Over 120 days since last post..... And then some!
Apologies for my huge absence from general forum life.... I've been a little preoccupied building my house and fixing my car.... Both almost qualify for full time job status!

I've managed a few hours in the workshop here and there but have failed to post the pic's, call it lazy if you wish
So. I've decided to resurrect this thread with some piccies I've been hoarding and a few that were just last week....
A small descriptive line will accompany most pictures but since they speak a thousand words I'll mostly be shutting up now and post them!

Right, last picture was of the column being test fitted to the cylinder.
This is the picture that I omitted at the time due to a wait to see if it works first way of thinking....
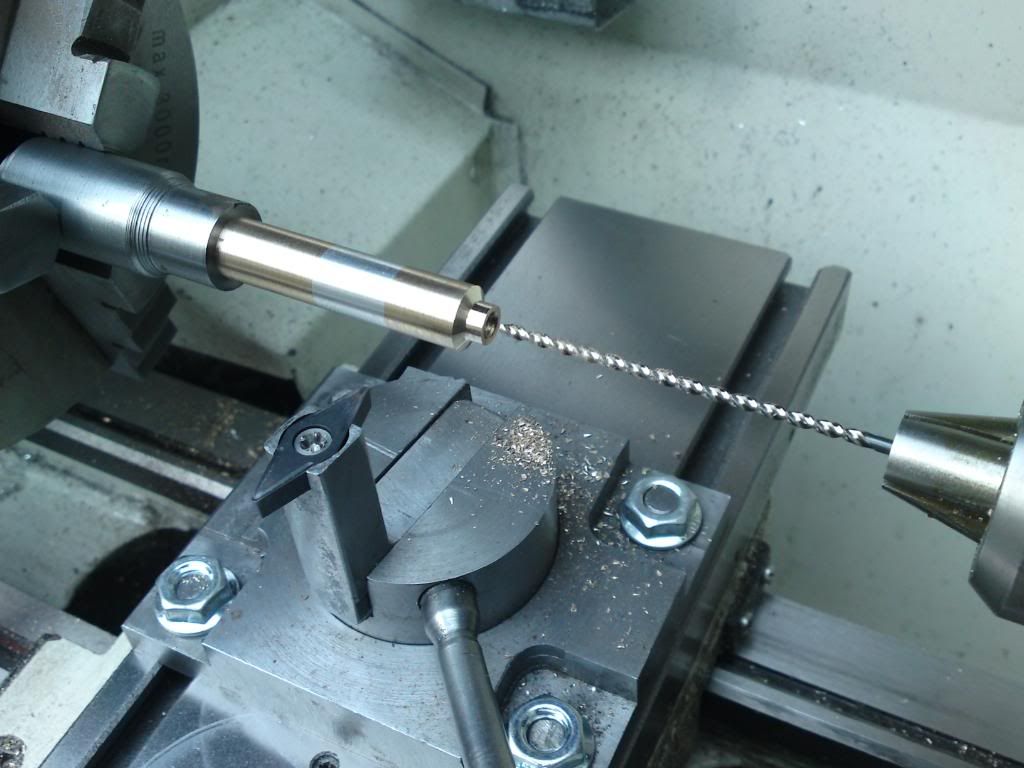
I've drilled right up through the column, reason to become clear very soon...
A little bit of pipe bending...
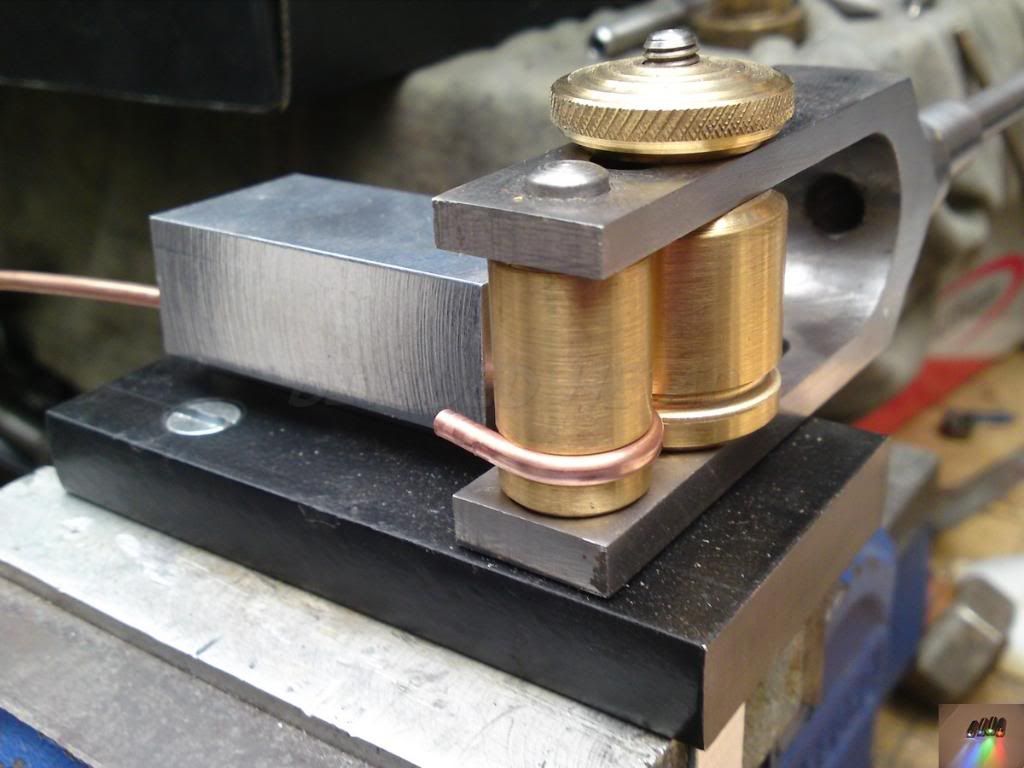
And you have the makings of an steam/air feed

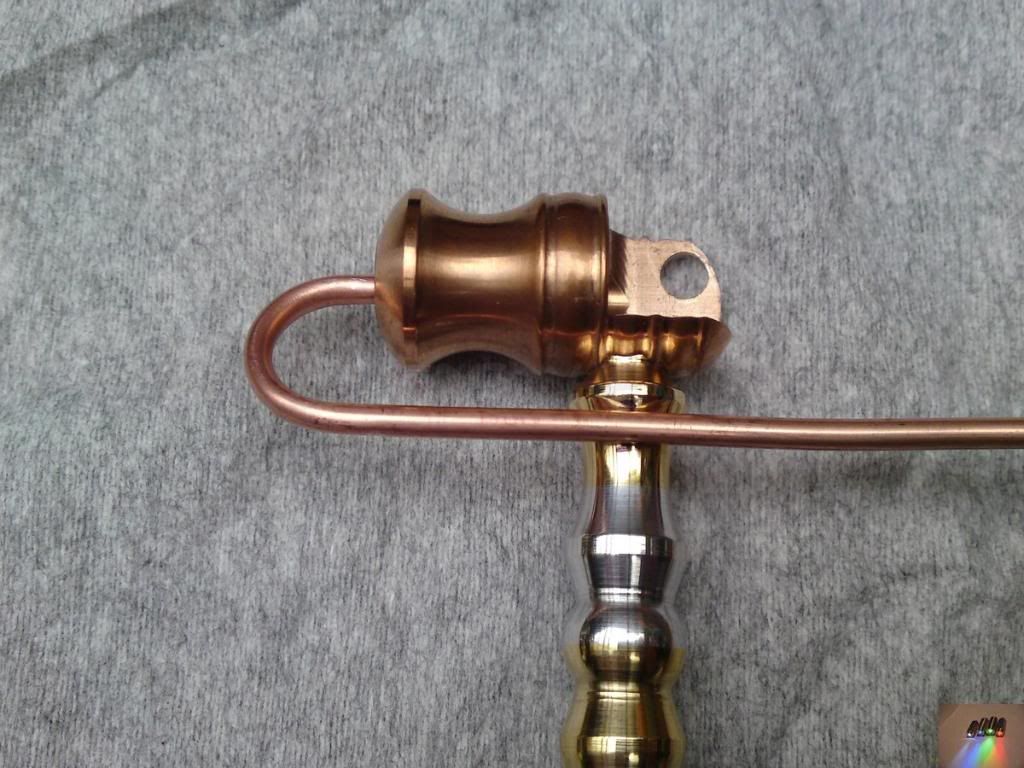
Then a bit to make a smooth transition from the pipe into the 6mm hole in the cylinder end.
