and how it looks inside. I am also not very good at throwing stuff away, but squirrel it away somewhere in my ever increasing pile of "that'll come in handy some day"
This is the mechanism from the fire extinguisher soon to be completely picked apart:
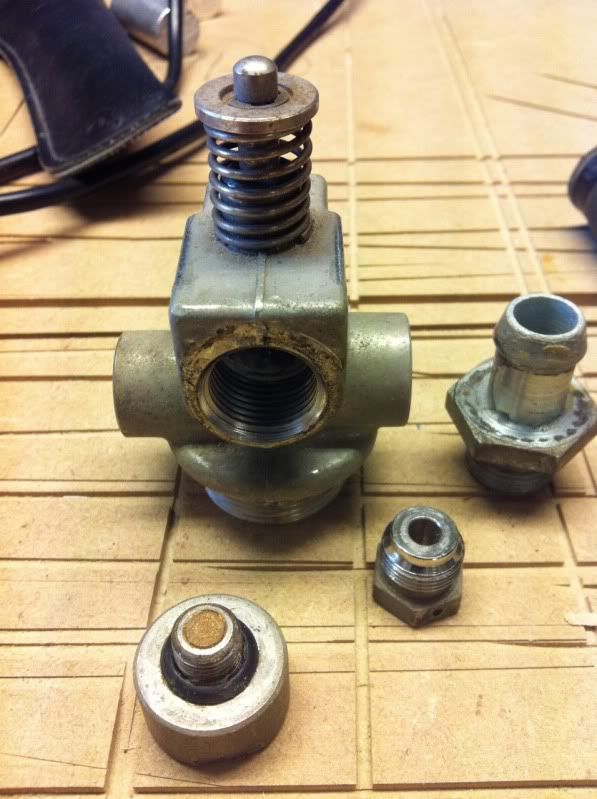
Now i had a small problem. The threads on the fire extinguisher was not very standard. Which meant i would need to make a new fitting for the tank :wonder: , then drill a hole, tap that and make another fitting for that :headsl: and then connect the various inlets and outlets.
Not a job i looked forward to, i admit, but then lightning struck and i had one of my brighter moments. The fitting from the extinguisher already had three threaded holes, one with a hose connection already and it would be quite simple to drill them and just make two new fittings for the last two holes.
Off we go! This is the top of fitting where the push valve used to be. I drilled and tapped for a regular thread, and this will, as soon as i manage to source a vacuum manometer be used for that. In the meantime i'll just plug it:
Then i drilled up the two holes in the mechanism which where already threaded but only had very small holes (manometer and safety valve):
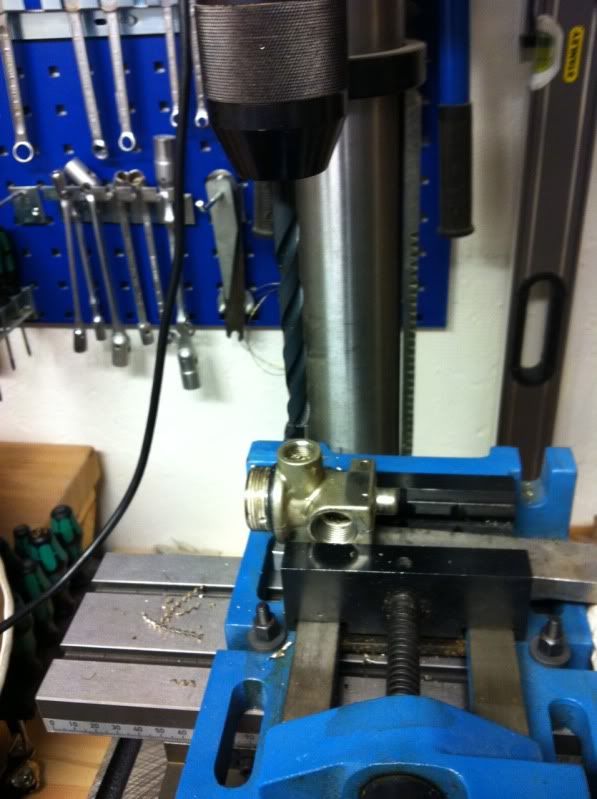
And made two fittings on the lathe (Not my prettiest, but they'll work, i guess):
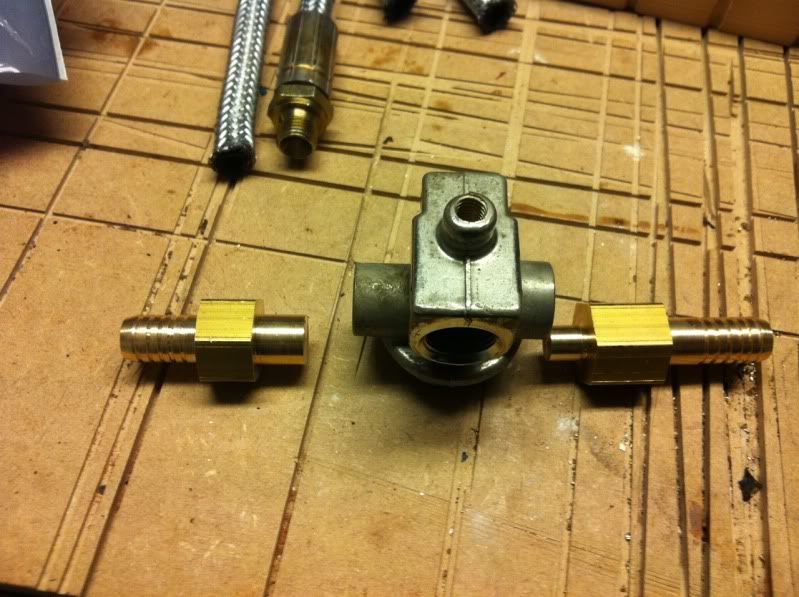
As luck would have it, i of course didn't have the right size threading dies (M10x1 would maybe not be a completely impossible one to find, but M14X1??? The only place i've seen that thread before is on old Citroen cars... In which they were left handed as well) so i will order them tomorrow and then get them threaded and then drilled through. These will accept hoses for the two separate outlets. A tame engineer i know said that it was no problem to do it like that, what do you all think?
