Hi to all modders,
My first try at a bit of a post on here, hope this is the correct place to post, it will take a while to finish.
This saga started from brand new. After the cleanup tried to turn some parts from PVC tubing with poor finish and not taking the same cut in and out. Investigation revealed the gib plates on the saddle to be LOOSE

. Trying to adjust this it was soon apparent that the bed ways was not parallel top to bottom, being a lot thicker at the tailstock end. This was corrected manually using various oilstones. The gibs were also adjusted with shims rater than the adjusting bolts. Since then I was able to turn quite a few parts but always had problems with the finish on mild steel and parting off, even plastics. Then added a Soba vertical slide for milling and had reasonable success milling aluminium. Recently I tried to do some simple milling in mild steel with a 8mm end mill with disastrous results, mill broke. Further investigation showed that under force the cross slide lifts up on the right (gib strip) side. Looking into this showed the gib strip to be to small and actually rotating around the adjusting screws. After a failed attempt to fly cut a new one on the lathe, frustration,

nearly putting a sledge hammer to the lathe

, as a last resort ended up making a new gib strip old school by hand. This was actually quite fast about 7 hours spread over 2 days. Here are some pictures of the process. The final surfaces were lapped with W&D on a piece of thick glass.
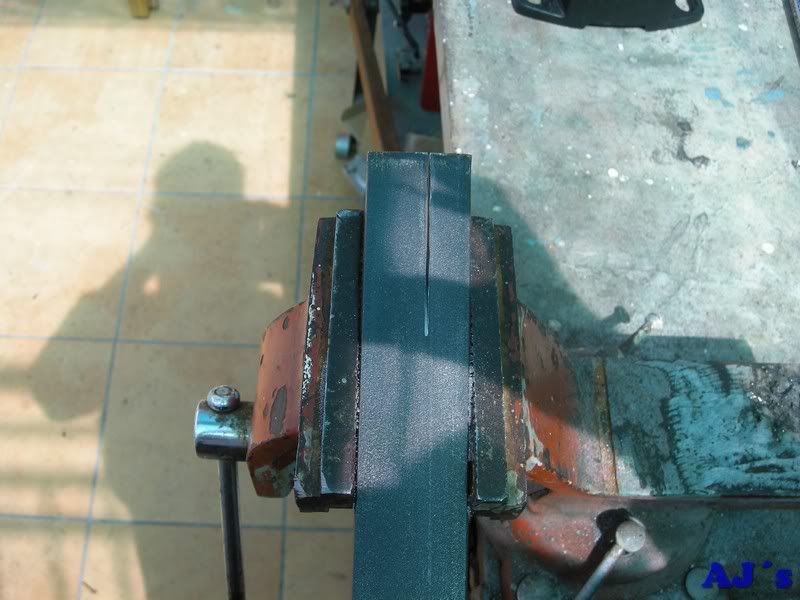
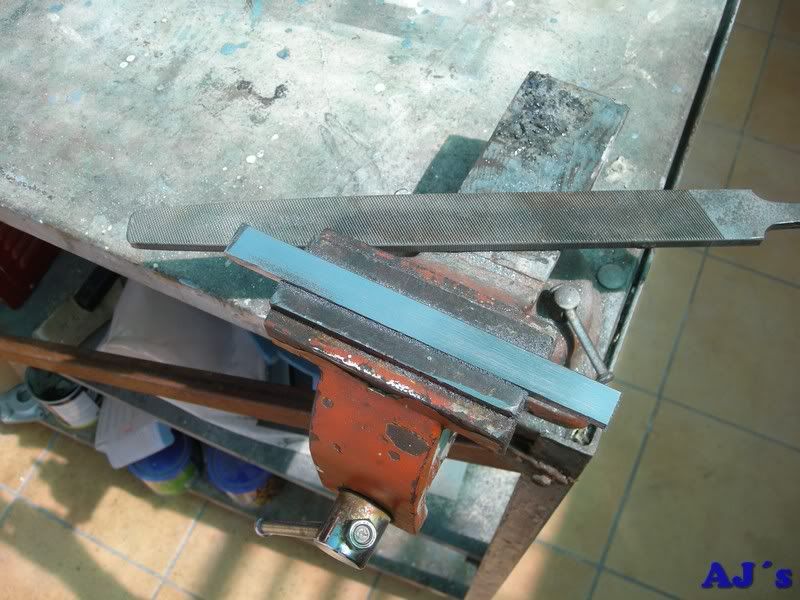
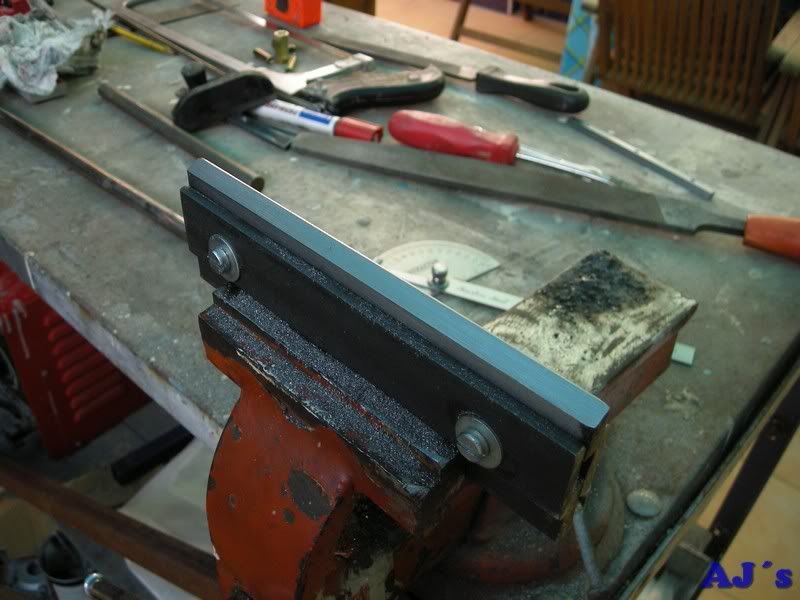
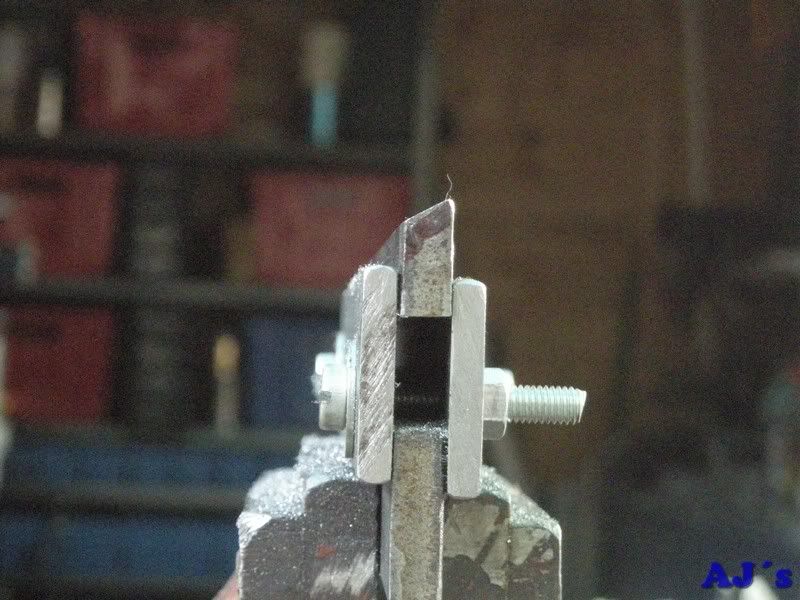
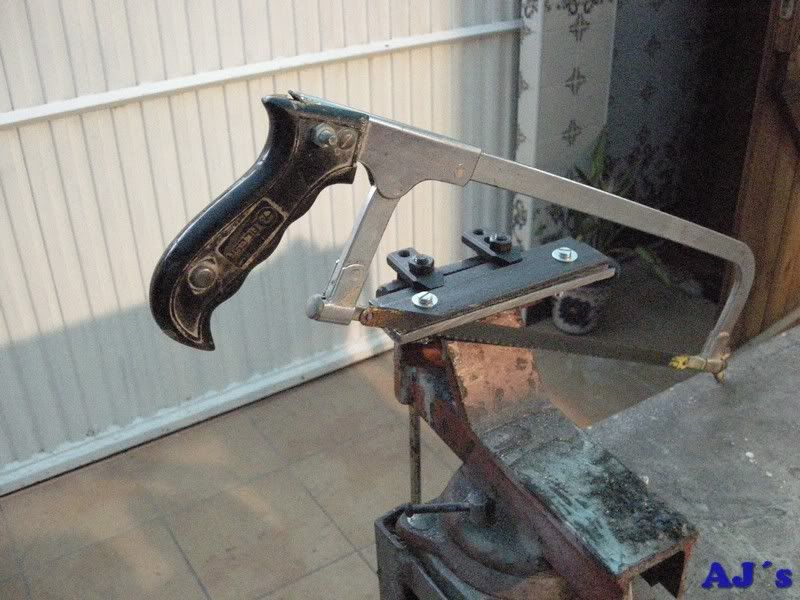
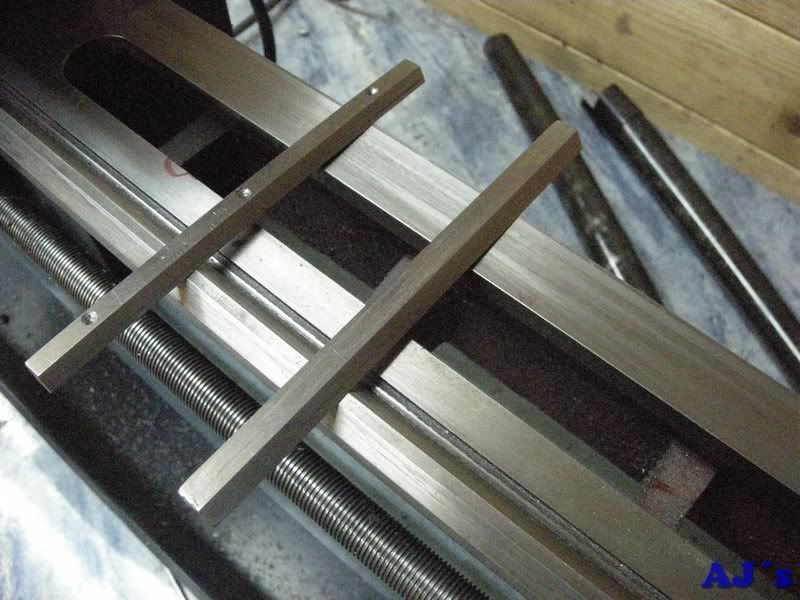
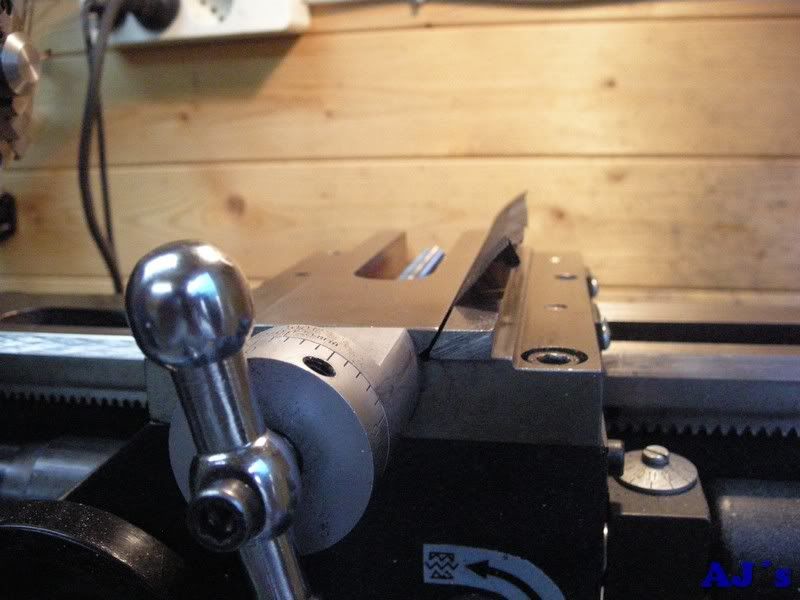
Before cutting to size the gib was used with some W&D to clean the dovetails.
