Thanks to all for the info on this thread. I had to renew the drive belt on my DW mill:
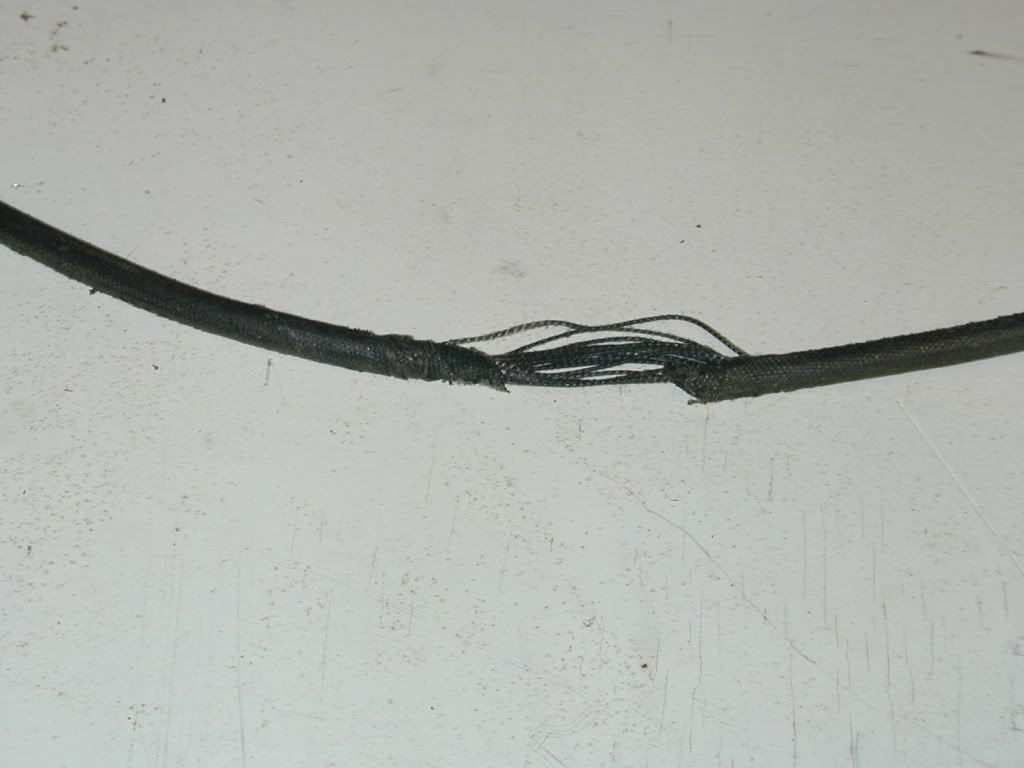
It was 1/4 in in old money:
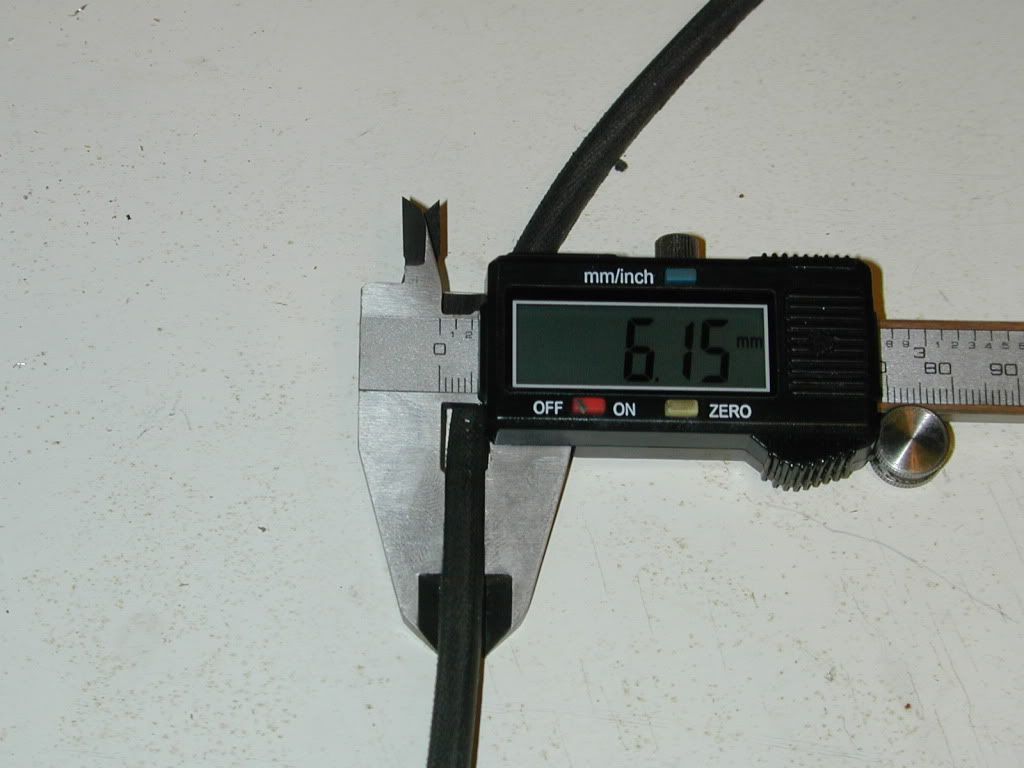
So 6mm should do it. A length of solid Redthayne belt arrived, 6mm:
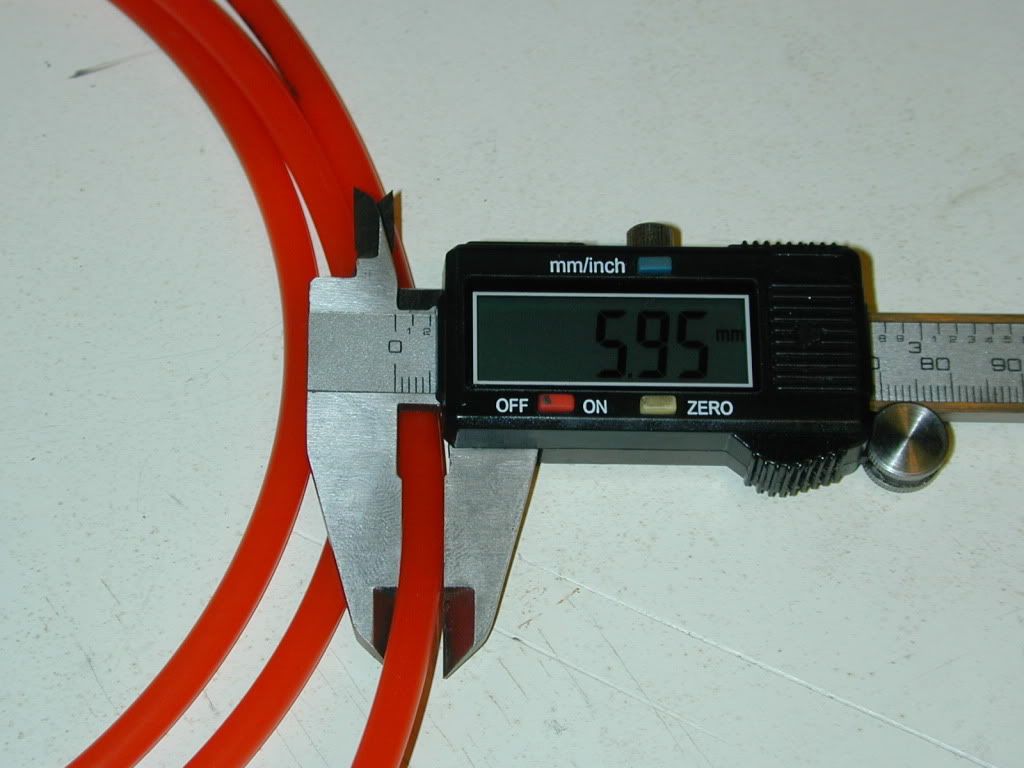
I looped the belt over the pulleys and marked off, just like Bogs did above. I subtracted 7% as
per instructions. I tried Bogs' high tech welding device but couldn't keep the joint still enough between heating
