This is my first attempt at metal spinning (not counting the one 10 minutes before this where I overdid the annealing and the metal went too soft

).
I have a car radiator which is leaking from the join with the filler neck - I've soldered it once and a professional has done it once and it's leaking again. This time the rest of the radiator is a bit tired so I plan to get it recored. I want to try and stop this leak properly and I think a flange that bridges the joint might give it sufficient extra strength. Here's a picture of the filler neck. In spite of the bracing piece it cracks the solder underneath the neck.
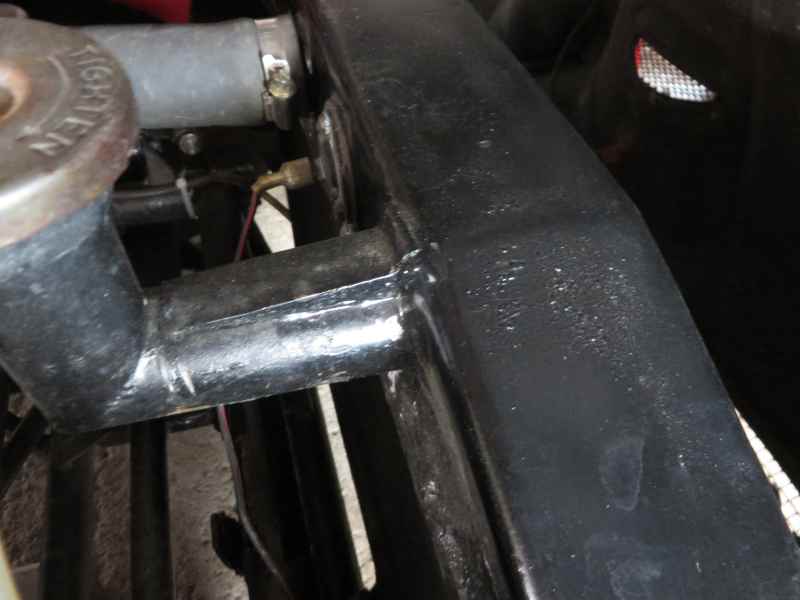
I could turn a flange from a bit of bar but I haven't got any and it would be expensive. I have got some brass sheet though so I thought I'd try metal spinning.
Here is the setup to try it. The former is from the scrap box (a collet chuck which I took too much off). The brass sheet has been fitted to it with a hammer and a jubilee clip. I drilled it in the lathe.
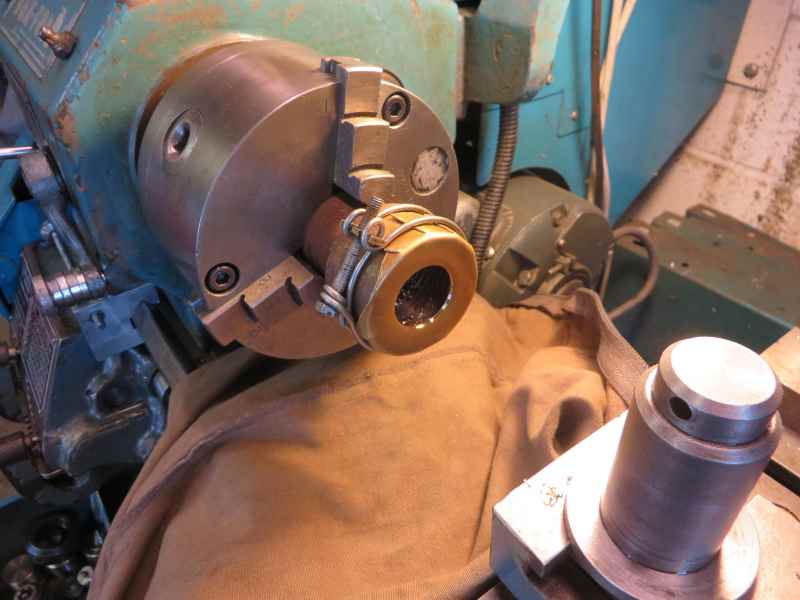
This is the lever arrangement. The toolholder isn't clamped to the toolpost and the toolpost has been oiled. The bar has a rounded end from a test of a ball turner. The bar is just resting on the toolholder slot.
