I ran into some trouble awhile ago,I had this pulley that should fit over a bigger shaft than the original, so I bored and reamed the hole, no problem there, went over to the shaper to make the keyway, so i put it in the vice and SLAM! the pulley bent in the vice!
So to avoid that happening again I'm going to make a simple dividing head and fit a 11" 3 jaw chuck that way I should be able to clamp future pulleys that needs broaching, without the possible danger of bending them!
I apologize for the large pictures.
This is about 62kgs of steel
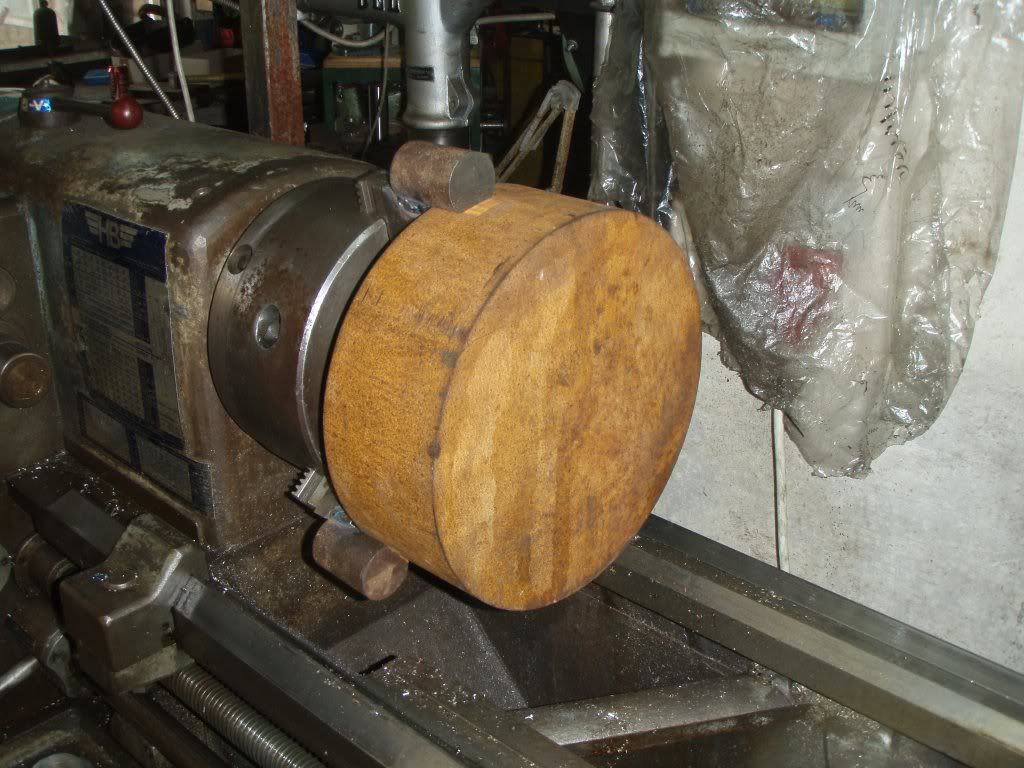