and getting to the angle iron. So, a low tech jig. Apologies to those of a nervous disposition - the jig uses the fibrous brown stuff
normally used for making sheds:
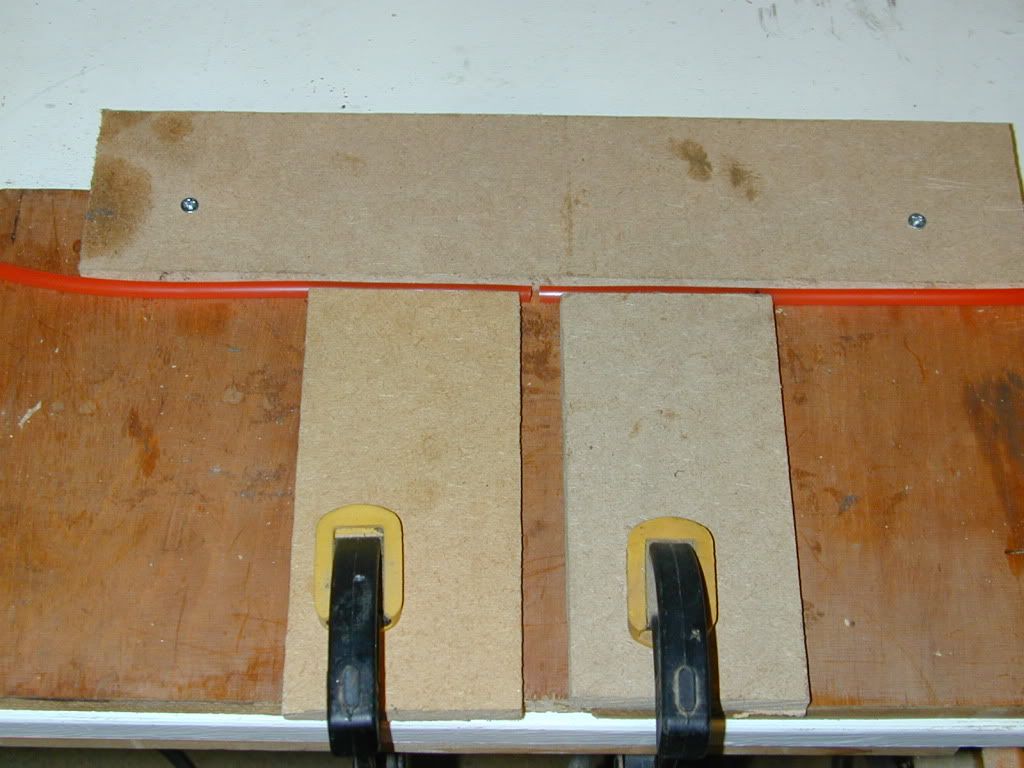
I trapped the belt in each side so it could just be pushed together after heating.
