I got the idea for these from another blog. The original original is from
Workholding in the Lathe by Tubal Caine. A highly recommended read that has stopped me from abusing my chucks

.
These faceplate dogs are designed to be used for attaching odd shaped objects to a faceplate where you want to have access to the entire surface. They bolt into the slot up against the work to be clamped and then the set screw is tightened to hold the work in place. Sort of like a primitive chuck.
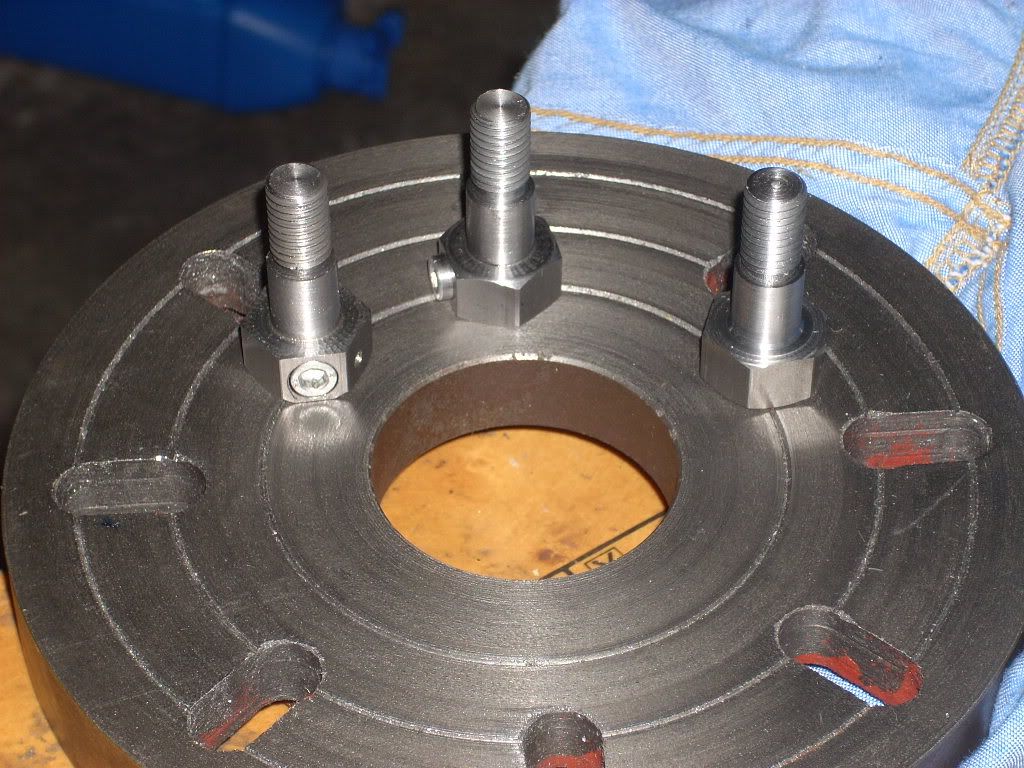
The one on the left has an extra little hole there. That is the original set screw hole that was mis drilled, so I had to start again from another face.

Here's how I made them:
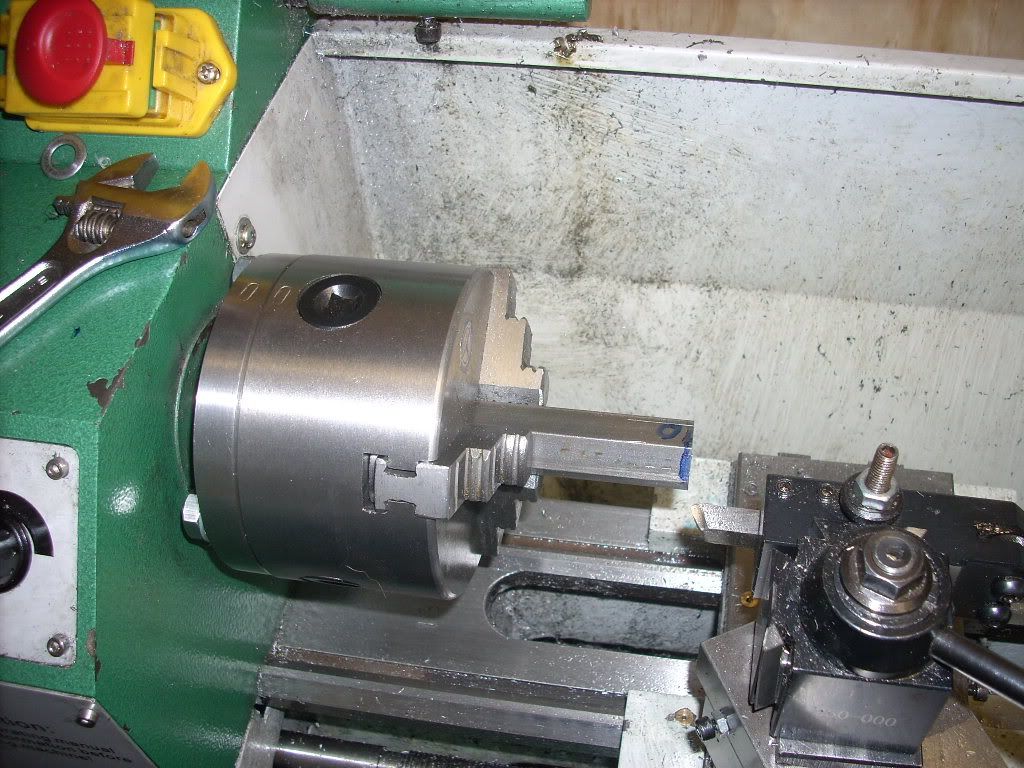
I started with a piece of 3/4" hex bar - note the marking to line it up with the stamping on the three jaw chuck. An attempt to get some repeatability. I should have marked it right along.
