Well, a bit of tooling for a change. I actually wanted to start on an ER25 collet chuck for my mill. The Cheap 'n Cheerful import I have works well, but after having used the bearing-based closer nut on the lathe's ER chuck, the closer nut on the mill's is a pain to tighten and release. Unfortunately that chuck uses non-standard dimensions, so it's not as easy as just adding a bearing-based closer nut. I've already added some extra collets of the regularly-used sizes to my set, and this morning I set off to start on the new chuck. Bummer... I thought I had some suitable steel to make it from, but I thought wrong. So it'll have to wait till I can buy some steel.
Instead, I started on another collet chuck - an ER11. I've found that the ER25 on my lathe works very well, but at the smaller sizes it's inclined to shrink the collets if they are regularly used at under-sizes. So a couple of months ago I bought a set of ER11 collets which have been sitting idle on the shelf since then.
First I clocked up a bit of 16mm silver steel in the 4-jaw. I took my time about it to get it really close - less than 0.0025mm run-out (less than 1/4 deviation between two markings on my best dial indicator). Two years ago this would have taken me 30 minutes; now it takes less than 10... I left quite a bit of stock sticking out of the chuck; that was so that I could check both close to the chuck and further away for run-out:
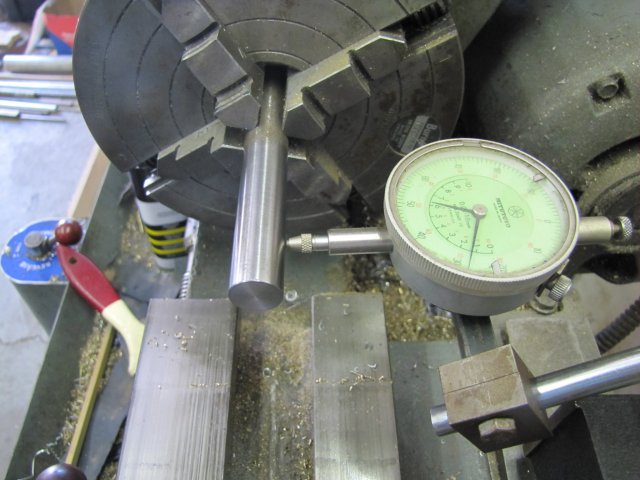
Then I center drilled the end, turned a 13mm length down to 14mm diameter, and put a threading run-out groove in it:
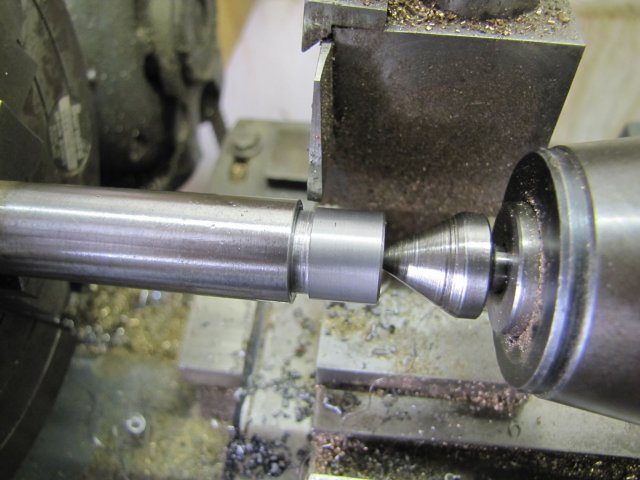
I set up a 60 degree threading tool:
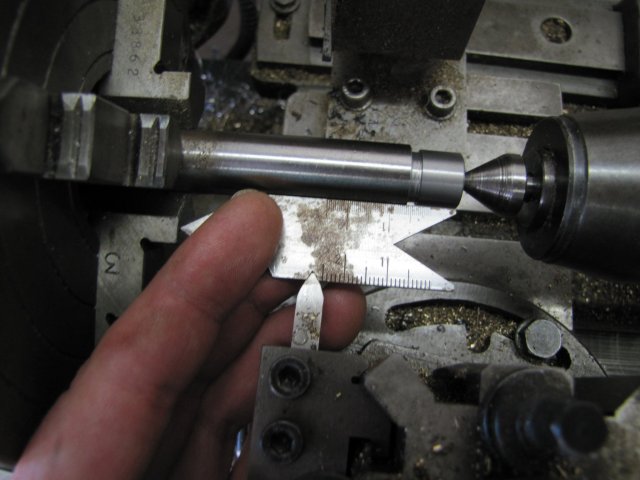
And started to set up the change gears for a 0.75mm pitch using a bit of paper to set gear clearance:
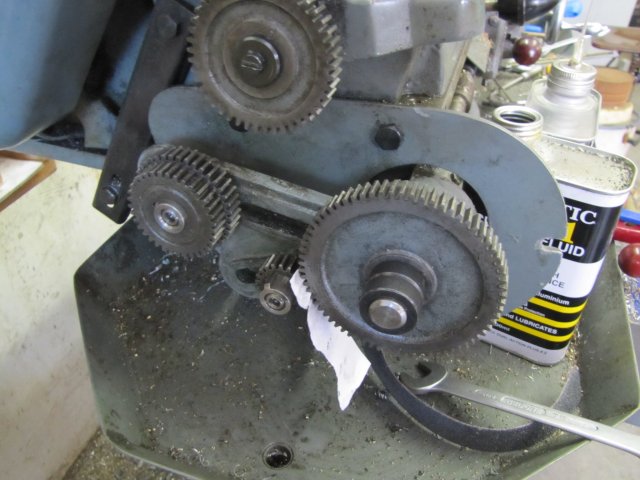
A very light cut across, and a thread gauge to measure that I had the correct pitch:
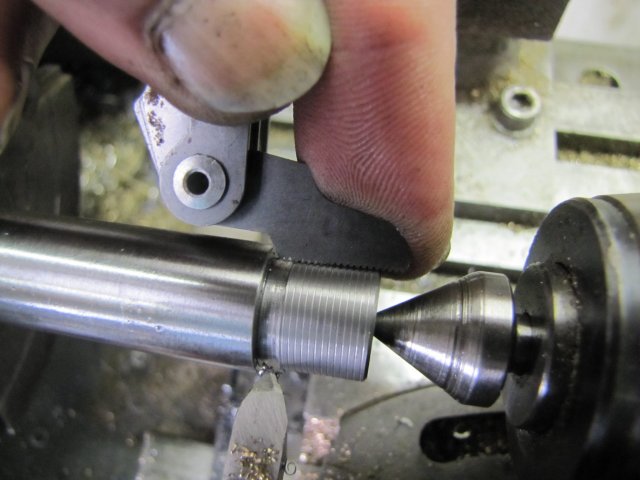