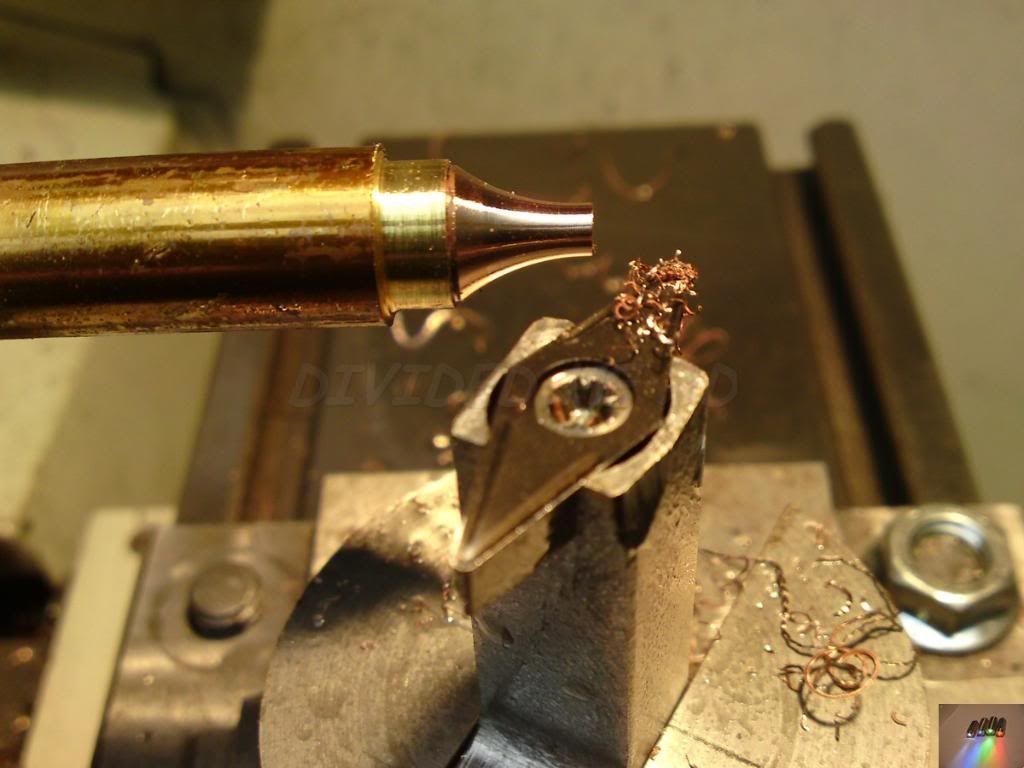
Skipping a few pic's of soldering (Pipe not soldered yet) we end up with this...
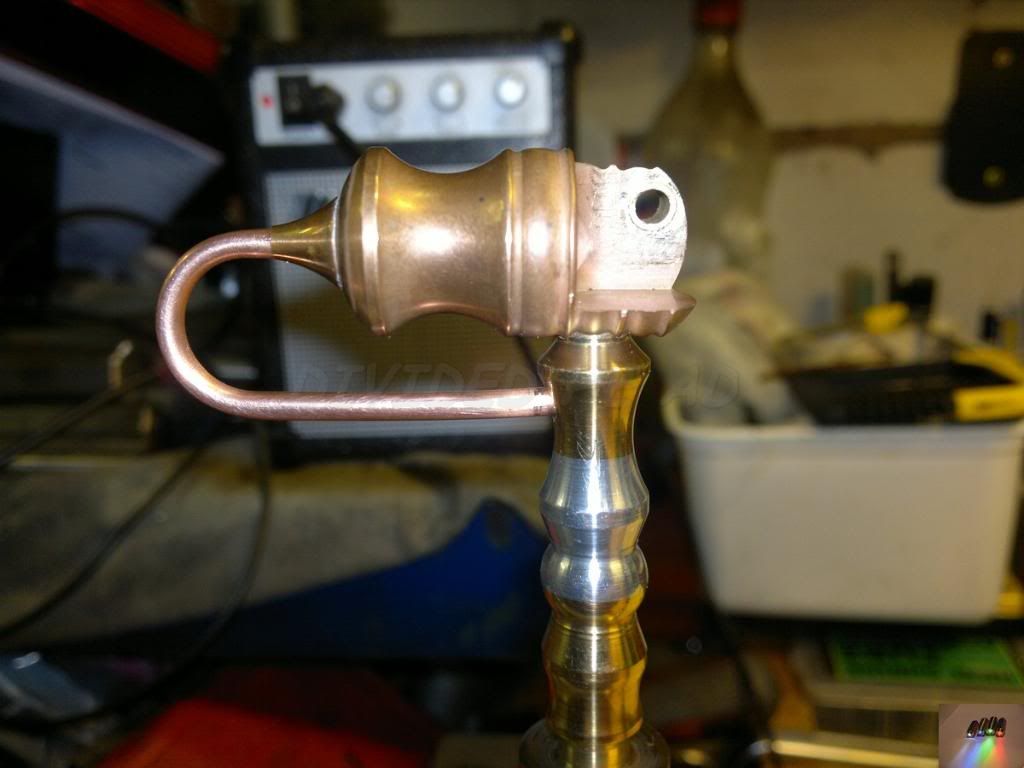
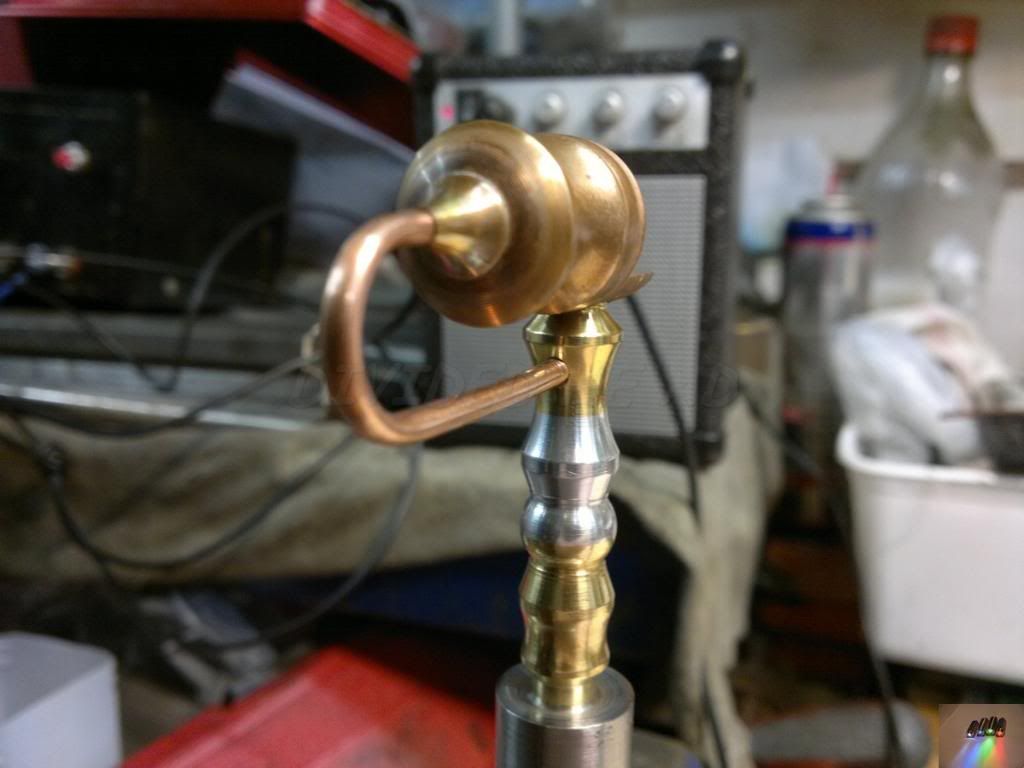
Now that's where the body parts stopped and the moving parts began....