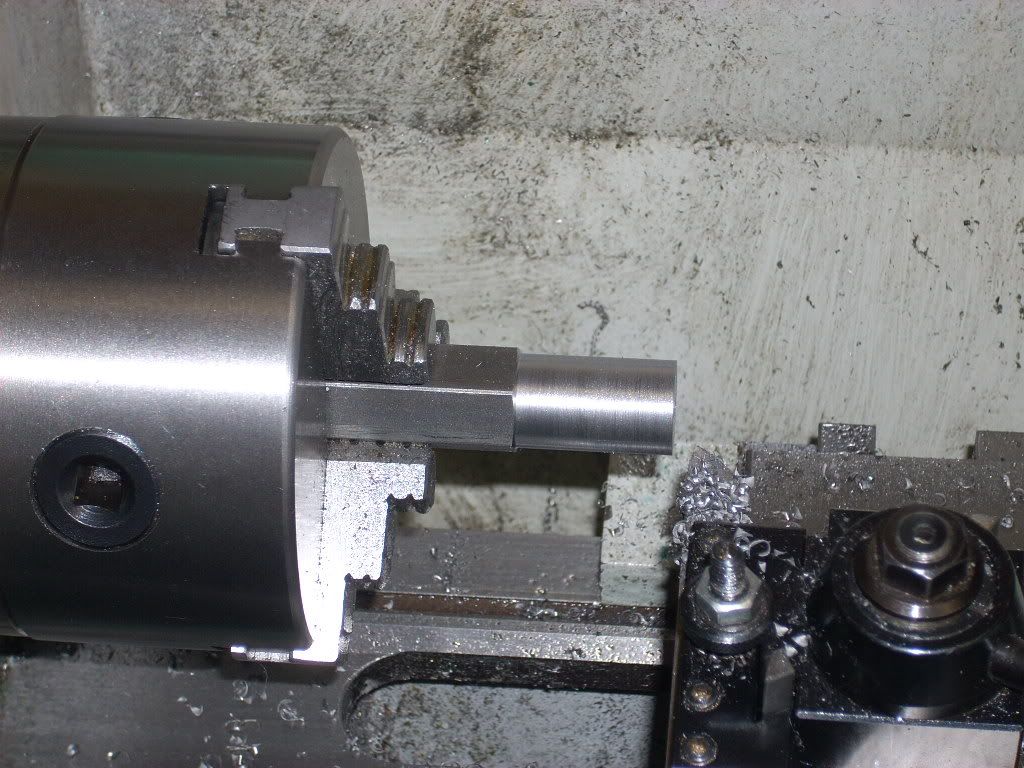
Here I have machined off the flats for the length of what will be the shank.
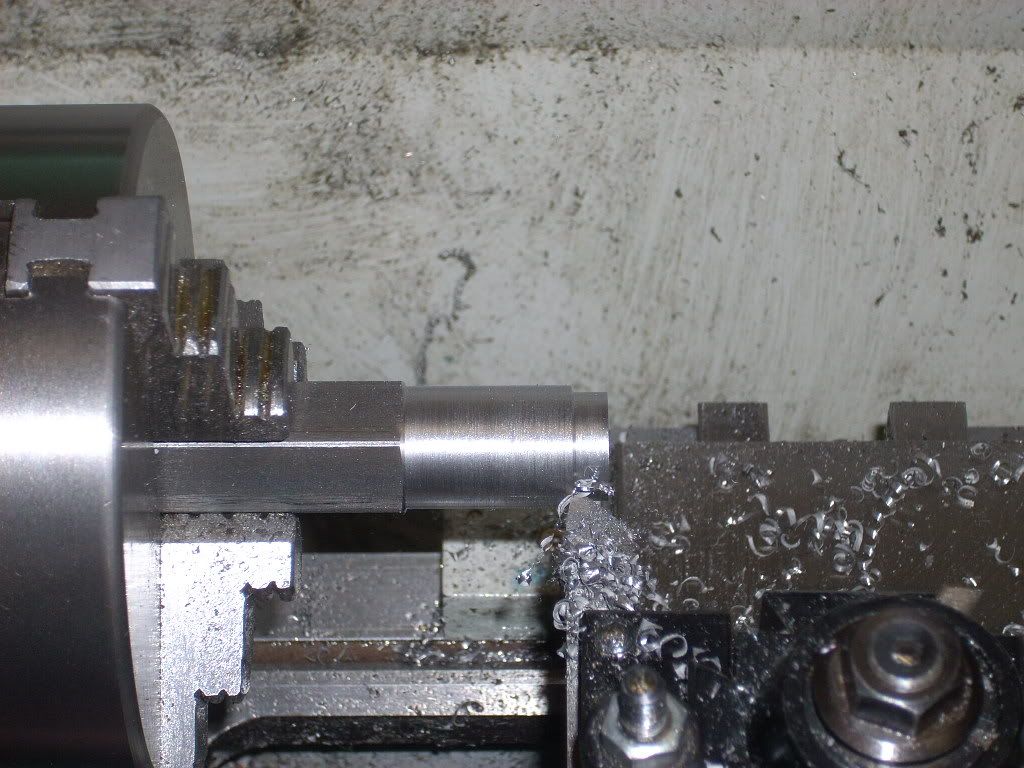
Roughing down the diameter to fit my faceplate
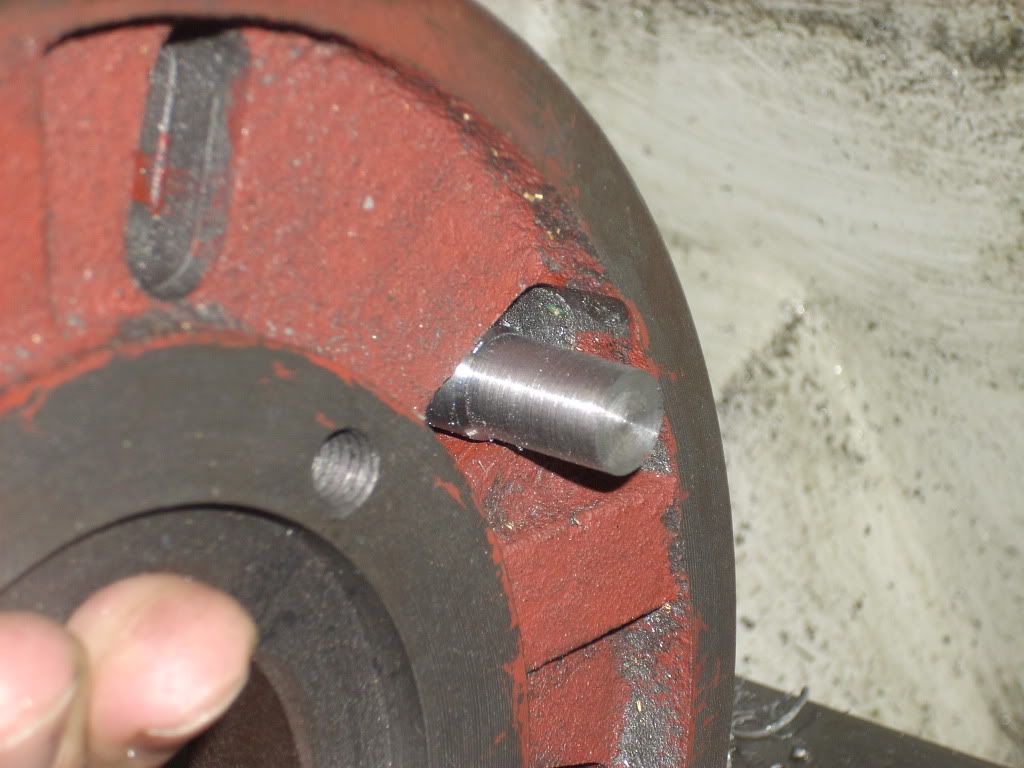
Once the shank fits through the faceplate. I turned down the end to 10mm for long enough so that the fatter part doesn't project out of the back of the faceplate. You can see it being checked against my faceplate here.

Cutting the relief groove ready to turn the thread. There are lots of tutorials for cutting threads, and everyone seems to have a preferred way, so I'll skip ahead here except to show this.