First few cuts at 160rpm 0.15
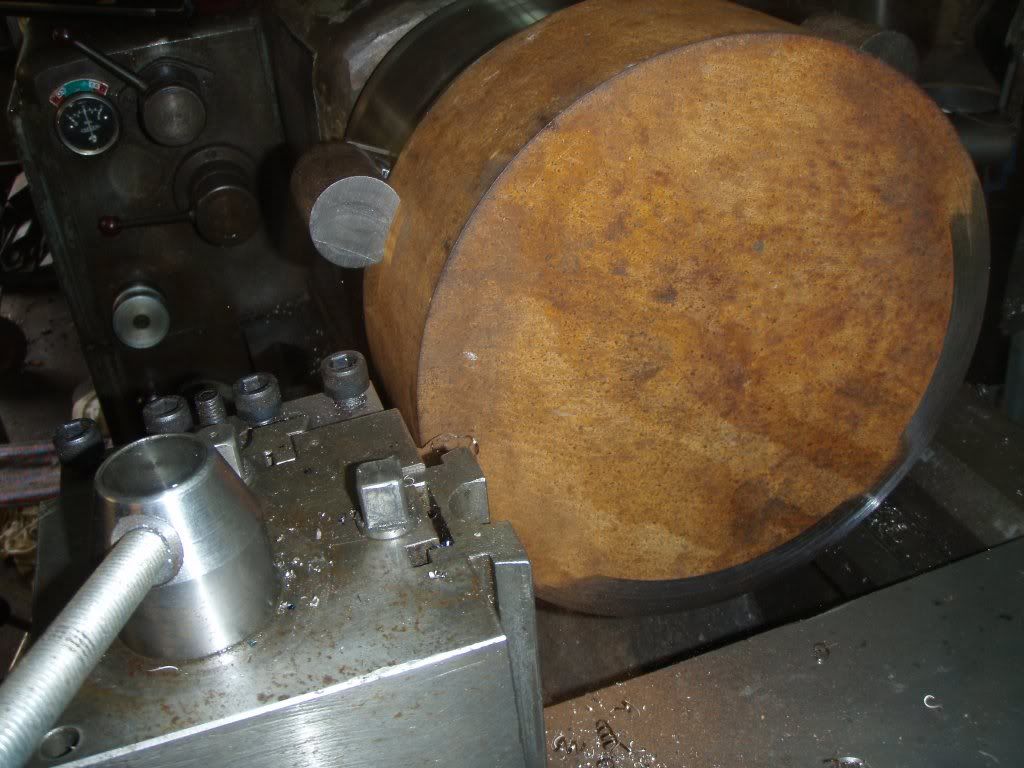
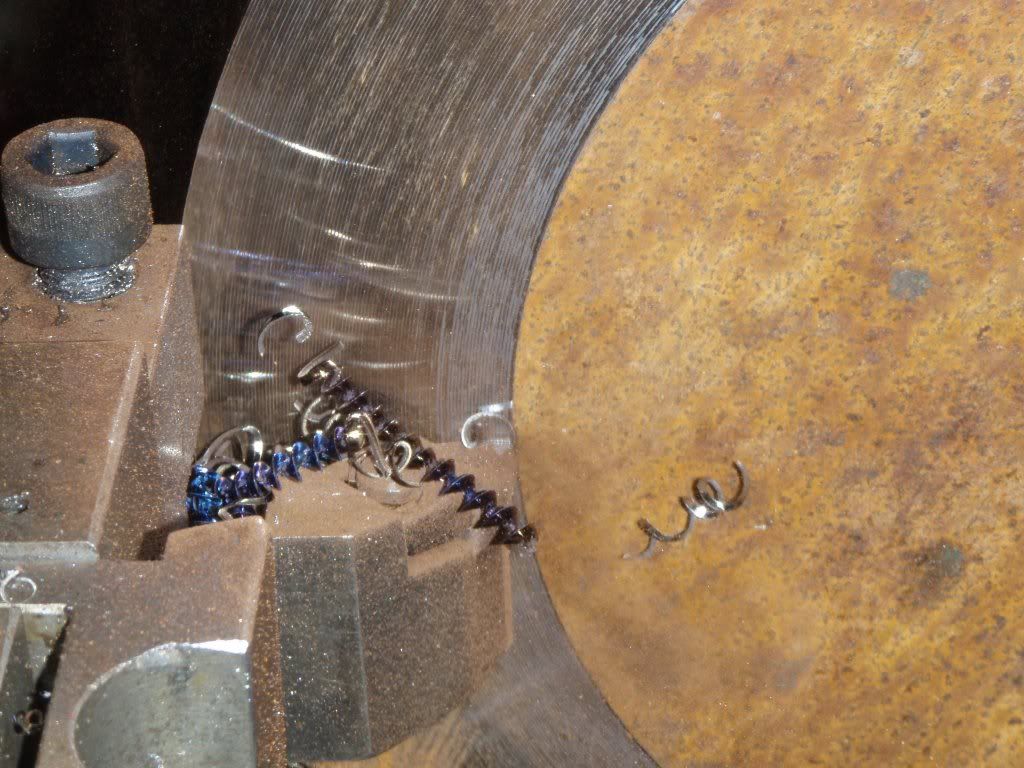
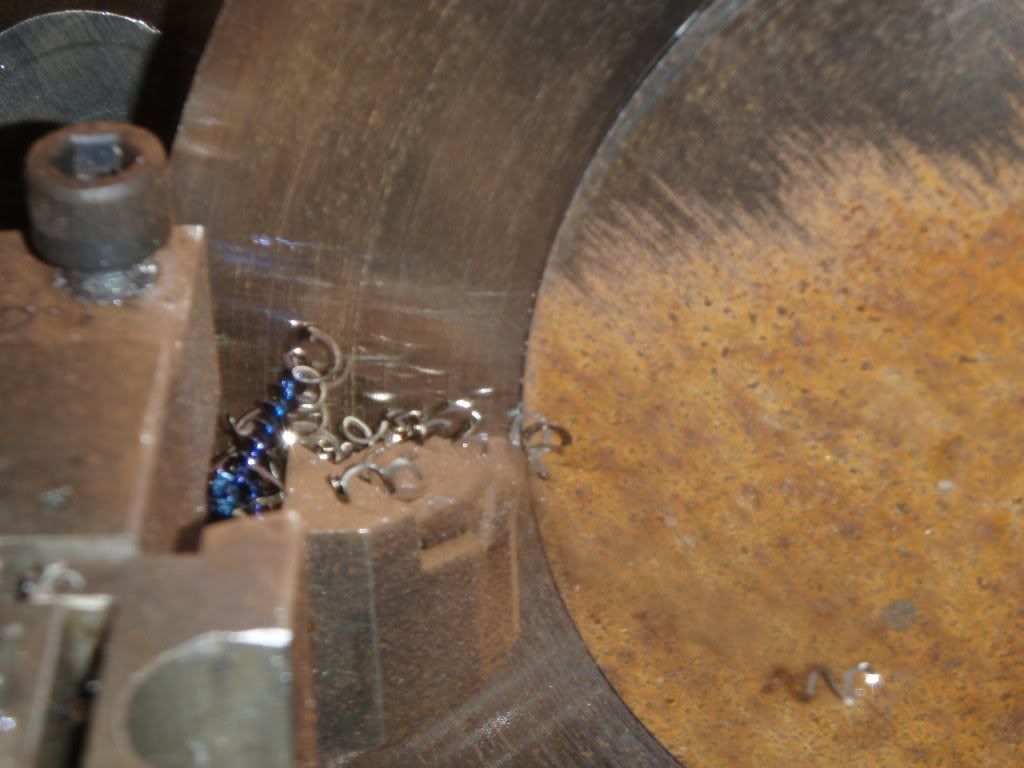
300mm to 140mm (roughing) started from 160rpm 0.03 feed and 5mm diameter(2.5 depth) and ended at about 250rpm same feed and depth.
