I saw this idea on one of the Yahoo! groups, or someone's site, or something. Anyway, the idea is
- insert one of the optics in the through-hole,
- peer through the optic and move the thing around until it's right where you want a punch mark,
- hold it firmly in place while you remove the optic and replace it with the punch, and
- give the punch a tap with a hammer.

There are two optics, both
3/
8" acrylic. Each has a flat end and a lens end. One has a crosshair etched in the flat end, and the other has a small circle. Both etches are filled in with Sharpie. The punch is
3/
8" water-hardening drill rod, with one end knurled and a small point turned on the other, hardened and tempered.
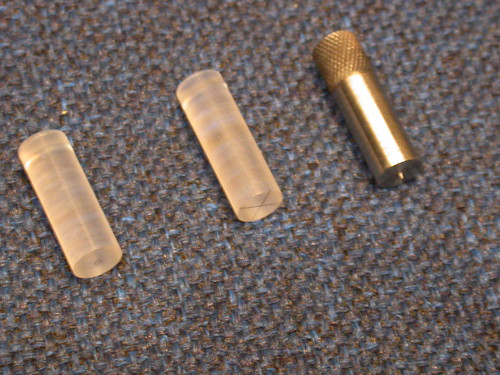
The aluminum body of the punch has one through hole and three not-quite-through holes drilled and reamed to
3/
8", for keeping the pieces.
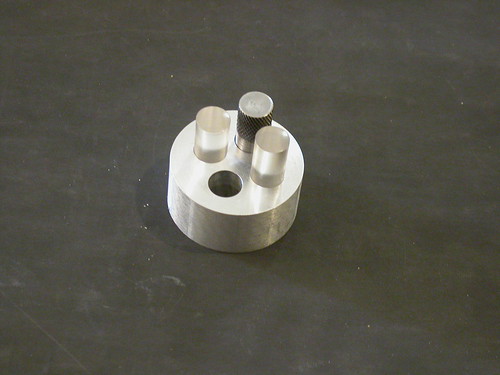
Gluing a piece of non-stick rubber sheet to the bottom would complete it by making it frictionful when positioning.
Making the optics was arguably the most challenging part. I had to calculate the appropriate radius for the lens based on the length of the optic and the refractive index of the material, and then make a tool to cut that curve (since I don't have a radius cutter -- yet):
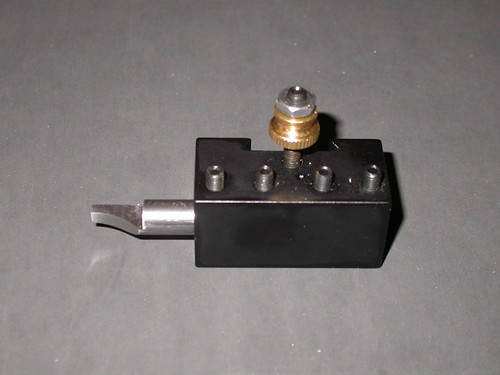
In retrospect, I should have made the cutter from normal square cross-section turning tool stock rather than boring-bar stock, since the latter is a right bugger to get leveled before tightening in the toolholder.
After cutting the lenses, I used #1000 wet/dry sandpaper, followed by #1200 and #2000, and finally Meguiar polish to make both ends nicely transparent. (I also discovered the hard way that you do
not try to polish acrylic at high revs.

)