I used an old hacksaw blade, heated up and cleaned with emery to remove any deposits,
then heated to cherry red and placed between the ends of the belting. In the time between
removing the heat and getting to the jig the blade had cooled somewhat, but still easily melted the belt :
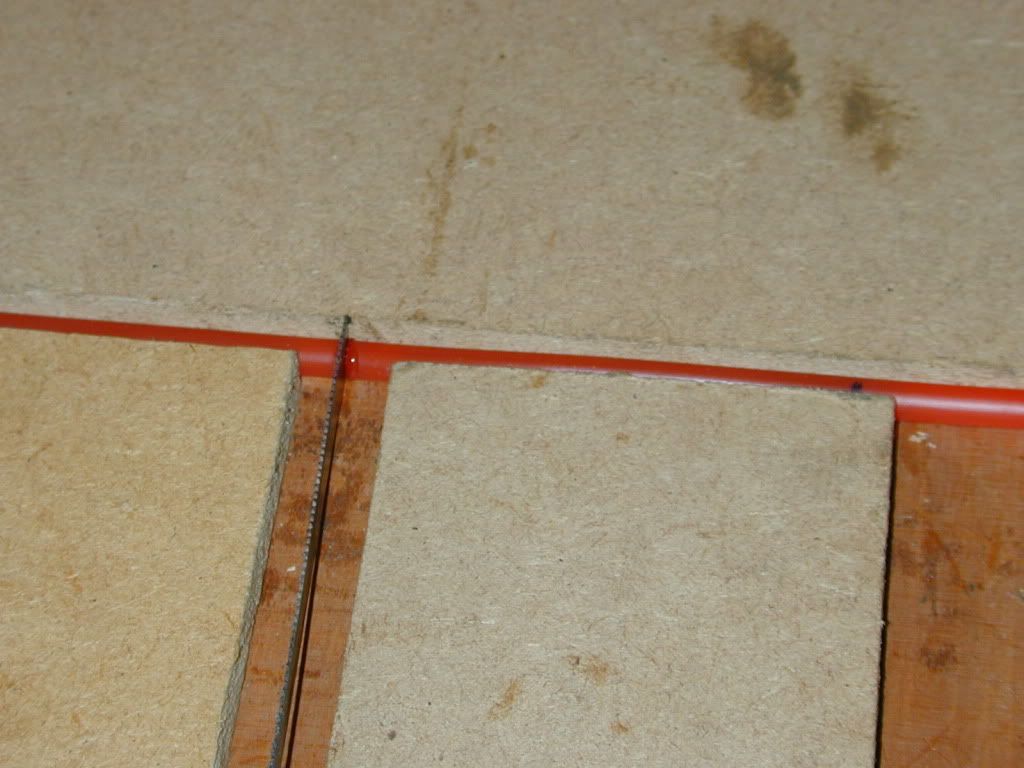
I then gently pushed the ends together and went off for a brew
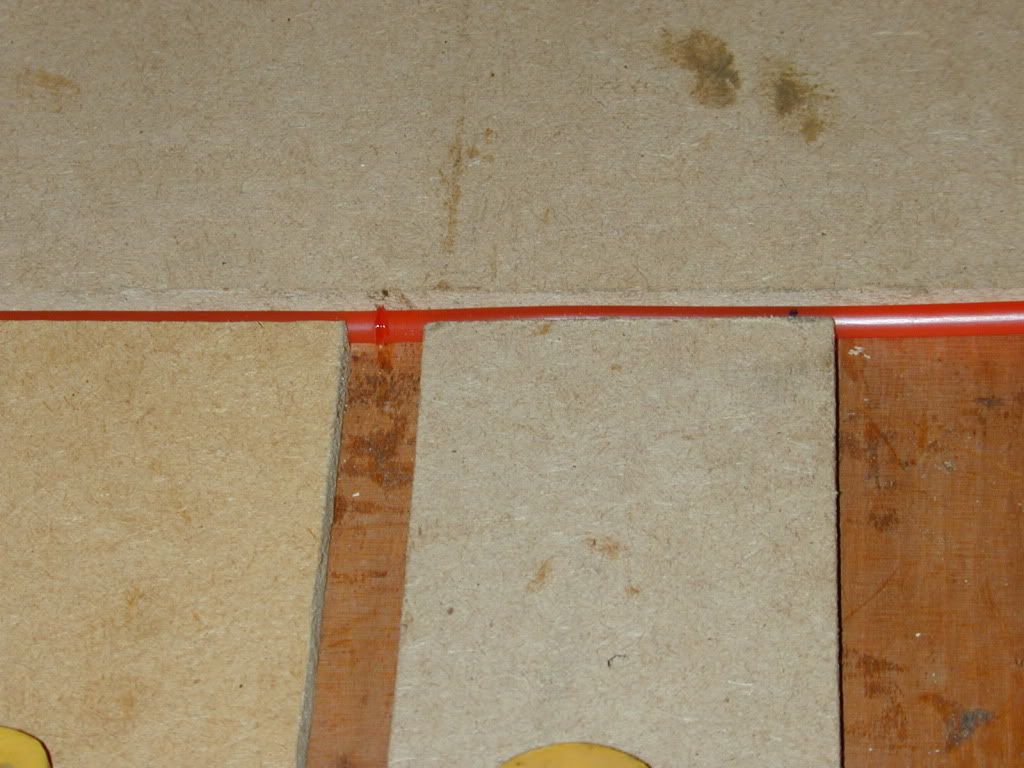
