Thanks for the great comments.
Pete49: I would be happy to share the drawings, if I really had any! I made a rough layout drawing of the casting pattern in my old CAD program for a reference and then proceeded to ignore most of the dimensions.

NickG: Ya, I find casting kind of difficult at times also. It's nice I have a good supply of good scrap aluminum to work with and made various pieces of equipment to make it easier on me. It definitely as a learning curve! I learn something every time I try it.
madjackghengis: Thanks. I didn't know if I really needed a die filer at this point, but it looks to be something that could be useful and I thought it would be fun to try to make one. I looked at he prices of the casting from a couple of sources + shipping and figured I would try it. I'm looking forward to seeing how it works!
Bernd, DaveH: Thanks.
dickda1: Thanks, like I said above it's nice to have a good source of cast hydraulic pump housings to work with. I have had some issuses with defects and have used JB weld to fill pit holes it need be.
On to making rest of the parts. I made the drive shaft from a piece on 1/2 inch O-1 rod, a slice off a chrome plated cylinder rod, and 5/16 dowel pin from a hydraulic pump. All pressed together with a little Loctite.
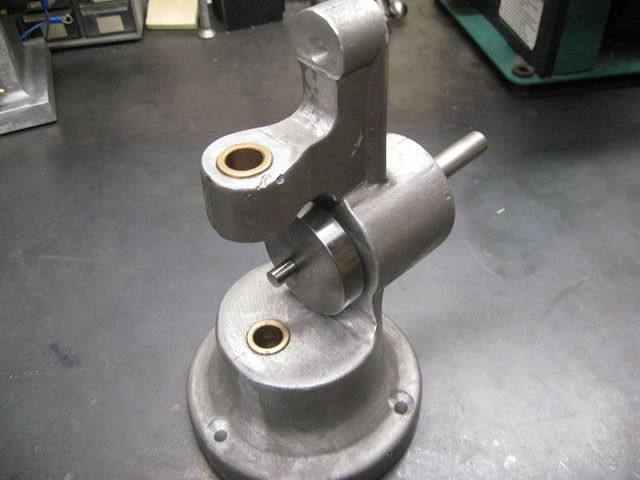
Testing the fit of the reciprocating shaft and getting the measurement from the end of drive pin to the shaft. The 6 inch A belt pully was bought at the local hardware store, I'm to lazy to make a pattern for something I can buy for $11.50!
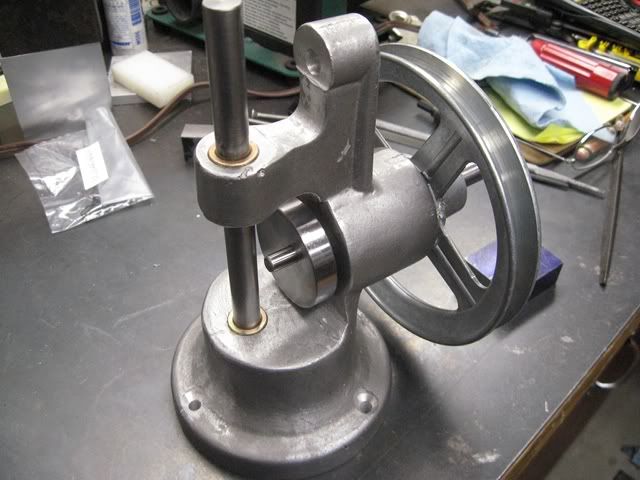
Fitting the cross slide block. The brass came from melted down pump wear plates which I cast a block from. This whole project owes it's existence to people destroying hydraulic components!