Also noted the saddle has picked up some play, so this was removed and then following methods from here and some other sites on the web the saddle was lapped to the bed ways, testing regularly with mechanics blue.
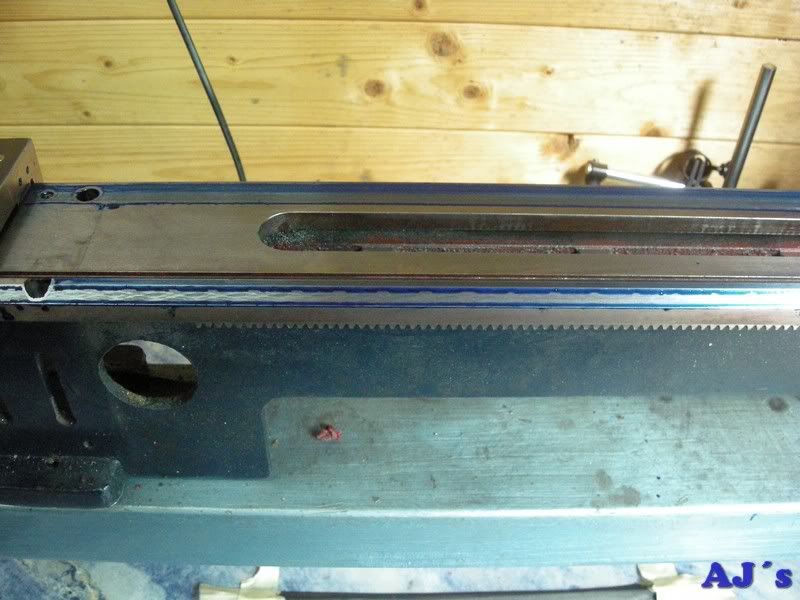
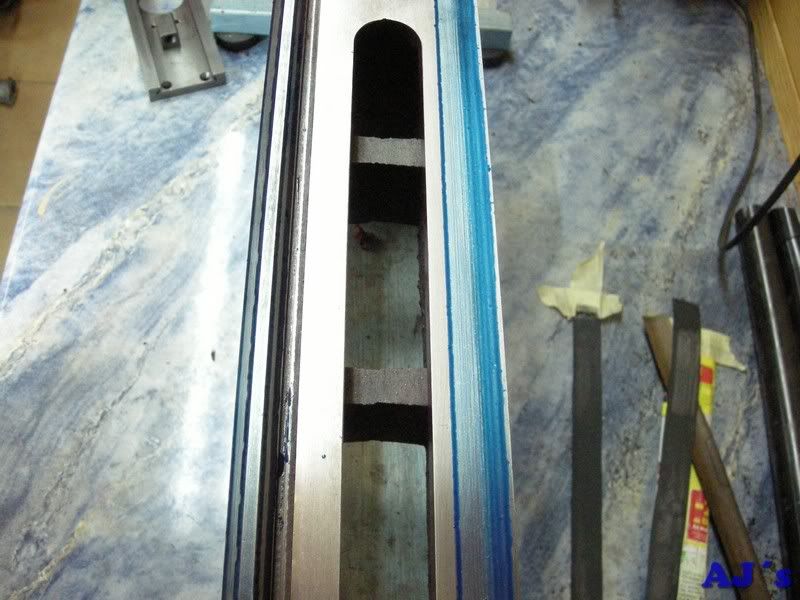
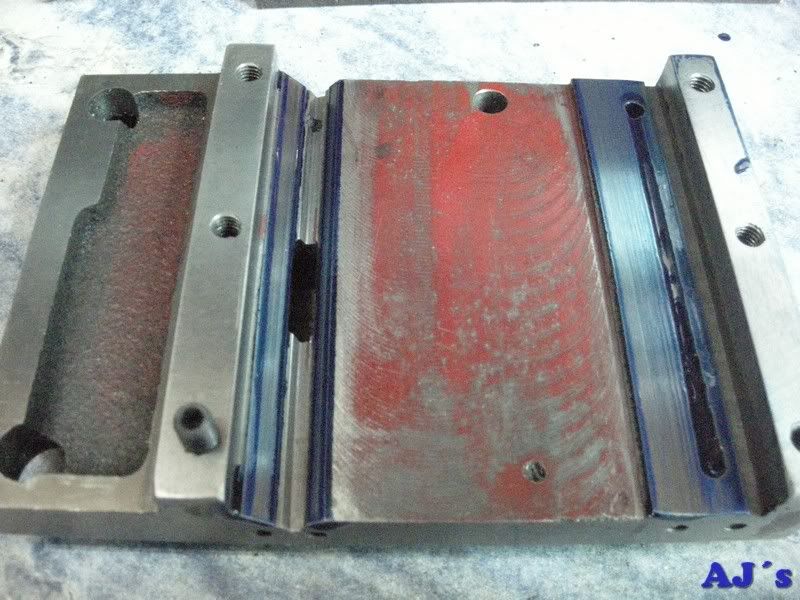