Lastly, i had to rebuild the outlet part of the pump after a small mishap with the coarse filter in there.
The filter consisted of very fine stainless steel mesh, something i couldn't produce after an hour of going through my "that'll come in handy someday"- piles anyway, i was a bit lost as to how to produce the holder for the mesh (Small steel ring to the back right of the picture).
So, i've tried something different, and i will be sure to keep an close eye on this, as i am not at all sure it will work, but this is how it looks now:
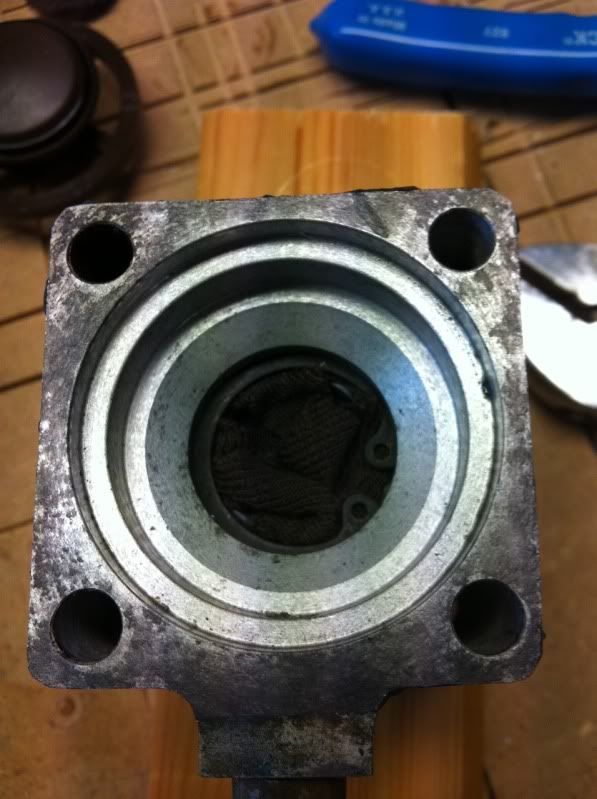
It's hard to see, but i made a coarse filter out ofa piece of fabric from an old thin woolen sweater, then forced that with an o-ring and the lock ring which held the old filter.
Not sure it will work, but if it does, it will probably be very good! My main concern is that it will be sucked into the pump, but as air passes freely through, i hope that will not happen. Anyone have any thoughts on that?
Here's the rest of the innards of the part in question:
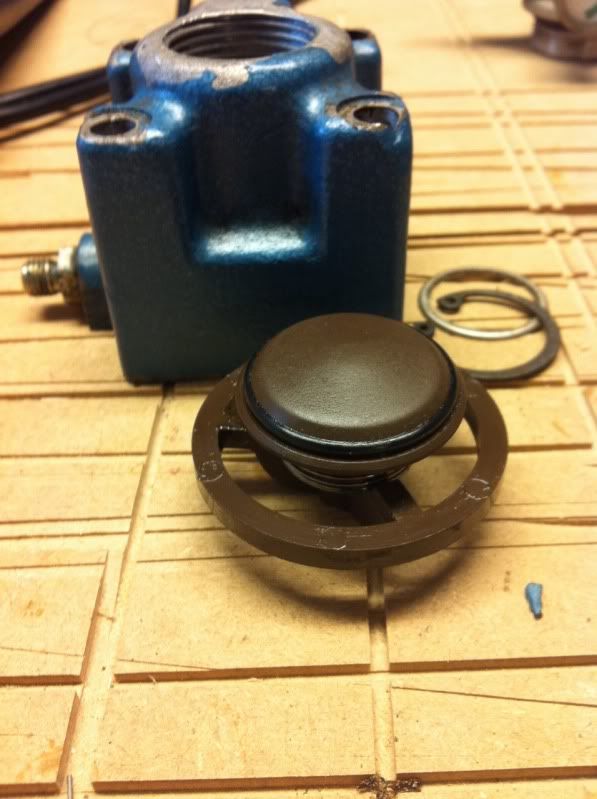
Tomorrow, i will try and continue on the cart, after having geared my shop back from metal working to woodworking, something which is no small job with my very, VERY limited space!