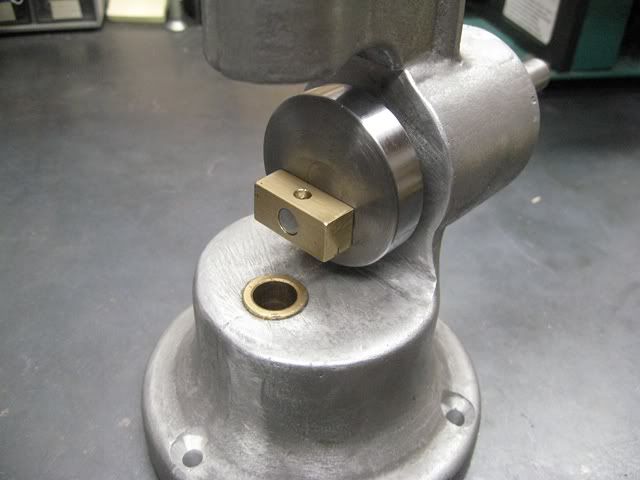
Test fitting the cross slide block:
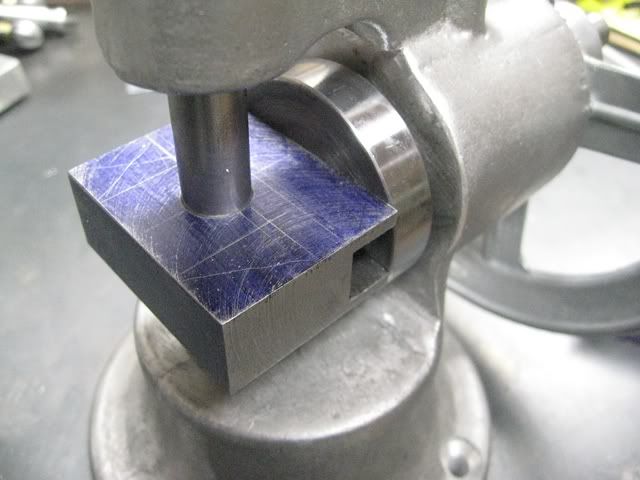
Forming the rest of the block:
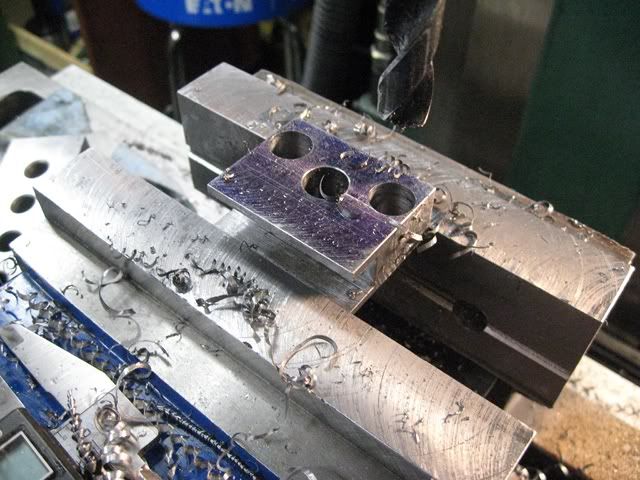
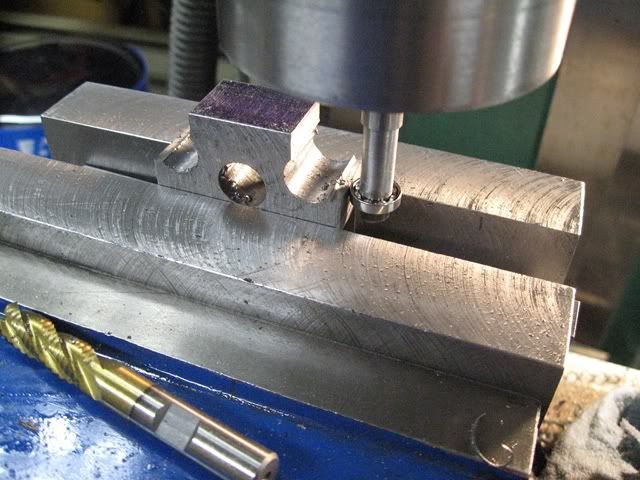
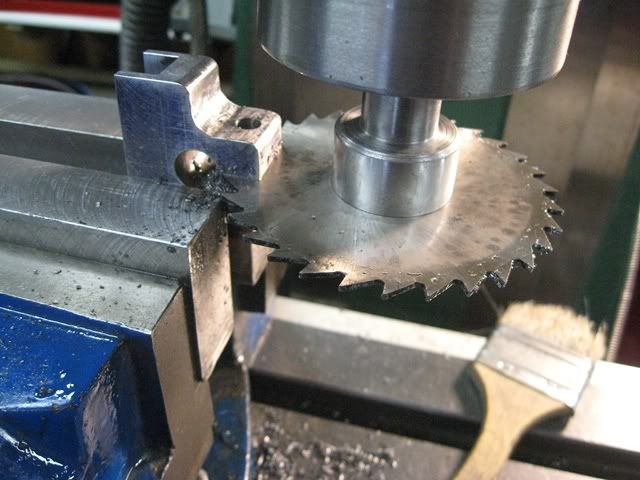
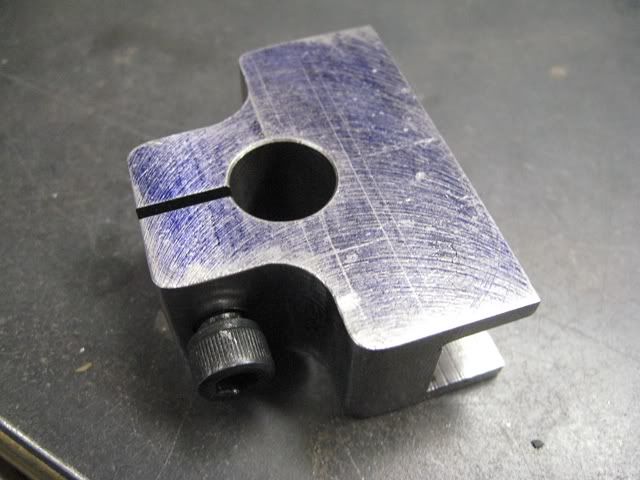
The reciprocating shaft was drilled for 1/4 inch diameter file