The piston. Take one part stainless steel and one part brass and silver solder together...
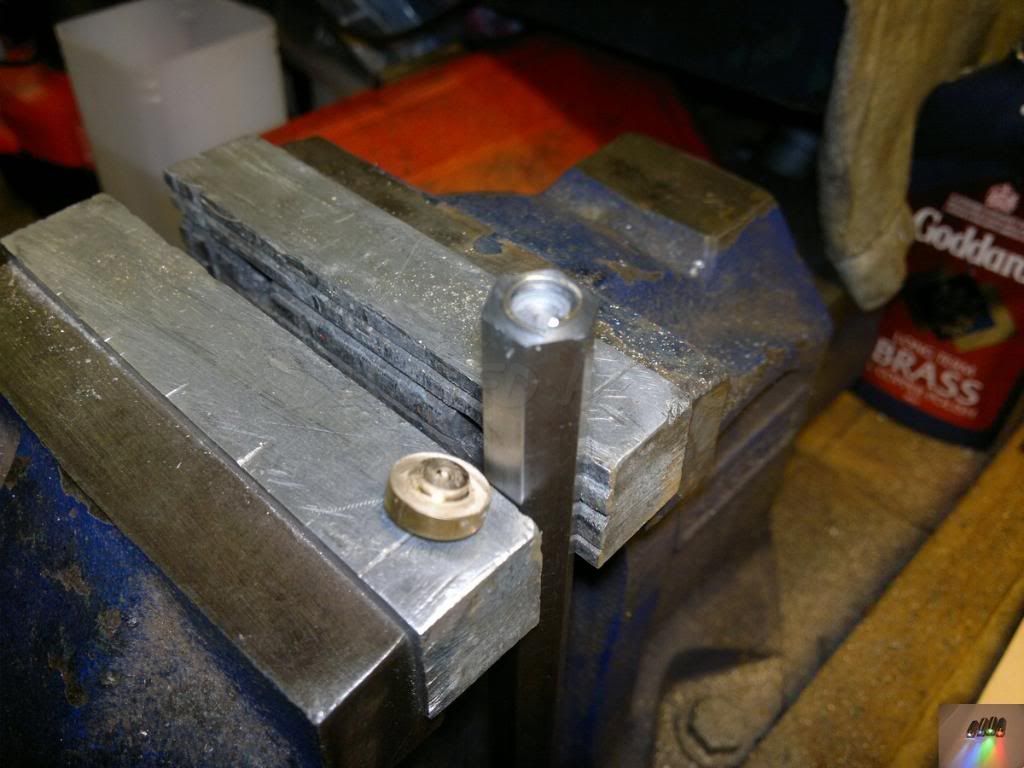
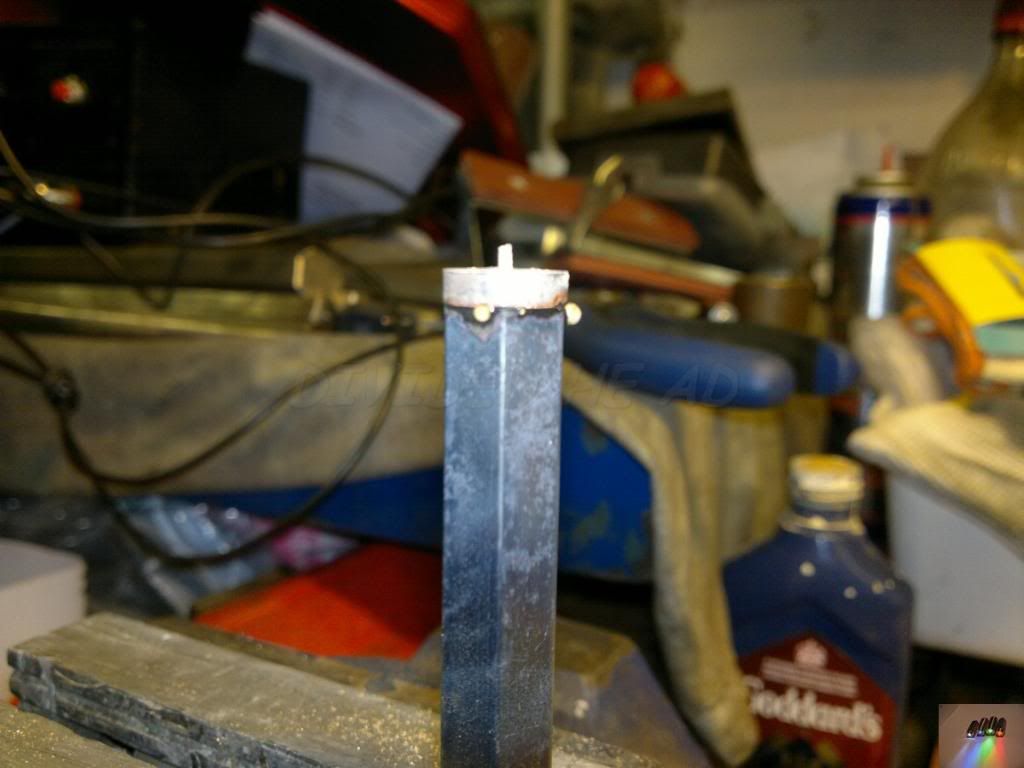
Now make it into a pleasing shape... and drill a hole for the crank pin.
