Harold,
I have two machines that can do 4 facet, well one is close but more later.
One is a German Meteor drill grinder that goes from 0.1mm up to 6mm in two stages. ).1mm to 3.2mm and 3mm up to 6mm on a second collet.
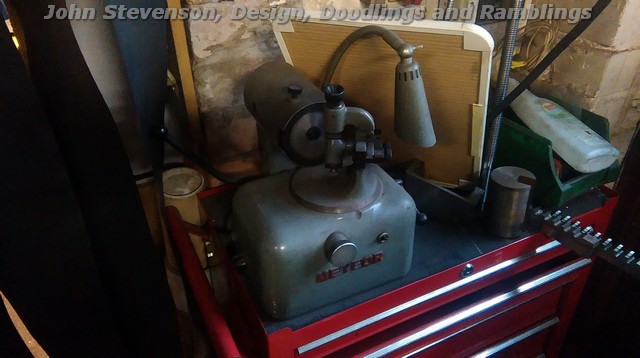
Very similar to a Christian but not as many bells and whistles and because they are not so well know they can be picked up cheap. I paid £40 for this off Ebay. It can only do 4 facet, it has no means of doing what I call a swept grind which we are all used to. It has preset stops so you do the two primary angles first, then drop down to the lower stop and it does the secondary with the cross over exactly at the centre of the drill. It has a microscope fitted so you can see what the drill is like before removing it from the collet.
Quite quick, I recon on a 2.5mm drill it's between 1 and 2 minutes to do a drill.
I do a lot of CNC drilling in 2.5, 3.0 and 3.12 [ 1/8" ] sizes hence buying this machine. I grind brand new drills up from straight out of the box.
The reason for this is these parts have from 250 to 750 holes in per part and even buying good drills like Guring I can get 2 parts and 'may' break the drill in the third part because the web has degraded. It's not the cost of the drill or part for that matter but they can be on the machine for just over 1 hour so I loose this time.
If I turn a new drill into a 4 facet I can guarantee 4 parts before I swap the drill over so it does pay.
The second machine is one I'm working on with the Chinese. It goes from 3mm up to 20mm in two sets of ER collet ranges, ER20 up to 13mm and ER32's from 13 to 20mm.
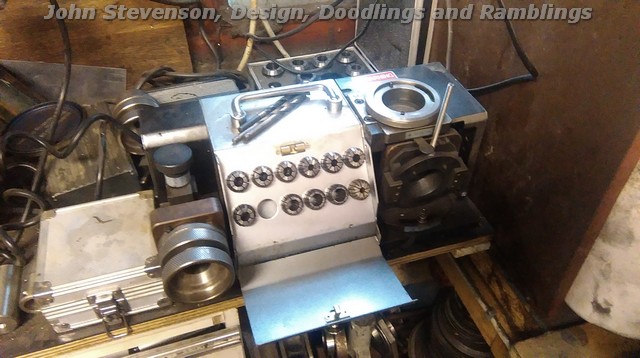
Small collets are carried inside the machine, larger collets are carried in an external box. as you can see from the picture. It can handle HSS, cobalt and carbide in the 3mm to 20mm range.
To use you select the right collet and holder from the two supplied and insert the drill. The left hand side is for setting and the right hand side is for grinding. On the left you wind the top knob in to whatever size drill it is on the scale then push the drill thru the collet and rotate it clockwise until it comes up against the scale stop and tighten the collet. A bit like a drill doctor but in this case there is no plastic it's all hardened steel and very, very robust.
That's it for setting. All the skill needed is built into the machine, not the operator, my grand daughters at 11 and 12 can use this.
You then move the holder to the front hole right hand side and push in and rotate the cam a few time, not endlessly like a drill doctor, even on a 20mm drill it only takes about 4 or 5 wipes per flute.
Now this is where it gets clever although it's not a 4 facet in that its a swept grind and done in one pass with no extra settings the cam is very subtle in that the first part is same as a 4 facet and flat and then it sweeps away.
When I say subtle you can feel it, only see it in the correct light.
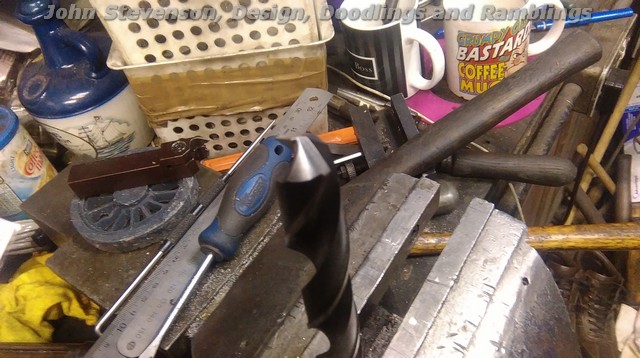
This is the best I can do with a camera phone on a 16.5mm drill.
The top hole is for split points but we are still working on this. We are on the 4th cam but still not right over the whole range.
I timed that 16.5mm drill at 1 minute 20 seconds and I dare say there are a few people on here who have seen this work at Harrogate and Doncaster and can back up the speed and lack of skill need to use it.