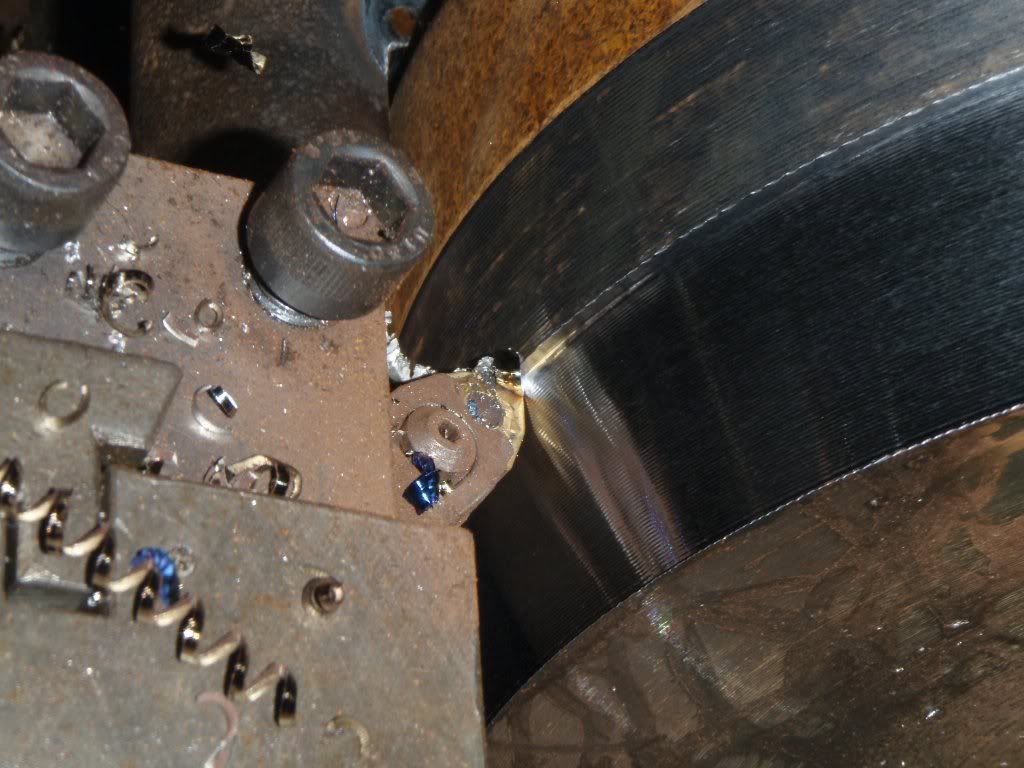
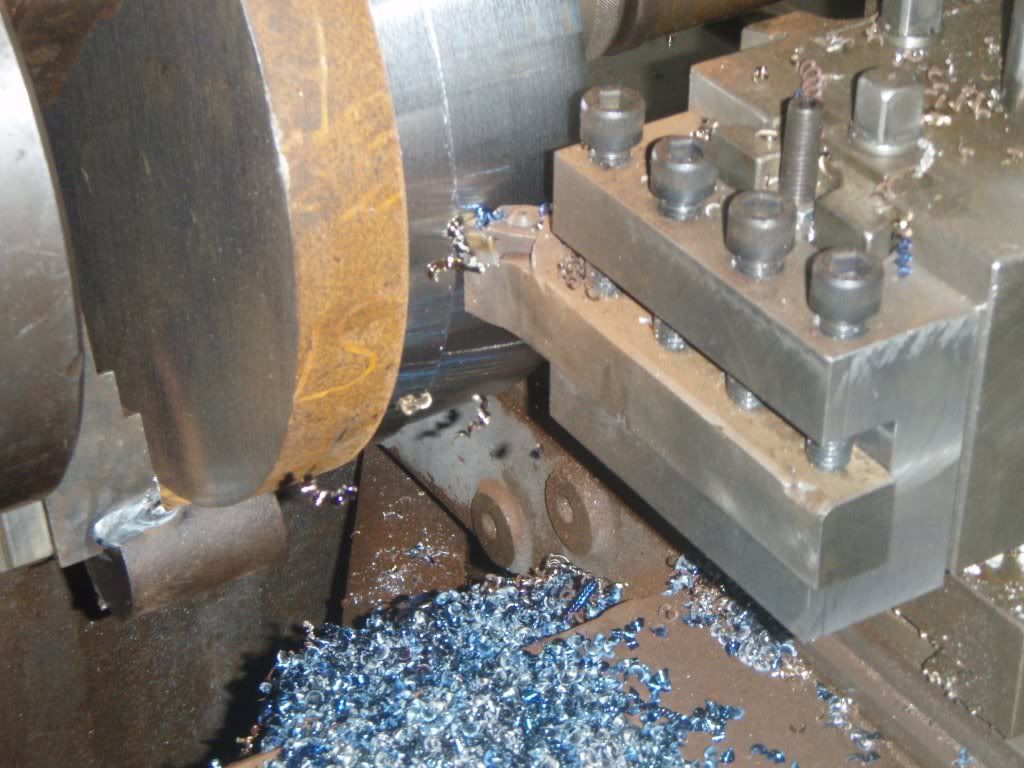
Finished surface (130mm) about 315rpm 0.015feed and 0.5 in depth really nice result.
