To all my friends and onlookers, sometimes work seems to insist on inserting its self into the day, and interfere with important things like model engineering.
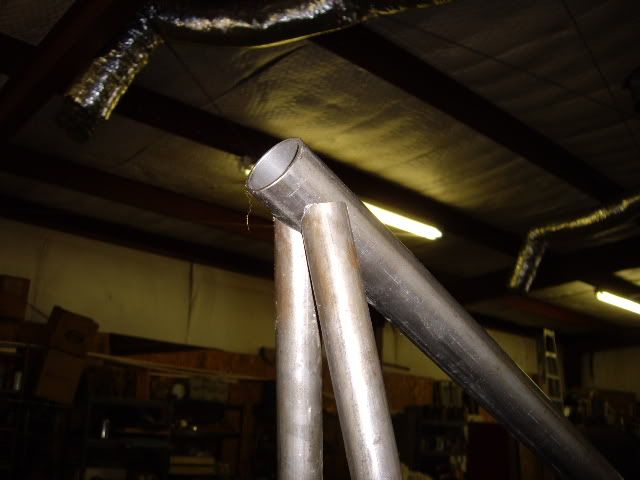
I have this frame I'm making, which needs some machine work to match up the pieces for welding, especially where the backbone meets the front main tubes, so I measured the angle, clamped the main frame tubes to a tilting table, and set up the boring head to bore at the right angle, to the size of the backbone
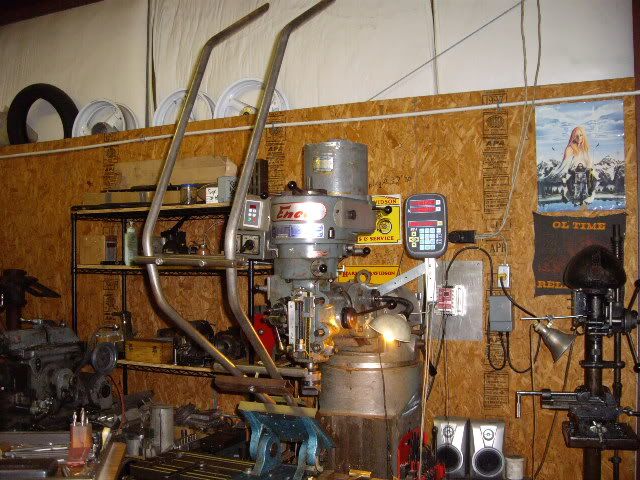
the angle plate setup with the main frame tubes clamped to it
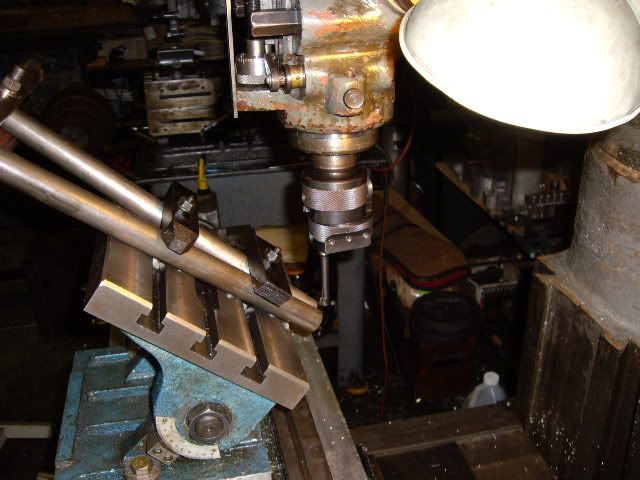