The bed was rechecked wit a micrometer and filed and honed some more for smooth constant fit.
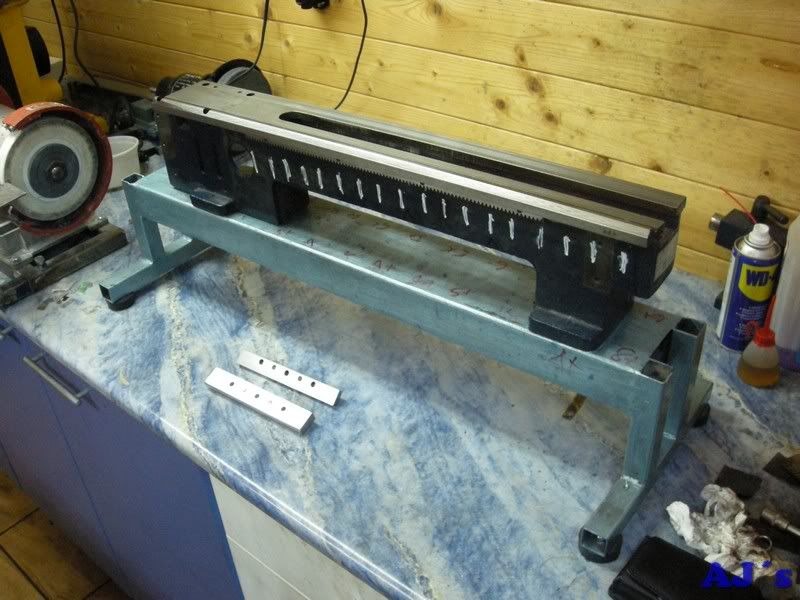
As I do not have a milling machine, new gib pates was hand made from calibrated mild steel flat bar, These are thicker and longer than the originals to add more rigidity. They will also be fastened buy SS