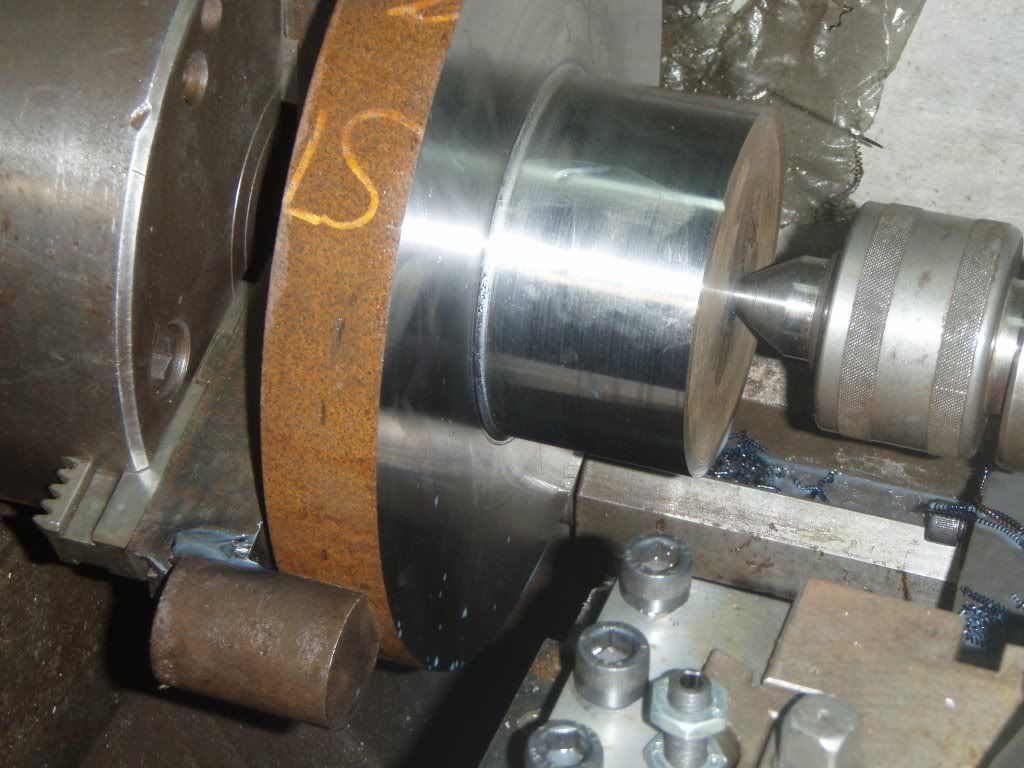
Treaded M130x1
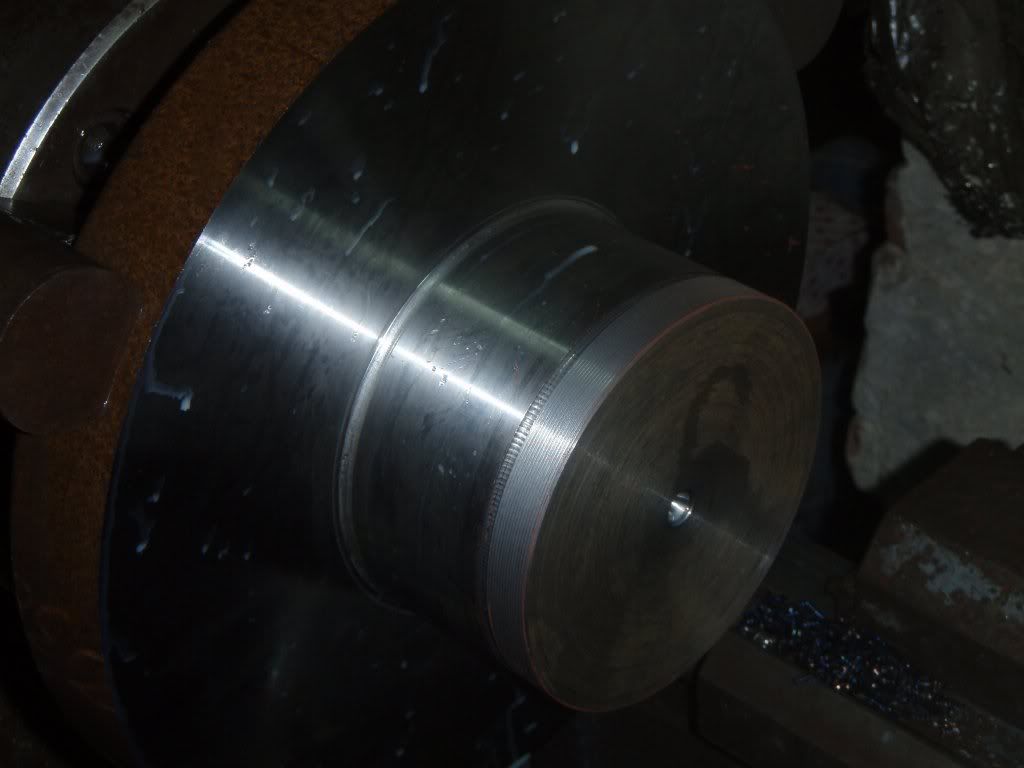