setting up the boring head. guestimating the diameter touching off the cutter at the tube, rotating the boring head 180, and putting a rule between the touch-off point, and the cutter tip
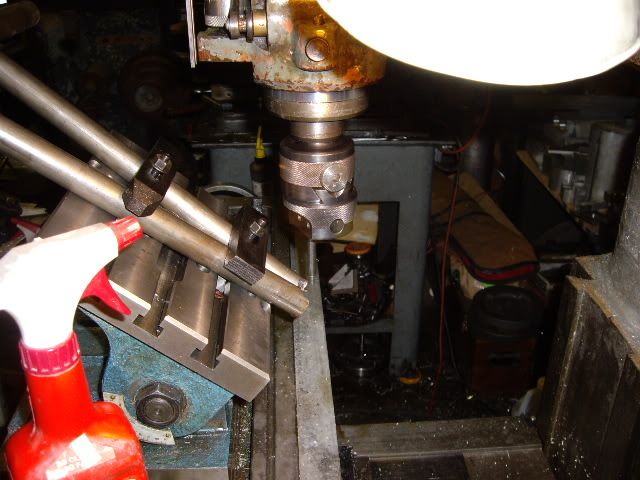
taking the first cuts and adjusting positioning for proper centering
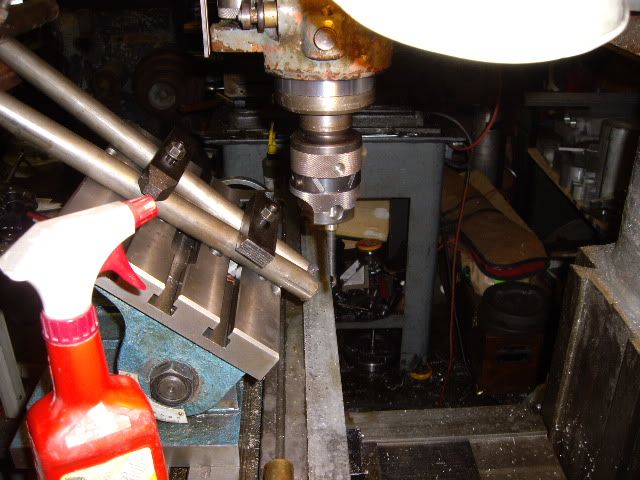
more cuts, everything in good position now.
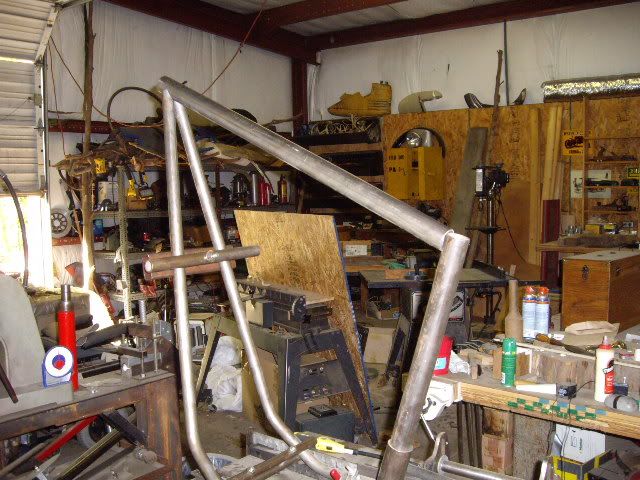
main tubes finished, testing the fit with frame in a jig
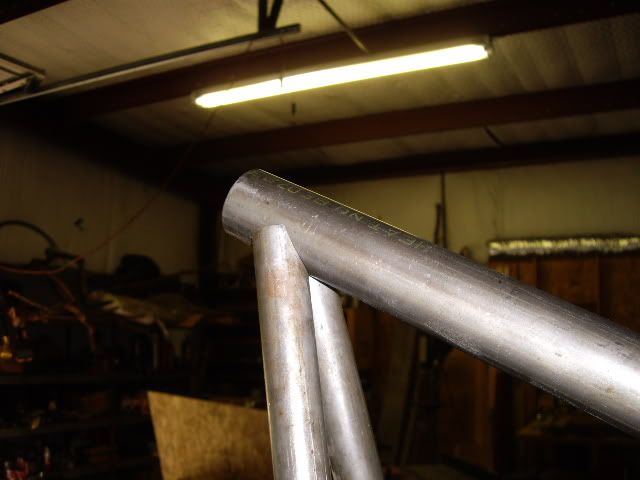
nice tight fit, no unseamly gaps, looks good
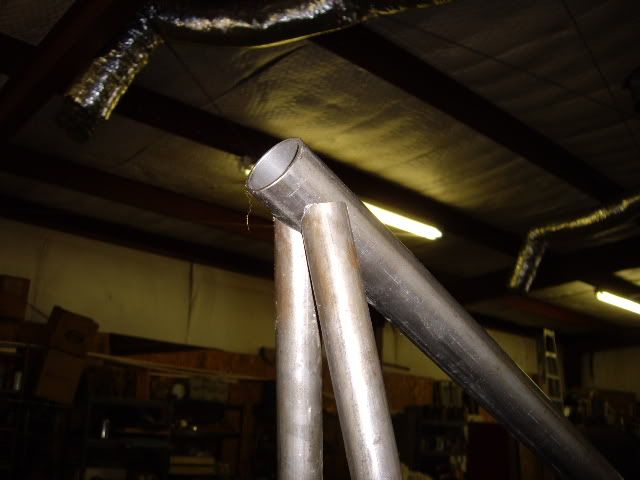
view from the front looks good too.