shanks. I only have 1/8 inch files, but I'm anticipating future options! I was then sliced in half to allow the bit clamp grub screws to tighten up on the file shanks.
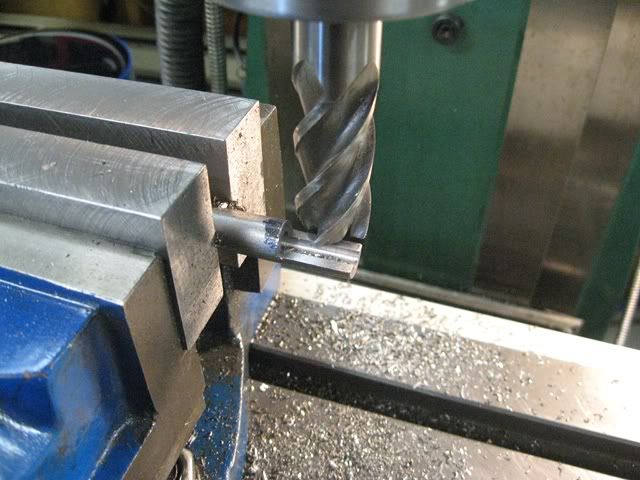
The clamp was made from another cylinder shaft, drilled to slide over the shaft, and tapped for two grub screws and finially cutoff and the cut faced on the lathe.