Drilling 50mm hole
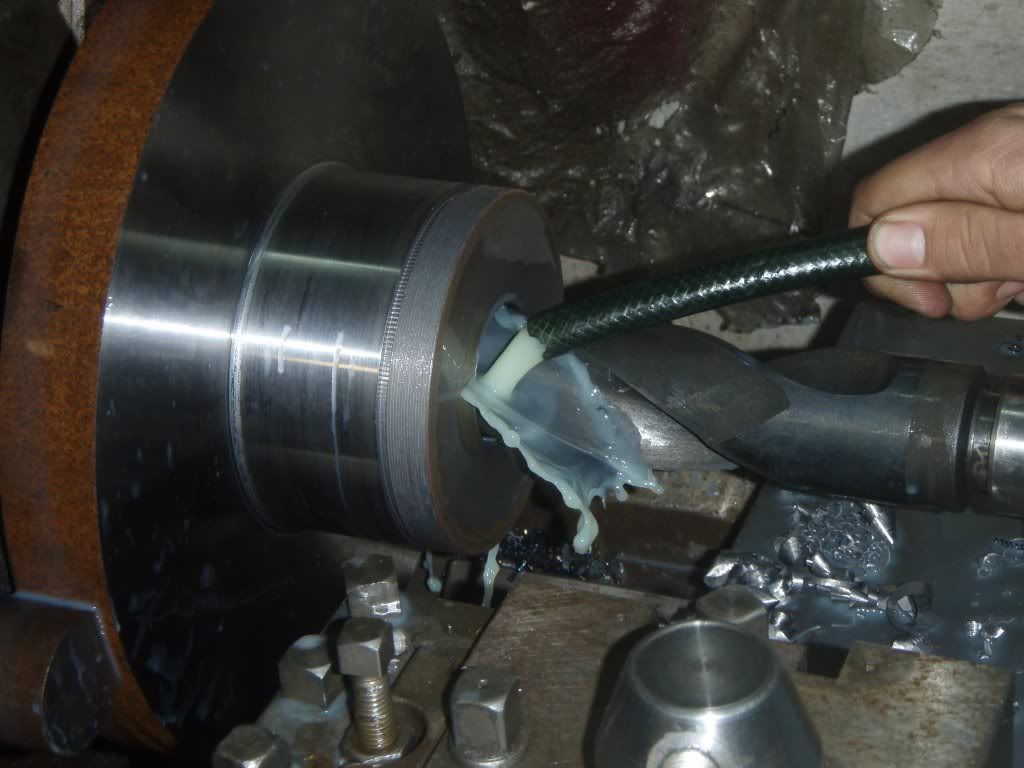