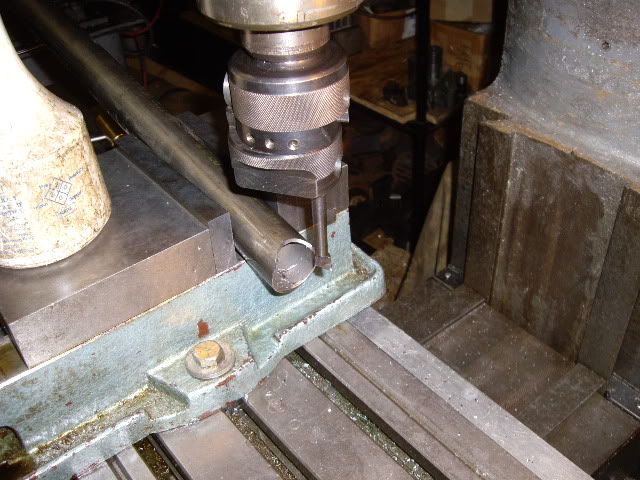
with the backbone in the vise, set at the right angle, preparing to fish-mouth the end to fit closely to the seatpost tube
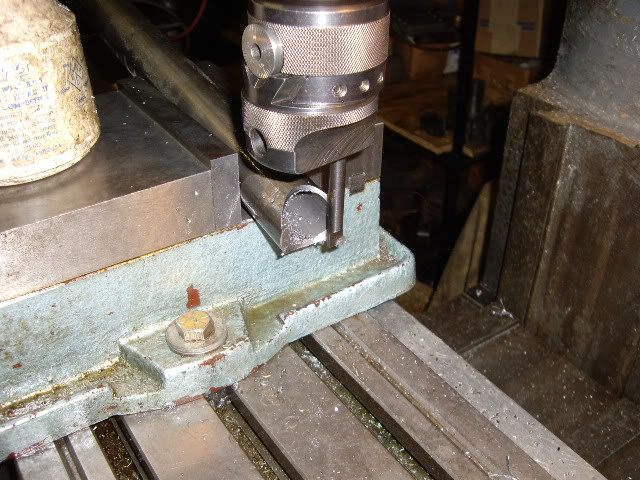
boring done, everything aligned ready to fit on the frame
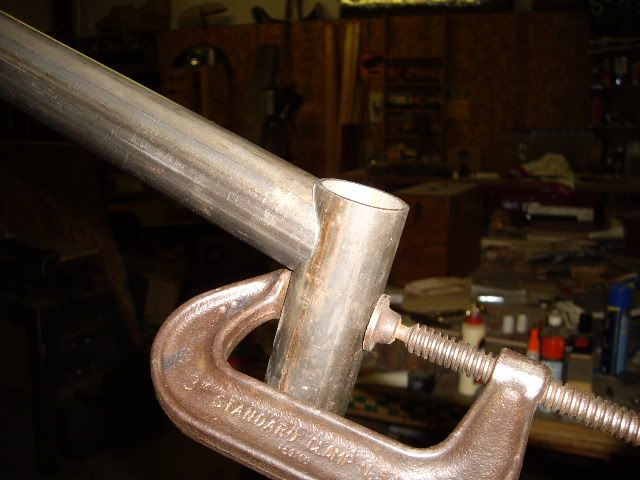
with the just cut end sitting on a C clamp, a perfect fit on the seat post tube
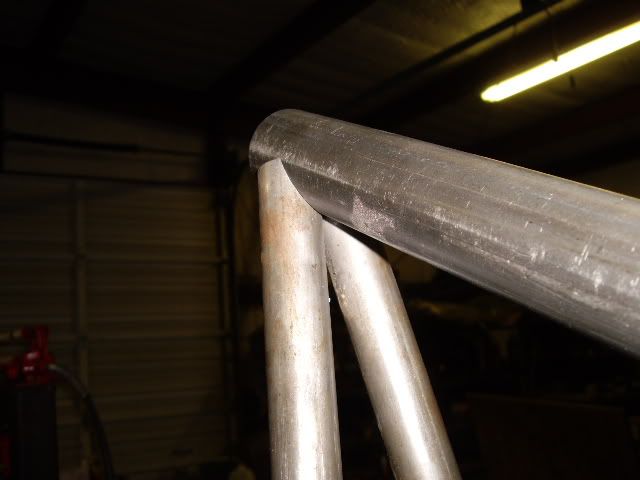
checking to ensure the fit is still good with main frame tubes, after second operation, everything is just right. Now, back to the important things.