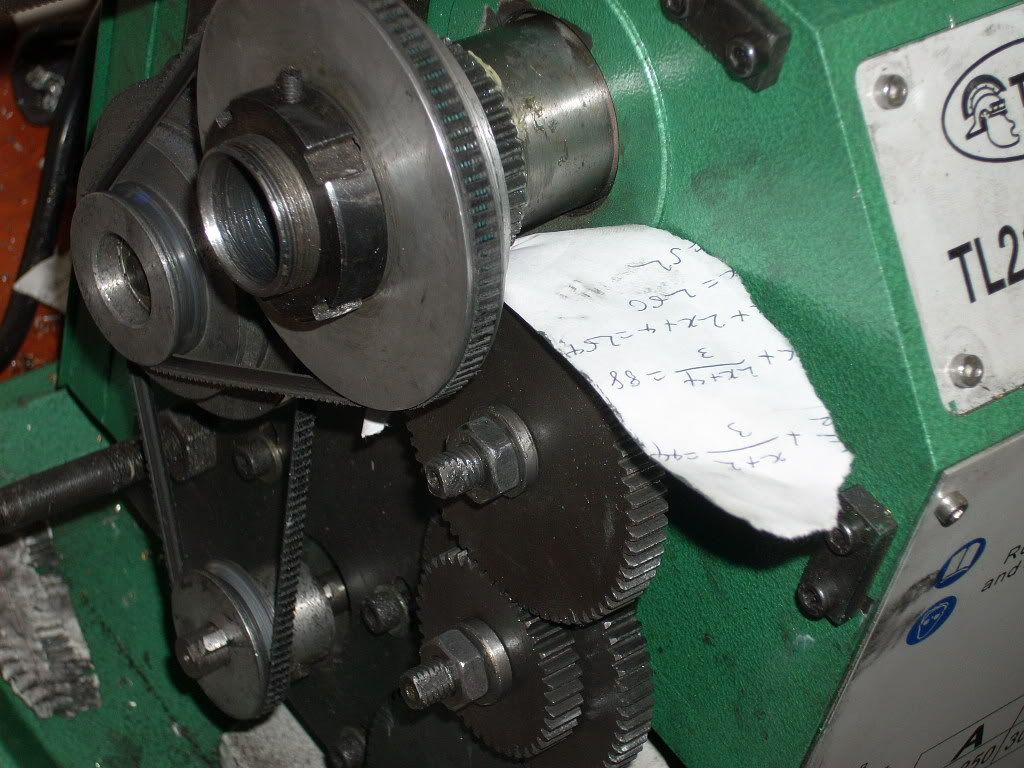
I run most of this job with manual feeding, and only engaged the leadscrew for cutting the threads. I did this for two reasons:
- Changing the gears is a long, tedious and messy job, that would have needed to be done six times for the whole job so it was less hassle to just feed by hand
- Feeding manually saves wear on the lead screw for jobs that really need it
