Thank you all, I'm putting my bad memory down to heavy metals, I had actually seen the Ox tools video, completely forgot it, maybe, now that I have a lathe with a thread indicator I might just remember the technique! Definitely take the panic out of things!
Russel, the face plate wont bomt up, there is a boss on the back, modification is going to be in order.
Thanks AdeV, I haven't cleaned up my thread indicator plate much yet, I could probably do better! Steve's photo editing methods should improve things.
Building up the end of the shaft.
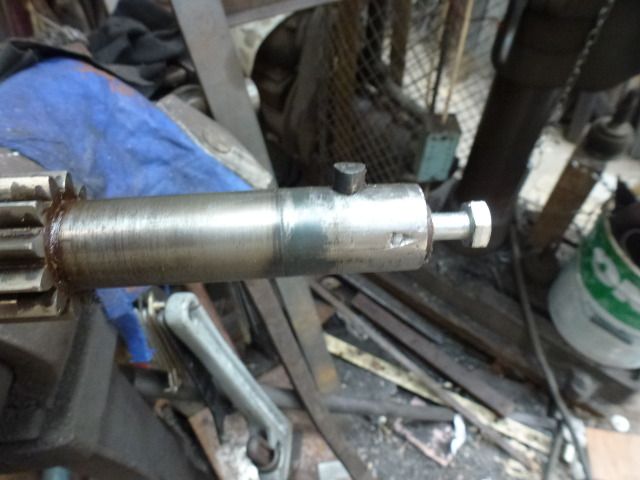
The shaft was broken between the hand wheel and the dial. Underneath the dial, was a buton to adjhust the friction on the dial. A screw in the shaft pushed against a taper, pushing out the friction piece. You can see where the shaft had been heated to remove or straighten it. The bearing part of the shaft is straight and untouched.
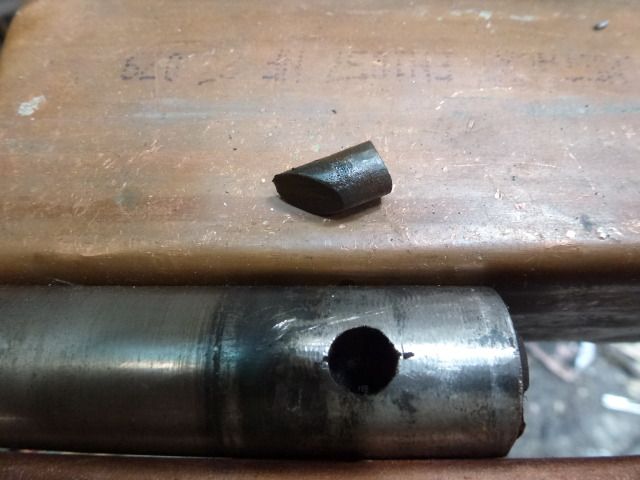
I was lucky, I got the wedge out easily!
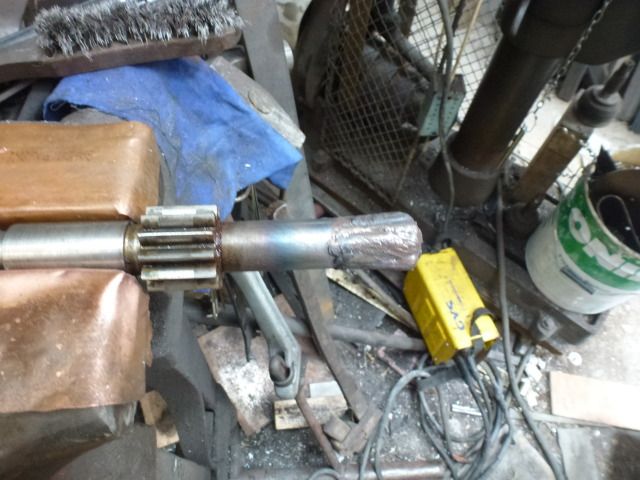
I began by building up on the side opposite the bend.
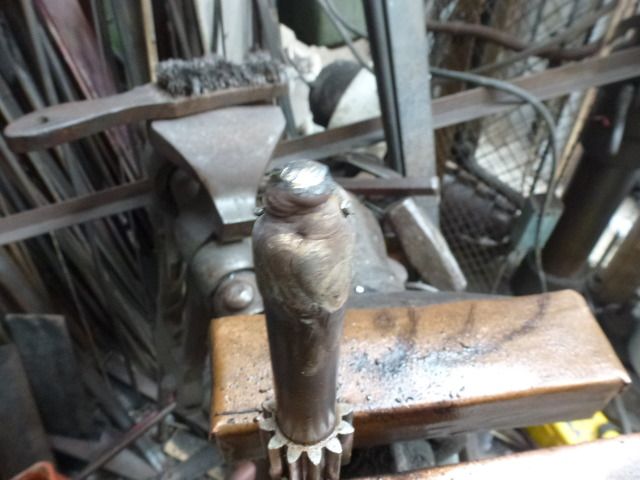
more building up. I used some Castolin rods that I bought for welding railway track! They don't quench harden. I was able to keep the shaft both cool and soft.