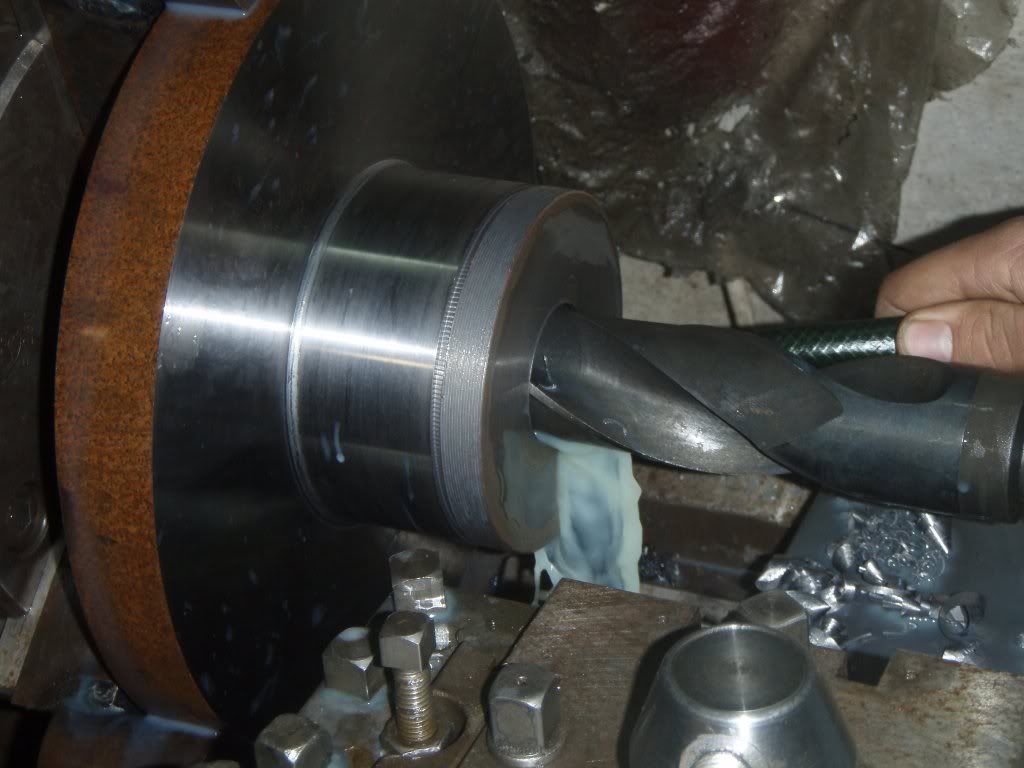
Boring from 50mm to 90mm