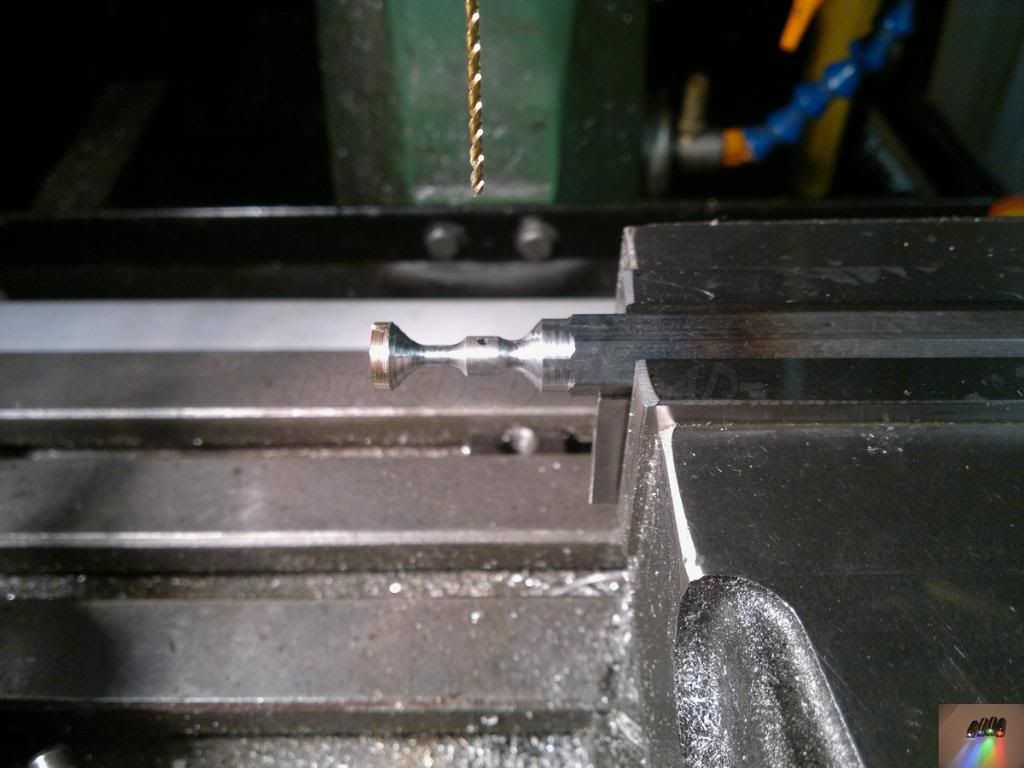
Then drill and tap the crown of the piston before parting off. Attach to an arbour and shape as you feel like.
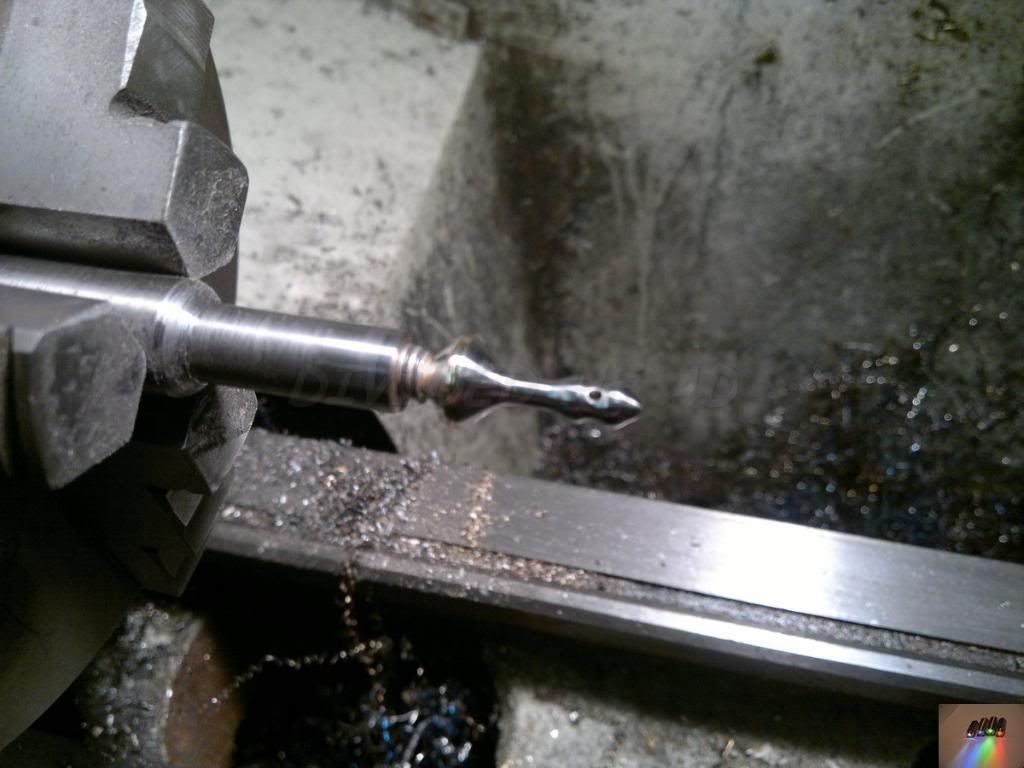
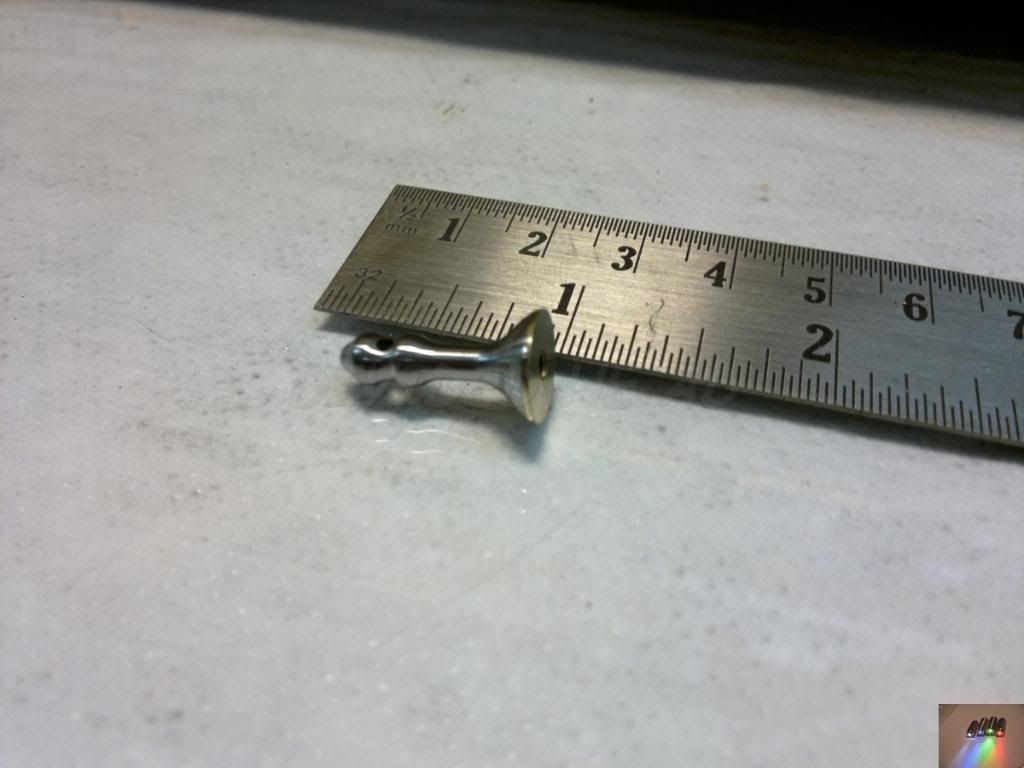
Solder it all together and give it a little clean up...
