With the cylinder block centered in the 4 jaw begin drilling out the bore. Step drill with about 3 or 4 drill bits to 3/8". Then switch to a boring bar. Take several light cuts until the bore is about .010" under 7/16".
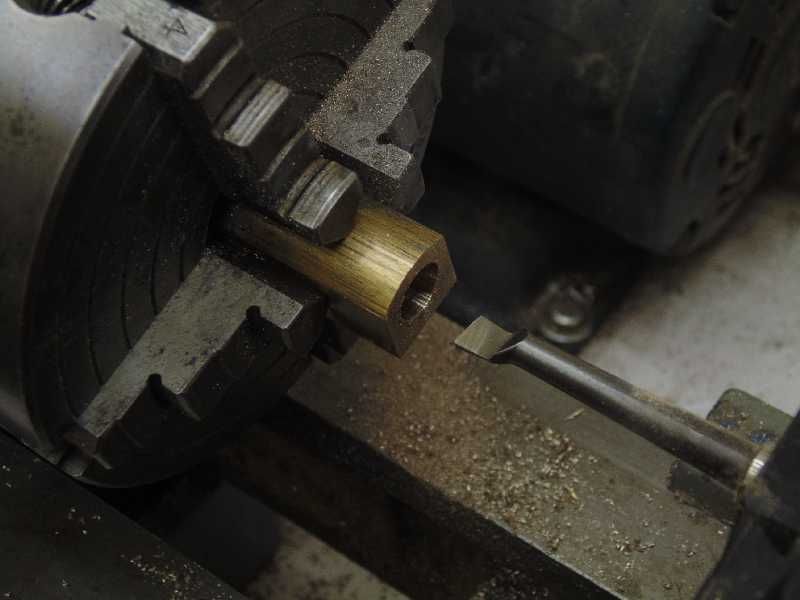
To size the bore exactly to 7/16" use a reamer in the tailstock chuck. Feed the ream slowly with the lathe set at its lowest speed possible. They say you don't have to, but I heavily oil the reamer.
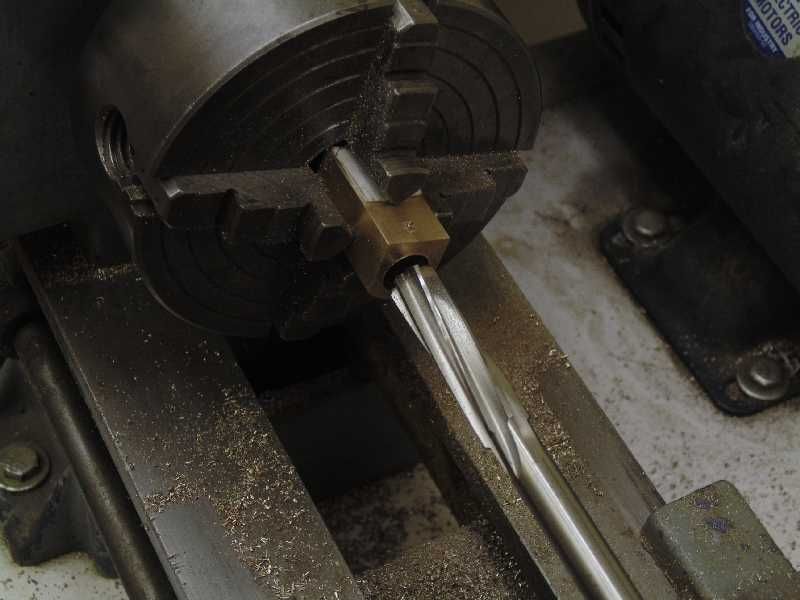
Turn the bottom end of the cylinder to remove excess metal.