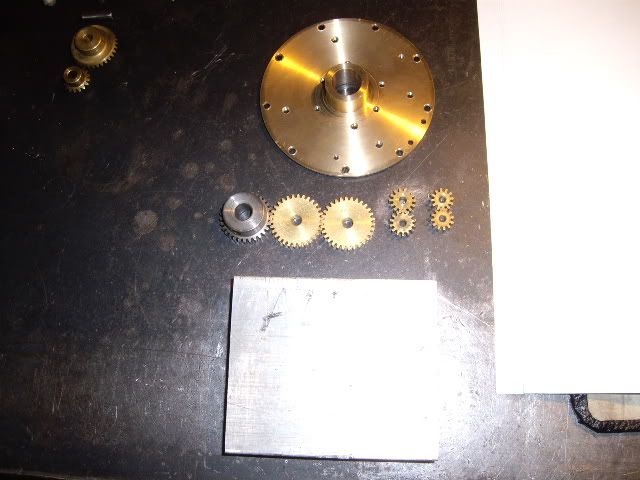
the parts for the oil pump, steel drive gear, two brass driven gears, and two pair of smaller gears to pump the oil in, and then collect it and pump it back out. The plans call for the aluminum blank to be turned round, the machine work done, and then the pump cut out to its proper shape when all the details have been machined. I didn't want to waste a perfectly good piece of stock so the piece I'm using will be less than round, but have