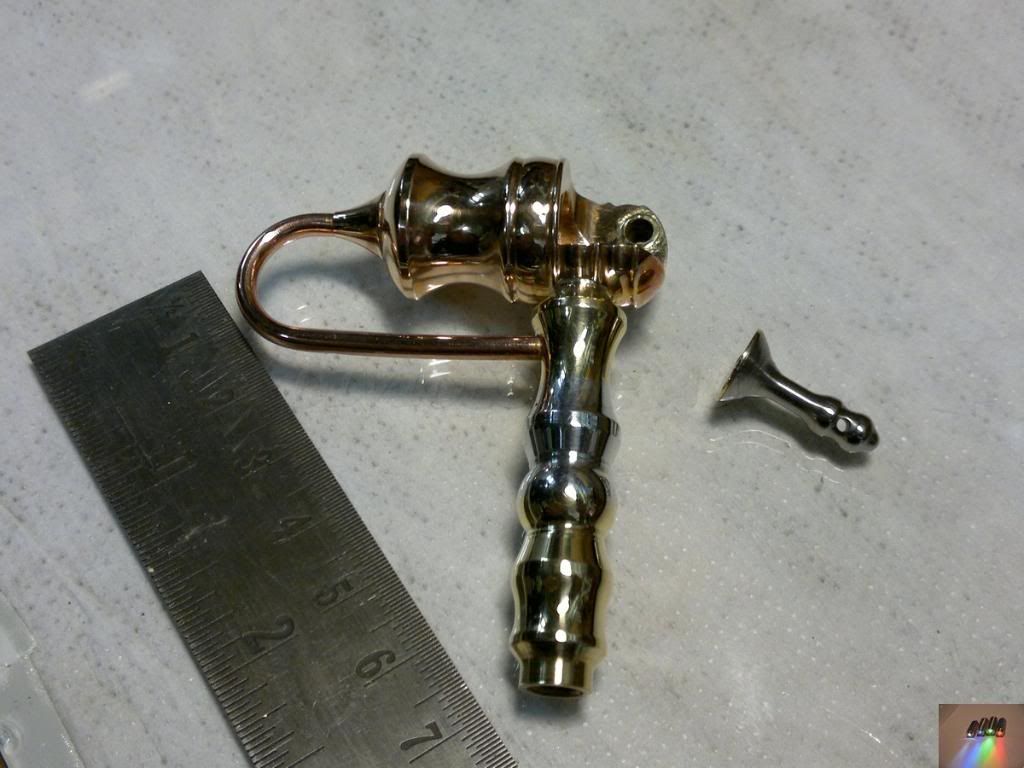
Now the base was intended to be a visual delight.... Maybe intended but not quite as I'd have liked. I may re-design this in the future?
I started with a few pieces of 1/2" hex stock. Thinking of the different materials and contrast theme I used brass stainless and aluminium bronze.... This is where the issues started!

opted to soft solder due to heat requirements of silver solder.....
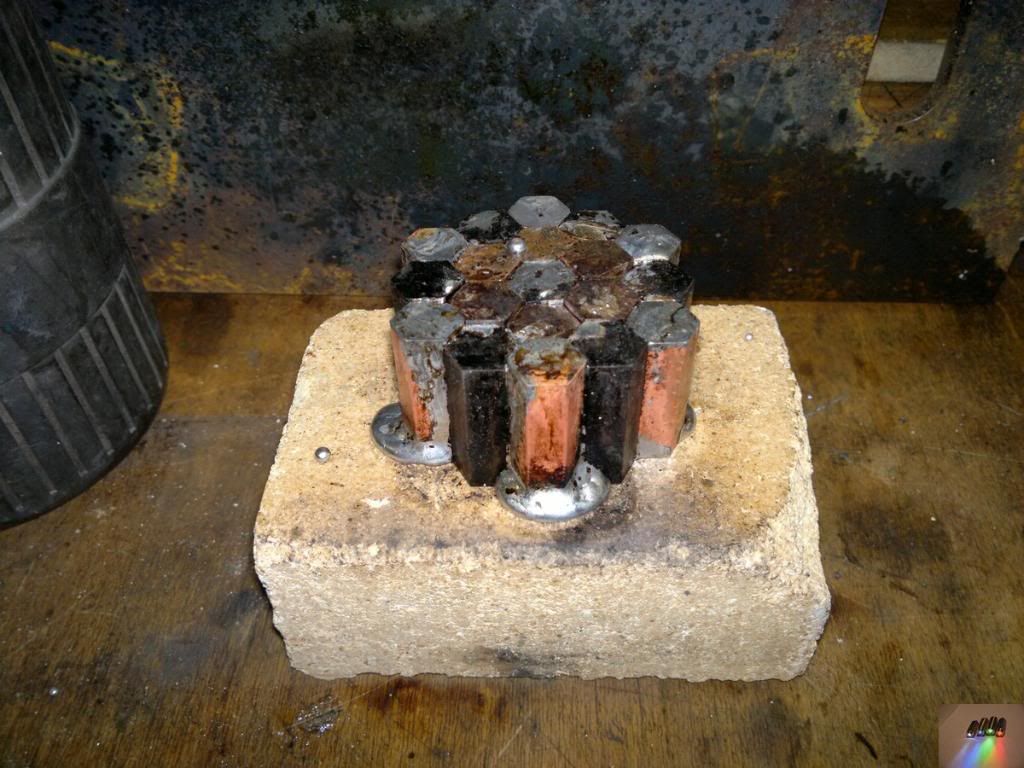
It machined ok for a while....
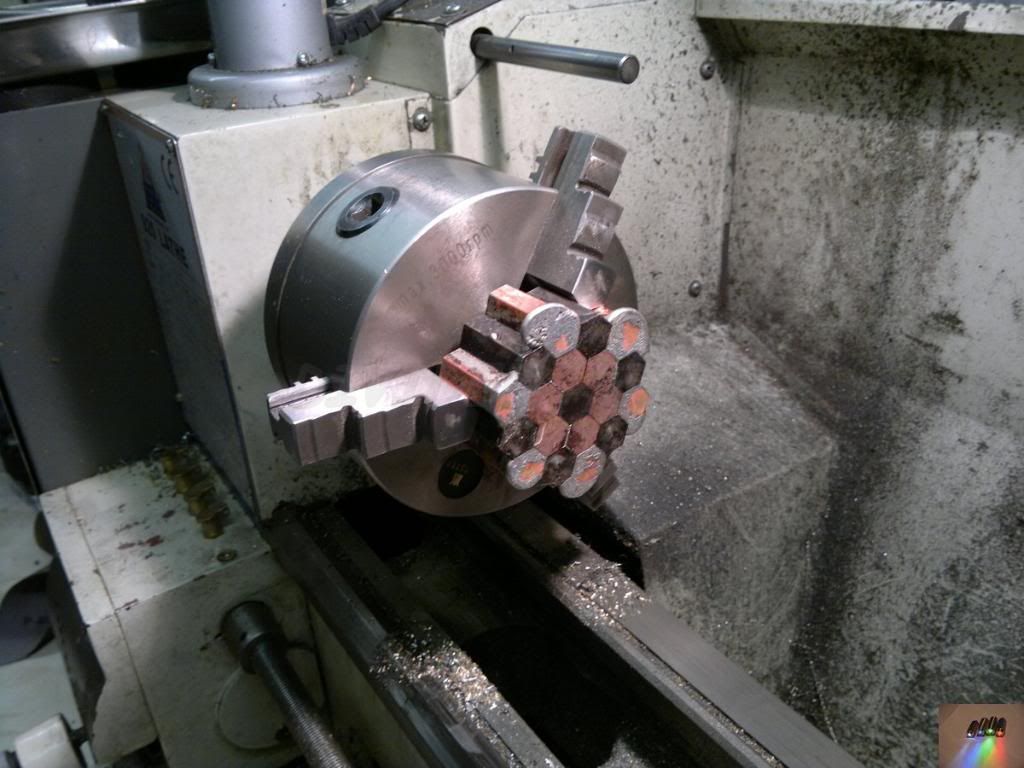
But then it nearly tested my new face shield!!!