I took threading easy; just small increments at a time; 6 passes in total with the final pass at the same infeed as the previous one, and ended up with a nice smooth thread that's a spot-on fit for the ER11 closer nut:
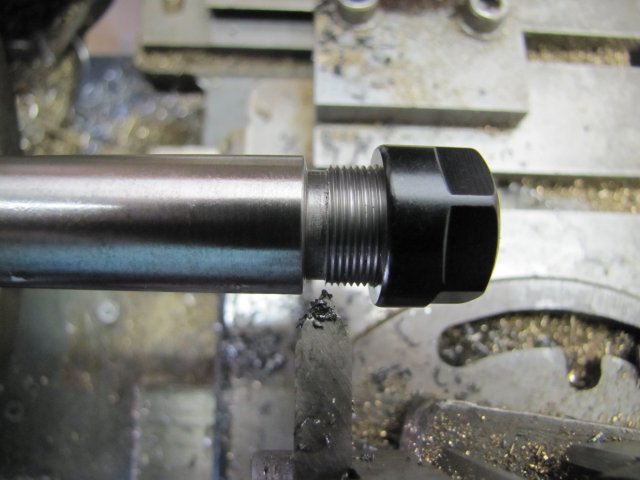
Then I deep-drilled the work through with a good quality sharp 6.5mm drill - I didn't want it to wander too much.:
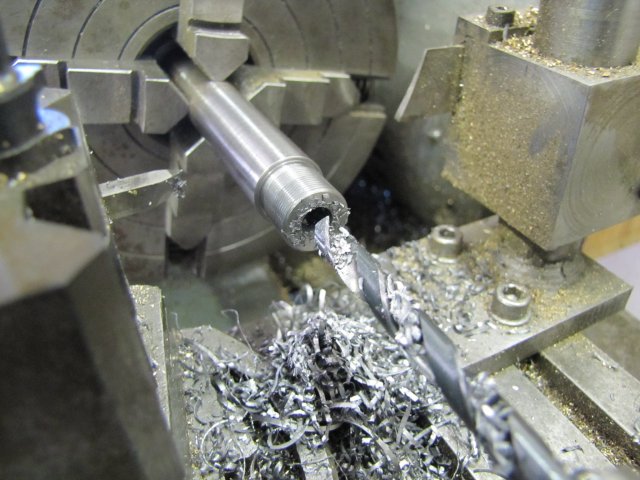
That was followed by a 7.5mm drill, which is the root depth for ER11 collet chucks. The Myford's top slide swivel graduations are pretty accurate, so I just set it to 8 degrees; that's the standard taper on all ER collets:
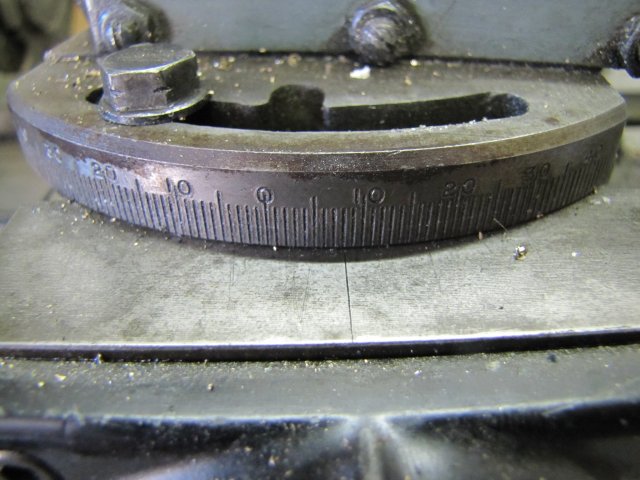
Of course I didn't have a small enough boring bar, so I ground one up from some 4mm square HSS blank:
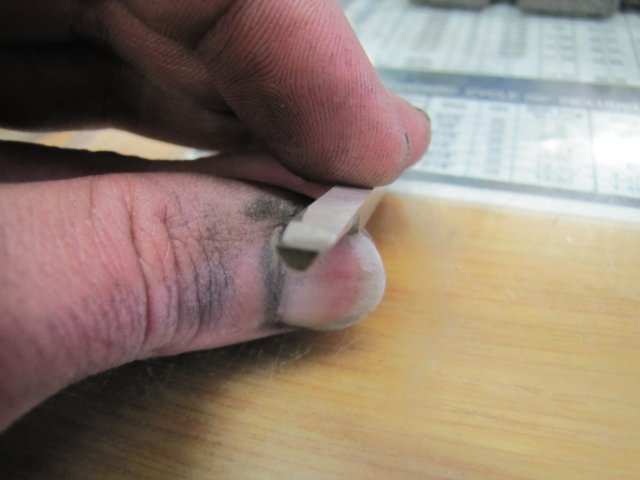
A bit of round 6mm HSS would have worked better, but I don't have any; shopping list amended... The cutting tip was honed on the oilstone to a nice sharp corner, with a very slight radius.