studs rater than cap screws. (This is not my idea, seen on the web)
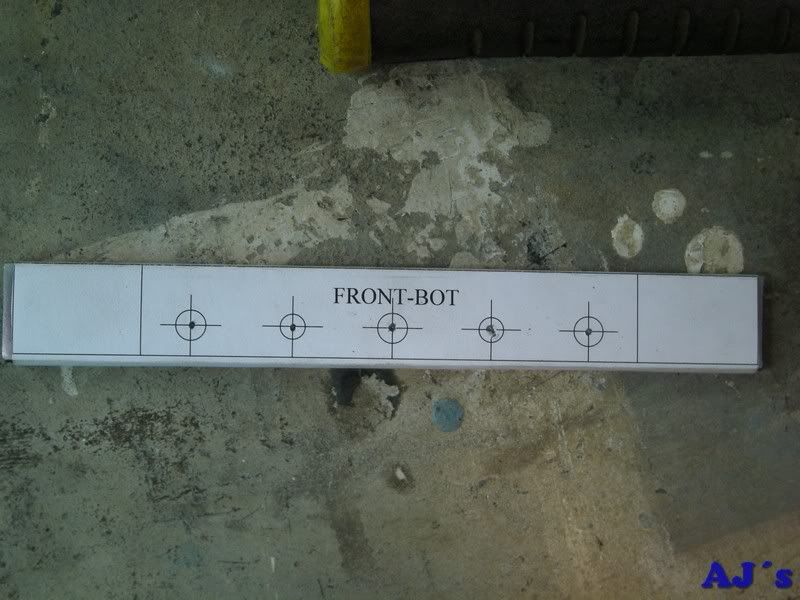
As the bolt holes in the saddle are all over the place a template was drawn to drill them.
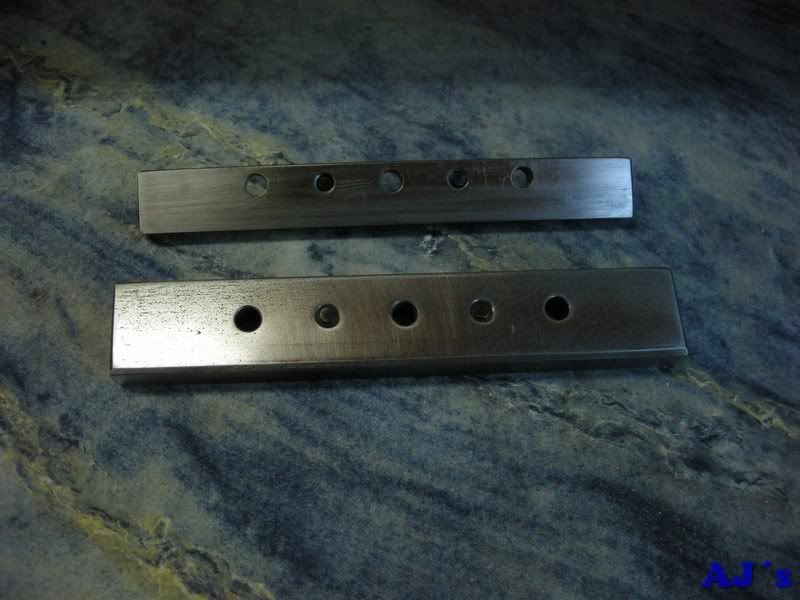
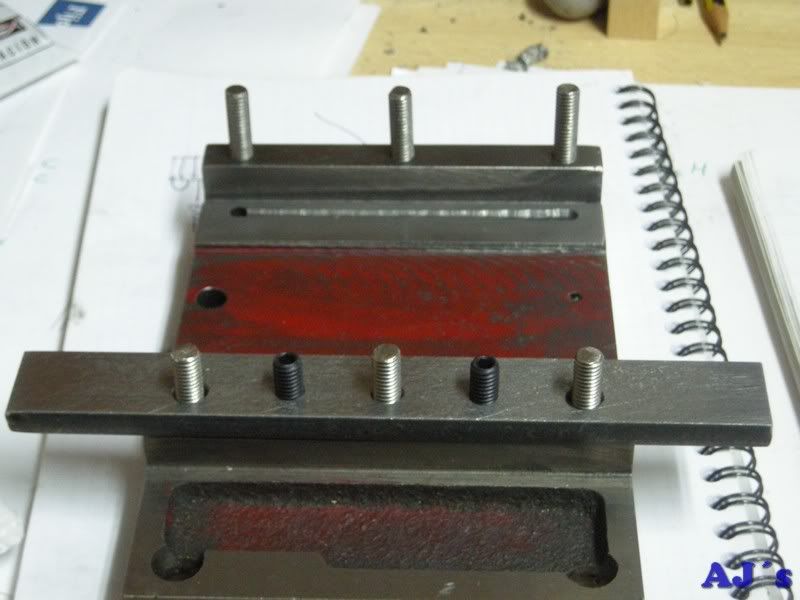
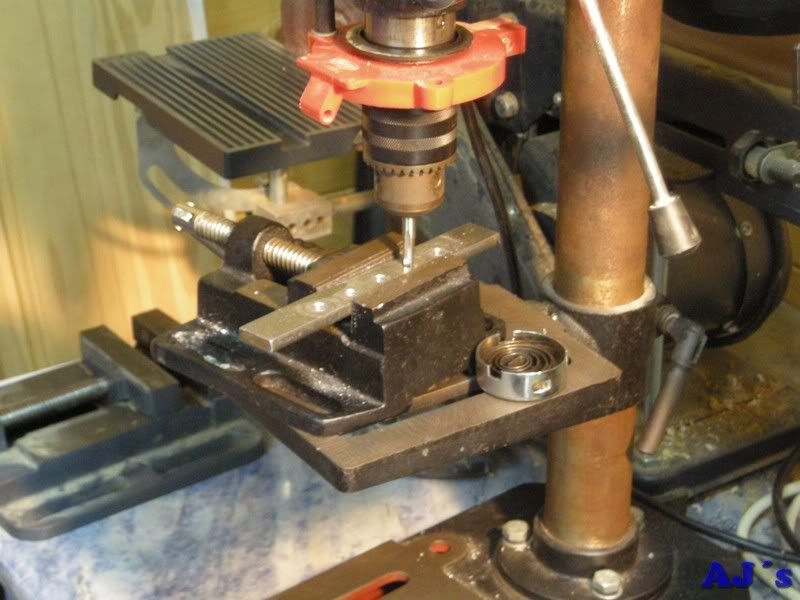