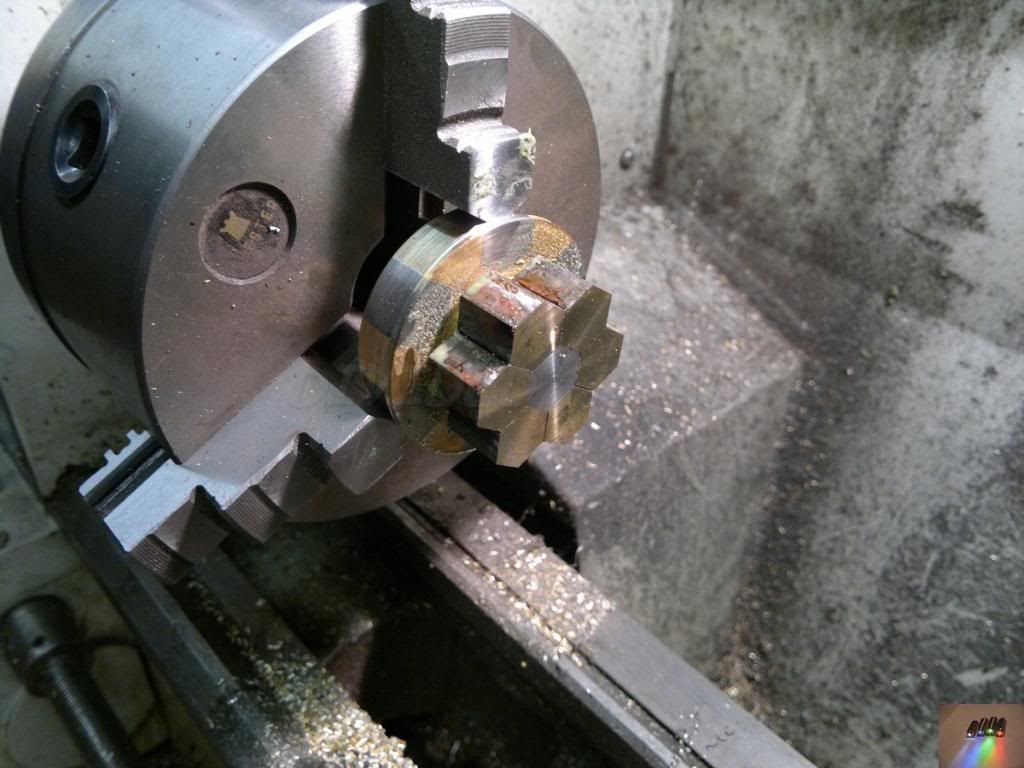
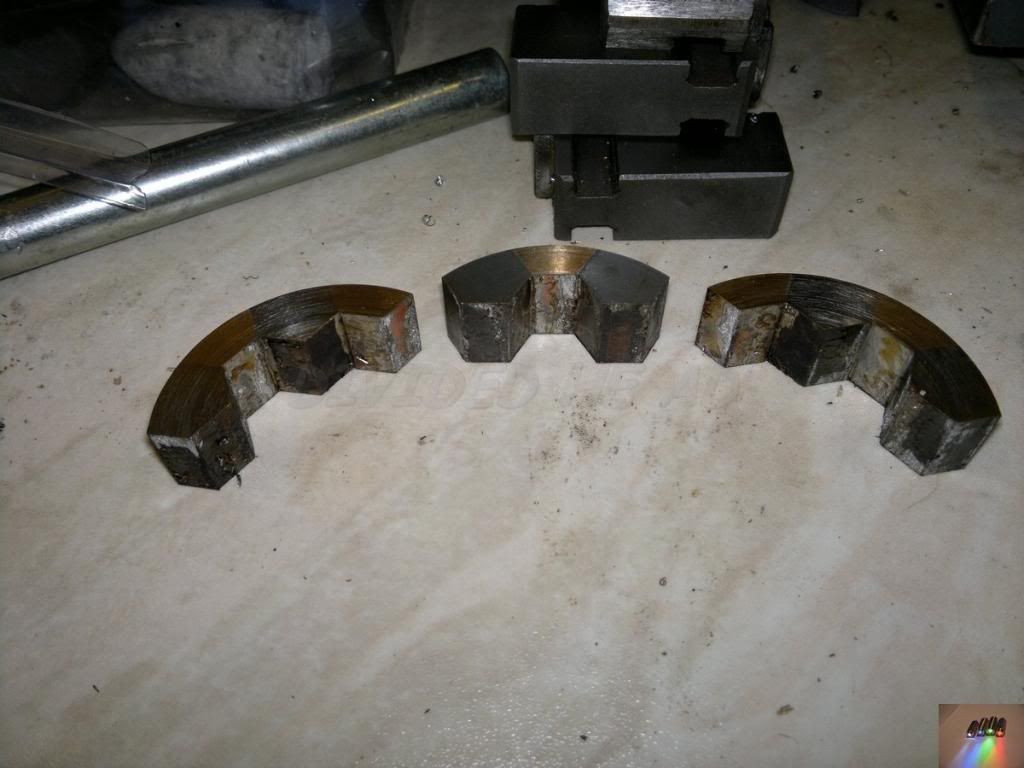
Let it be know (not that many wouldn't have this knowledge already..... Aluminium bronze does NOT soft solder!
So. Not to be discouraged the next evening I salvaged what I could from the disaster and tried again using all brass and stainless.
There was a slight size discrepancy between the stainless and the brass so it wasn't quite as neat as I was shooting for. But it's not bad.... Proves the theory for the