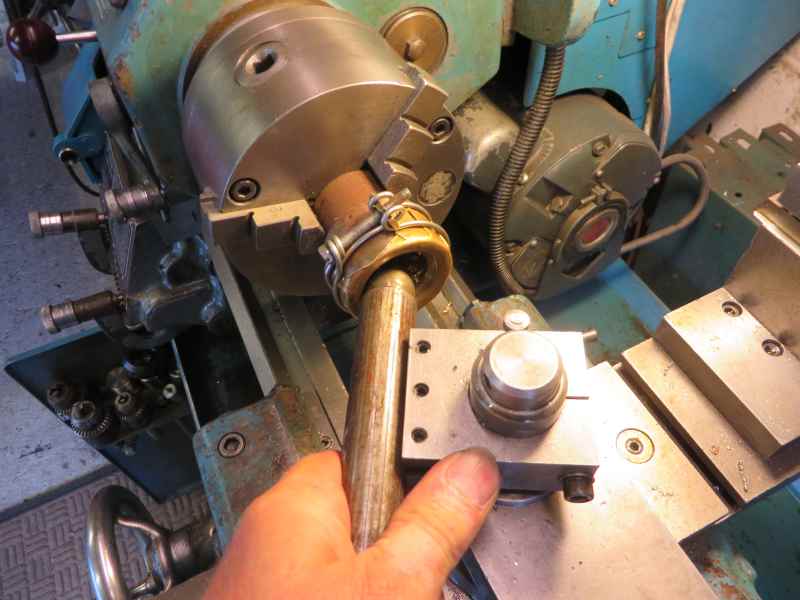
This is the result. It took much less force than I expected. I annealed it twice.
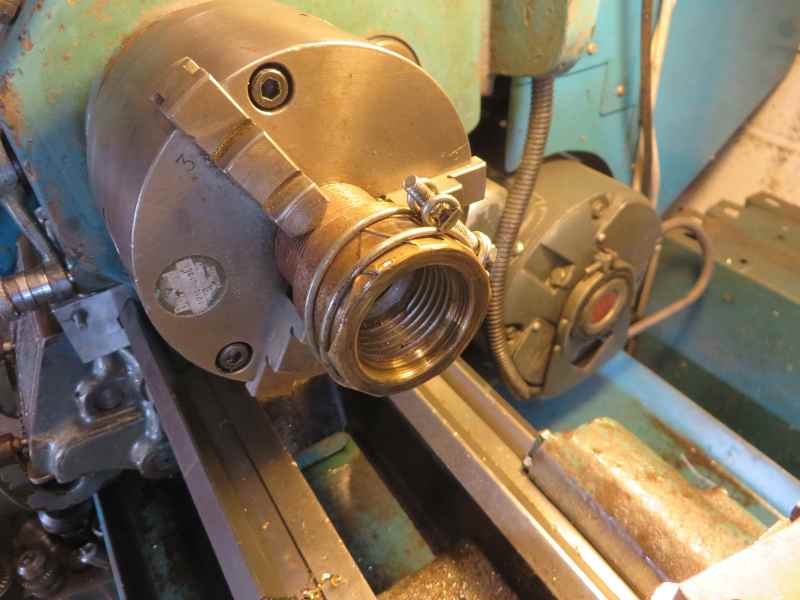
And here it is parted off and cleaned up.
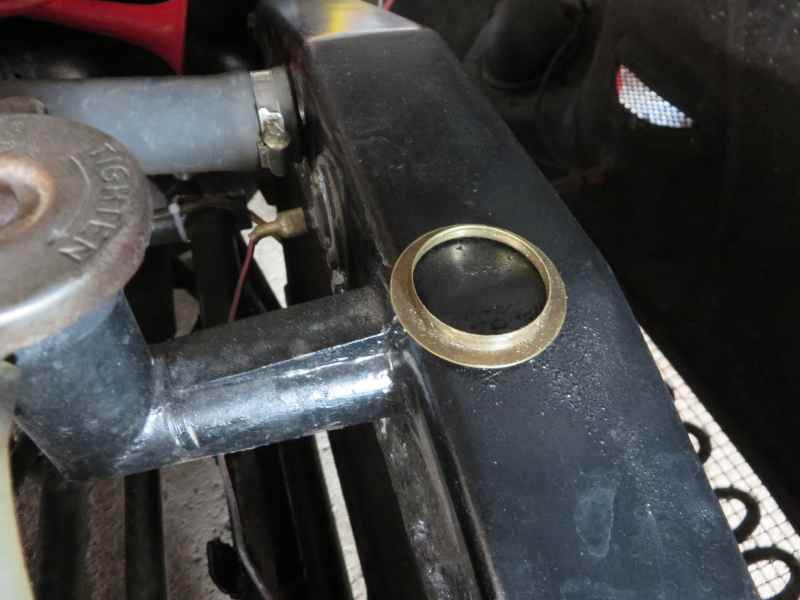
I'm encouraged by this experiment - it didn't feel like I was abusing the lathe much - and the result was OK.
The next step is to make a former the correct size.