The taper was bored out with light cuts as the workpiece was sticking out so far. When the outside end reached 11mm in diameter I stopped - this is the measurement where the "11" in ER11 comes from:
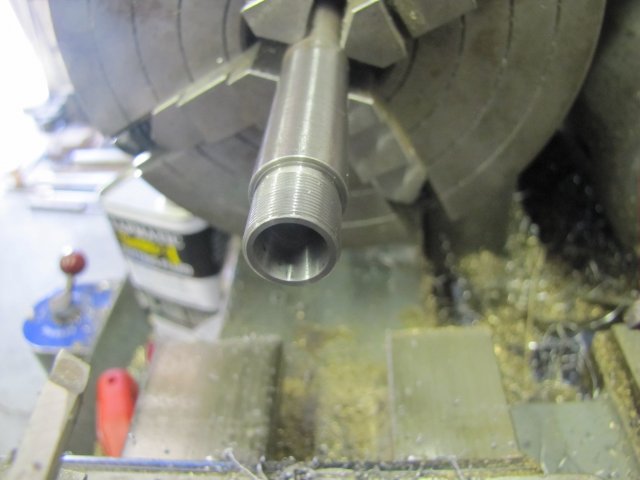
I love turning silver steel; it's easy to get a nice smooth turned finish.
Just had to try it out

- a 3mm collet with a 3mm drill bit chucked up:
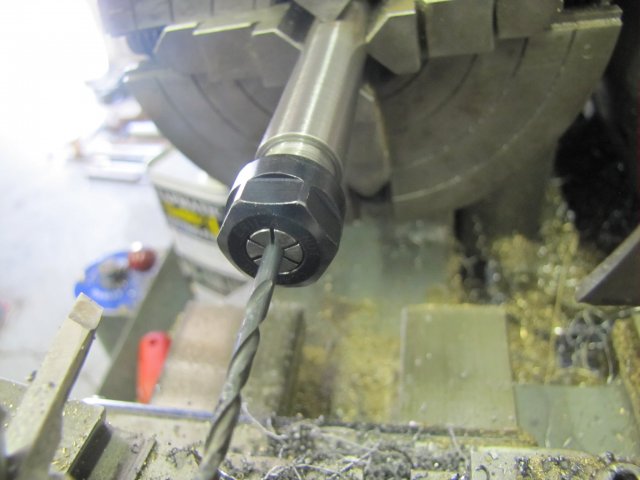
Parted it off, and the final result. Chuck body:
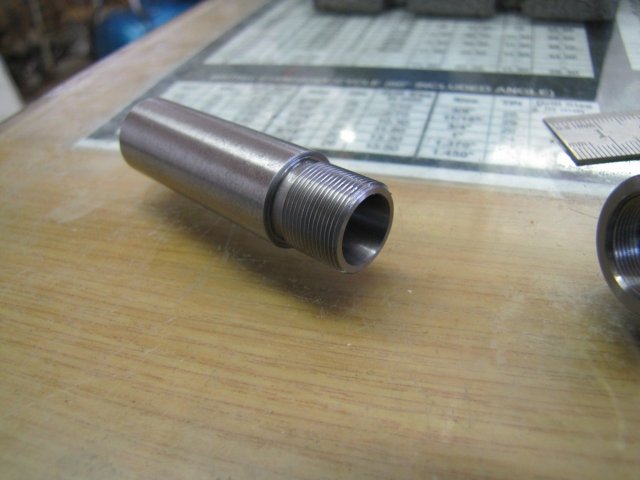
Where the collet fits before it starts to compress:
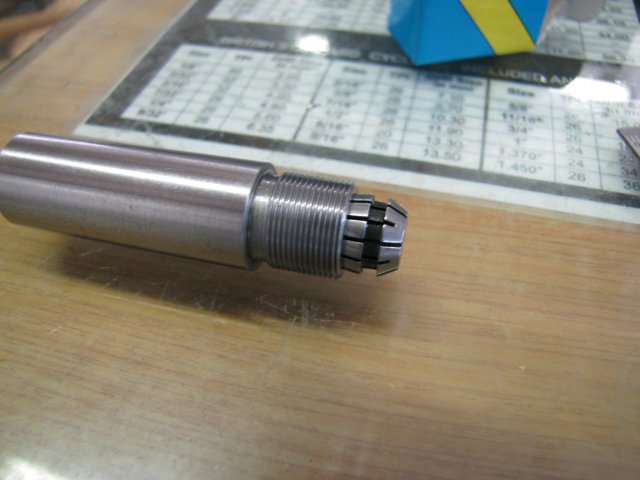
And the 3mm collet compressed with the closer nut to near its smallest diameter:
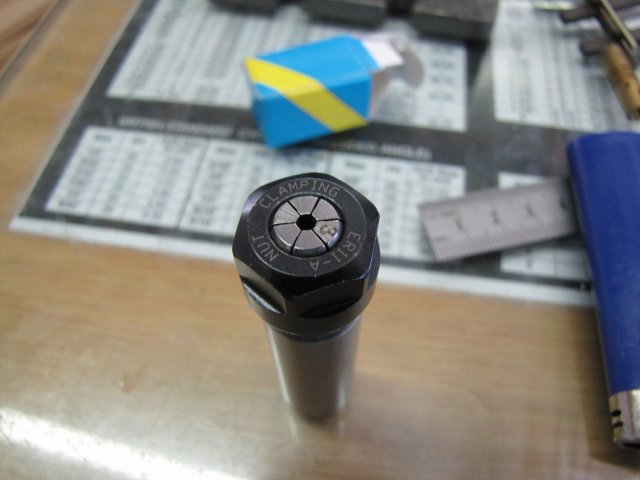
Of course, the center 7.5mm hole goes right through so that I can extend stock through it:
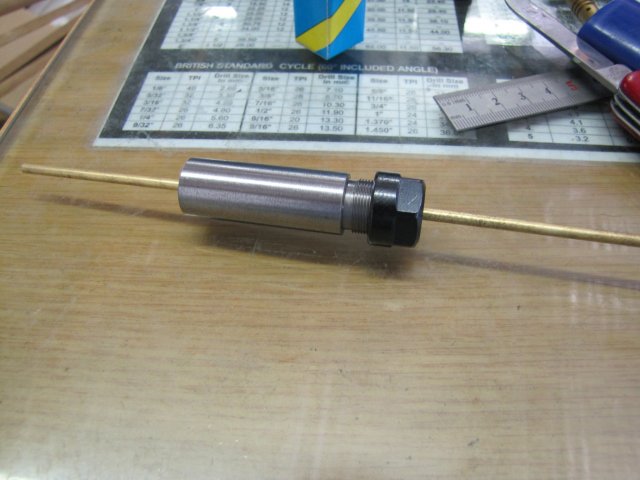
And a final check on the lathe. I chucked it up in the ER25 collet chuck, as it will see most of its use like this. The 16mm ER25 collet has about 0.01mm run-out; both combined in this setup measured less than 0.015mm run-out; which is fine with me. If I need higher precision, I can always just clock up the ER11 chuck in the 4-jaw chuck:
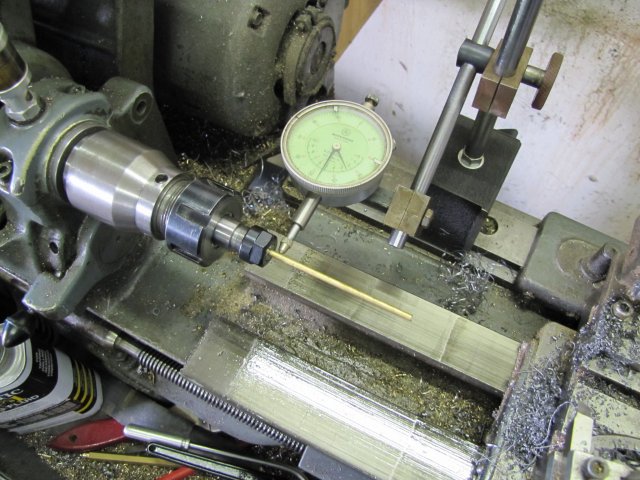
I didn't add spanner flats to the chuck body; if it's really needed I'll add them later. Of course, this is not the most ideal setup, but will do in more than 80% of the cases where I need to grip small bits on the lathe. It will also work on the mill to grip small cutters or drills. I'll make a dedicated ER11 chuck for the small lathe once I get around to making a stand and mounting it.
Regards, Arnold