The photo shows a piece of paper inserted between the gears to get the perfect clearance.
Finally - parting off. I don't know who said that parting off steel in a small Chinese lathe is impossible, but it isn't. Here's the proof:
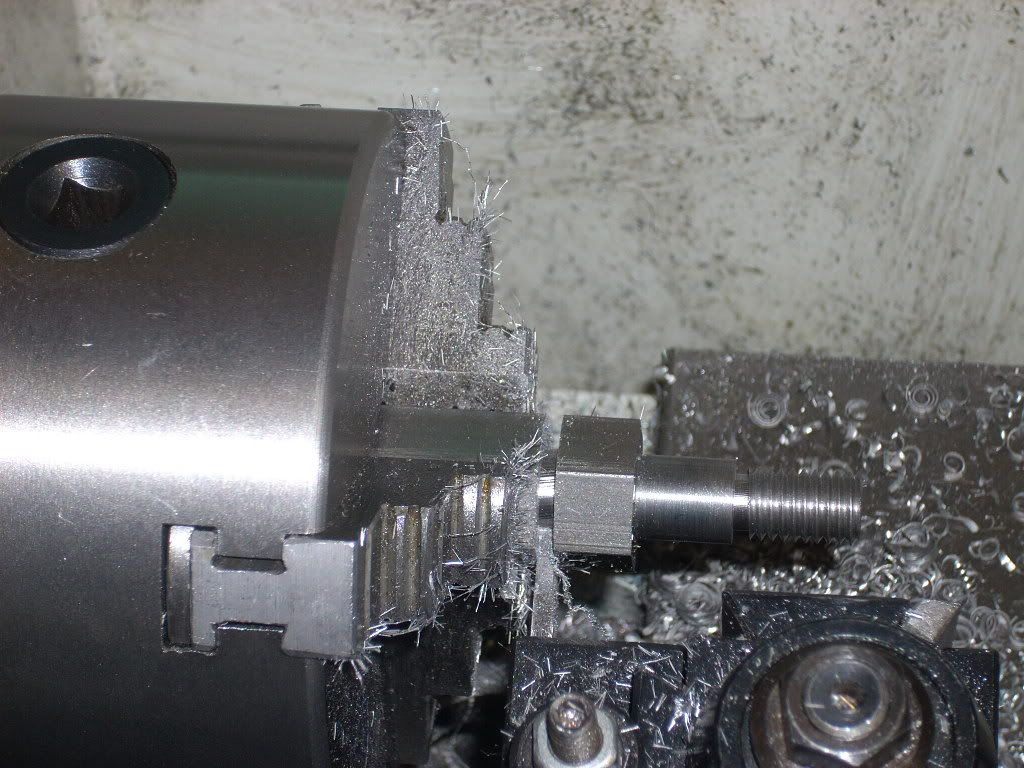
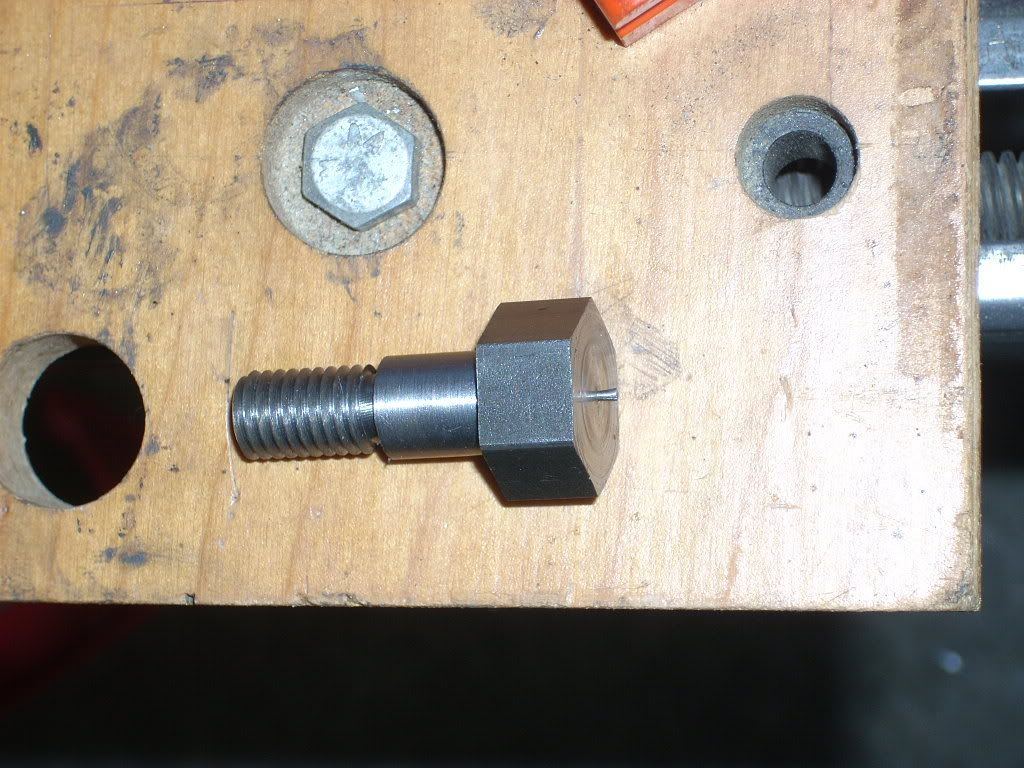
Then facing off the end:
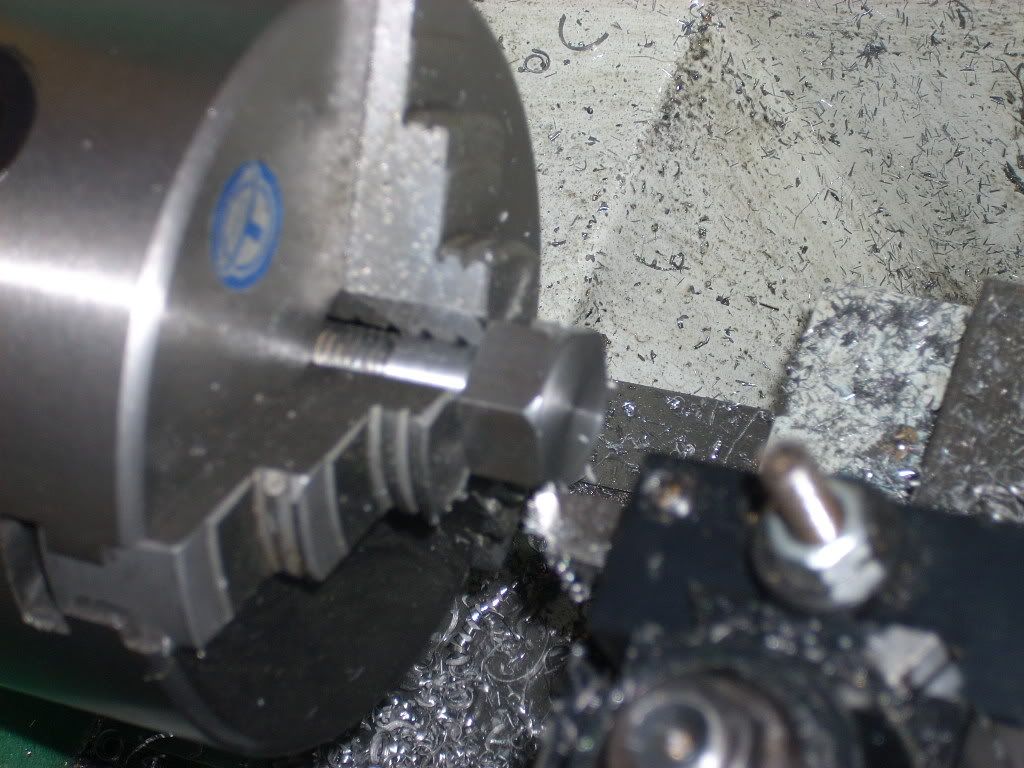
Now to the drill press to make the hole for the set screw.