all the area where details are machined in, just pretend its round when you see it in the chuck and later in the mill vise.

the blank, mostly octagonal
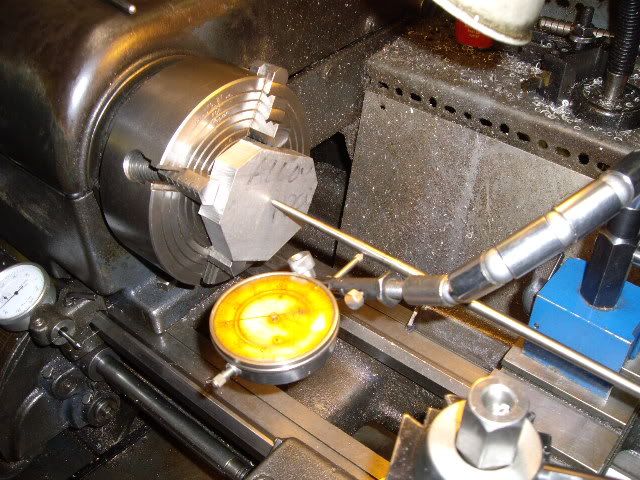
centering the blank with a rod and an indicator
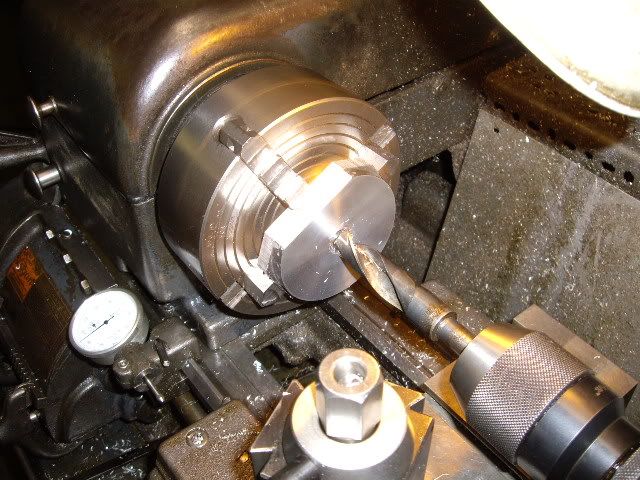
first side faced and turned down to 3.374, drilling before boring to a tight fit on the main bearing
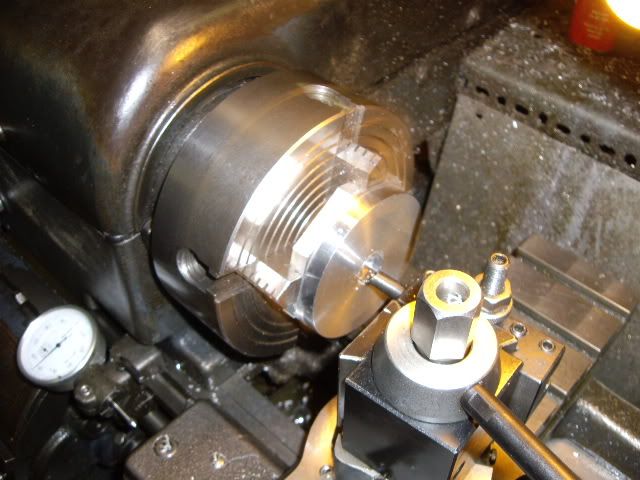
first cuts boring to fit the main bearing
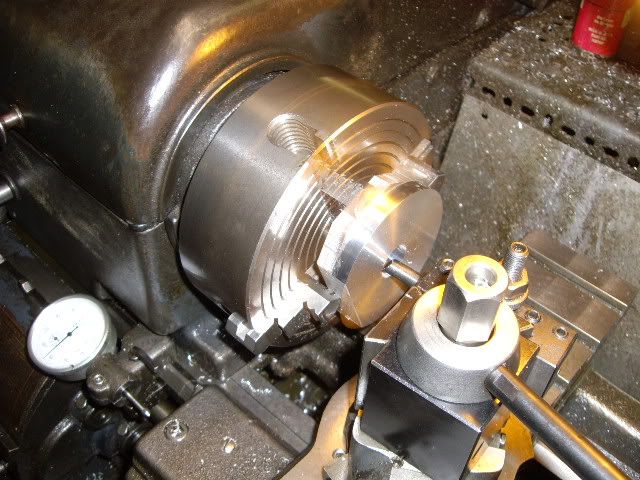
more boring