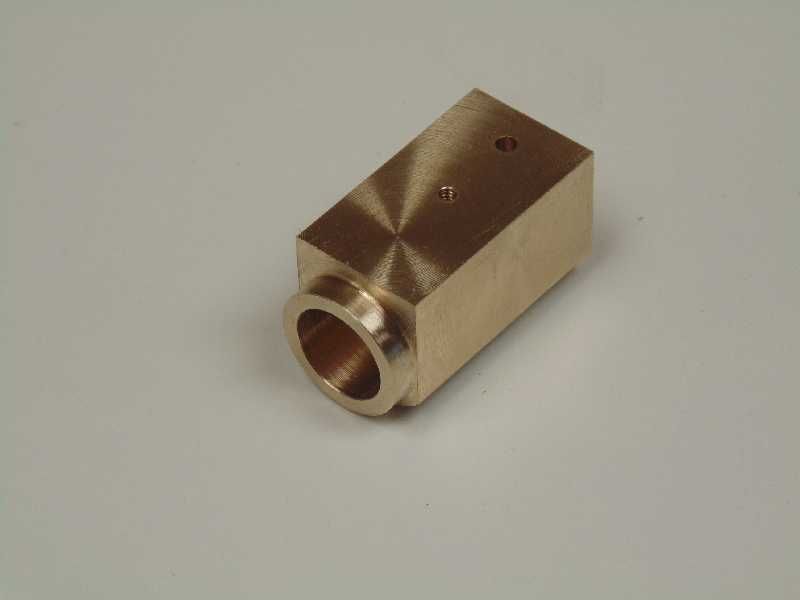
Even though the ream leaves a very good bore surface, it's still not good enough. The bore need "lapping" to remove the microscopic burrs left by the ream. Turn a piece of wood, either maple or oak, to 7/16" diameter. Obtain some fine, #280 grit, grinding paste.
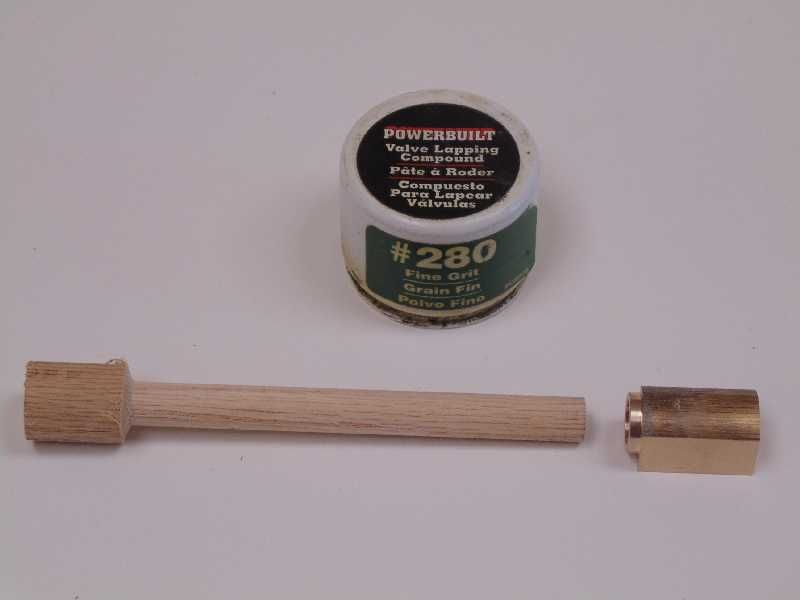
Chuck the wooden lapping rod in the lathe chuck. Apply some grinding compound to the wood lap. Slip the cylinder on and start the lathe. Work the cylinder back and forth on the lap for about 15 to 20 seconds. That's all it needs.
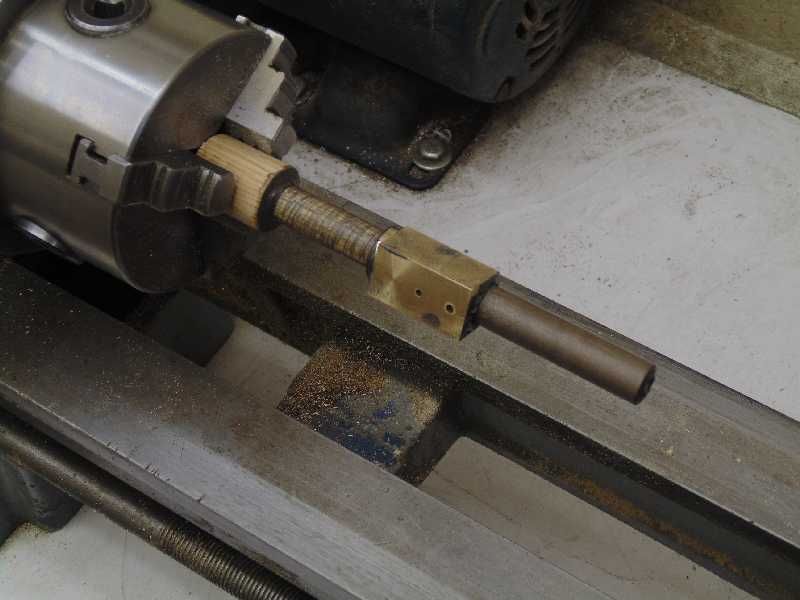
The process requires a lapping rod that is softer then the cylinder, in this case wood. The grinding paste embeds itself in the softer lapping rod in order to hone the cylinder surface. If a harder lap was used, the grinding paste would embed in the cylinder wall and cut the lap. The cylinder bore must be as true as possible before lapping. Lapping will not correct a bad bore. When finished, the bore will have a very smooth frosty surface.