Using the modified drillpress as a tapping stand.
For the mods/repairs to the bed and saddle the lathe was striped down and a nasty surprise found in the headgear.
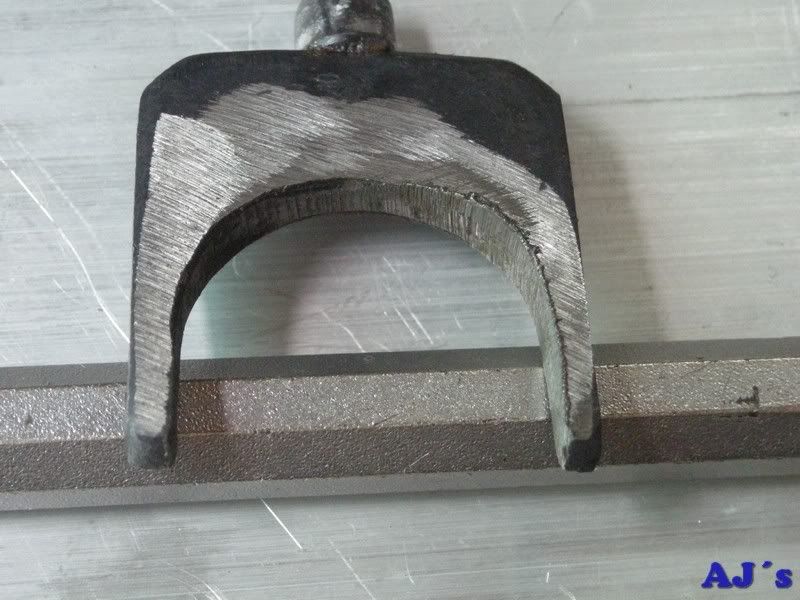
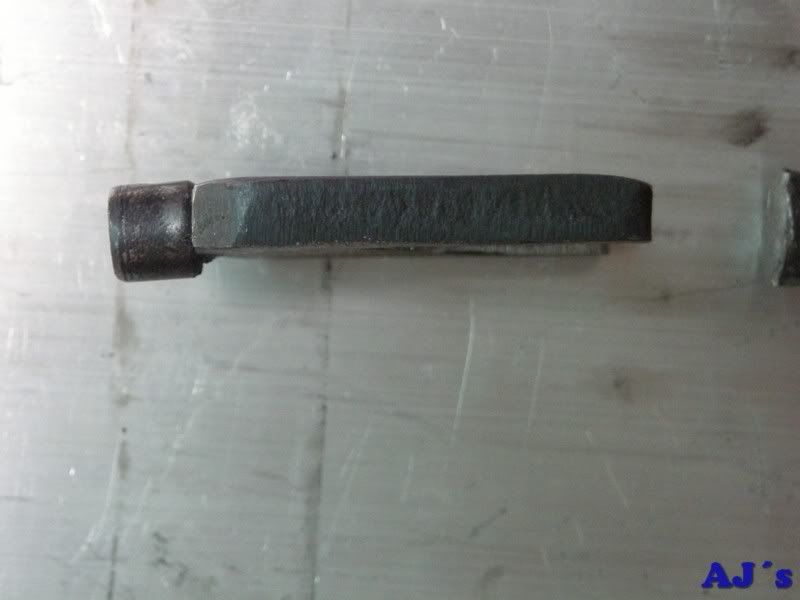
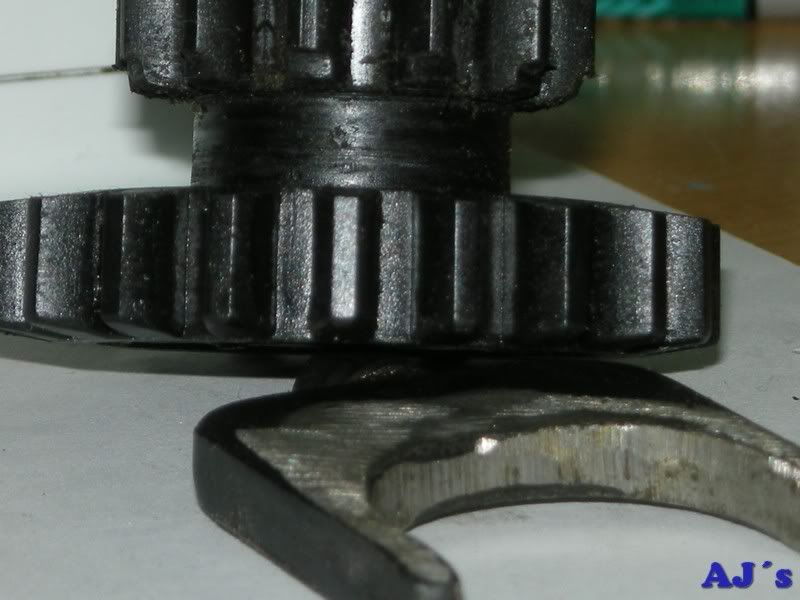
Looks like a gorilla with an angle grinder made the shift fork

. The detents are also no good, causing the damage to the change gear. This will be looked into later in the rebuild. Hoping to save funds for taper bearings and metal gear.
Next up is refitting the rack to the bed, this will be shimmed for better engagement. Unfortunately rain, blocked drains and doctor’s appointments will be delaying this a bit.