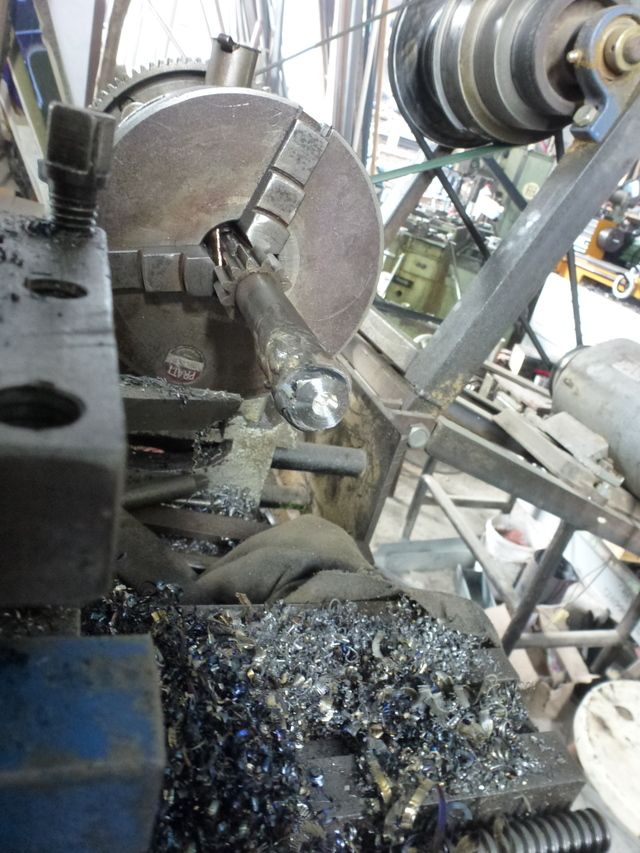
Faced off and centre drilled.
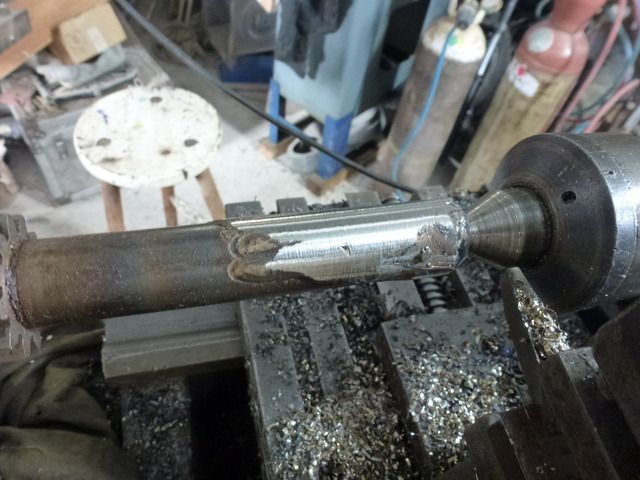
Turning down the weld.
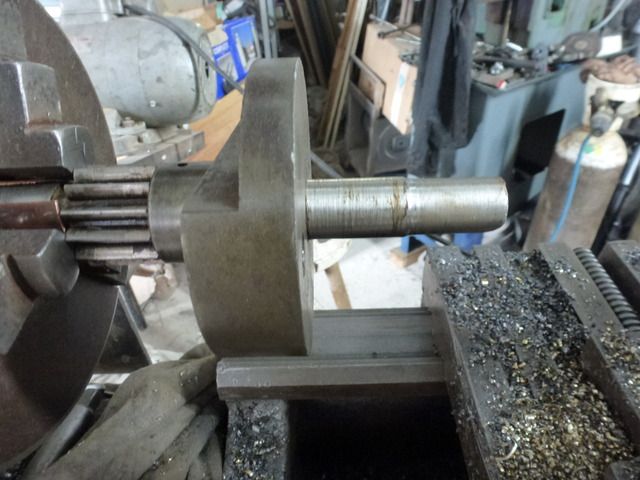
As the bearing part of the shaft was untouched it was relatively easy to cut the major diameter.
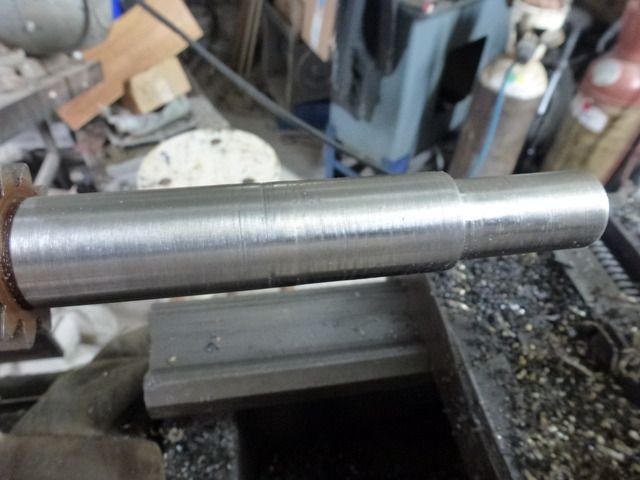
It's not very photogenic! This was after a little touch up with emery paper, it looks better "in the flesh"!
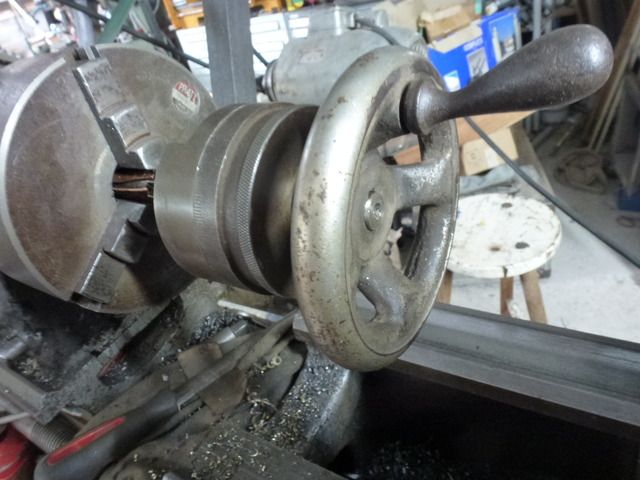
All the bits fit, it needs the key way and drilling and tapping for the friction adjuster!
Regards, Matthew