Now lap the portface on the engine standard and cylinder. Do this by taping a quarter sheet of #320 wet/dry sand paper tightly a flat surface. Oil the sand paper and gentle grind the port faces with a circular motion. Repeat the process with #400 grit and again with either #1500 or #2000 grit sandpaper. If you don't have the finer paper, #400 is good enough. It will just take a bit longer for the engine to "run in".
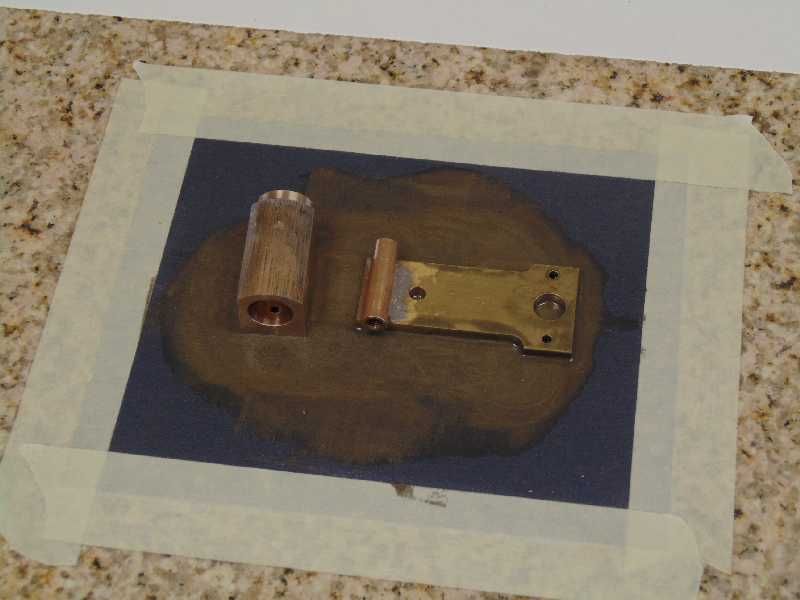
When complete the portfaces are dead flat with a smooth frosty surface.
