Jamesemery728 asked about a little arbor with a Dremel chuck that I showed in use while building my Little Blazer engine.
I'll bore you with the background first, then get on with the gory details

Earlier this year when I bought my milling machine, I was disgusted to find that the chuck supplied with it could take 3mm bits at it's smallest. I was in the
middle of a project then, and very broke after buying the machine, so had to get a quick-fix for drilling small holes instead of splurging on a new chuck. I had a Dremel chuck lying around that I bought a bit earlier in the year at a whim. So the little drill adapter idea was conceived and executed.
The Dremel nose thread has an external diameter of 7.1mm and uses a 60 degree 40 TPI thread.
I used a bit of 8mm silver steel and the Dremel chuck to start off with:
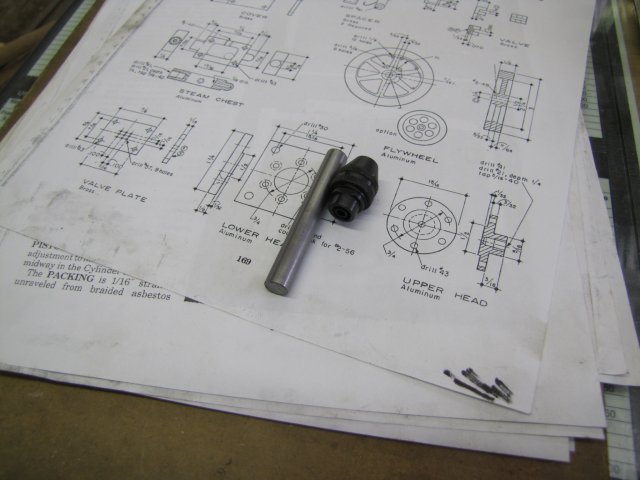
The arbor needs to be as accurate as possible. My home-built collet chuck has less than 0.002mm run-out with my 8mm collet, so I just chucked the silver steel straight up in it. If you don't have an accurate collet chuck, it would be well advised to use a 4-jaw chuck and clock the shaft as center as possible. Even better would be to use over-sized steel and turn down and then thread the entire job between centers, though that will leave you with no way to test the thread to the chuck before finishing.
Use a parting tool to turn an undercut for thread run-out; the threaded section needs to be long enough for the chuck to screw on quite a distance, as it uses the arbor to close it's jaws.
40TPI is a fairly fine thread to single-point turn, so just take a little care and clean all the lathe change wheels and feed screw very well before starting - it does make a difference. Don't be tempted to try and single-point turn a fine thread right down to size; it needs a delicate approach to get a good finish; I used about 6 consecutive infeed passes to get down to root diameter - with two passes at the exact same setting to get the finished result. It's easier to test the thread by trying to screw the chuck on it when you near final size - you want a smooth but not stiff action to keep tolerances to a minimum. A sloppy thread will result in bad concentricity of the chuck. Also, your toolbit needs to be razor sharp at the tip. I ended up with this after single-pointing:
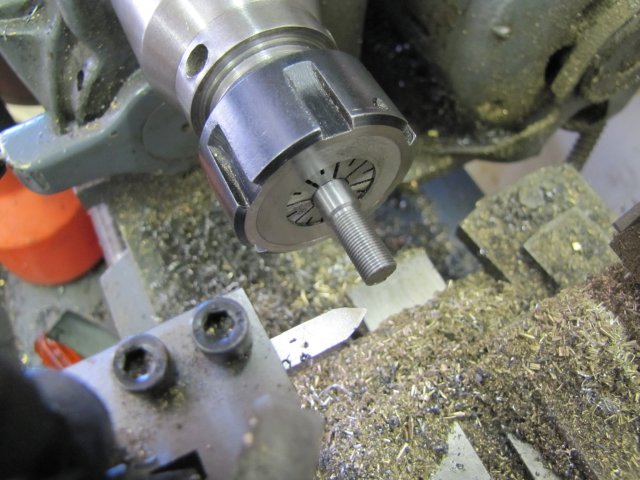
Then lightly face the end of the arbor - it needs to be smooth and square, as the chuck presses its jaws against this face to open and close. As a final step, drill a 4.3mm hole down the center; about 40mm deep is fine; this is to allow drill bits (or whatever you hold in it) some room to get inside. Finally, mill (or file!) some spanner flats to a convenient size on it just beyond the threaded section; it can be very handy to have these.
This is what mine ended up like:
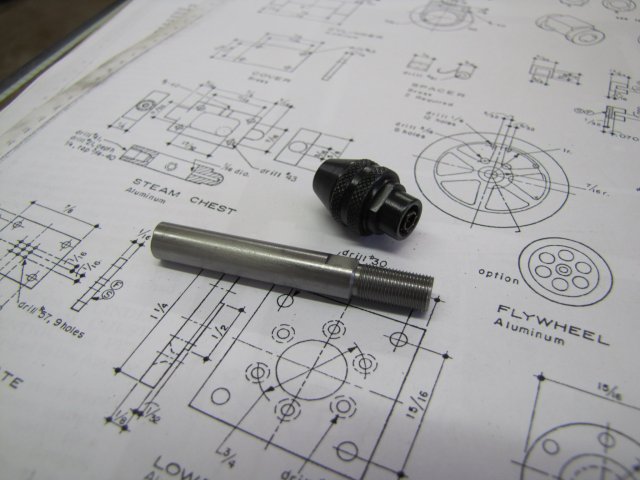
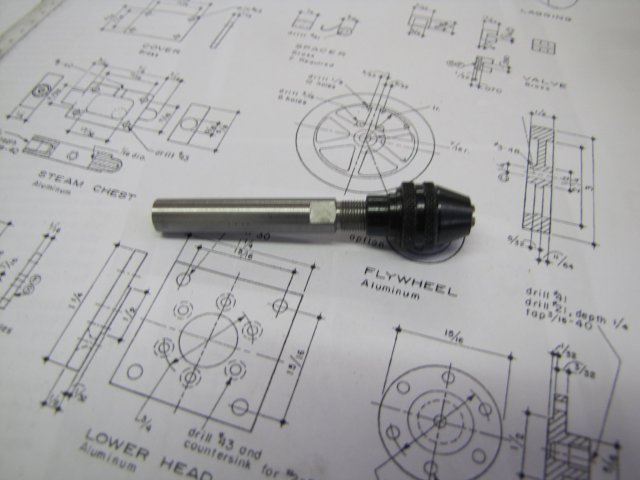
This is probably my most-used home-made bit of tooling; invaluable in the mill (keep the speed up for drilling small holes - and lightly does it!), and I have even used it in the lathe to turn some clock axles down to 0.4mm out of 1mm rod on the lathe. The only regret I have is that I have not yet made one each for a 6mm and 10mm arbor size - as these are the most-used ones on my mill

, Arnold