I set up the workpiece using a spirit level like this
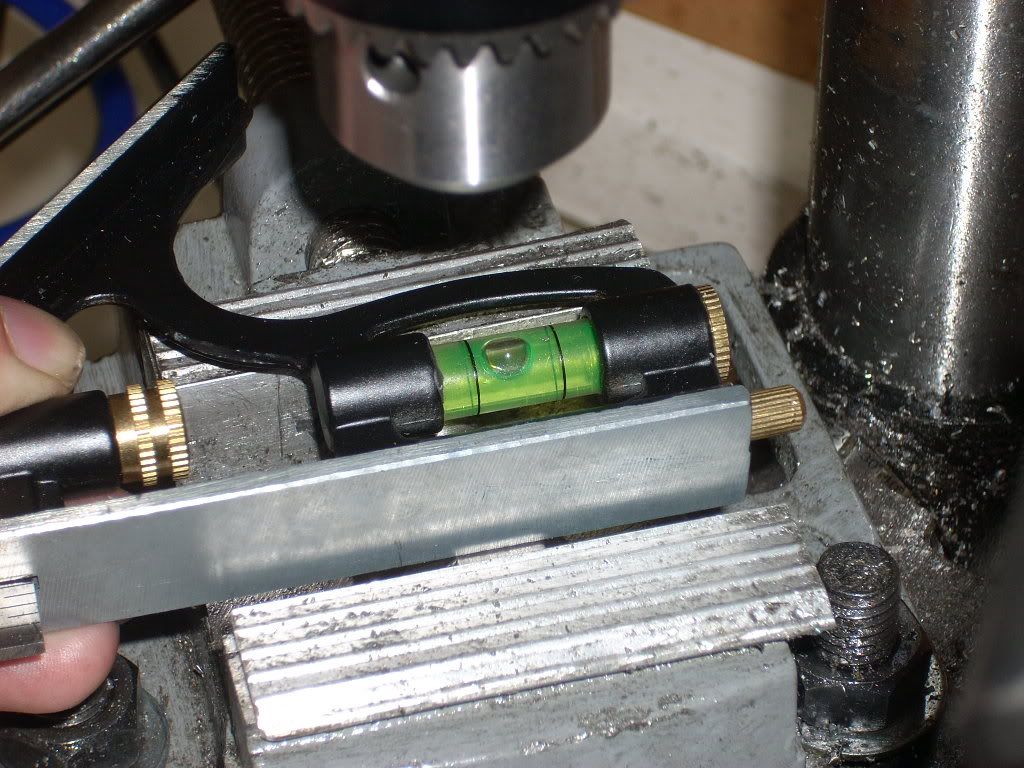
The hole was drilled for a 5mm tapped hole and counterbored to 8mm.
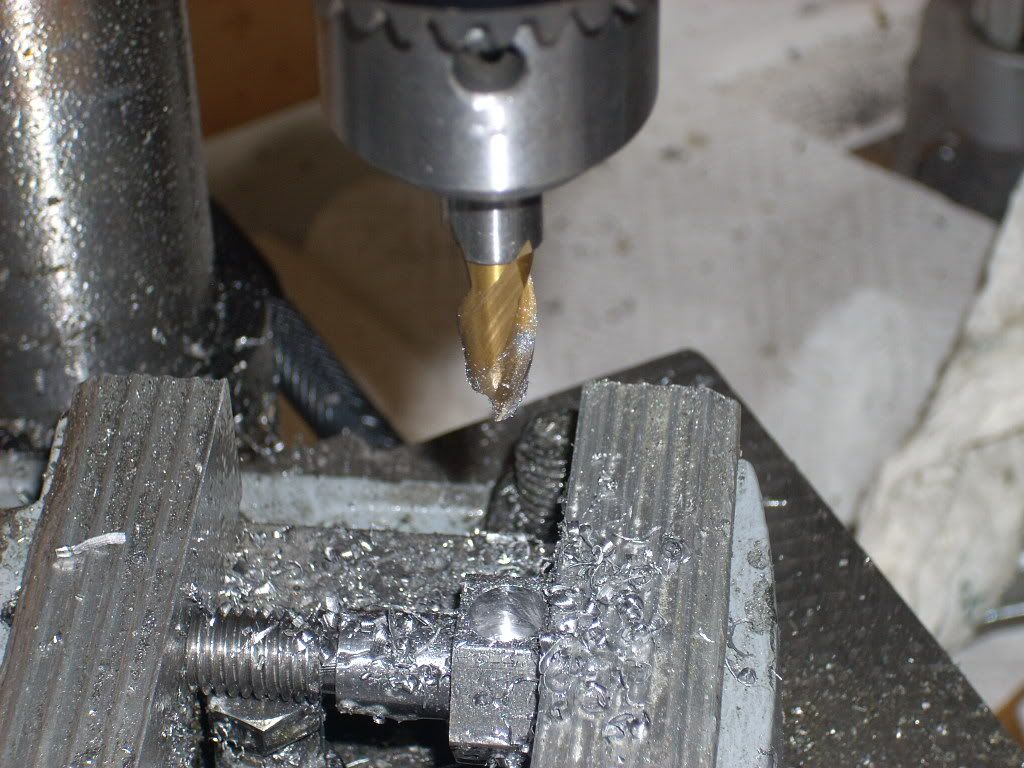
Tapping the hole
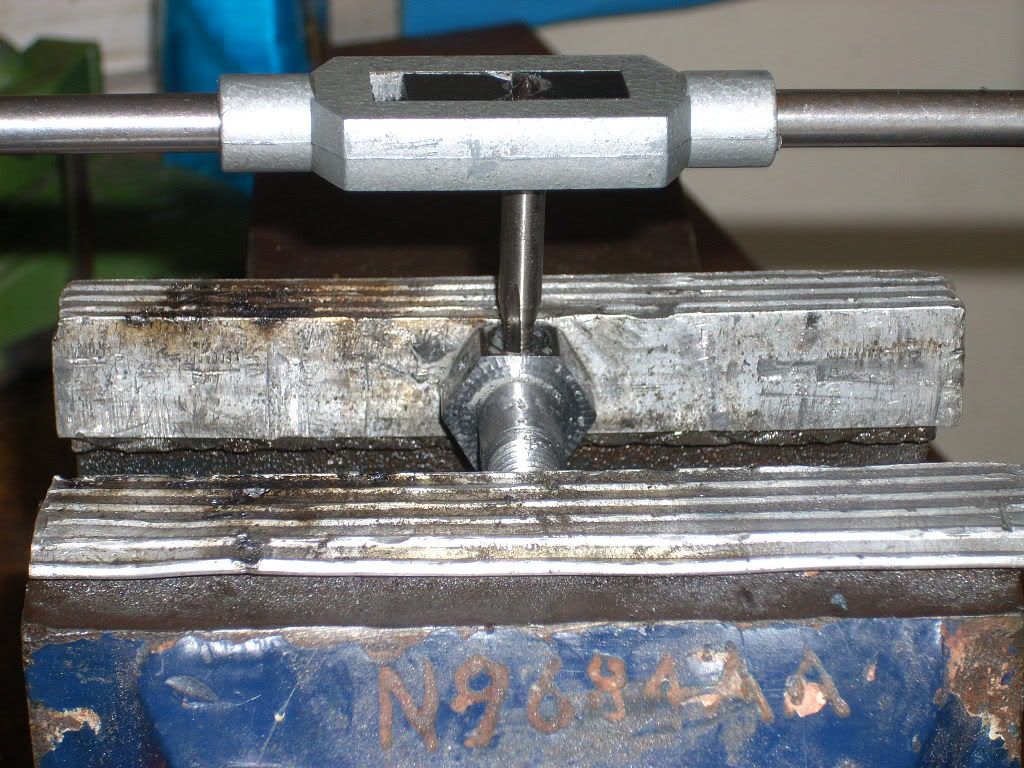