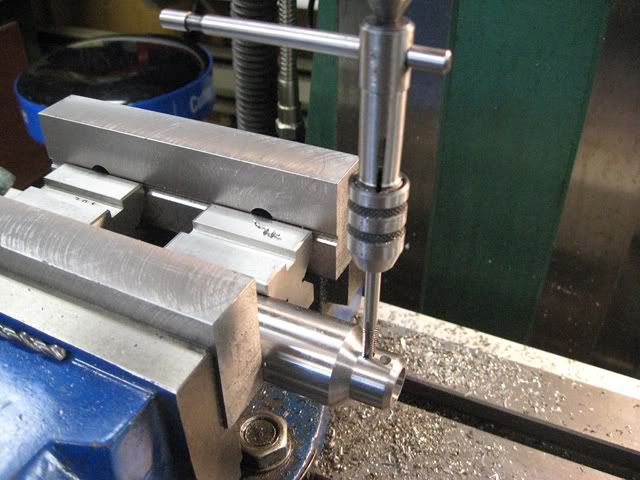
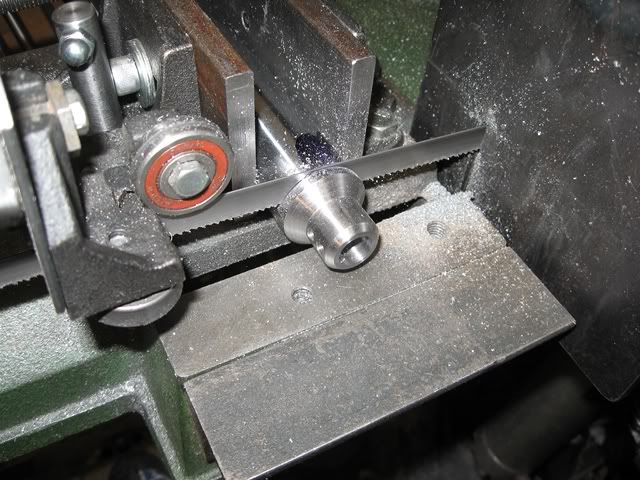
All the main parts made:
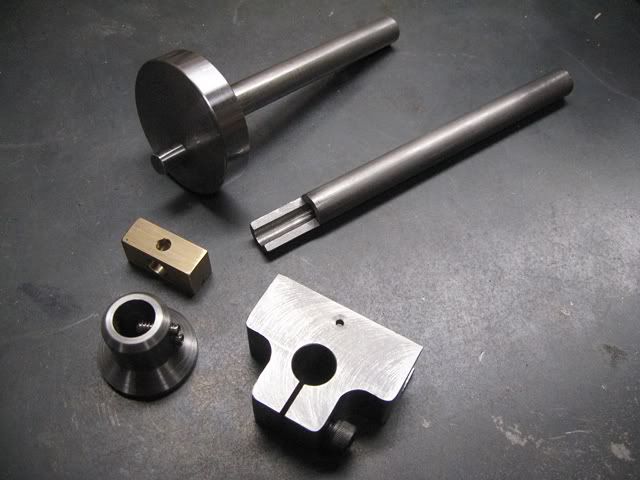
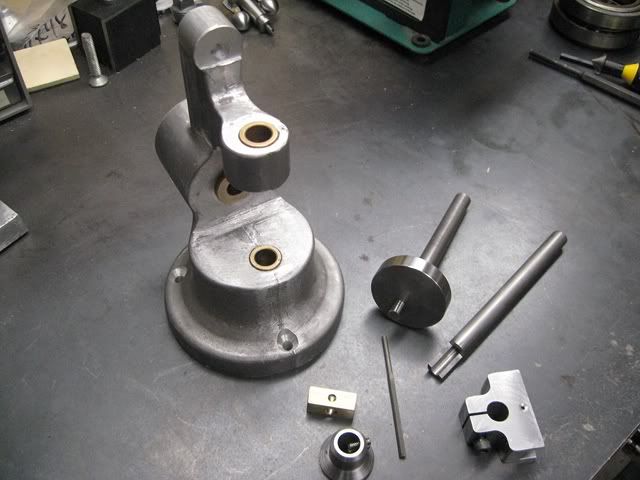
It's coming together now! I hope to get it assembled tomorrow and run in and start making a pattern for the table.
Thanks for viewing.
Al