I trimmed the joint with nail clippers (saw that on another post - due credit)
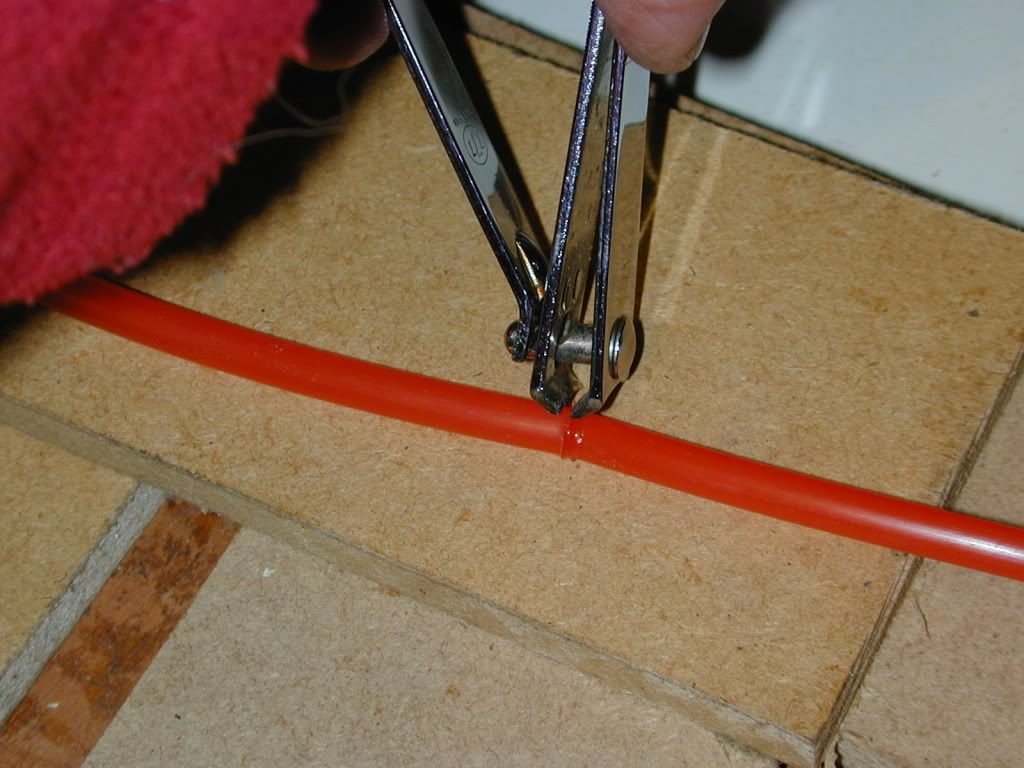
And - result!

The 7% shortening seemed a lot, but the belt stretched nicely over the pulleys and the joint
shows no sign of weakening.
(And Neebs - if you read this, yes, that is your old machine, doing sterling work!!

)
Again, thanks and due credit to all on here who provided inspiration.
John