design. Just a bit hard to hold it all together and squeeze the molten solder out of the cracks.
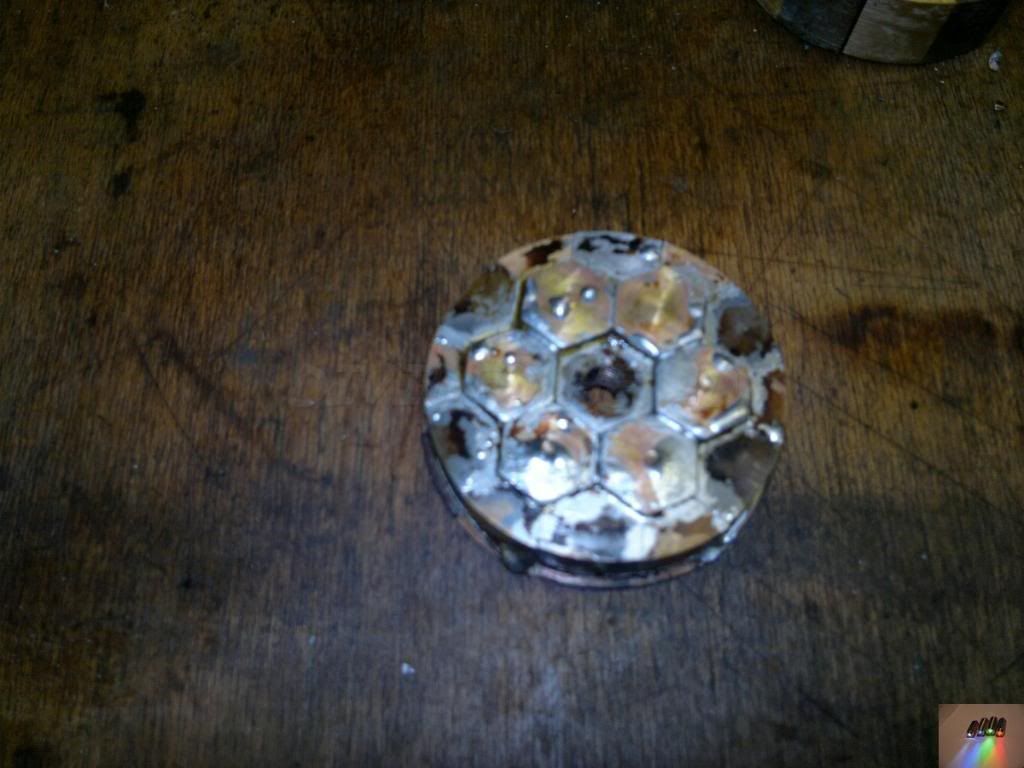
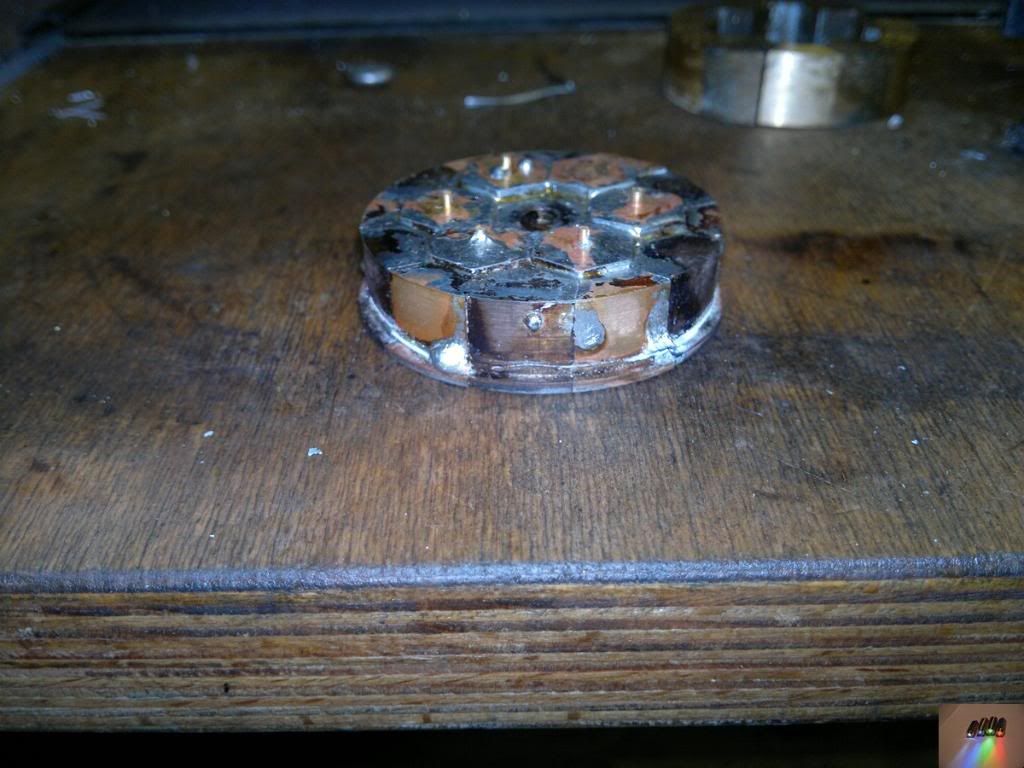
Mounted on an arbour (well... An arbour made from a chuck adapter for my lathe chucks!) I set to work on it with my favourite piece of tooling
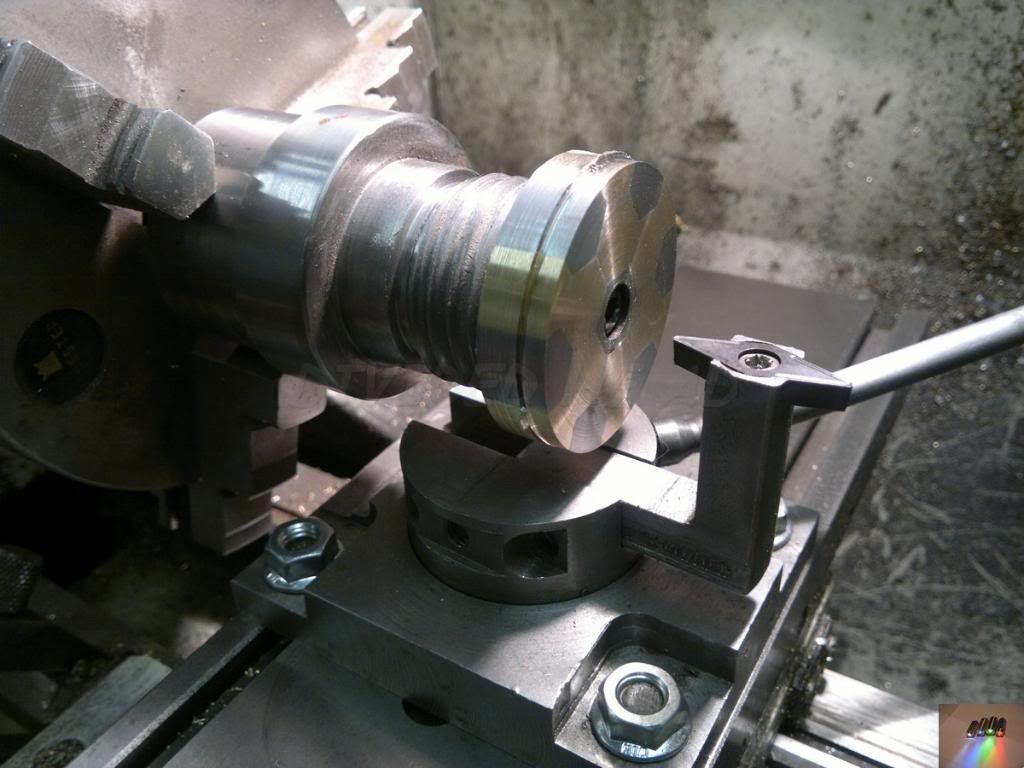
Not much room for error here

Hence the makeshift saddle stop

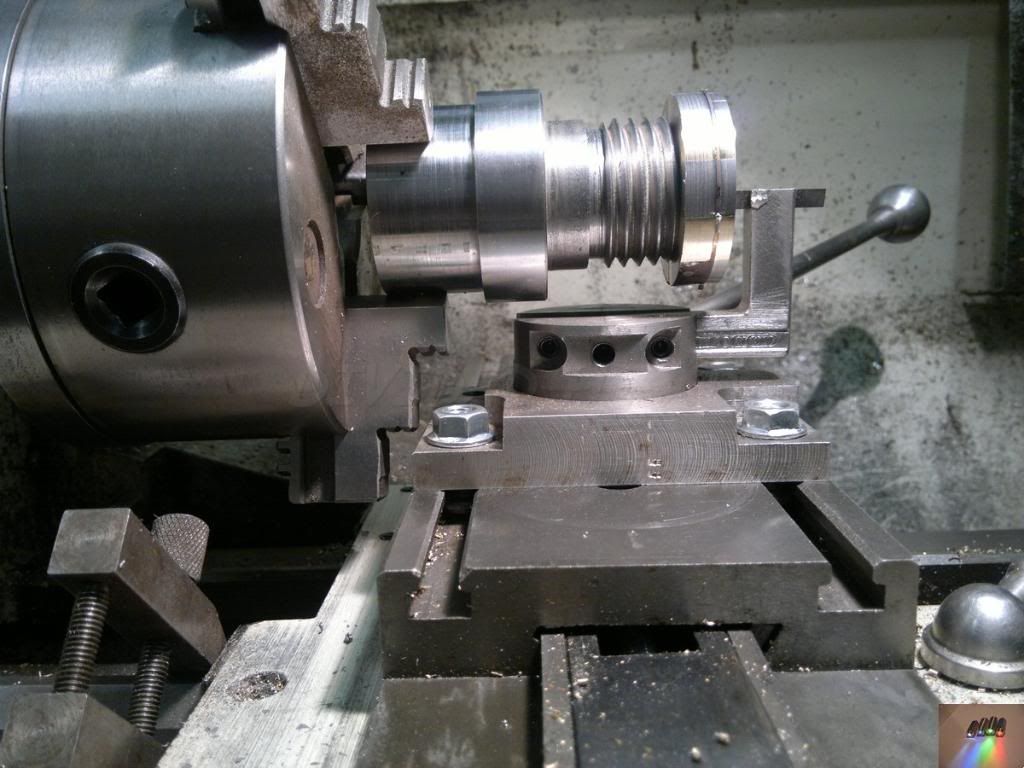
Pretty soon I had this.....
