I don't get that exactly, if it is like I think there are two similar type measurement problems:
Bore and arbour on the same line---this is often soleved by installing close fitting bushing (pin) to bore and maching diameter pin or arbour, then arbour and bore (pin) measurements are clocked with DTI. DTI does not rotate, arbour usually can be rotated with relative ease.
Another measurement problem I am aware is alingment of the two shafts (gear coupling assembly ot such) that used to be abiach, before laset aligment units came common. Measurement guy had to lug along heavy suiticase of measurement fixtures. Smallest one had a prism that rode atop of the shaft, tightened with a strap (or chain) and had pipes to mount DTI, something like this:
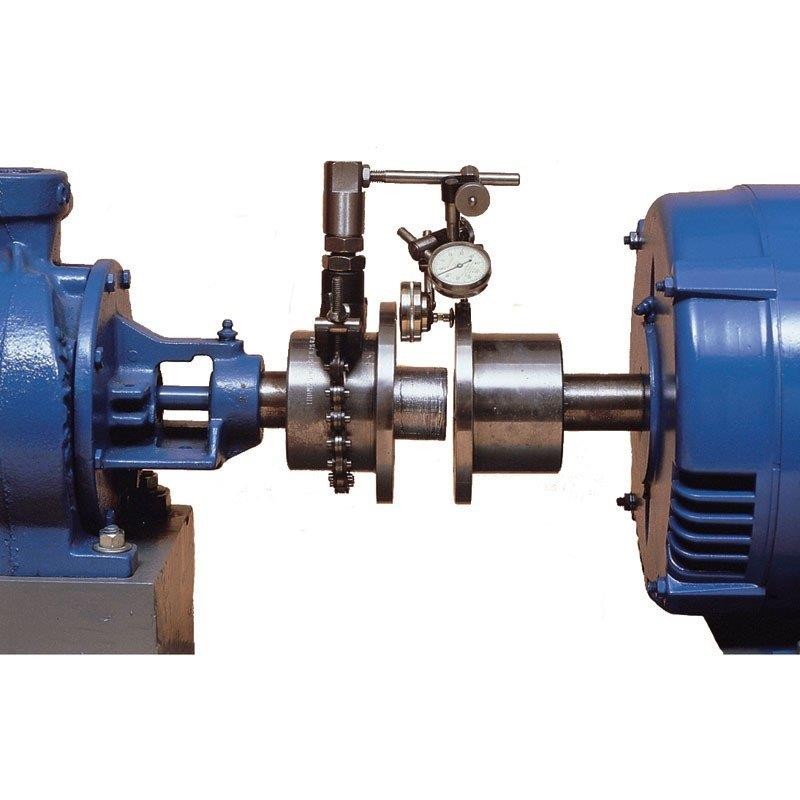
That one looks the part, excluding the "bolt" that mounts the DTI. We used 20 mm hydraulic pipe, sag was neglible in 150 mm extension....tested that on proofing bar, because one mechanician did not believe on sag with his easier magnetic stand
I am pretty sure you have used or seen one used. Am I right?
if unknown/flexible mount was used the trick was to rotate the assembly and use another DTI to measure "sag" - it is the arm/mount that sags and not the DTI....but this takes some experience and an analythical mind set.