The set screws I had had heads that were 8.2 mm diameter so I needed to turn them down to fit the 8mm counterbore. To protect the threads while I did this, I made a simple 5mm threaded mandrel out of 3/8" hex bar.
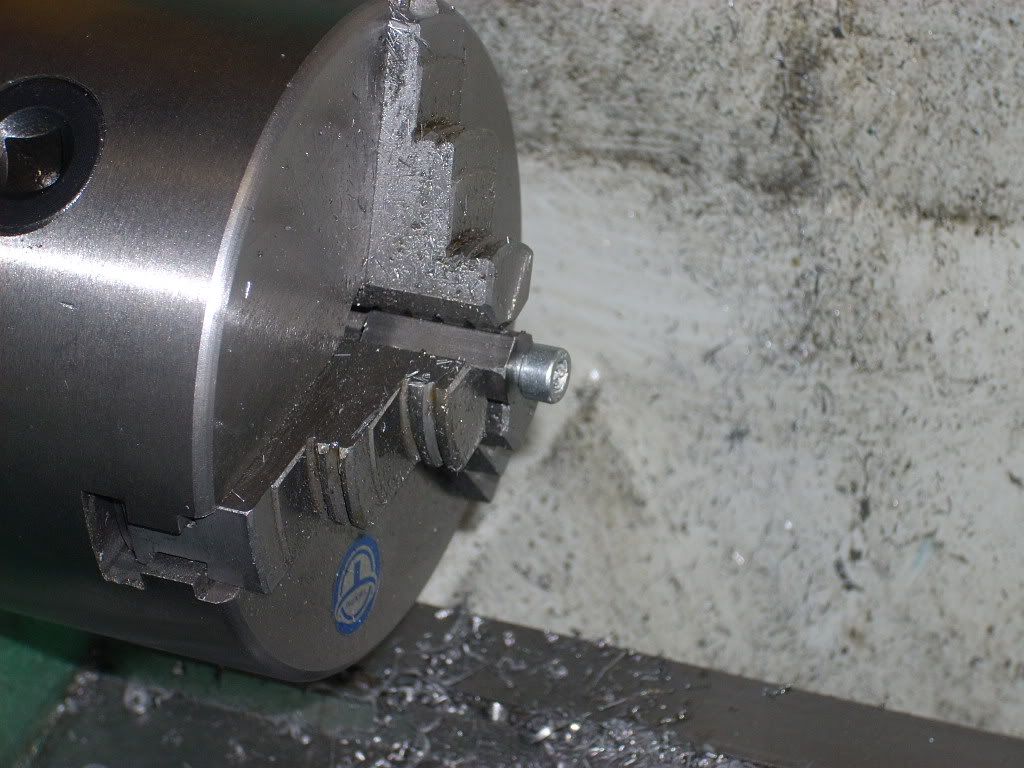
A finished piece
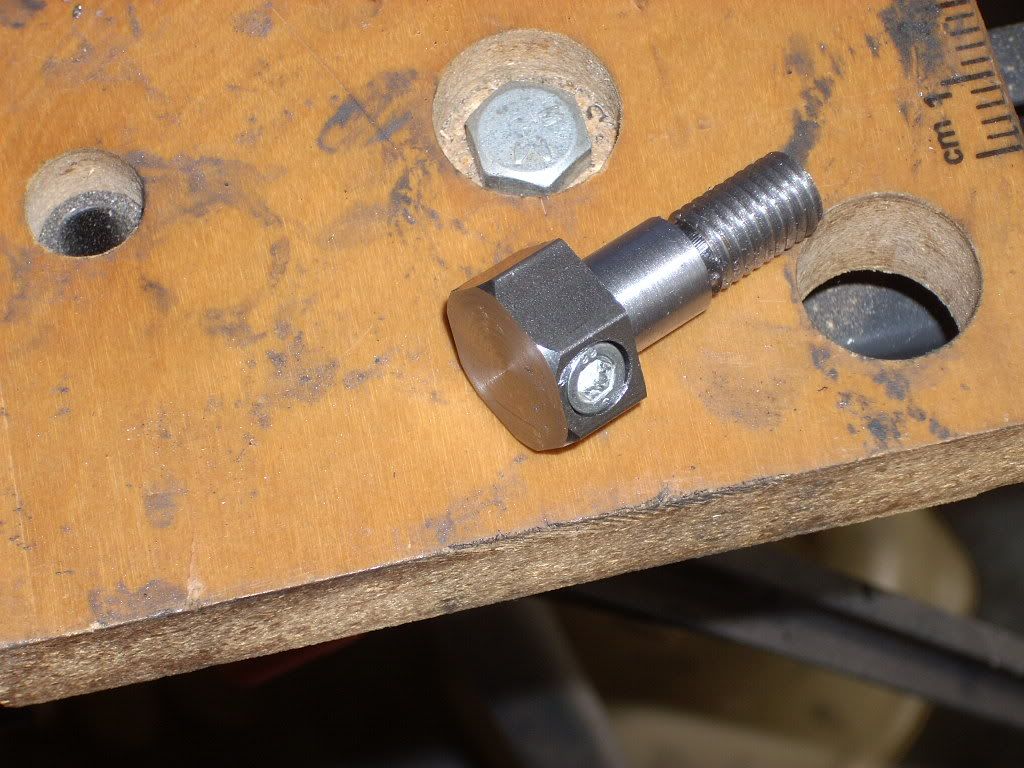