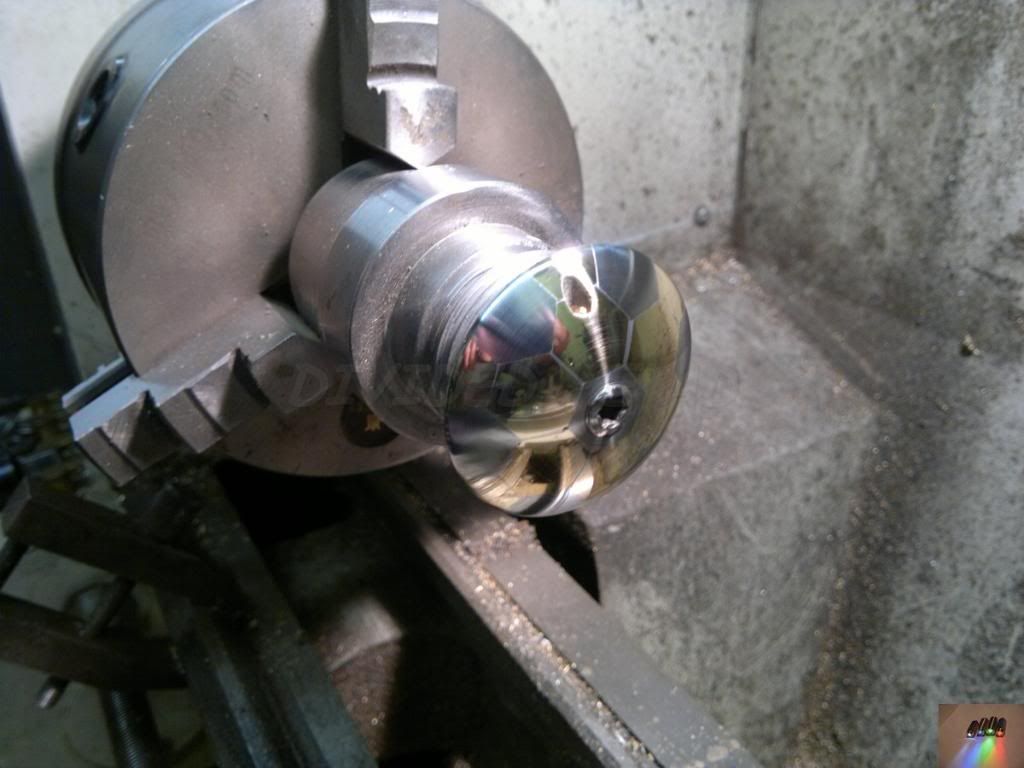
A quick mock up....
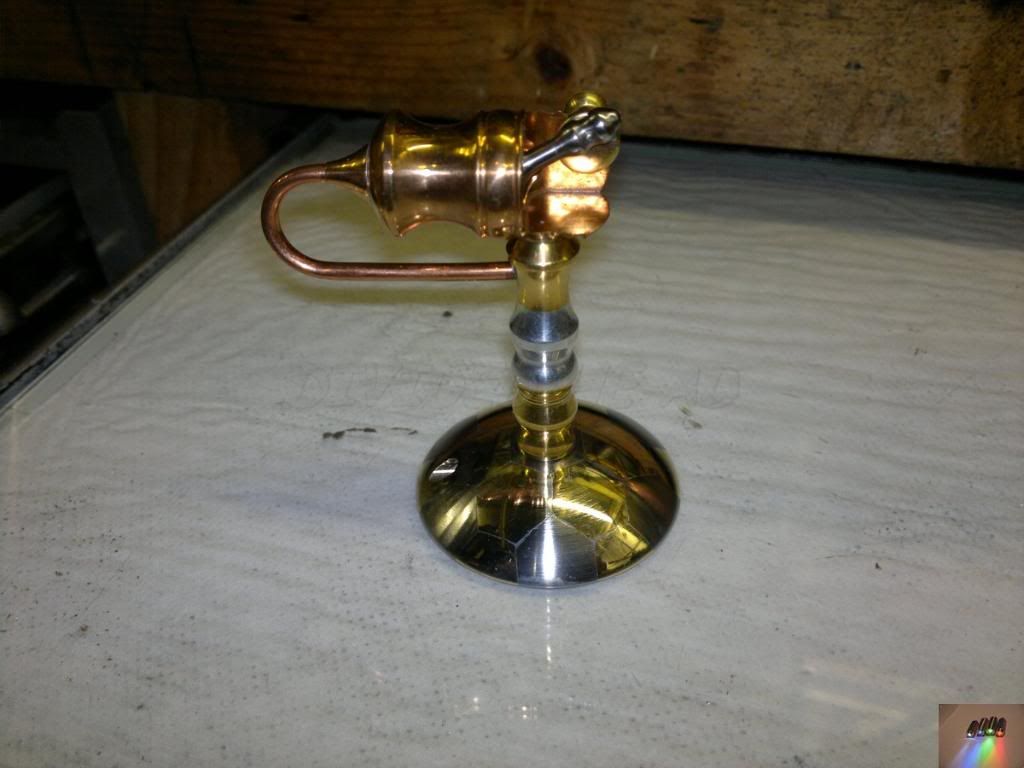
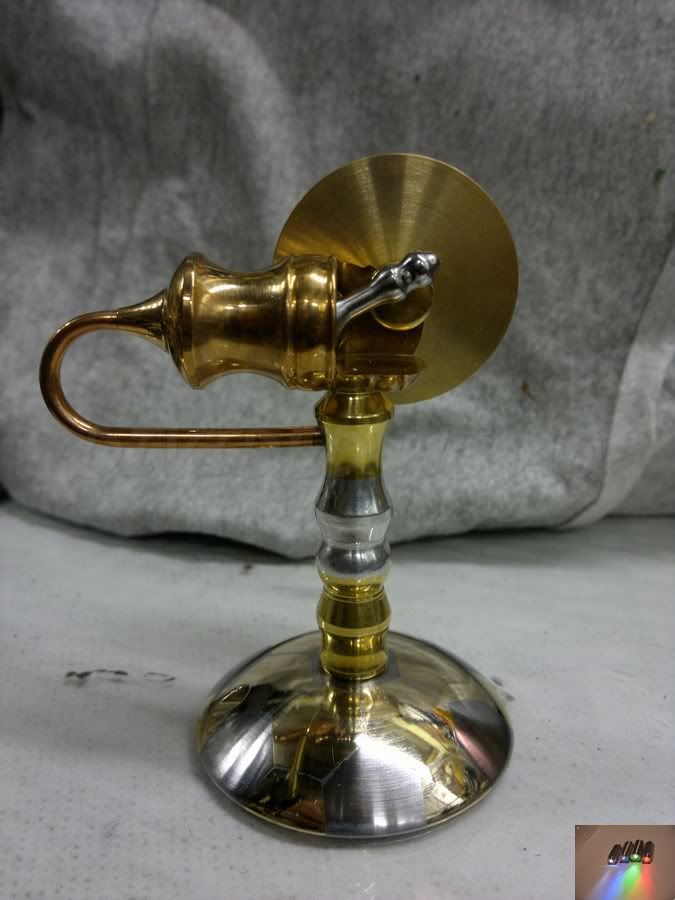
Now just a flywheel to make and it'll be as finished as it'll probably ever be..... Another well learned lesson in home model engineering!
Hope that wasn't too long and too larger post?
Ralph.