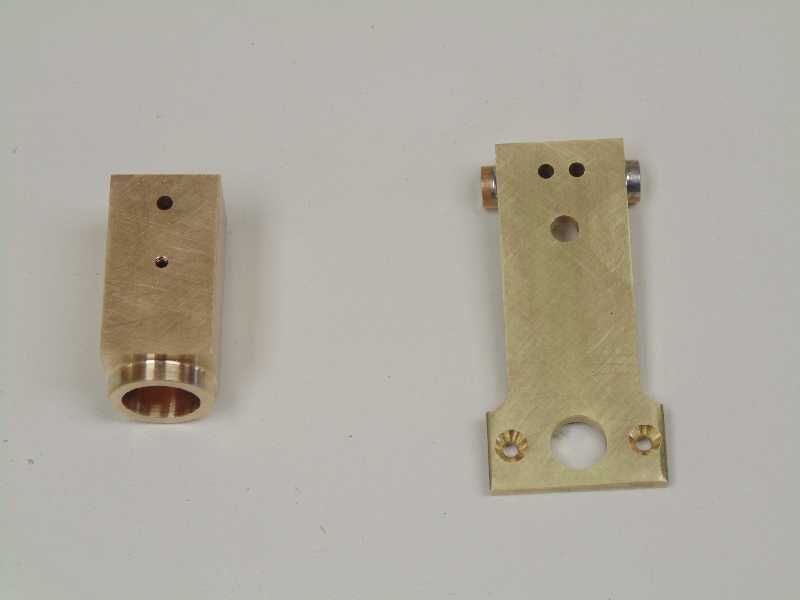
Finally time for the piston. Here is the drawing:
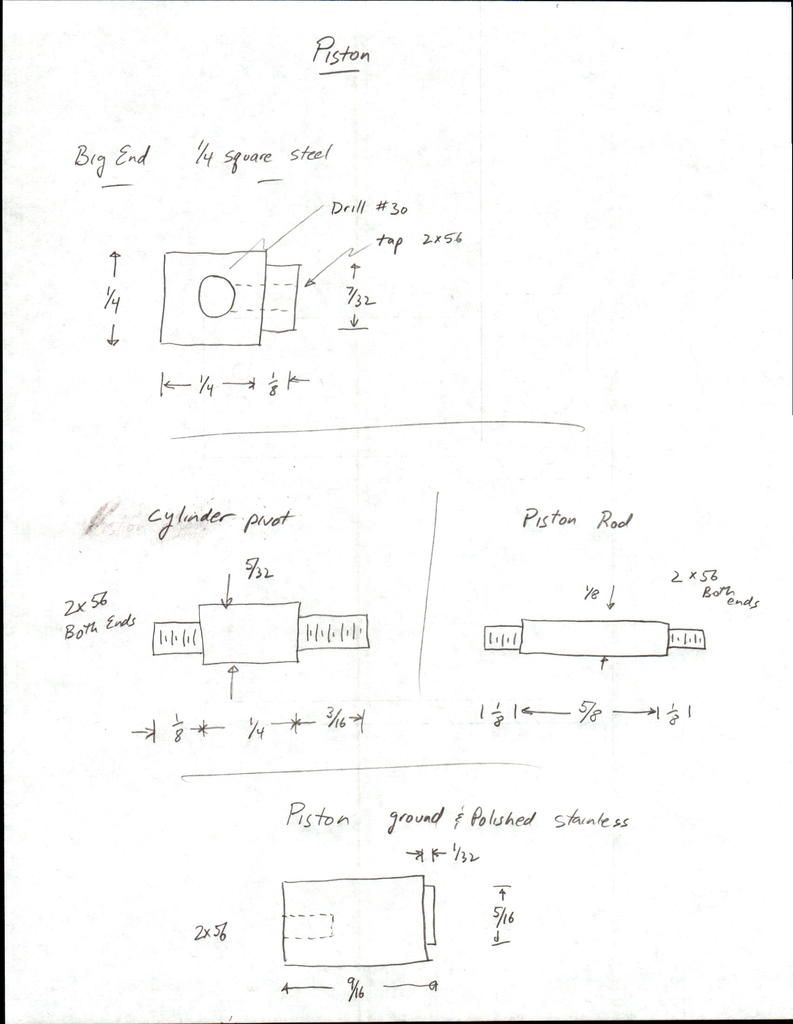
Fabricate the piston with 3 parts, the big end, piston rod and piston. The big end is the hardest part to make. It is 1/4" square stock. To get the big end stock centered in the 3 jaw chuck, make a split collet that fits over the square stock.
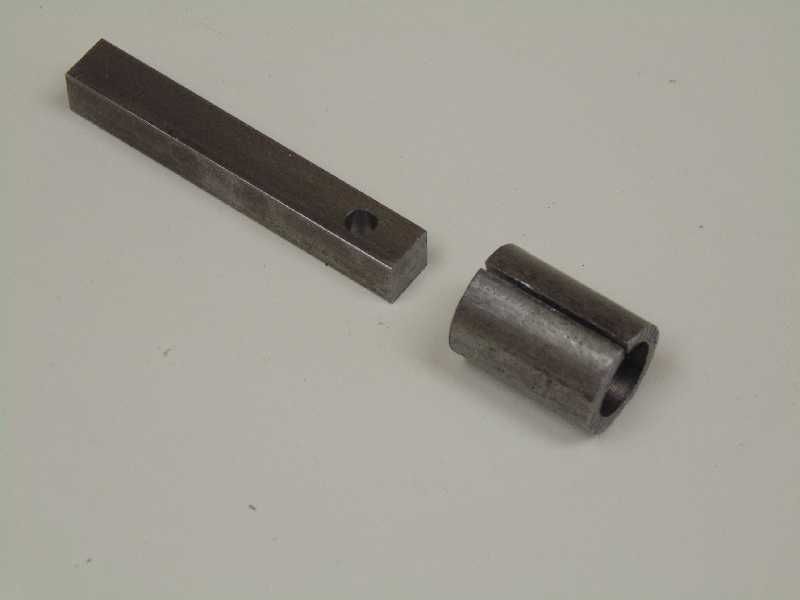
Cross drill the big end with #30 to fit the wrist pin. Chuck the stock with collet in the 3 jaw.
