Last week I made a prototype repair part for a broken auto door latch torque rod on a vehicle at work. It worked so well the parts mgr. said he can sell some to other dealers and asked me to make up some more. The proto took several hours of head scratchin' and chip making to complete so I decided to make a form tool to speed things up a bit.
I had previously drawn the part in CAD so I copied the "knob" profile onto the end of a 3/8" wide rectangle to simulate the toolbit and printed it on the laser printer. I glued that to top of the 3/8" HSS blank with superglue, set the table on the HF grinder to 10 degrees and ground the profile carefully using a magnifying visor so I could see it well enough to get it right on the line. A little honing with a stone and I called it good.
I chucked the stock with just enough sticking out to clear the toolholder, clamped the tool as short as possible, squirted oil all over everything and slowly cranked the tool in. No chatter, just shiny, curly chips rolling off until it was down to the finished size. Ya could'a heard me cackle for city block!
You experienced guys probably knew this already but I thought I'd post it anyway in case there are others out there that (like me) were hesitant to make a form tool for fear of the chatter demons. My lathe is a an 8x16 Taiwan made EMCO Compact 8 clone from the middle 80's. I have my QCTP mounted directly onto the cross-slide and don't use the compound unless I absolutely have to. That gives me a bit more rigidity.
Anyhoo, don't fear form tools!
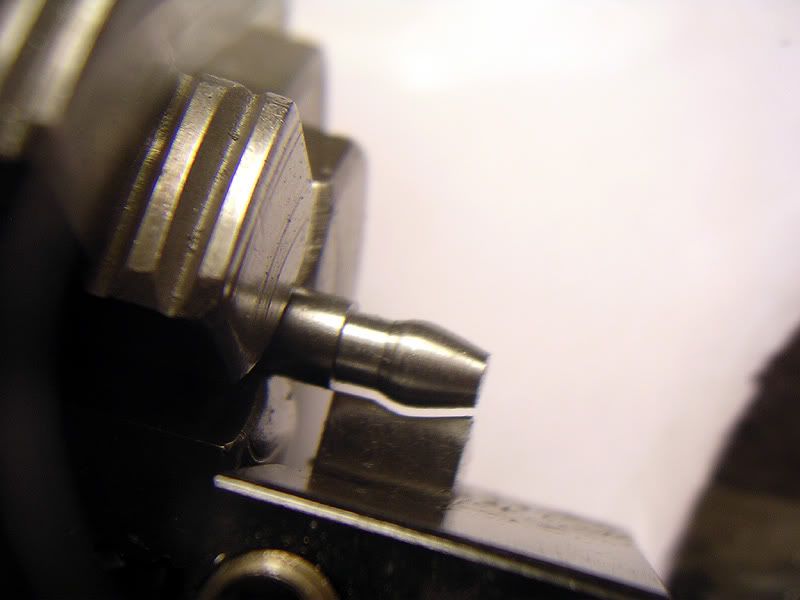
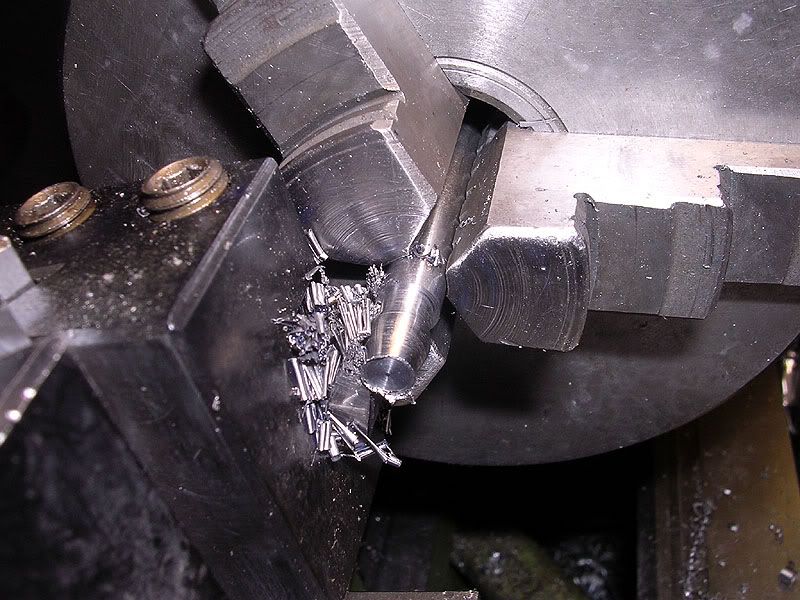
Here's the repaired part alongside a good one.
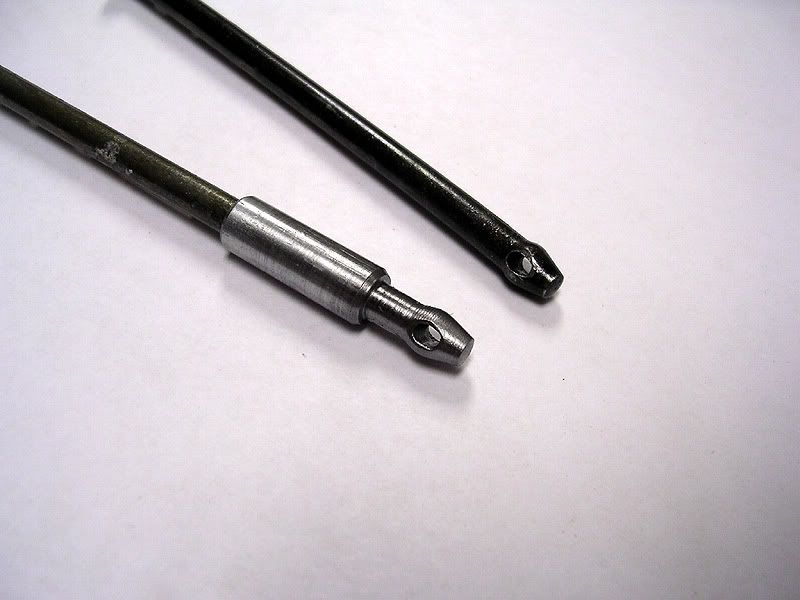