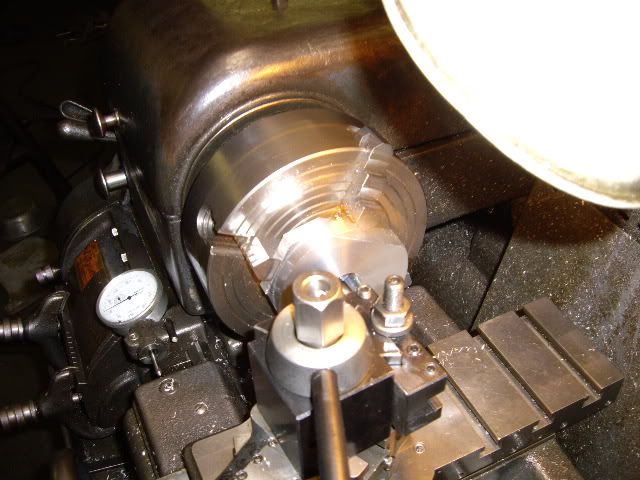
final cut, blank flipped and centered, o.d. turned to match first side at 3.374
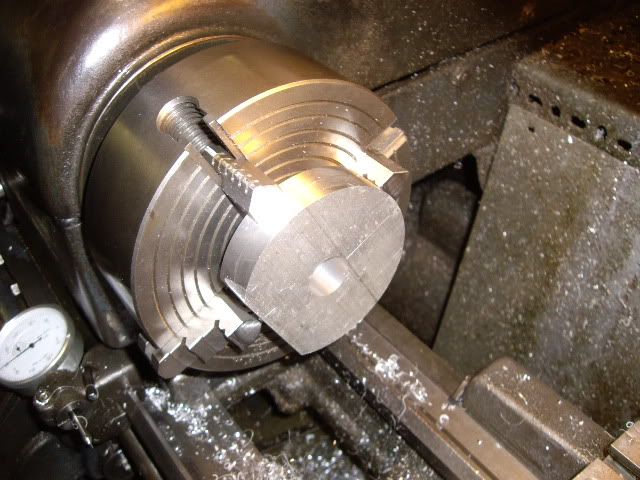
second side, ready to be faced down to final thickness of .468
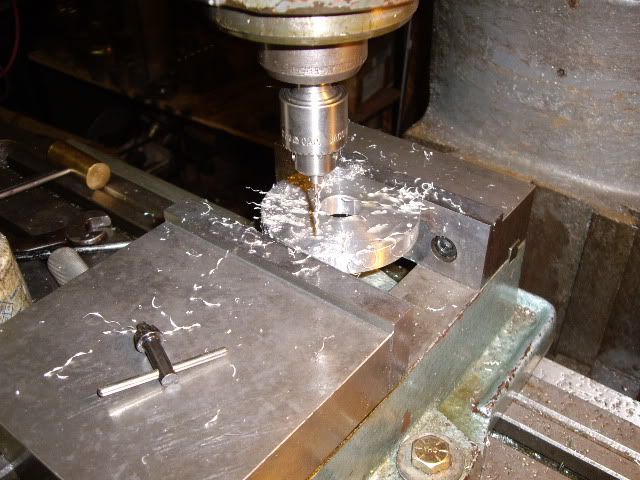
blank set up in the mill vise with parallels which are removed, for drilling and tapping mounting holes for the rear main bearing
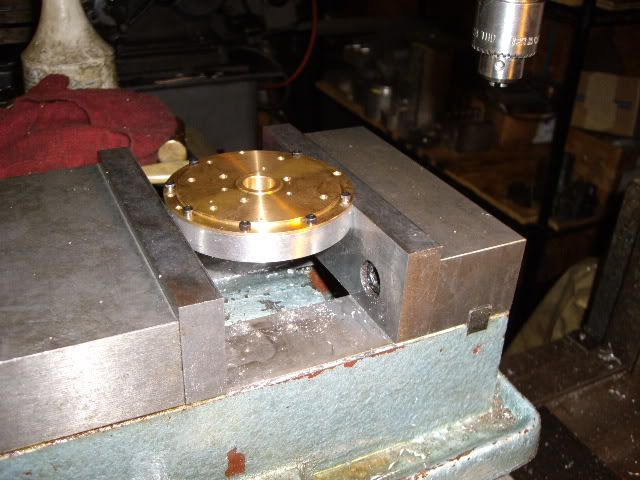
rear main bearing bolted in place for line drilling and reaming oil pump shaft holes through bearing and pump body