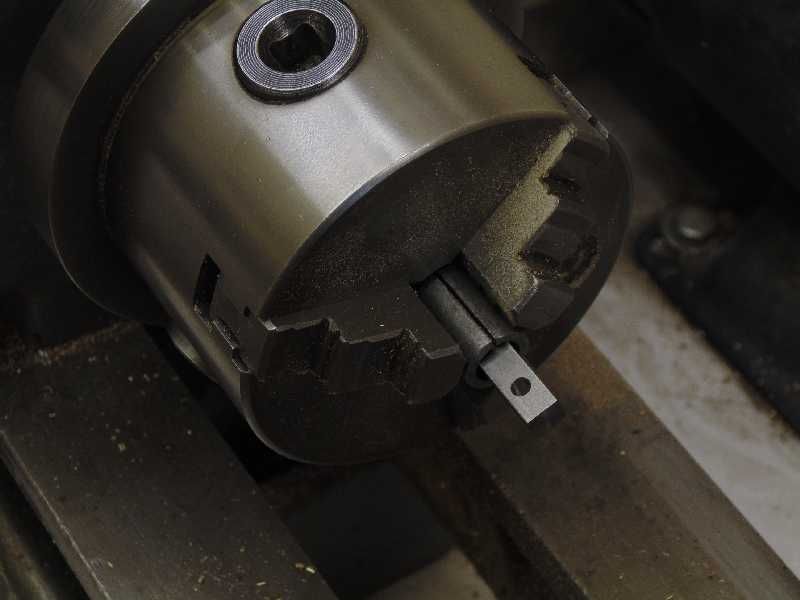
Drill and tap with 2 x 56, turn the end a bit then part the big end off the stock.
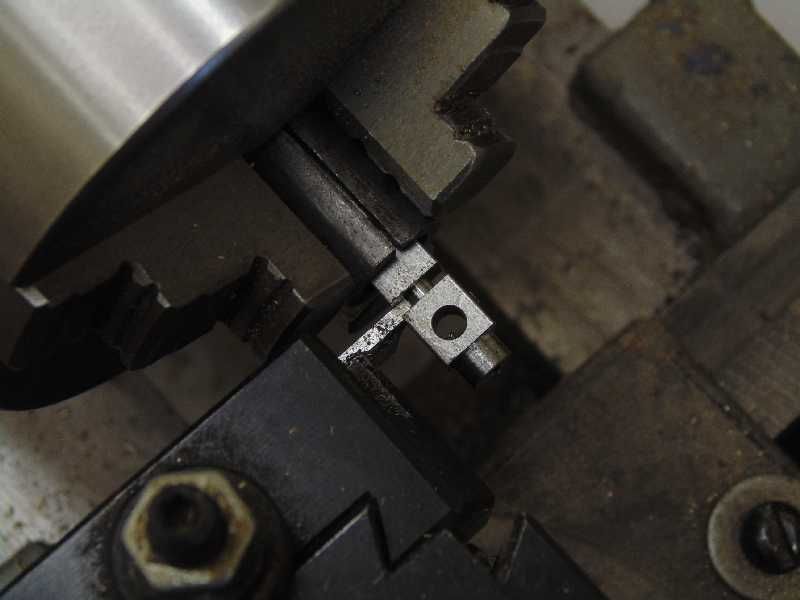
The piston itself is alloy #303 ground and polished stainless steel. The G&P stainless fits perfectly in the reamed and lapped cylinder bore. Drill, tap and turn according to the drawing being careful not to mar the surface.
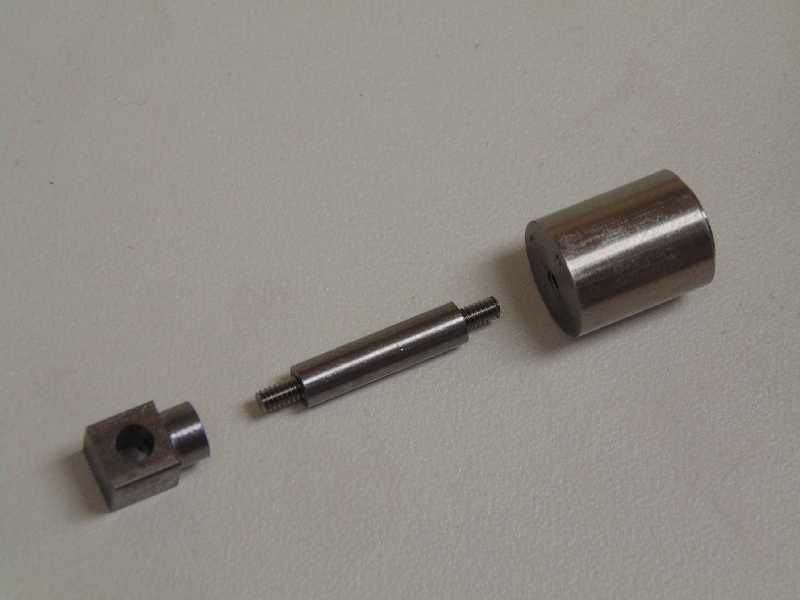
Oil the cylinder and try a test fit of the piston. It should slide close but free. The piston should slide freely when blowing in the portface hole by mouth. If it's too tight, give the cylinder a few more seconds on the lap. When all is ready, soft solder the top cover on the cylinder and make the pivot pin.