..and how it fits into the faceplate.
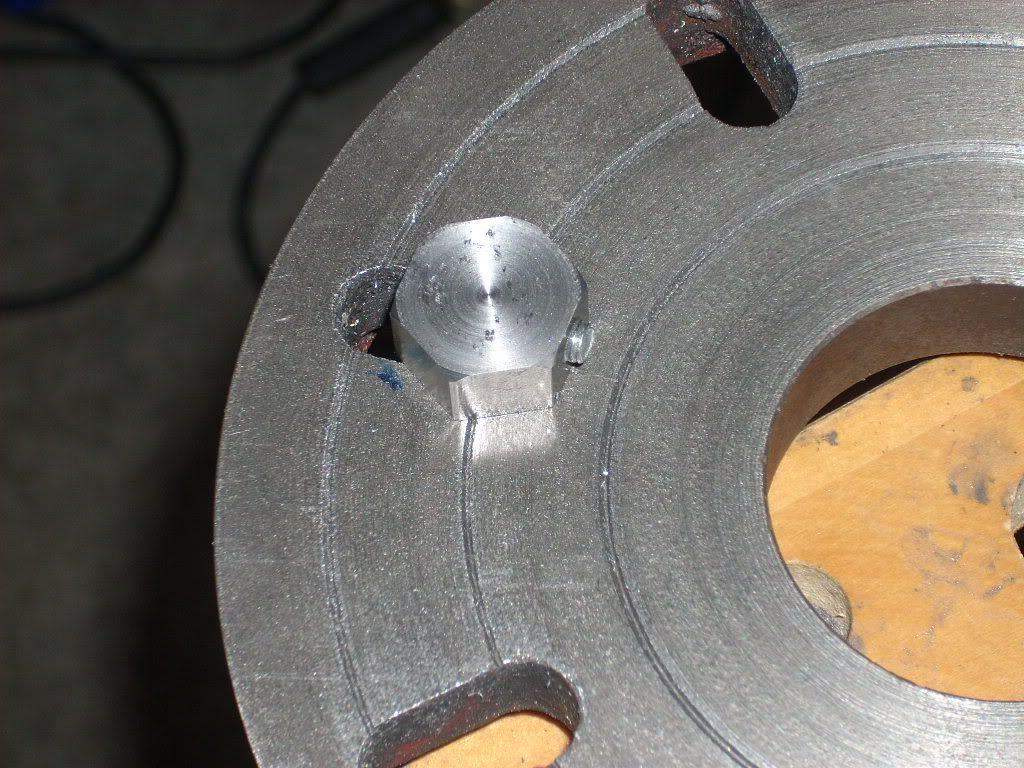
The motivation for making these was largely practice, but I also wanted to be able to make better use of the faceplate that came with my lathe. By using these, I can turn anything that will fit on the faceplate.