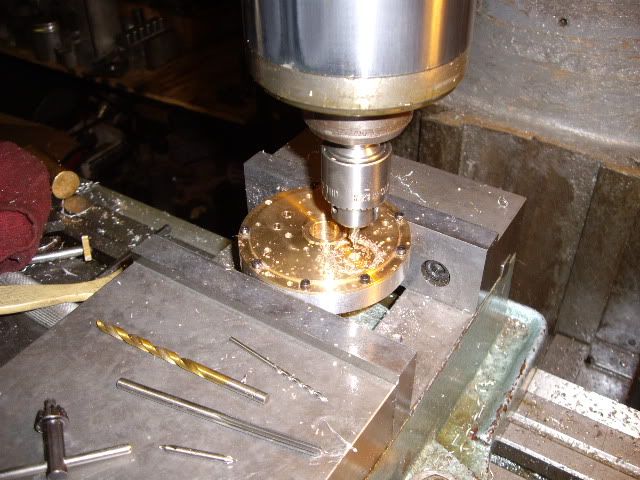
each of four holes is center drilled, drilled and reamed to ensure accuracy
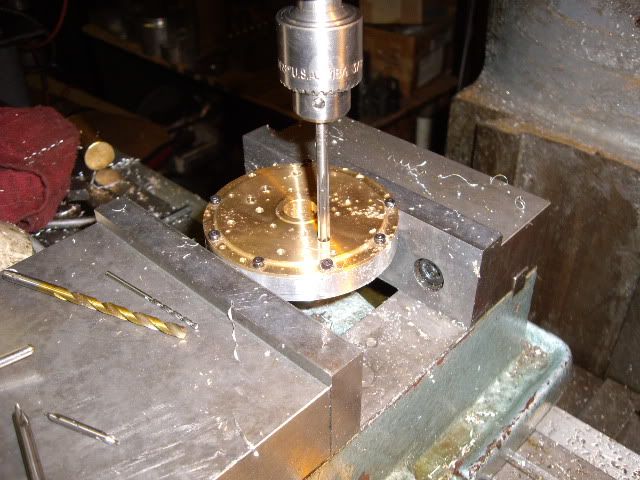
reaming through the main bearing and the pump body to ensure alignment
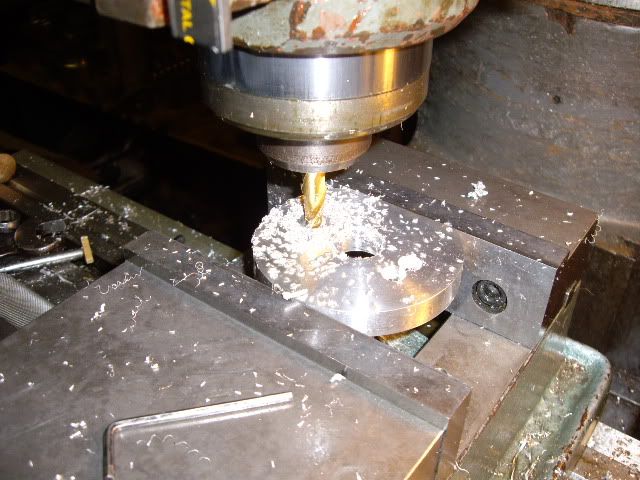
pre-boring one of the gear cavities with an end mill
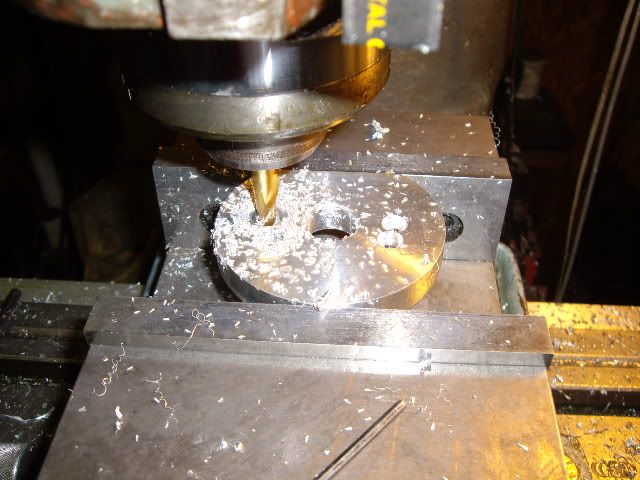
another cavity pre-bored. final fit will be half a thousandth over the gear size
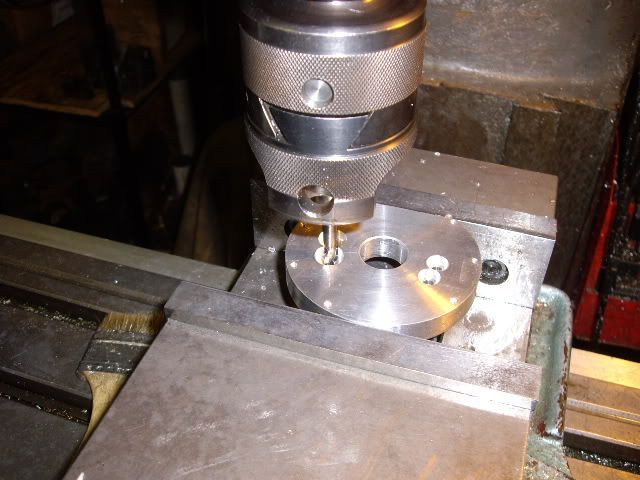
finish boring the scavenge pump gear cavity
