Thank you everyone, for the warm welcome!
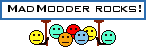
Bernd, I have resized the photos, and adjusted white balance and brightness with Nikon Capture 4 software. The photos were taken with a Nikon D200 digital SLR with a 60mm Macro lens on a tripod.
Twinsquirl, all of the photos are using fluorescent light. I either calibrate the white balance with a 15% gray card, or adjust it later with the Nikon software.
Darren, It's funny that you should ask "electricity?" I power my Lathe and Mill both with solar power. I also use solar for the fluorescent lights. The only thing I run on the mains is the DRO, connected to a small computer uninterruptible power supply. I don't trust the DRO to my little 200 watt square wave inverter. That, and it is a real pain to lose the DRO setting when the power drops out in the middle of a machining operation that I spent a half hour indicating in. (Yeh, I know that's slow, but I'm getting faster.) I have two 50 watt solar panels each independently feeding a car battery through a charge controler. Then I use a little inverter to power the machine tools and lights. Just to give you an idea of the massive power my mill uses, if I stall it, it instantly blows the 10A fuse on the 12V leads to the inverter! Here is a photo of my "power station." If you noticed the vertical white power strip in one of the earlier photos, that is the one coming from the inverter.

I'm not trying to single handedly save the planet by running my stuff from the solar power system. It's more like, I have the solar power system, I should use it for something!
Anyway, back to my little project. Today, I will be using my "micro" lathe:

(Notice the Mill stored in the background.) How many of you store your Lathe on a shelf?

If you look closely at the next photo you can see the misalighnment of the threaded part.

So, In order to remove it, I machine some flats for a wrench:

I am aware that because the part is not threaded into the base perfectly straight, the bottom of the flats won't be perfectly straight. But, it is not critical, and I doubt the error could be seen by eye. The flats after all are just for a wrench.

I should have cut flats to begin with, but sometimes we all get impatient
Here is another photo ilustrating the problem:

First off, I have carefully indicated the Z axis of the mill by using the flat surfaces of the base near the dove tail for the Y axis. That seemed to give me a much more repeatable and consistent indecation with the DTI. The table isn't very wide and I was having trouble with the slots, so I moved it all the way back on the Y axis and used the surfaces on the base.
Anyway, what I decided to do, using an idea I got from Bogstandard, is to loosen the threads a little, allowing for enough wobble to allow the part to seat against the base. I figure the best way to do this is with a speed wrench on the end of the tap, with a slight pressure in the corrective direction while threading the tap in and out.

Well, that seems to have done the trick, but I ran into another small problem. When I thread the end that is suppost to face up in, the part seats into the base perfectly. But, when I thread the end that is suppost to face down, it has some resistance just before seating. So, I took a closer look at the threads:

Sure enough, there is a nice bur sticking out. My plan was to cut a relief at the base of the threads, so that this wouldn't happen. I had cut the threads with a die, then flipped the die over to complete the threads. I obviously miscalculated how much to relieve the part at the base of the thread. So, I chucked the part back into the lathe with a 4 jaw chuck, indicated it in, and cut the bur off.

A test fit, while still chucked into the lathe, confermed that fixed the problem.

Then part seats straight, with no resistance just before seating. So, my mount is a little straighter, and I learned a little about how I might do this next time. I guess the easy way to relieve the threads at the base would have been after, not before threading it, while it is still in the lathe chuck.
Anyway here is it is after the "adjustments."

I'm thinking the next thing that I need to fabricate is a device to keep the tap aligned while threading in the mill. When I cut the threads, I drilled the appropriate size hole with the mill. Then used the mill to start the tap and after it is in a few threads, I release the tap from the mill chuck and finish by hand. When I discovered that the threaded hole was misaligned, I checked the mill and improved the alignment of the Z axis. But, I think part of the error was from finishing the threads by hand. I've seen some good ideas here at Madmodders, for tap guides to use with a mill. I just have to decide what I want to make.
Russ