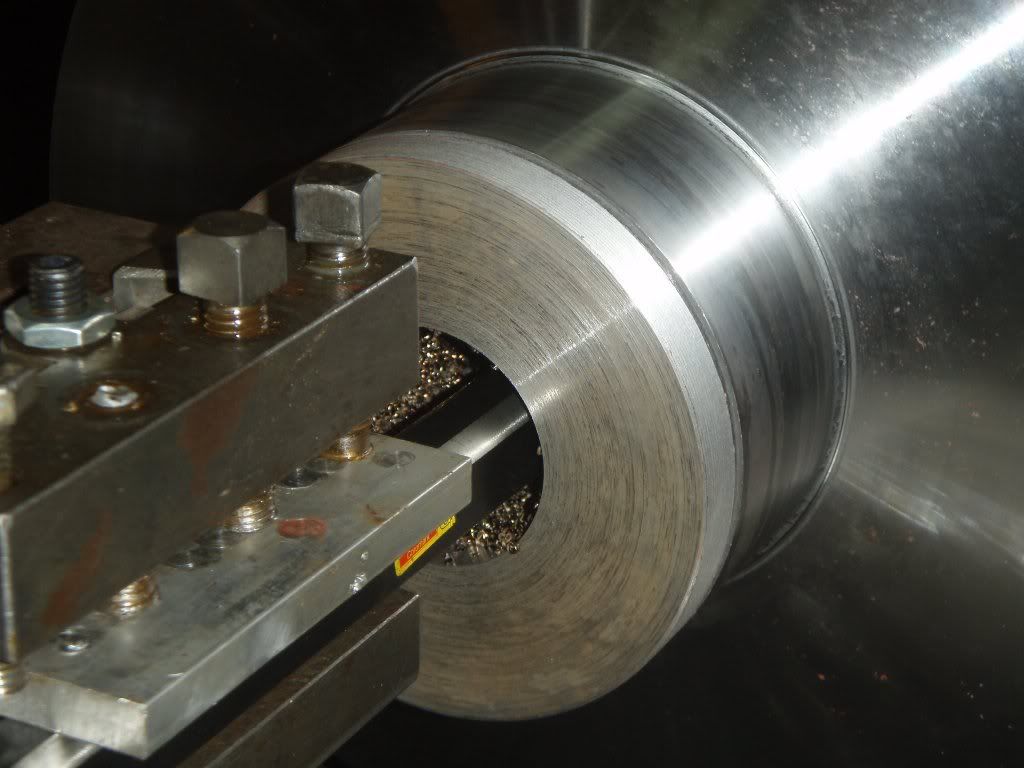
The 11'' chuck
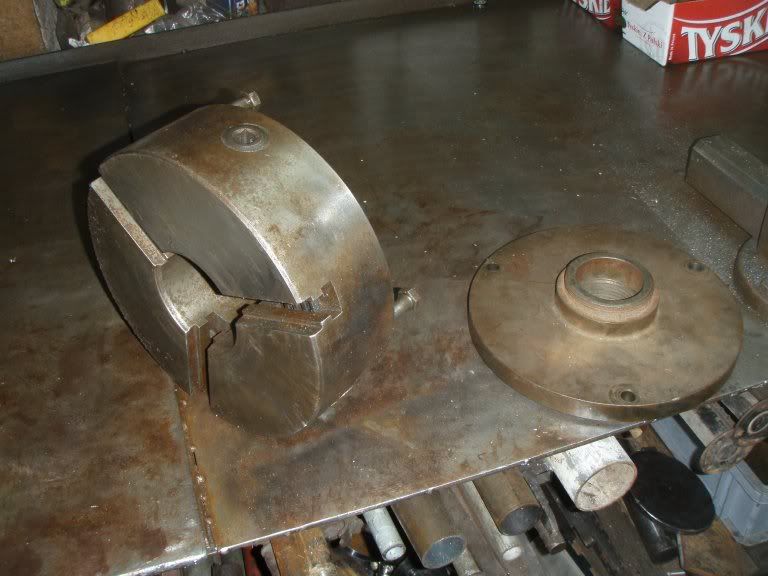