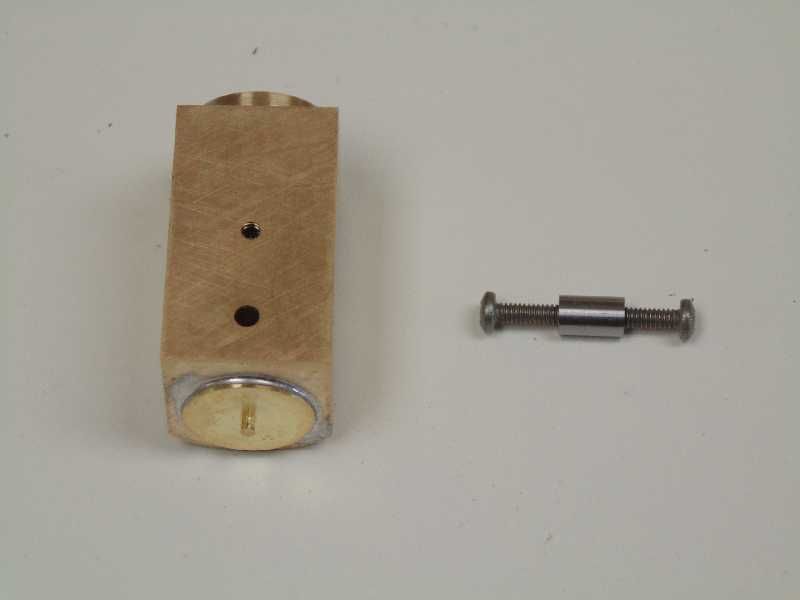
Assemble the motor onto the frame. The cylinder spring is 1/4" long, 1/4" diameter, 0.020" music wire. The exact spring is McMaster Carr part number 9657K259. An equivalent works fine. Oil everything in preparation for the air test. Put a drop of light machine oil between the cylinder and engine standard.
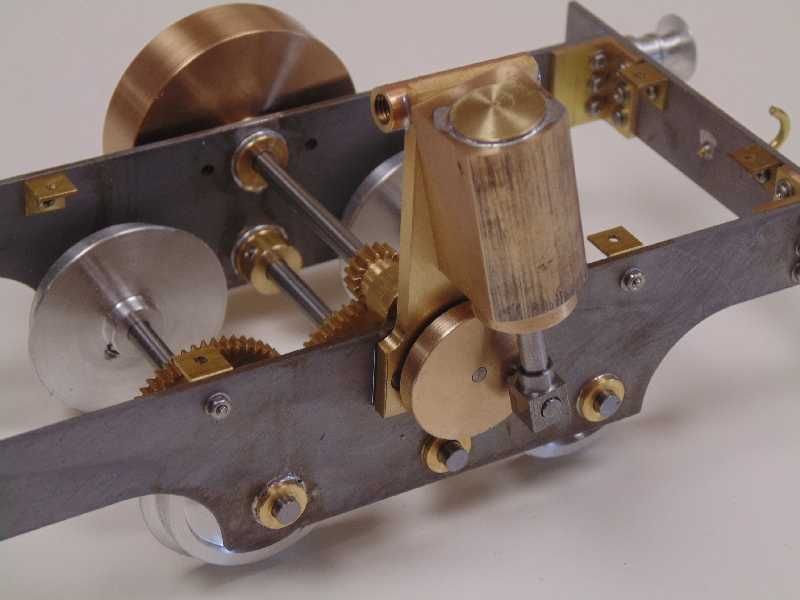
Hook up a regulated air source to the manifold and block up the engine. This engine runs fast on 6 or 7 PSI. Run the engine for about 30 minutes on air. Stop every 5 minutes or so to disassemble the motor and clean it. Do a "dyno test" with a finger against a wheel. It will take some effort to bog the engine down.
https://www.youtube.com/watch?v=2yZPM22uW80Next time is the footplate and fuel tank.