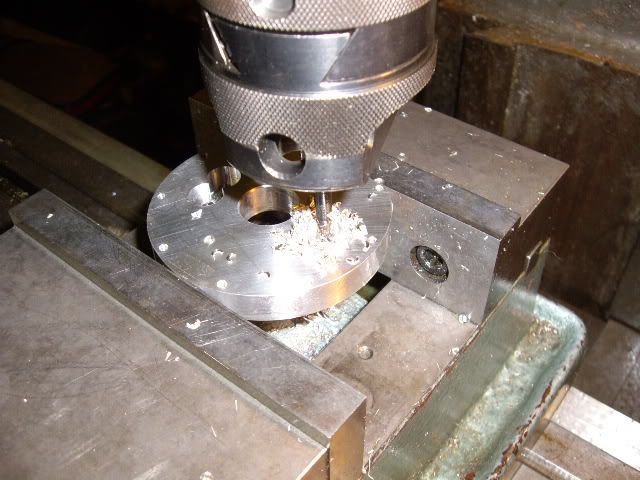
finish boring one of the pressure pump gear cavities
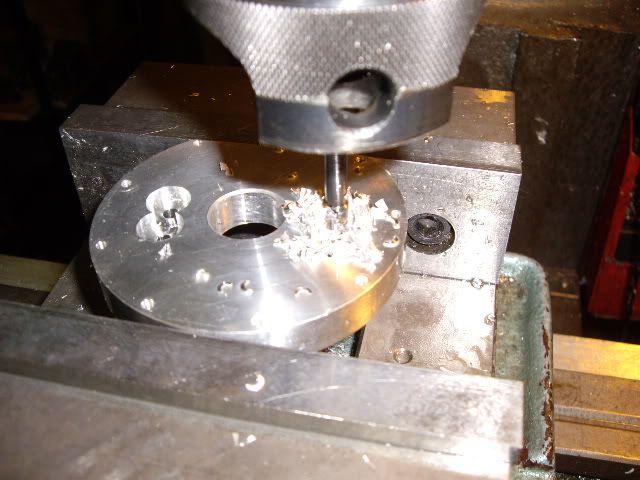
finish boring the second pressure pump gear cavity
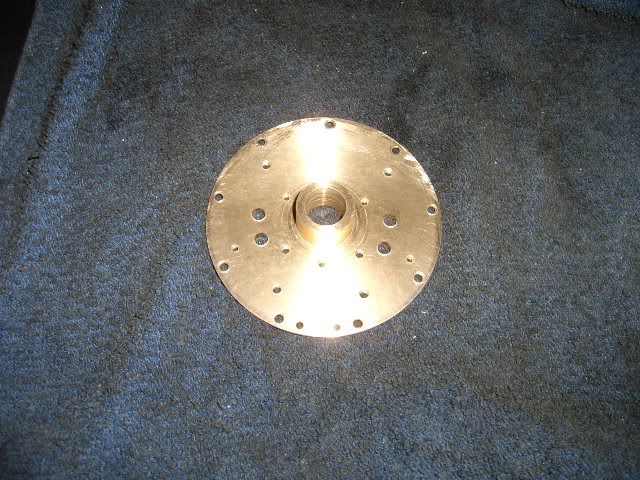
rear main bearing with all the oil pump shaft holes line reamed in place. what is left is drilling the pump body for its passages, cutting it to profile, drilling the crankcase with the main bearing and pump in place to fit the pump to the crankcase and ensure free movement of the oil.